Las subestaciones y líneas aéreas ubicadas a lo largo de la costa oeste de Suecia experimentan altos niveles de contaminación marítima. Particularmente, dos de estas subestaciones expuestas, que se construyeron en los años setenta, se han equipado con aisladores de porcelana relativamente cortos: la única opción disponible al momento de su construcción. Para asegurar un mejor manejo de la contaminación, se consideró que era necesario instalar un equipo de lavado automatizado para la línea viva. Aunque la automatización del lavado se modernizó a fines de 1980, el sistema no siempre funcionaba sin problemas. A veces, el sistema de detección de contaminación activaba el lavado más a menudo que lo necesario, mientras que en otras ocasiones, lo hacía demasiado tarde. Incluso había casos en los que el sistema de lavado mismo iniciaba arcos eléctricos en la aislación en vez de prevenirlos. Como resultado, eventualmente, una de las subestaciones decidió realizar lavados en forma regular en vez de confiar en el sistema de detección de contaminación para activarlo.
Recientemente, estas dos subestaciones habían realizado una renovación y uno de los objetivos era descontinuar la aplicación del sistema de lavado que era muy costoso por el alto consumo de agua. Por ejemplo, el volumen de agua desmineralizada necesario para cada lavado era de 140 m3. Este artículo editado para la INMR, escrito por Milan Radosavljevic del Operador del Sistema de Transmisión (TSO) sueco Svenska Kraftnät (Svk) e Igor Gutman y Andreas Dernfalk del Independent Insulation Group habla de porqué se decidió elegir la aplicación de un revestimiento de silicona RTV en lugar del lavado. También explica la matriz no estandarizada de pruebas que se utilizó para seleccionar el material óptimo de revestimiento para el lugar.
>
El sistema de lavado instalado originalmente en las subestaciones de 400 kV de Ringhals y Barsebäck consta de un estanque grande de agua desmineralizada con una estación de bombeo y tuberías, un sistema de rocío con boquillas y un sistema de detección de contaminación automatizado. El procedimiento de rociado en relación a que partes de la playa de distribución se lavan y en qué secuencia, depende de la velocidad y la dirección del viento. El sistema de detección de contaminación automatizado depende de un aislador de porcelana pequeño instalado verticalmente que recolecta la contaminación natural. Periódicamente, el aislador rota 90° y queda inmerso en una pileta de agua. Luego, se mide la contaminación a través de la conductividad del agua donde se ha disuelto la sal de la superficie del aislador. Para activar el lavado, es necesaria una conductividad crítica. Luego, la secuencia de lavado se determina según la velocidad y la dirección del viento. Existen 20 rampas/secciones en la playa de distribución con un tiempo de lavado típico de 90 segundos por sección y ya que existe una pausa de 30 segundos entre las secciones, terminar el ciclo de lavado toma alrededor de 40 minutos.

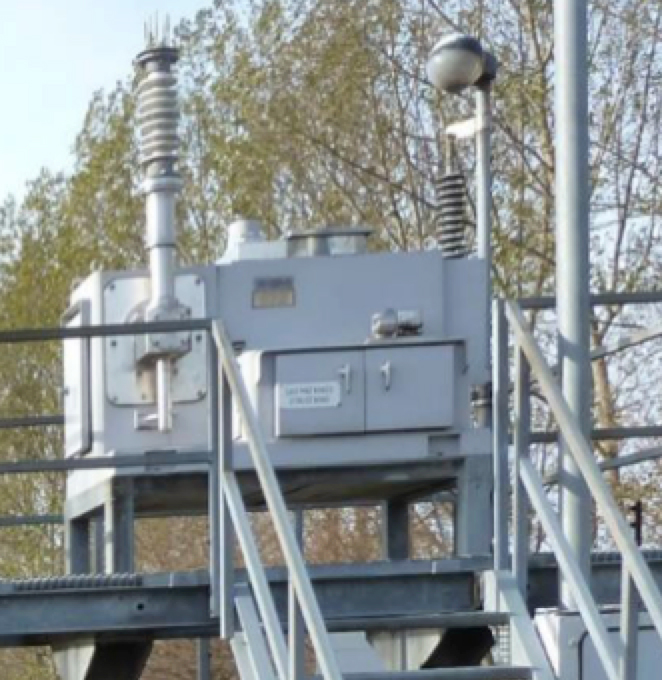
La política general en Svk ahora es solo especificar los aparatos aislados poliméricos en todas las subestaciones nuevas y esto también es válido para la renovación de las subestaciones existentes. El factor principal tras esta política es la relativa seguridad de los aisladores poliméricos en comparación con los de porcelana en caso de falla. Los aisladores poliméricos también ofrecen un excelente rendimiento en circunstancias de contaminación, lo que los hace especialmente adecuados para la aplicación en la costa oeste: la única área enormemente contaminada de forma natural en el país. Esto ha sido confirmado con una serie de investigaciones de monitoreo de contaminación, así como también con el mapa de contaminación de Suecia creado recientemente.
