The evolution of composite insulators since their inception in the 1970s shows that market experience for apparatus insulators has been much different than for line insulators based on this technology. While hollow composite insulators have never suffered from any documented single mode of failure, such as brittle fracture, and service experience has been positive, the rate of their application has proven far slower than initially anticipated. One reason for this is that hollow insulators are typically purchased by manufacturers of HV breakers, transformers, arresters, terminations and other substation apparatus. For these types of customers, purchase price – not life cycle cost – has been the driving factor. Therefore, unless directly specified by the end user, there has been a tendency to continue relying on traditional porcelain, whose cost (especially at lower transmission voltages) has typically been lower.
However, given the power industry’s focus on safety and minimal maintenance and with more information on long expected service life, application of hollow core composite insulators has been undergoing rapid growth. While only tens of thousands of such units were in service in 1993, the population has soared and now numbers in the millions.
This edited past INMR article was based on a contribution from experts at STRI as well as at the power system arm of ABB (now Hitachi Energy). It explored efforts to assess service performance of hollow composite insulators operating under different applications and service conditions.
A total of 11 sites of interest were selected based on local service conditions and criteria such as: relatively long time in service; diverse heavily-polluted environments (e.g. deserts, industrial, coastal) preferably combined with high UV radiation levels; less polluted environments (e.g. inland) but with low temperatures as well as frequent rain; AC and DC applications. This resulted in investigating insulators at substations in seven countries: Argentina, Australia, China, Iceland, Denmark, Oman and Sweden. These inspections eventually covered sites with all of the five different environments defined in IEC 60815-1, i.e. desert, coastal, industrial, agricultural and inland. More than 50% of the climates studied were classified as humid while about half the sites were in areas with heavy to very heavy Site Pollution Severity (SPS), according to IEC 60815-1. Moreover, 4 sites were located in areas with high levels of UV radiation but below 1000 m altitude. The apparatus insulators inspected represented a range of voltage classes from 145 kV to 420 kV AC and from 400 kV to 500 kV DC. Total operating time of these insulators varied from 2 to 17 years.
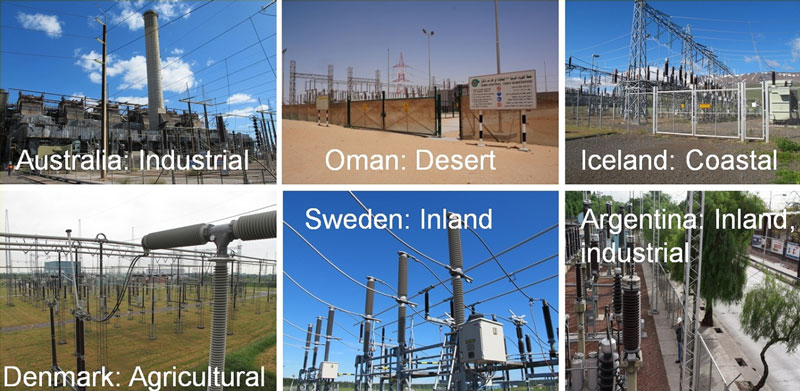
Inspection Procedure & Results
A standard form of data collection was developed and included data on climate and environment at the inspection site as well as existing service experience with standard porcelain-housed equipment (where available). The inspection procedure included: careful, close visual inspection with photography; ESDD/NSDD measurements according to IEC 60815-1 (ESDD measurements were performed directly on composite apparatus insulators according to the latest CIGRE Brochure, i.e. average values were weighted for different parts of the insulators); hydrophobicity measurements were done according to IEC 62073 with measurements of Wettability Class (WC).
Results of Visual Inspection
A total of 58 insulators at 11 sites were inspected using the special STRI Guide for assessing deterioration and damage to apparatus insulators. Most were in good condition, with no observable deterioration, although a few minor surface marks were found e.g. mechanically induced, although such marks will not influence safe operation. In regard to biological growth that has also been observed, it has been shown that algae do not feed on silicone rubber and are only a surface phenomenon. Moreover, past researchers have concluded: “The risk for flashover due to biological growth is rather low because in order to lead to flashover, the resistance of the pollution layer should be relatively low. However, biological growth normally occurs in relatively clean areas leading to a situation where either the insulator will be hydrophilic, but clean, i.e. with high resistance, or it will be contaminated but free of biological growths and therefore hydrophobic (due to recovery of hydrophobicity) with high resistance”.
