The goal of a lightning proof transmission line has been attainable since the early 1990s when the first polymeric-housed transmission line arresters became available. Indeed, based on IEEE 1410 and IEEE 1243, installation of arresters on every phase of every tower of a shielded line will ensure no lightning induced insulator flashovers – essentially a line that is ‘lightning proof’. However, for a number of reasons, most engineers involved in overhead line design have still not adopted this guaranteed strategy to improve lightning performance. Perhaps the most cited reasons for this are that the arresters themselves are seen as a potential factor in reduced reliability and could also require a lot of maintenance.
The dominant design of transmission line arrester used over the past 20 years – the non-gapped type (NGLA) – has demonstrated that such concerns are generally not valid. The NGLA has demonstrated that it is highly reliable and failures are comparatively few. Nevertheless, it seems clear that another approach towards the goal of lightning proofing a line is necessary in order to eliminate all possible concerns by line designers.
This past article by arrester expert and INMR columnist, Jonathan Woodworth, discussed the basics of the externally gapped line arrester (EGLA) in order to increase knowledge and confidence in applying them for line protection.
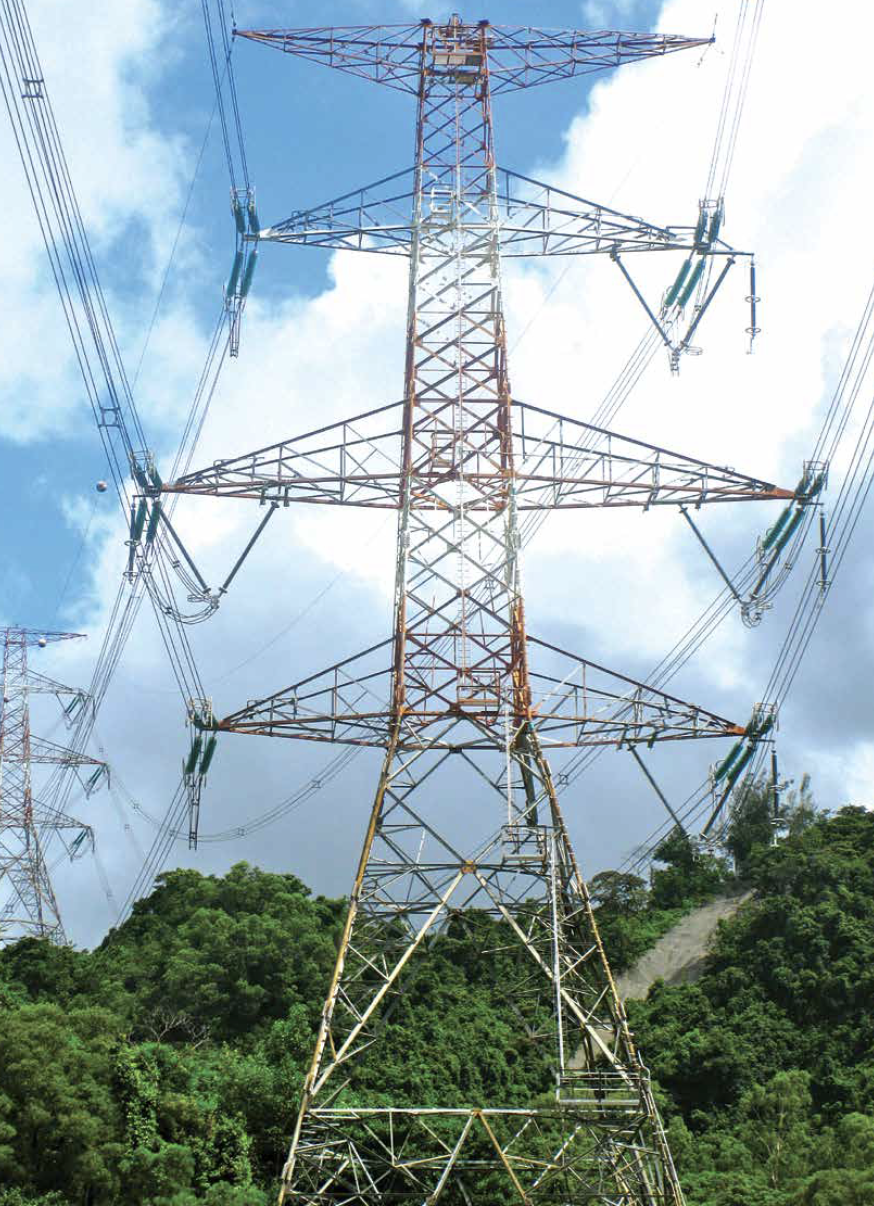
The EGLA concept dates back to the earliest stages of surge protection on power lines, although in subsequent years it became an internal gap that performed the same function. The reason for this long history is that air gaps have an excellent capability to withstand voltage and predictable breakdown at a very specific voltage level. It is therefore no accident that arrester designs over the years continue to make use of it and that there are currently millions of arresters in service that use the air gap to hold off line voltage until a surge appears. In the presence of a surge, they sparkover and protect equipment on the line.
