Live-line maintenance relies on insulated tools to manipulate network components under full service voltage. This has proven an effective low-risk practice at utilities worldwide. But behind this safety record is the need for preliminary inspection and evaluation of what has to be done. There has to be a check to determine if there are too many defective discs in a string of porcelain insulators. Similarly, guides for visual inspection of polymeric insulators help identify units that may be too degraded to support line voltage during a change-out. Also, special cameras show partially punctured ceramic shells as well as composite insulators with a distinctive thermal signature indicating that they may be electrically weak.
This past edited contribution to INMR by Dr. William Chisholm discussed additional considerations that may apply in certain severe service environments.
[
Risk of live insulator replacement is managed based on whether the intact portion of a string or a composite long rod can support a switching surge once the tool configuration has been installed and the worker is in place. Switching surge overvoltages are further controlled using ‘hold-offs’, whereby automatic reclosing is disabled so that the line is not re-energized in case of a fault. Surge arresters also limit magnitudes of such faults. If hold-offs or arresters are not used, a conservative value of 3.5 per unit, i.e. 3.5 times the crest of the line-to-ground voltage, is assumed by regulators such as OSHA for minimum approach distance (MAD).
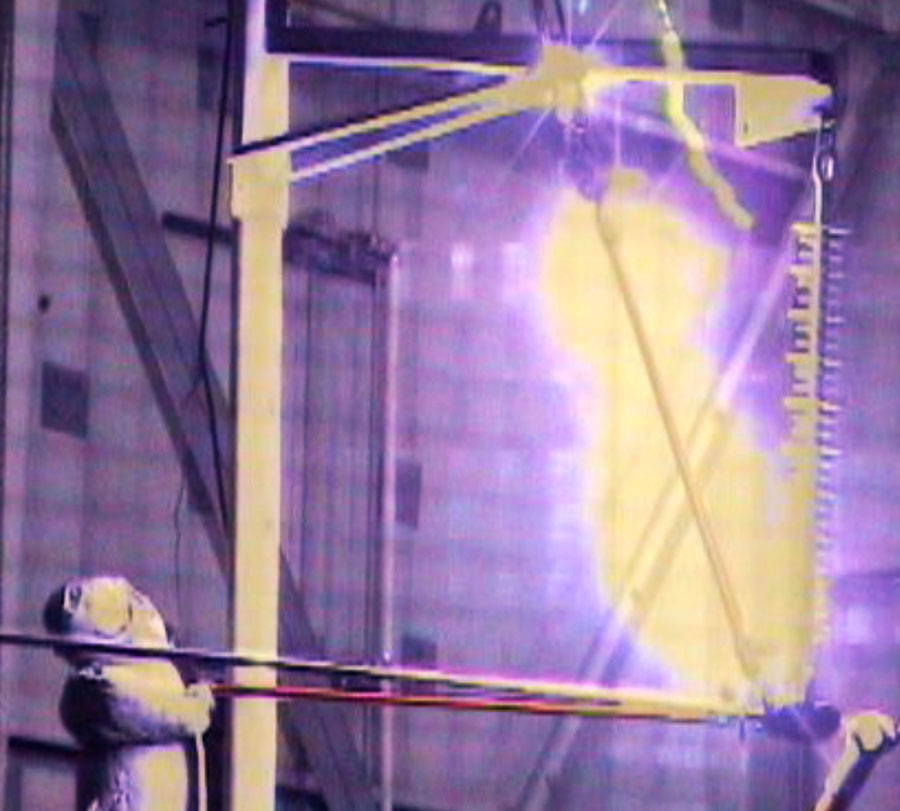
Still, there are occasional surprises when evaluating MAD. For example, conditions on new lines in western Canada recognized a 5% reduction in switching surge strength (or 5% increase in MAD) at altitudes of 1500 m. Yet one concern was that some areas had frequent periods with high ambient temperature (20-30°C), low air pressure (< 89 kPa) and little moisture in the air (e.g. relative humidity < 20%, dew point temperature less than 0°C, or absolute humidity < 5 g/m3). Here, an appropriate reduction factor for switching impulse strength was 18% during warm, clear summer afternoons that might otherwise be ideal for live line work. It is a bit counter-intuitive that dry air has lower flashover strength than moist air at the same pressure and temperature – especially since wetted insulator surfaces are prone to leakage current and dry-band arcing. However, the process for atmospheric correction is found in both IEEE Standard 4 and IEC 60060.
