En un cable HVAC, la distribución del campo eléctrico depende de las capacitancias que son dominadas por la permisividad del material de aislación que es estable con la temperatura. Por lo tanto, cuando se prueban dichos cables, no se requiere especificar un ∆θmax. Por el contrario, la distribución de campo en un cable HVDC se determina mediate la resistividad del material de aislación, que varía enormemente con la temperatura. Esto genera la necesidad de controlar la diferencia de temperatura, ∆θmax, durante las tensiones térmicas representadas por el ciclo de carga en una prueba. En operación, un cable HVDC también experimenta sobrevoltaje SI/LI que se superpone sobre el voltaje de servicio DC. Así, para simular de manera apropiada una condición en servicio, superponer un sobrevoltaje de maniobra y un transitorio de rayo sobre el voltaje DC de operación, es un requerimiento estándar.
Este artículo editado el 2017 para INMR, escrito por Hong He y W. Sloot de KEMA Labs en los Países Bajos, describe un circuito de prueba con dos sistemas de prueba por separado, un generador DC y un generador de impulso, conectado con un sistema de cable de prueba ubicado entre los dos. El sistema de cable de prueba consta de tres piezas de cable de XLPE HVDC de 50 m ensambladas con dos terminaciones exteriores y dos uniones. Una complejidad mayor de este arreglo es evitar el daño a cada sistema de prueba debido a la presencia del otro. Por lo tanto, se instala una brecha entre esferas para bloquear el voltaje DC del generador de impulso con una impedancia de amortiguación fija para proteger el generador DC de los transitorios muy rápidos.
Modelo físico térmico
Una diferencia de temperatura surge a través del cable y la distribución de temperatura por dentro se puede medir con termocuplas o calcular con un modelo numérico. En la Fig. 1 se muestra un circuito térmico equivalente para el cable, donde
Q ̇, es la tasa de transferencia de calor (flujo de calor), W;
θc, θcs, θi, θis, θis, θamb, es la temperatura del conductor, de la pantalla del conductor, de la aislación, de la pantalla de aislación, de la funda y la temperatura ambiente, °C;
Δθcs, Δθi, Δθis, es la caída de temperatura en la pantalla del conductor, la aislación y la pantalla de aislación, respectivamente, K;
Δθc-is, es la diferencia de temperatura desde el conductor a la pantalla de aislación, K;
Tcs, Ti, Tis, es la resistencia térmica de la pantalla del conductor, la aislación y la pantalla de aislación, respectivamente, K·m/W;
Ts, es la resistencia térmica en total desde la funda metálica hasta por sobre la funda, K·m/W;
Ttm, resistencia térmica del material de aislación térmica externa, K·m/W;
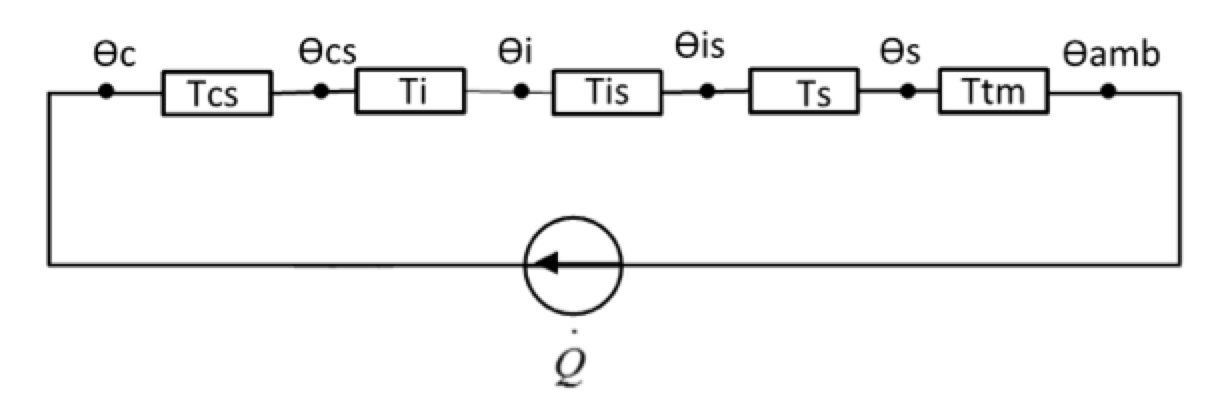
La diferencia de temperatura a través de la pantalla del conductor, la aislación y la pantalla de aislación se calcula de la siguiente manera:
θis, and θc se miden directamente con termocuplas. La diferencia de temperatura general desde el conductor a la pantalla de aislación es, por lo tanto:
Según la Ec. (2) y la Ec. (4):
La Ec. (5) es la fórmula simple para calcular Δθmax. Ya que los alrededores también influyen, la principal caída de temperatura en un cable está entre la superficie del cable (funda) y el ambiente (θs – θamb). Con el fin de controlar la ∆θi dentro del límite de Δθmax, el material de la aislación térmica externa (por ejemplo, burbuja de plástico) se aplica para minimizar la influencia del ambiente. Este material de aislación térmica ayuda a ajustar la Ttm según el diseño diferente del cable y la condición de los alrededores.