When highly non-linear metal oxide varistors (MOV) are connected in series with the age-old air gap, the combination takes on unique features not available in earlier designs of gapped arresters. It is these unique and repeatable characteristics that make the externally gapped MOV arrester the ultimate in distribution and transmission line protection. The EGLA schematic in Fig. 1, for example, has been applied in Japan, Europe and Mexico as an IEC certified device for many years.
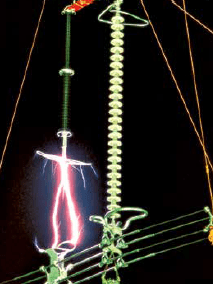
CLICK TO ENLARGE
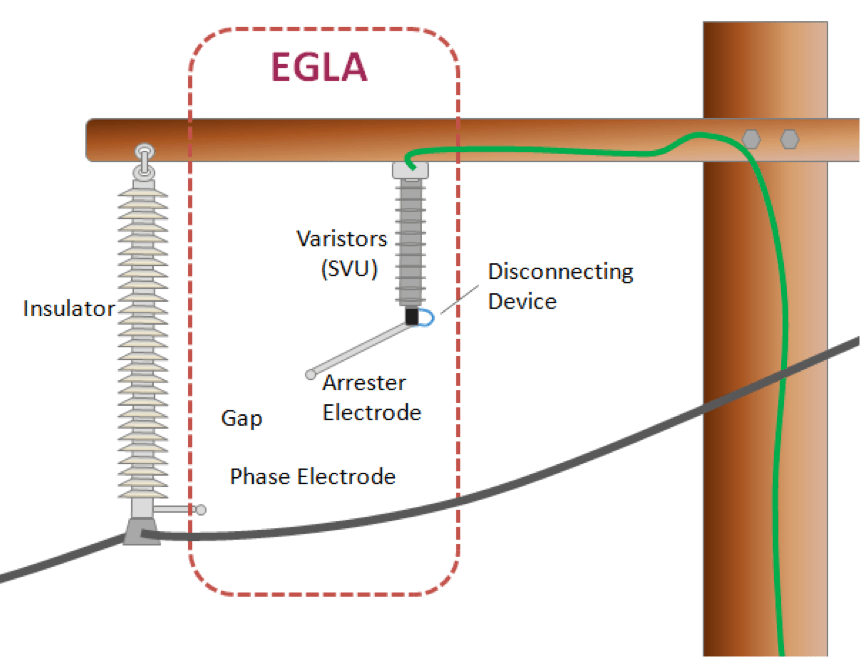
CLICK TO ENLARGE
The IEC type EGLA differs in that it is designed to only protect lines from lightning. This is achieved simply by increasing the gap spacing to a level that will not sparkover in the presence of switching surges. For systems above 230 kV, the IEC type EGLA does not need larger varistors to handle the energy associated with switching surges. It is characterized by a larger gap section and smaller tolerance in gap dimension than the EGLAs that are discussed below. This type of EGLA is also an arrester recognized by the IEC community and has its own specific test standard.