[
Not long ago it became apparent that live line tool dimensions that respect guidelines to avoid flashover under switching surge conditions can still flashover under normal line voltage given specific outdoor conditions. Data from Canadian utilities, for example, suggested such problems at reduced pressure and low temperatures (0 to -20°C). Flashovers during live work occurred at the negative peaks of the AC wave, starting at the worker’s hands and developing along the length of the tool to the energized conductor. This peak-of-wave behavior is a symptom of contamination rather than switching surge flashover and indeed utility fault recorders confirmed there was no switching activity that could have provoked these incidents.
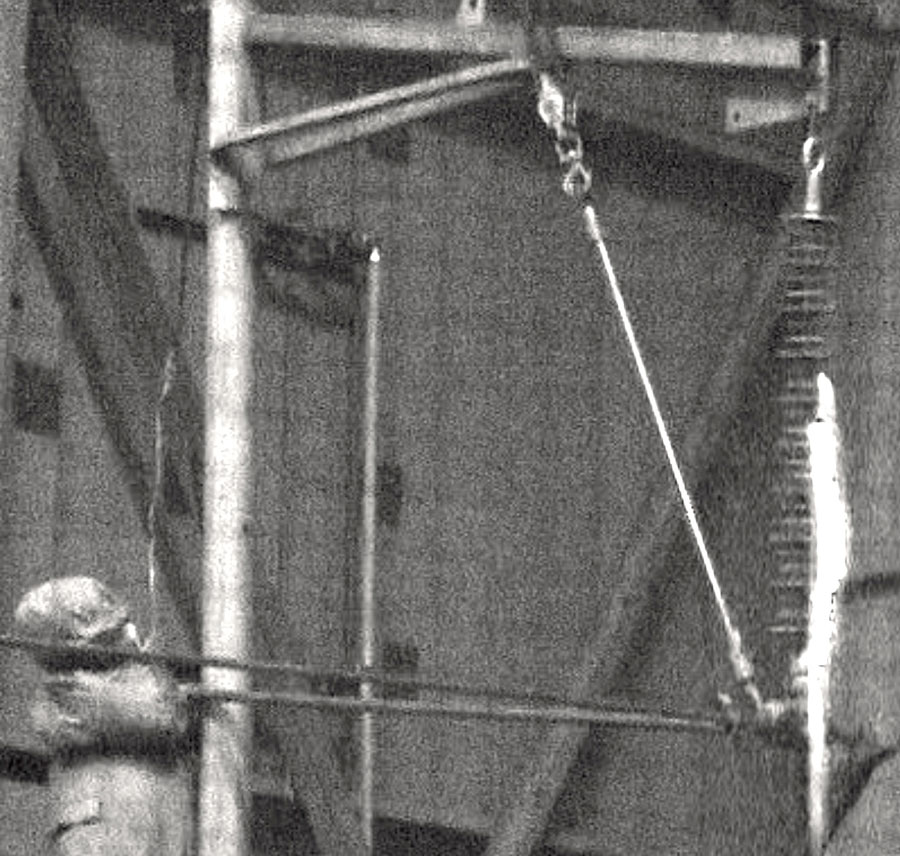
signature under line voltage. Reduced flashover path and strength means live replacement should not be undertaken.
Live-line tool flashover as a result of surface contamination and wetting or ice accretion has been explored at several high voltage laboratories. Half of these events could be traced to the vulnerability of insulators to depressed flashover voltage just below the freezing point, where surface layers of frost change to water and increase electrical conductivity by a factor of 100 or higher. Most industrial experience with these ‘cold fog’ flashovers is at pre-contamination levels that exceed 0.2 mg/cm2 ESDD. Tests showed that live-line tools, cleaned before use, usually have ESDD levels of less than 1 microgram/cm2 – near the minimum detectable level.