Medición de temperatura & ciclo de carga
Con el fin de monitorear el ambiente térmico del sistema de cable HVDC, se ubicaron termocuplas en un total de más de 20 ubicaciones diferentes en un cable de referencia y un cable de prueba. El cable de referencia se debe instalar próximo al cable de prueba para asegurar un ambiente térmico igual. Se monitoreó la temperatura del conductor del cable de referencia (según la θc máxima nominal, por ejemplo, 70°C) para guiar la misma corriente aplicada al cable de prueba simultáneamente. Al aplicar la Ec. (5), se calculó la Δθmax especificada y se monitoreó durante el ciclo de carga. En la Fig. 2 se muestra un ciclo de carga típico de 24 horas.
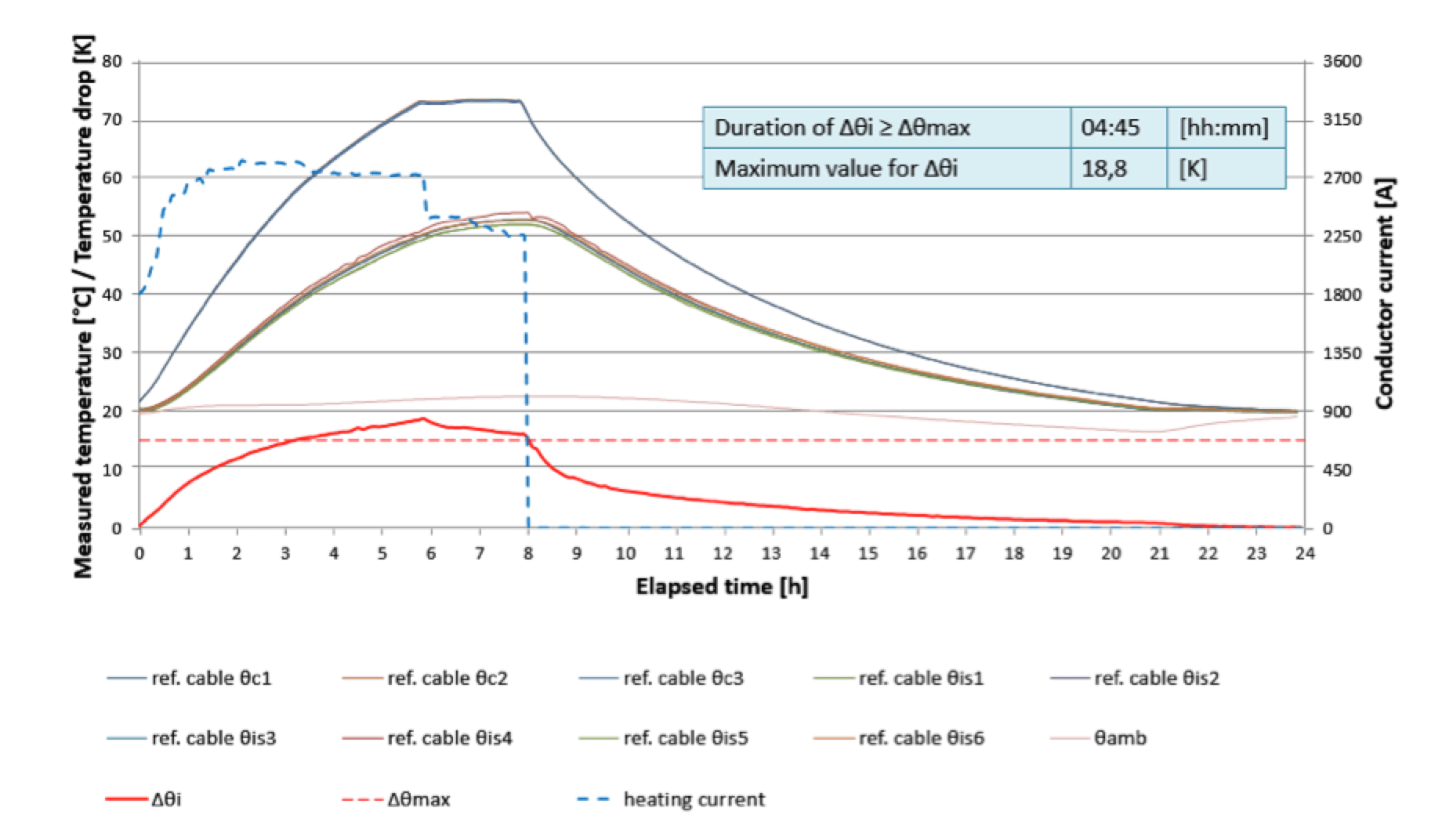
Las Figs. 3 y 4 demuestran esquemáticamente la sección transversal del cable (ej.: 2500 mm2) y las ubicaciones de la temperatura medida, respectivamente.