It is important to emphasize that the EGLA is being referred to in this article is a line arrester designed to be applied to eliminate insulator flashovers and not to protect sensitive oil-insulated equipment such as transformers. Because it is being used only to eliminate insulator flashover, the front-of-wave sparkover of this type of arrester is not relevant and not an application issue. Fig. 2 contrasts the front-of-wave characteristics of EGLAs and NGLAs. It also demonstrates that while EGLAs work well to eliminate insulator flashover, they cannot be expected to protect sensitive transformer insulation.
Mode of Operation of EGLAs
The well-coordinated gap and varistor of an EGLA work in conjunction to turn the arrester on and off. In spite of the high sparkover characteristic of the gap, it is more than adequate to protect the self-restoring insulation of line insulators – whether on a distribution system or even a 500 kV transmission system. When a lightning surge from a direct strike travels along the line and reaches a standard insulator, it will flashover the insulator and cause a power system fault. Such a fault can be prevented by using an EGLA to protect the insulator. In such a case, lightning will be directed through the arrester, which turns on immediately because the voltage is above the sparkover of the gap and turn on point of its varistors. Immediately following the lightning charge transfer, the varistors terminate all current flow and there is no power frequency follow current or fault. The robust withstand characteristics of line insulators, combined with the self-restoring capability of an EGLA, make it a perfect candidate for this type of protection.
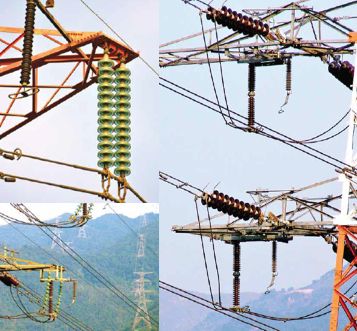
CLICK TO ENLARGE
Gap Function & Design Criteria
The gap of all externally gapped line arresters is the critical component in determining its turn on voltage. In this regard, it is important that this gap be large enough to withstand typical voltage swings during temporary overvoltage events yet small enough that it will always sparkover before the protected insulator flashes over. Fig. 3 is a graphic that outlines the various considerations determining gap settings for a unit that sparks over for both switching and lightning surges. The minimum acceptable gap setting of an EGLA is determined by three factors:
1. system voltage;
2. expected temporary overvoltage levels (TOV); and
3. safety factor.
The maximum acceptable gap is set by both the CFO (U50) of the protected system plus relevant safety factors.
Minimum Gap Spacing Rationale & Equations
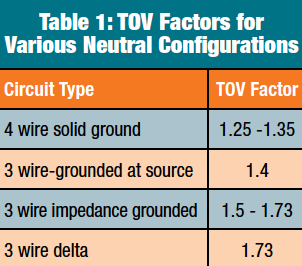
For switching and lightning type EGLAs, the gap needs to be spaced such that no AC power frequency voltage swings can cause it to spark over. To achieve this, the gap is set to withstand the maximum expected temporary overvoltage level plus a 20% safety margin. The maximum temporary overvoltage of any system can be determined accurately with transient modeling. It can also be estimated based on knowledge of the source transformer’s grounding configuration. This procedure is basically similar to selecting the MCOV rating of standard MOV type arresters. TOV factors recommended for this procedure are presented in Table 1 below:
Because there is no current flow through the arrester prior to flashover of the gap, the arrester does not influence gap flashover voltage. The minimum AC power frequency voltage at which the EGLA’s gap will flashover is:
where:
CFOpf 50% power frequency flashover voltage (kVrms)
Esys Max line-to-line voltage (kVrms)
TOVfactor TOV factor, as per Table 1
SF1 Safety factor (typically 1.2)
The minimum gap spacing can then be set from the minimum critical flashover voltage (U50) as determined in Eq. 1.
where:
Smin is the gap spacing (in inches)
Note: This applies for gaps <79 inches or about 200 cm (for greater spacing a gap factor is used).