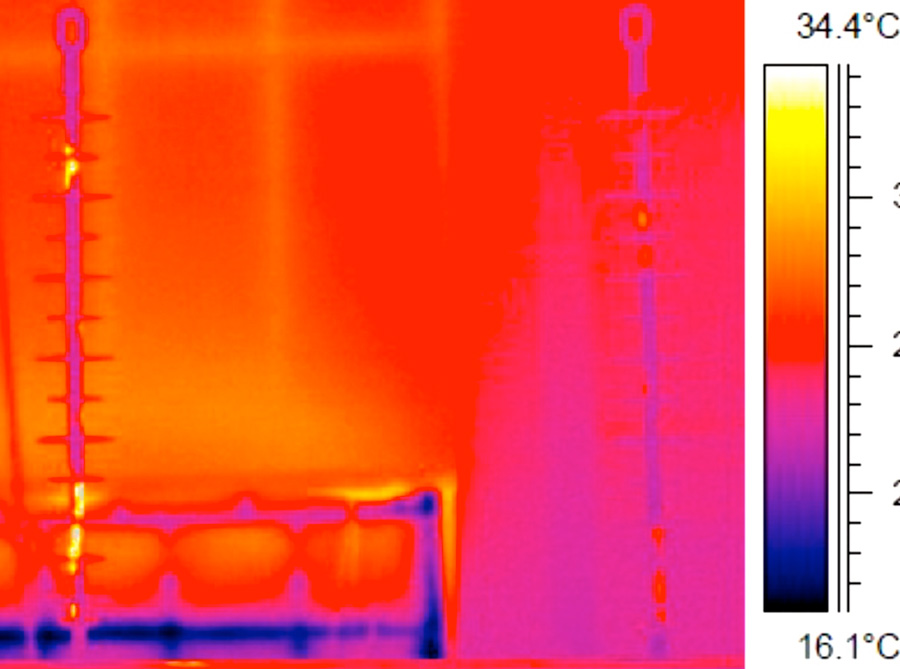
On outdoor insulators, electric stress is typically 25 to 50 mm/kV of line to ground voltage, or 20 to 40 kV/m of leakage distance. Live-line tools do not use sheds or protrusions that are difficult to clean and inspect and, as such, leakage distance equals dry arc distance. Tools are thus operated at stress levels of up to 100 kV/m of leakage distance, i.e. 2 to 5 times higher than insulators. As long as the tools are clean and dry this does not pose a threat. But if they are moderately contaminated and coated with ice that turns to water, difficulties may arise.
[
Live line tools are handled with leather glove covers that absorb salt pollution and moisture and also prove rather effective in transferring salt and moisture onto live line tools in a special way. The wet glove leaves a thin, smooth coating of salt water that evaporates quickly – just like wiping down a car with a chamois after washing it to eliminate water spots. This effect proves helpful to researchers when reproducing flashover problems on live line tools as it gives a thin, uniform ESDD of 1 to 3 micrograms/cm2 on FRP surfaces, without needing kaolin to stabilize the deposit.
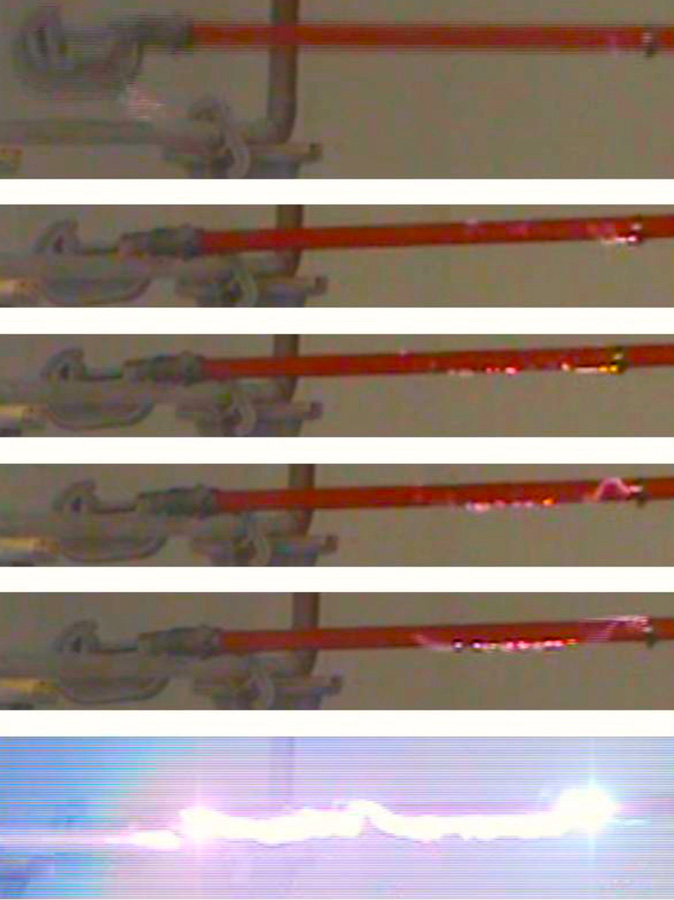
(Source: DEIS December 2014 Special Issue on Cross-Disciplines in Outdoor Insulation, Vol. 21, No. 6, pp. 2628-2633).
Technical papers in past issues of IEEE DEIS Transactions have discussed how contamination and ice bridging, rather than switching surge performance, now govern insulation coordination of EHV system insulation in many regions. A few articles also described recent research on live-line tool flashovers in freezing conditions, even though such a problem was first noted back in 1997. This industry is still coming to terms with the fact that live-line tools might satisfy their switching surge requirements yet still be vulnerable to contamination flashover. This calls for added caution, particularly during winter.
[