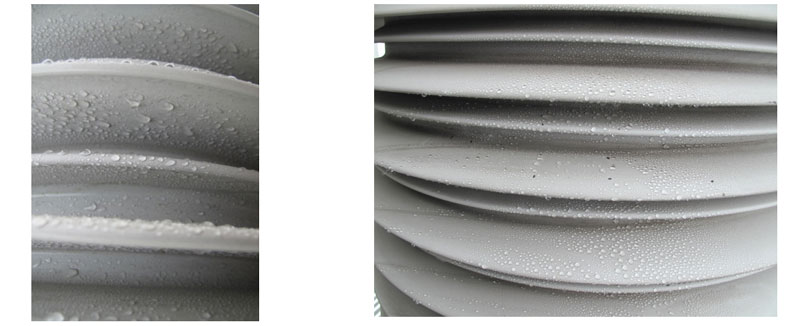
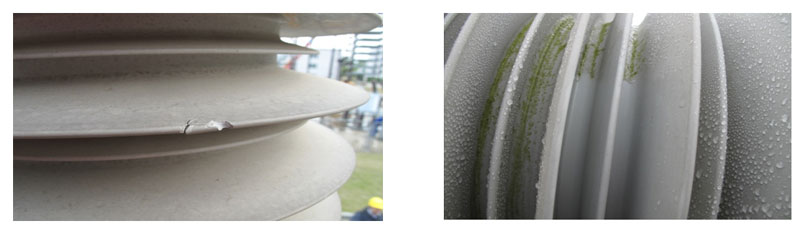
Results of Pollution Measurements (ESDD/NSDD)
Pollution was sampled from small areas (about 12 cm2) in different locations along insulators being assessed. Typical areas used were the top larger diameter shed, the bottom larger shed, a trunk larger shed, and similar for smaller diameter sheds. It should be noted that a stochastic single collection of ESDD and NSDD samples is not sufficient to estimate site pollution severity (SPS). According to IEC 60815-1, ESDD/NSDD measurements for estimating SPS must be performed on ‘standard’ ceramic insulators and at least over a period of one year, following the special procedure. A single measurement of ESDD and NSDD performed on composite apparatus insulators is therefore only a rough estimation of their pollution state on that particular day. Moreover, the pollution state of the insulator will vary over time, depending on a number of factors, e.g. wind, rain and season.
In order to obtain average ESDD/NSDD levels from small sampling measurements, as in this case, it is necessary to estimate the percentage of the entire insulator that corresponds to each typical measurement zone so as to make a weight-corrected calculation. The trunk area, for example, is a small part of the whole insulator compared with the large top shed area. At the same time, it is noteworthy that some insulators inspected were exposed to regular cleaning by the user utilities – a procedure not really