Maximum Gap Spacing Rationale & Equations
The maximum gap spacing is set so there is little risk the insulator flashes over during a lightning surge. In order to achieve this, the CFO of the insulator being protected must be known and the CFO of the gap set at a safe level below CFOins. The relationship of the CFOgap and the insulator CFOgap is shown in Fig. 3.
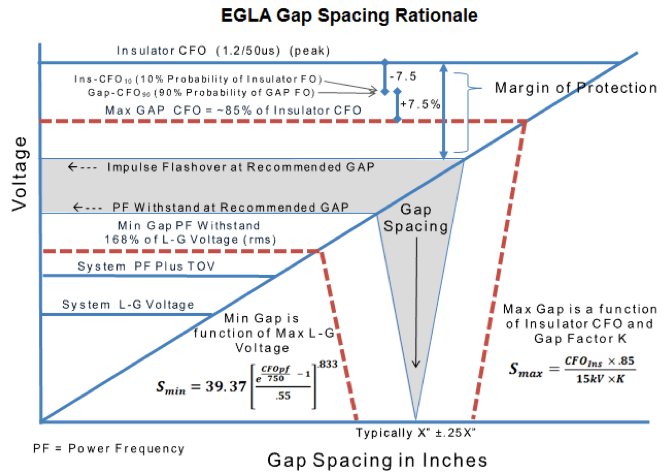
CLICK TO ENLARGE
Margin of Protection
Margin of protection is an important part of determining maximum gap spacing and minimum margin of protection is defined as:
MinMOP = CFO90 (U90) of gap ≤ CFO10 (U10) of insulator
where:
Gap CFO90 is the voltage level that represents a 90% probability of gap flashover.
Insulator CFO10 is the voltage level that represents a 10% probability of insulator flashover.
The recommended value for Gap CFO90 is 7.5% above gap CFO. The recommended value for Insulator CFO10 is 7.5% below the insulator CFO.
Given the relationship of maximum gap CFO, as above, once the CFO of an insulator is known, the gap CFO can be calculated as 85% of insulator CFO to meet the minimum margin of protection. It is a generally accepted fact that the impulse breakdown voltage of air is 560 kV/ft or 15kV/inch at STP.
Eq. 3 then describes the relationship of gap spacing (in inches) and gap CFO
where:
Smax is the maximum gap spacing in inches
CFOins CFO of insulator in kV peak
Vbreakdown Pos. impulse breakdown voltage of air (accepted as 15kV/inch at STP)
K Gap factor (1 for rod to plane gaps)
Other Gap Spacing Considerations
Fortunately, if a faster surge arrives at the arrester/insulator, both devices will flashover at higher voltages/ As such, once the spacing is set for a standard wave, it will work for faster waves as well. If the installation is applied at higher altitude, gap spacing must increase as a function of air pressure. Moreover, if the electrodes or the arrester can move relative to one another, a second safety factor must be factored in to the equation to account for such motion.
The gap can also be affected by environmental conditions, but this applies as well to the insulator in parallel with the EGLA. If the gap is set to flashover before the protected insulator, it will remain so under most weather conditions. However, if the parallel insulator is so severely affected by pollution that it flashes over at power frequency, the arrester cannot protect against this.
Lastly, as with all transmission line arresters, lead management is a significant consideration. In the case of an EGLA, the electrodes are generally shorter than leads and electrode management is therefore less a challenge than in the case of the leads of an NGLA.
Impact of Incorrect Gap Spacing
Incorrect gap spacing can lead to an array of problems. These will vary depending on whether the spacing is set below the minimum level or above the maximum level. If the gap spacing is installed below the minimum, the risk of flashover during a temporary overvoltage event increases and could lead to arrester damage or even failure.
If the gap is installed with its separation greater than the maximum recommended level, the insulator could flashover before the gap sparks over. While this will not cause arrester failure, the flashover could result in a momentary or even long-term outage. Fortunately, EGLA gap spacing is quite flexible. For additional insight, see the various system voltages and recommended gap settings shown in Table 2.