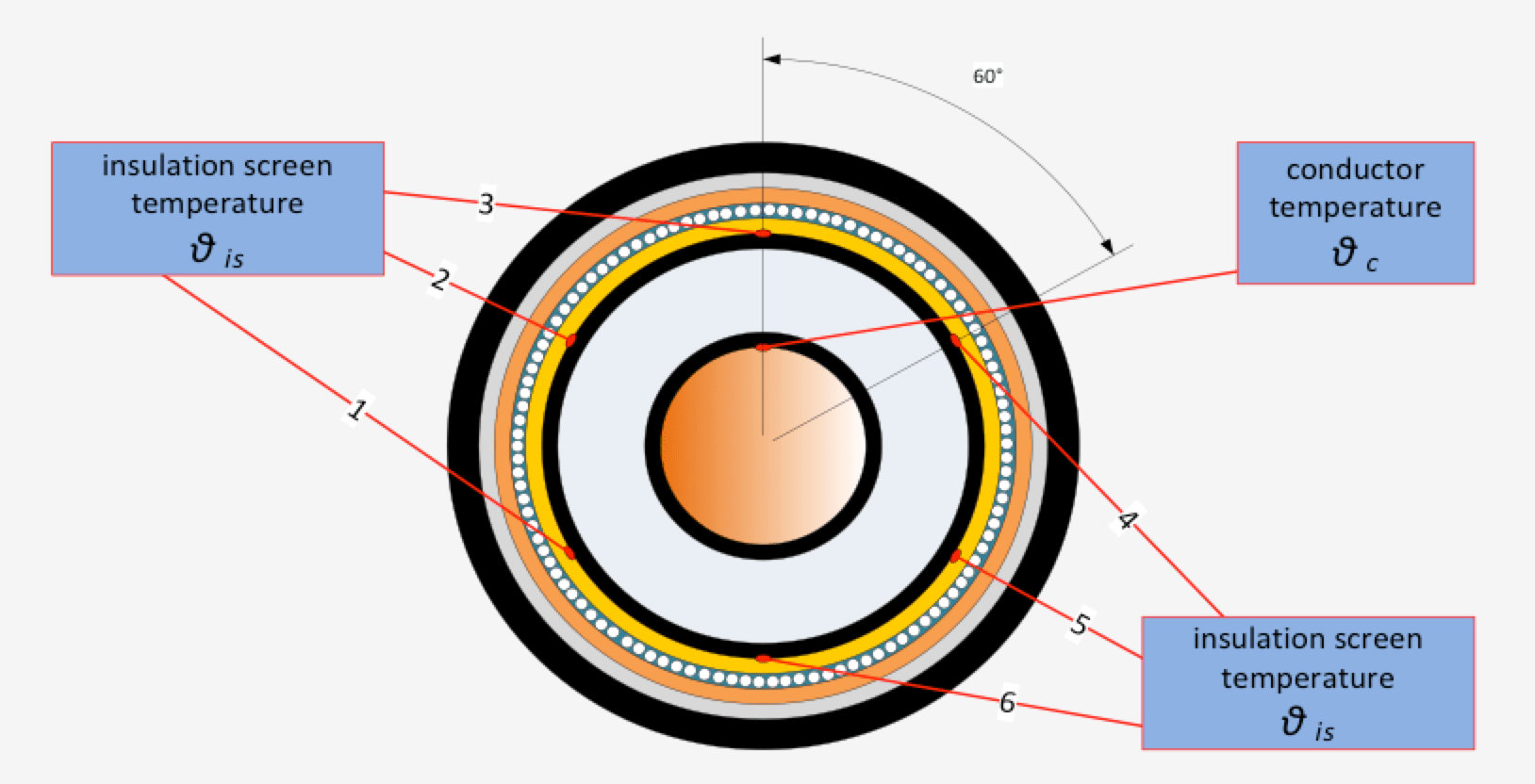
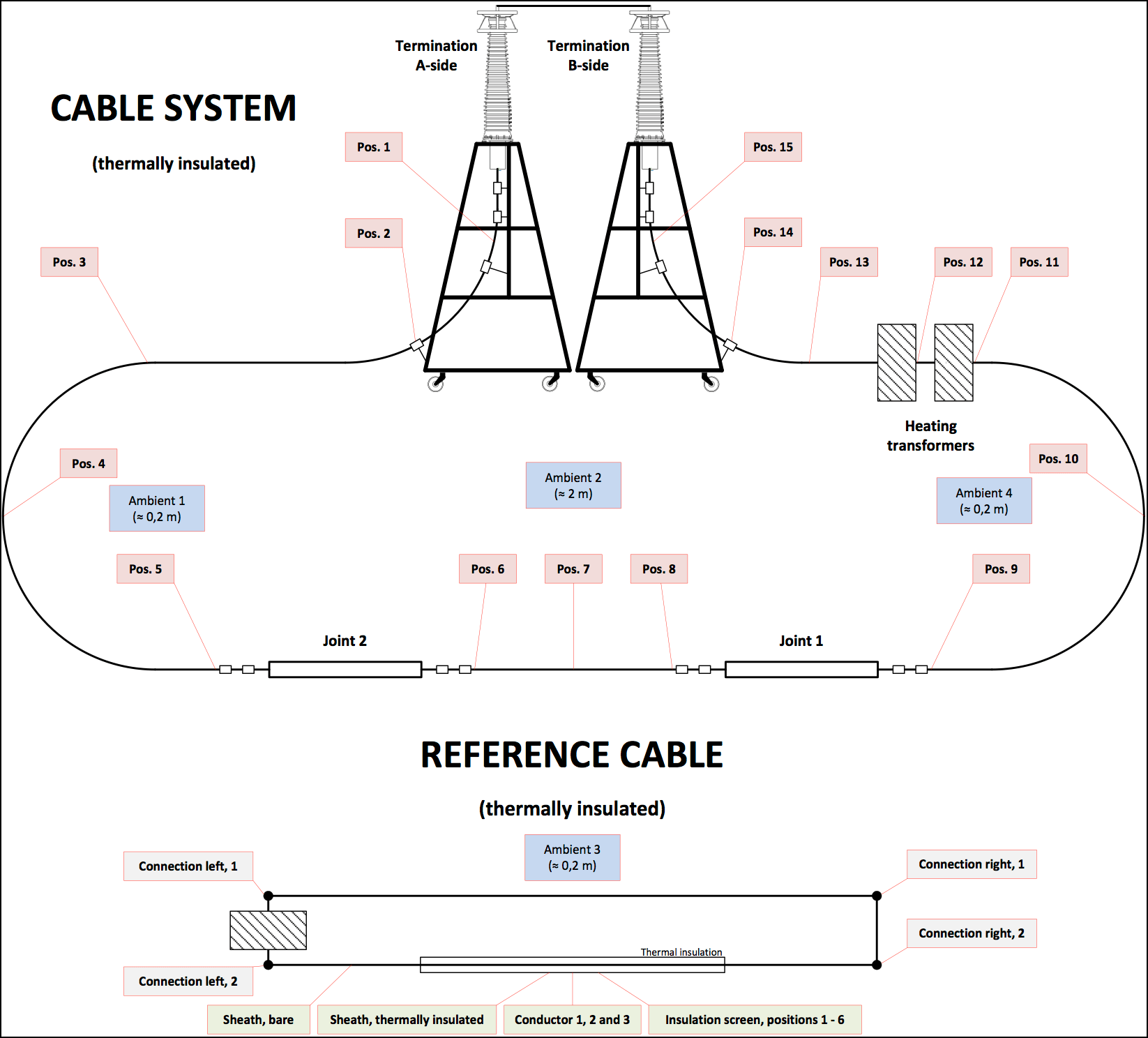
Configuración experimental
La configuración experimental incluía un generador DC, un generador de impulso y el objeto de prueba, un sistema de cable DC de 320 kV incluido el cable HVDC XLPE (conductor de cobre y aislación XLPE, capacitancia nominal de 0,26 µF/km), dos terminaciones de aceite exteriores y dos uniones premoldeadas con interrupción de pantalla. En las Figuras 5 y 6 se muestra un esquema del circuito de prueba y una configuración de prueba real. Cada sistema de prueba estaba equipado con su propio divisor para medir el voltaje DC (Divisor 1 en la Fig. 5) y SI/LI (Divisor 3 en Fig. 5) respectivamente. Se aplico un divisor combinado (Divisor 2 en Fig. 5) para medir el voltaje de resistencia superpuesto sujeto directamente al objeto de prueba.
Se instalaron un par de esferas (diámetro de 0,5 m, SG2 en Fig. 5) en posición vertical, con la esfera inferior directamente fija a las terminaciones exteriores. También se conectó el generador DC a la esfera inferior con el resistor de agua de protección (10 MΩ, R1 en Fig. 5) y la impedancia de bloqueo (35 mH, L1 en Fig. 5) entre medio. La esfera superior se separó de la esfera inferior y el cable con un espacio de aire y se conectó al generador de impulso. Se instaló un pararrayos (A1 en Fig. 5) para proporcionar una protección extra del generador DC.