needed and in fact not recommended by the manufacturer. If the insulator is washed regularly (e.g. from once a year to once every few years) the level of ‘instantly-measured’ ESDD and NSDD might be lower. For this reason, it was seen as beneficial to collect past washing data from end users.
The findings from measurement of ESDD/NSDD are shown in Figures 4 and 5 while Fig. 6 offer examples of insulators contaminated in different manner and Fig. 7 features some of the most contaminated insulators. The place with the highest pollution in this assessment study was a substation in Argentina located in the middle of a busy four-lane highway from each side of the substation (see Fig. 8).
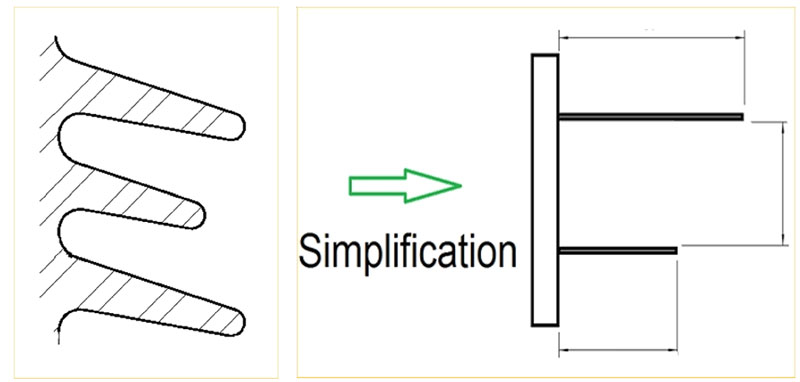
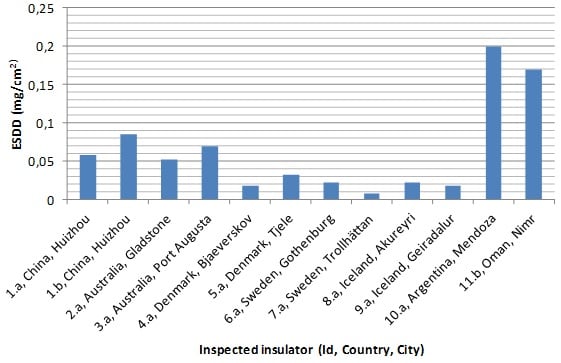
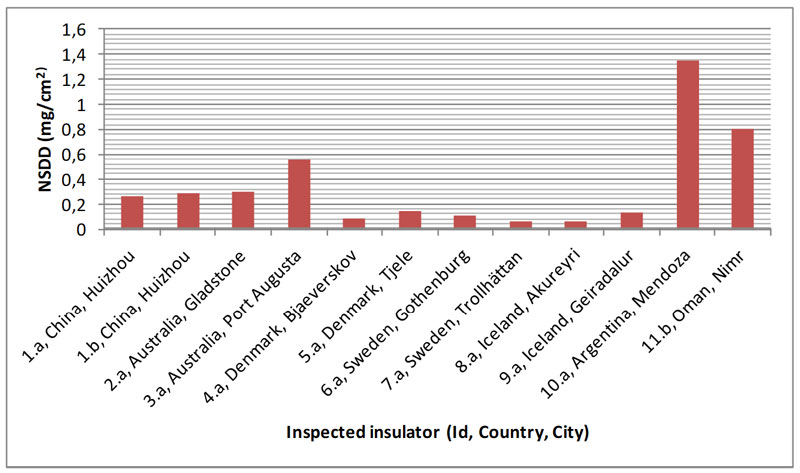
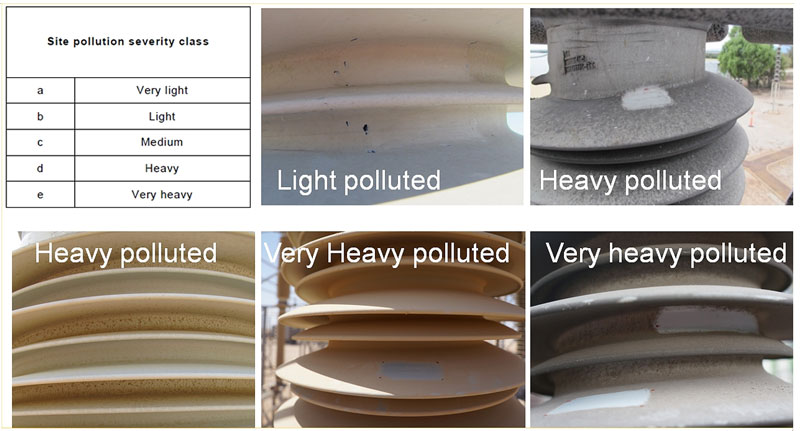
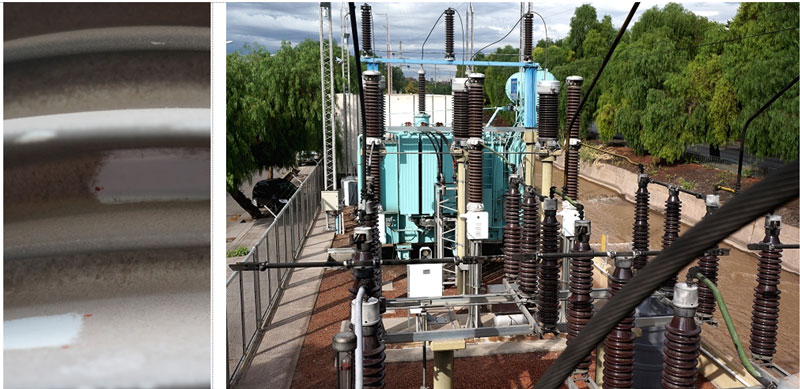
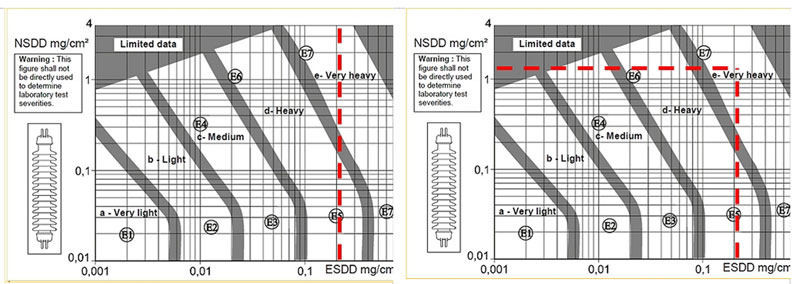
Results of Hydrophobicity Measurements (WC)
One of the special features of silicone rubber insulators is that, even if surface hydrophobicity is temporarily lost or reduced due to persistent wetting and contamination, it recovers in a relatively short time. In this regard, it is important to note that most of the insulator inspections were performed only a few hours after the substation was de-energized and therefore did not benefit from the influence of such recovery. In this regard, all findings on hydrophobicity can be considered as typical of real service conditions.