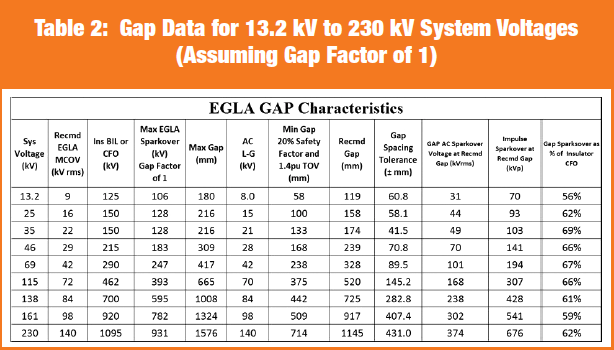
Arrester Overload Considerations
In arrester overload situations, the optimum configuration would be to use a disconnector or failure indicator, as shown in Fig 4.
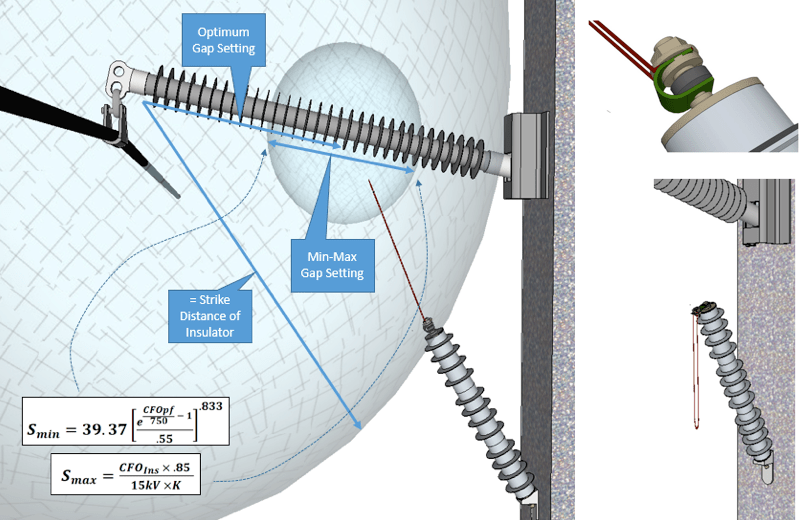
CLICK TO ENLARGE
Function & Design of Electrodes
Although the electrodes might seem a simple component in this type of arrester, they fulfill important functions, such as:
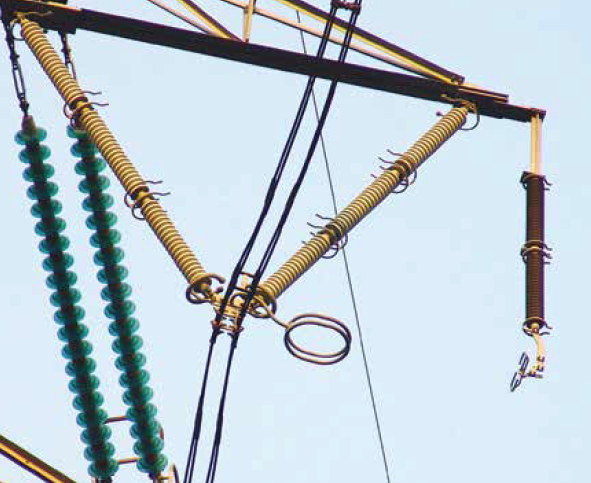
CLICK TO ENLARGE
1. Creating a durable location on the arrester or phase conductor for any arc due to a surge to land on without damage;
2. Allowing for adjustability of gap spacing, when needed;
3. Offering a surface that is equidistant from the opposite electrode given periodic movement of insulator or arrester;
4. Producing a shape that has consistent and predictable flashover;
5. Generating full CFO to the system upon failure if the electrode and EGLA is also equipped with a disconnector (as in Fig. 4).