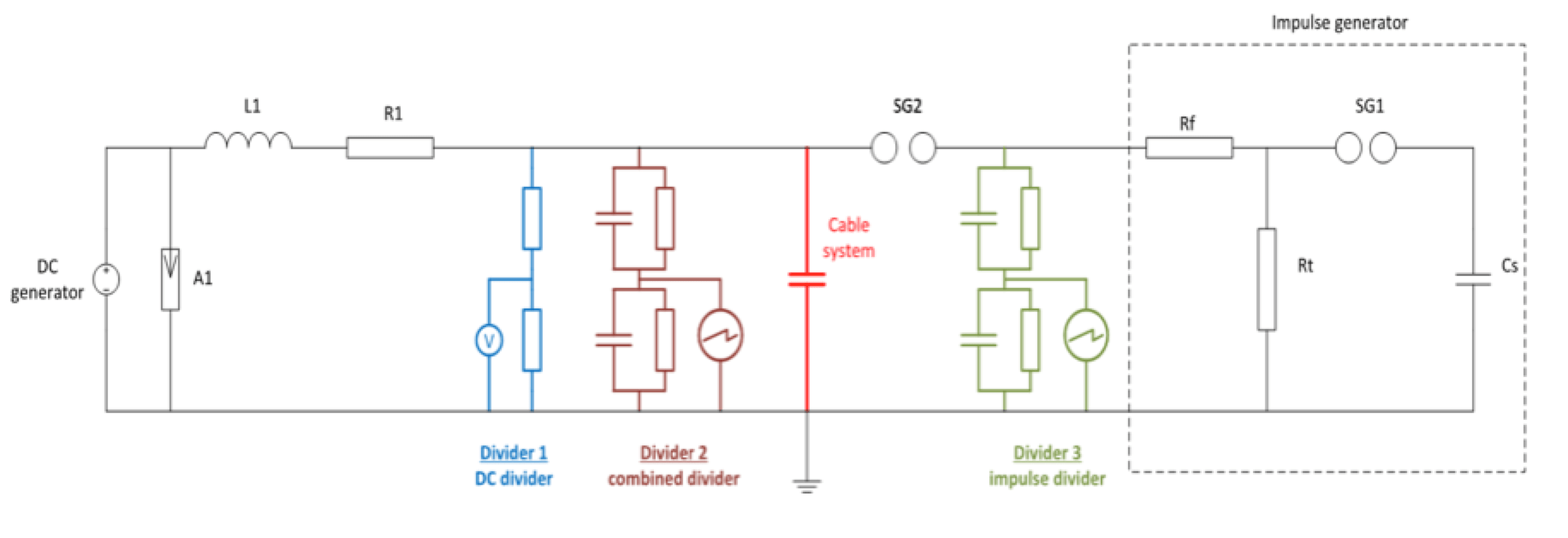
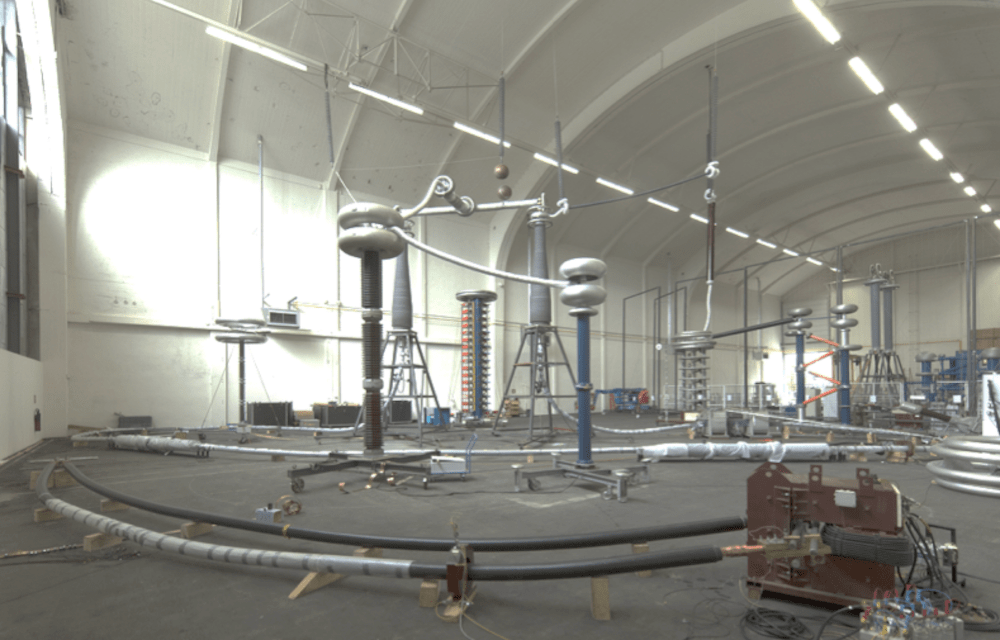
Procedimiento de prueba
La medición exacta de las formas de onda de voltaje y de la autoignición de la brecha de esfera son los dos aspectos esenciales de una prueba de impulso superpuesto. Por medio de una brecha de esferas, esta brecha debe encenderse a un cierto nivel y transferir el SI/LI al sistema de cable. Se debe considerar y ajustar la distancia de la brecha. Con la misma polaridad de dos voltajes (por ejemplo: + UDC y + USI, una tensión unipolar), el voltaje de ruptura de la brecha de esferas (Ubd unipolar = UDC – USI ≥ UDC, así USI ≥ 2 UDC), contrario a una tensión bipolar (por ejemplo: + UDC y – USI), el voltaje (Ubd bipolar = UDC – (– USI) ≥ UDC , así USI absoluto ≥ 0). Por lo tanto, en tensión bipolar, la ruptura del espacio de aire no es crítica; sin embargo, en tención unipolar, es un procedimiento complejo debido a la Ubd unipolar. Además, estos pasos de calibración son necesarios para evitar el sobrepaso del objeto de prueba [4]. Es necesario ajustar la distancia de la brecha de esferas que corresponde a la calibración de los voltajes de impulso desde las escalas bajas (50%, 65% y 80% del voltaje de prueba) hasta la escala completa (100% del voltaje de prueba ).