In some industrial environments, the interaction of the pollution layer and silicone rubber can actually lead to ‘super-hydrophobic’ properties and this observation should be investigated further. Still, in general, it can be seen from Fig. 11 that, on average, wettability class (WC) of the insulator sampled was typically between 1 and 3, where Class 1 is completely hydrophobic.
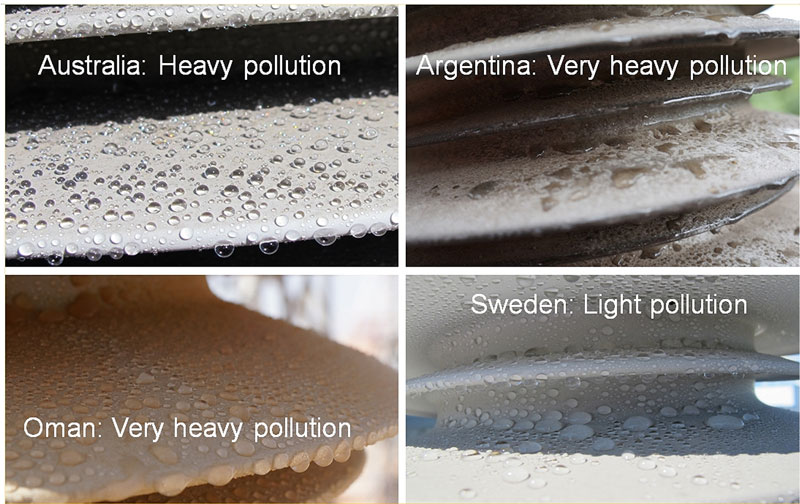
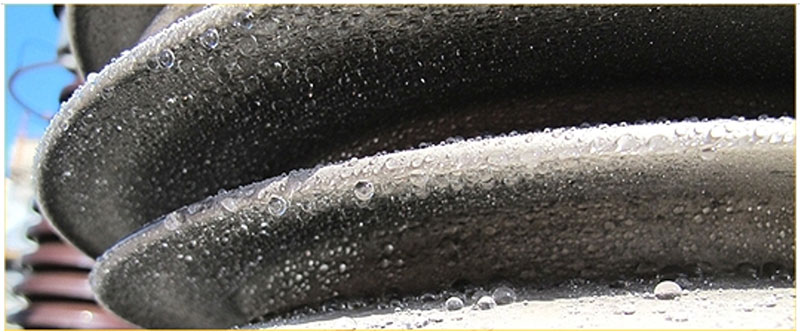
Summary & Conclusions
Careful inspection was conducted on a total of 58 hollow apparatus insulators with helically extruded, HTV silicone rubber housings and operating at 145 kV to 420 kV AC and ±400-500 kV DC. These insulators had been in service from as little as 2 to as long as 17 years, with most at least 5 years in operation. Among this sample, 5 per cent were installed horizontally and 95 percent operated in a vertical position. Ten per cent were used in DC and 90 percent at AC voltages.
The assessment survey covered all typical environments defined by IEC 60815-1 (desert, coastal, industrial, agricultural and inland) and several of the substations visited reflected a combination of two or more of these environments. The survey also covered 4 of a total of 5 Site Pollution Severity (SPS) classes, as defined in IEC 60815-1 with the only pollution class not represented being ‘very light’. About 50% of the insulators were located in areas with ‘heavy’ to ‘very heavy’ SPS, according to IEC 60815-1. No significant deterioration was observed on any of the 58 insulators inspected. None had lost their hydrophobic properties – even to an intermediate level – and all had an average WC level better than 4, with the majority between WC 1-3 (where WC 7 is completely hydrophilic and WC 1 is completely hydrophobic).
Based on the insulators inspected, all having helical extruded HTV rubber sheds, the following conclusions can be drawn:
• No ageing or deterioration of any significance;
• Good performance with respect to pollution and ageing;
• No signs of ageing of silicone rubber in direct sunshine in areas known to have high levels of UV radiation (i.e. Argentina, Australia & Oman).
It is also noteworthy to point out that it is feasible to make an accurate assessment of the condition of composite insulators using only the simple diagnostic methods/tools utilized in this survey (i.e. visual inspection, hydrophobicity measurement and pollution sampling).