Note that every EGLA needs at least two electrodes and that the second electrode can be part of the existing system but not necessarily a separate component of the arrester. The electrodes must also meet additional requirements to provide the functions stated above, including:
1. Mechanical strength;
2. Non-ageing finish;
3. Shape conducive to system voltage and potential swinging of arrester or phase conductor;
4. Conductivity adequate for surges but not power frequency current;
5. Acceptable failure mode;
6. Sufficient withstand to wind loads.
Series Varistor Unit (SVU)
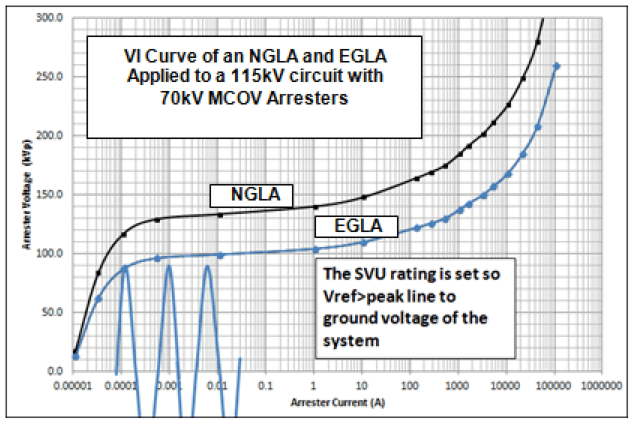
CLICK TO ENLARGE
The varistor component of an EGLA, also known as a series varistor unit (SVU), is comprised of non-linear MOV disks and performs a single basic function, namely to limit surge current. In effect, it terminates the surge event as the surge drops in voltage. The SVU is for all practical purposes an NGLA.
Voltage Rating of SVU
The most important consideration when selecting the voltage rating of the SVU is the maximum line-to-ground voltage the system will experience. As demonstrated in Fig. 5, the turn on level of the SVU is set just above the peak line-to-ground voltage of the system. As a general rule, the 1mA Vref of the SVU must equal or exceed peak line-to-ground voltage. The discharge voltage of the EGLA is the sum of the voltage across the gaps, the varistors and the leads. In most cases, this voltage is lower than in the case of a standard arrester so it can easily clamp the voltage well below the CFO of the protected insulator.
Energy Considerations of SVU
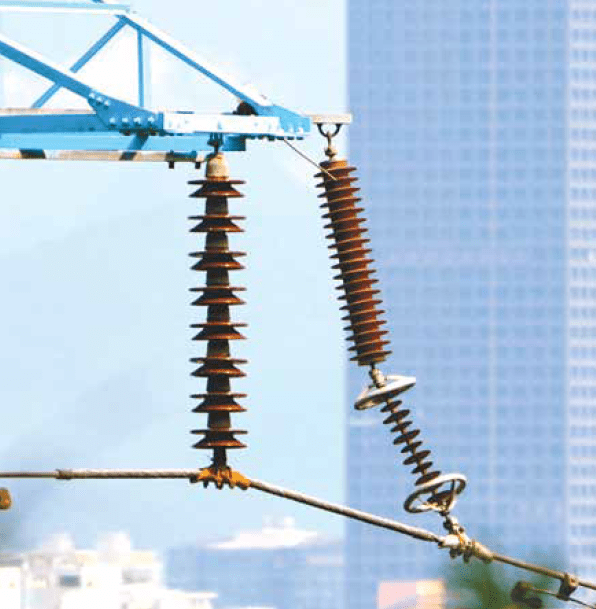
CLICK TO ENLARGE
Shielded Systems Below 230 kV
For shielded systems below 230 kV that are not equipped with large capacitor banks, the energy handling requirements from a lightning surge typically exceed switching surge requirements. Distribution class arresters are therefore commonly used for this application.
Shielded Systems Above 230 kV
In the case of this type of system, switching surge energy handling capability needs to be considered. For longer lines, switching surge capability can exceed lightning charge transfer requirements. A basic system study or the rule of thumb equations from IEEE C62.11 can be used to make the necessary determinations. It is even possible that station class disks may need to be used for such applications.