Análisis de los resultados medidos
Los tres voltajes medidos se obtuvieron con tres divisores: D1, D2 y D3 (ver Fig. 5) durante las pruebas. El voltaje DC se midió con el Divisor 1 mediante un medidor de voltaje digital y la escala completa del voltaje DC debería ser 320 kV. Los voltajes SI/LI se observaron con el Divisor 3 y los voltajes pico deberían ser 710 kV y 740 kV, respectivamente (ver Fig.7). El voltaje DC se superpone con la misma polaridad de SI como se muestra en la Fig. 8. Luego, se descubrió que el voltaje DC se superpone con SI y LI de polaridad opuesta en las Figuras 9 y 10, respectivamente.
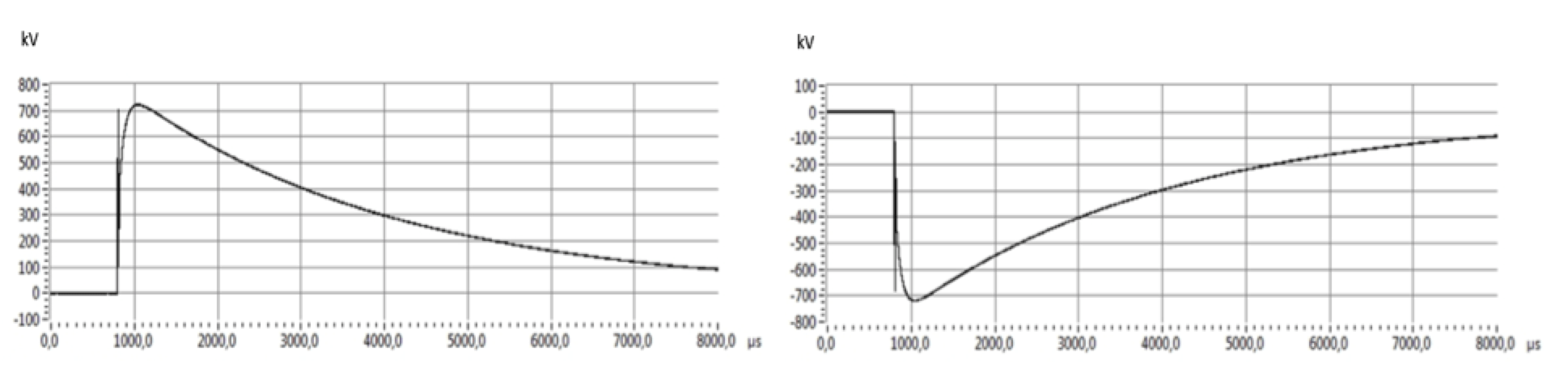
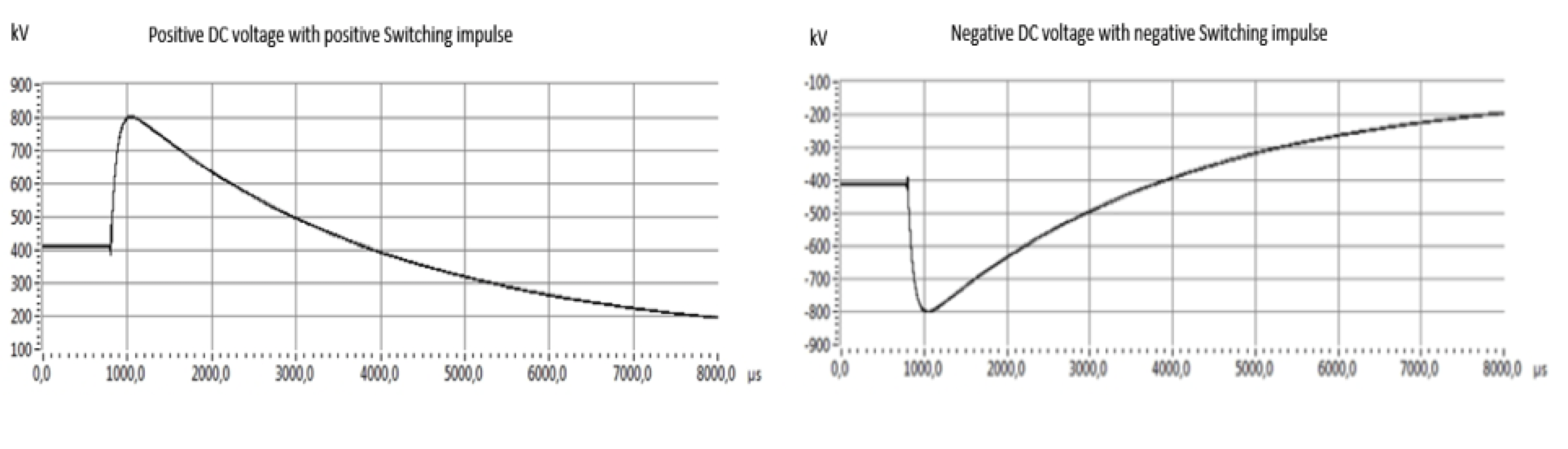
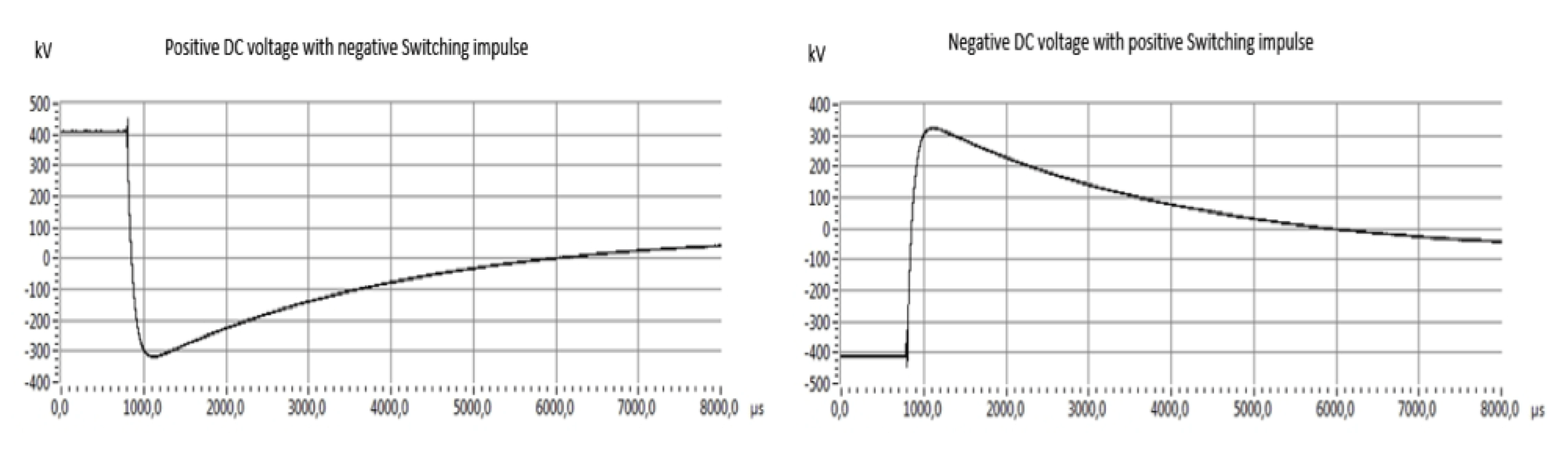
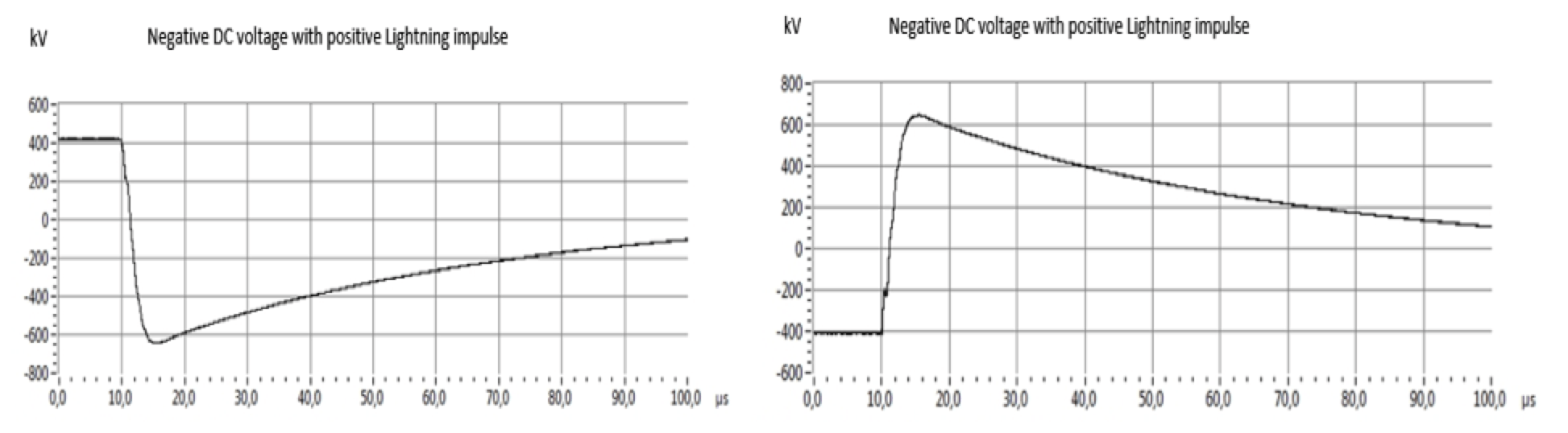
Como se muestra en la Fig. 7, el Divisor 3 midió un pico en frente de la forma de onda SI, que es el retardo de tiempo de la brecha de esferas de protección, fue hasta sobre el voltaje de ruptura, luego la brecha de esferas se condujo y el sistema de cable se conectó en ese momento al generador de impulso.
Como se observa en la Fig. 8, ocurrió un error de compensación DC sistemático durante las pruebas. El Divisor 2 se calibró con el voltaje DC y los voltajes de impulso, respectivamente. Para los voltajes combinados, es necesario un factor de corrección (es decir, un factor de 0,78). Esta compensación lleva a una diferencia de voltajes pico de impulsos medidos por el Divisor 3 y el Divisor 2.