Unshielded Systems
For distribution systems that are typically unshielded, a standard distribution arrester will suffice for the SVU of an EGLA. For higher voltage systems where current sharing between arresters is an option, higher charge transfer disks may need to be used.
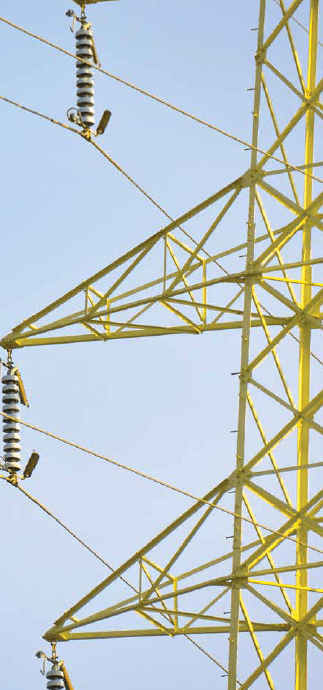
CLICK TO ENLARGE
SVU Housing & Leakage Distance
Because the SVU does not have a voltage stress along its surface, it does not require the long-term power frequency withstand capability of a typical arrester. Normally, arresters have some voltage stress along the surface over their full service life. This stress demands that the arrester have a longer surface distance than would typically be needed for the internal components. The only time the SVU experiences a voltage stress is during a surge clamping event. At other times, the voltage difference between the two ends of the SVU is virtually zero.
Because there is no voltage stress along the length of the SVU over its lifetime, leakage distance can in most cases be equal to strike distance. For contaminated environments, leakage distance may need to be somewhat longer. Reduced material requirement is in fact an area of opportunity to make such arresters more sustainable from an environmental viewpoint.
Besides providing leakage distance, the housing is also the major environmental seal of the SVU. Moisture ingress in the presence of voltage stress is a major challenge for the housing of any SVU. Even though the AC stress is minimal, it is still critical that the SVU remain well sealed.
Guarding Against Wildlife Intrusion
For arresters applied above 46 kV, the SVU becomes long enough so as not to have any serious concerns about animals bridging the ground to phase electrodes. However, wildlife can still get across the gap. In such cases, the resulting leakage current will likely kill the creature but not cause an outage. It is unlikely the arrester will fail in such instances since the current is limited by the varistors.
EGLA Arrester Voltage Rating Considerations
The voltage rating of surge arresters can at times be confusing because the standards and data sheets for nongapped arresters routinely discuss two ratings: MCOV and Duty Cycle Rating. The only rating that really matters to users, however, is the MCOV, or Uc in the IEC area.
In the case of EGLAs, the voltage rating that really matters is also MCOV. This is the maximum voltage the arrester can withstand over its service life and still withstand any TOV events as these arise. This level is claimed by the manufacturer and has been verified as part of the operating duty test. An 8.4 kV MCOV of an EGLA is the equivalent of an 8.4 kV MCOV non-gapped arrester. Similarly, the 70 kV MCOV rating of an EGLA is exactly the same as the 70 kV MCOV rating of a non-gapped arrester.
Benefits
The benefits of an EGLA are numerous. Because of the gap, losses are zero and there is no chance of a long-term fault due solely to the arrester. Construction is also more sustainable due to less material requirements. Moreover, the life of such arresters is virtually infinite because of the minimal AC voltage stress placed on the SVU. A more subtle benefit is that less rubber can be used on the housing because leakage distance is optional. Also, with no voltage applied to the varistor after an impulse, the MOV blocks do not need sophisticated formulation and processing as in some other arrester applications.
In the future, transmission lines everywhere will be better protected from momentary outages by using arresters. Based on its advantages, the EGLA will probably be the arrester of choice for this type of application.
Note: Mr. Woodworth wishes to acknowledge the contribution of NYSERDA for partially funding this project under Shawn Allen of Ceralink.