Se ve que, una vez que el arco entre las esferas se encendió, el voltaje en el sistema de cable siguió el voltaje en el terminal del generador de impulso. Así, el voltaje en el sistema de cable en un tiempo extremadamente corto (cientos o miles de µs) se descargó por medio del generador de impulso para extinguir el voltaje del arco (visible en los gráficos); luego, tomaría un corto tiempo de recuperación (unos pocos cientos de ms) para recargar el voltaje DC (invisible en los gráficos debido a la limitante de recolección de datos). En el intertanto, los resistores de protección mantuvieron la diferencia completa de voltaje de impulso y de voltaje de prueba DC.
Conclusiones
El cálculo de Δθmax se obtuvo según el método de transferencia de calor. Para mantener una temperatura superficial constante del cable, como es necesario para garantizar una Δθmax especificada, los métodos prácticos incluyeron controlar la corriente de carga a través del conductor, mantener una temperatura ambiente constante o aplicar un material de aislación térmica externo. Se ha desarrollado la configuración de prueba utilizando una brecha de esferas para la aplicación de SI/LI superpuestos en un voltaje DC. El ajuste correcto de la brecha es esencial para la condición de tensión unipolar. De lo contrario, en ciertas circunstancias, podrían ocurrir oscilaciones de alta frecuencia. Un trabajo experimental más a fondo se enfoca en un método para controlar la temperatura de la funda de cable y el desarrollo de un software de tres canales con tiempo de captura de datos extenso (hasta el tiempo de recuperación del voltaje DC). Un capacitor de protección es una alternativa a una brecha de esferas para realizar una prueba de resistencia superpuesta.
Referencias
[1] Cigre 496: Recommendations for Testing DC Extruded Cable Systems for Power Transmission at a Rated Voltage up to 500kV, April 2012.
[2] IEC 62895 Edition 1.0: 2017-05: High voltage direct current(HVDC) power transmission – Cables with extruded insulation and their accessories for rated voltages up to 320 kV for land applications – Test methods and requirements.
[3] E. Pultrum, W. Sloot, J. Fernandez, R. P. P. Smeets, “High-voltage cable testing: type test experiences and new insights into pre-qualification”, CEPSI, 2016.
[4] IEC 60060-1 Edition3.0: 2010-09: High-voltage test techniques – Part 1: General definitions and test requirements.
[inline_ad_block]