La Tabla n.° 1 muestra las diferentes opciones de tecnología para los aisladores consideradas cuando se planificó la renovación y que apuntaba a eliminar la necesidad de un lavado automatizado. El VERDE quiere decir que es la opción más prometedora, mientras que el ROJO significa que esa opción no es aplicable. Svk tiene requerimientos especiales para los aisladores tipo poste (soporte) de la estación, así como también para los interruptores de tierra, y prefiere no utilizar aisladores poliméricos para estas aplicaciones debido a que estos presentan una mayor deformación si se les compara con los de porcelana. Además, un requerimiento especial de Svk para los interruptores de tierra es que estos deben someterse a pruebas tipo, las que por ahora solo están disponibles para los interruptores equipados con aisladores de porcelana. Así, la única opción para mejorar el rendimiento en condiciones de contaminación de estos dos tipos de aisladores sería revestir la porcelana con material de goma de silicona RTV. También se consideraron aisladores híbridos que combinan un cilindro de porcelana con polleras poliméricas, pero se rechazaron ya que son una tecnología relativamente nueva con experiencia de servicio limitada.
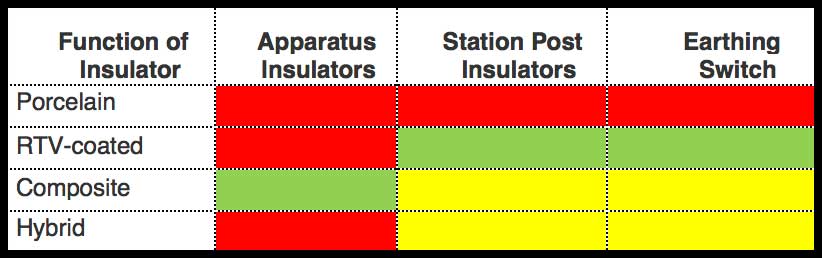
La subestación de Barsebäck fue la primera en renovarse y el proceso comenzó con un programa para establecer la severidad de la contaminación local del lugar. Esto incluyó la compilación y el análisis de las mediciones anteriores de los parámetros principales de contaminación, según se describe en la Norma IEC 60815-1, es decir, partes solubles/no solubles de la contaminación (ESDD/NSDD), análisis de la experiencia de servicio y evaluación de la contaminación con indicadores de depósitos de polvo direccionales. De acuerdo con los datos generados, se formularon los siguientes requerimientos preliminares para la distancia de fuga específica y la altura de la aislación respectiva necesaria en la subestación Barsebäck para cada opción de aislación (ver la Tabla n.° 2).
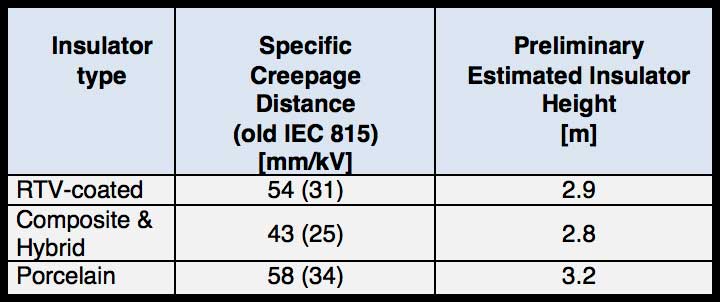
Los aisladores poliméricos de aparato ahora se han convertido en una opción probada en Svk debido a la experiencia de servicio altamente positiva. Por el contrario, los revestimientos de RTV en los postes de porcelana y los aisladores de los interruptores de tierra aún son un concepto nuevo en Suecia. Además, actualmente, no existen normas IEC y ni siquiera documentos CIGRÉ que describan las propiedades y los requerimientos de los revestimientos de RTV que se aplican en los aisladores de voltaje alto. El único documento de ese tipo disponible es una Guía de la IEEE. A pesar de que la comunidad internacional ha entendido la necesidad de esa información y de hecho CIGRÉ WG B2.69 ya ha comenzado a trabajar en esta tarea, la mayor parte de las aplicaciones de revestimiento que se estudian ahora involucran aisladores de cadena tipo cápsula & pin. Así, Skv tuvo que establecer su propia metodología para seleccionar el revestimiento RTV óptimo para aplicarlo a sus aisladores de soporte de porcelana. La selección preliminar incluyó identificar los productos disponibles de acuerdo con la experiencia de servicio informada y su evaluación con pruebas a pequeña escala.
Por razones de economía, Svk eventualmente decidió elegir solo dos materiales de revestimiento RTV para proceder con las pruebas a gran escala a clase de voltaje de 145 kV. Luego, se verificó el rendimiento de estos, los revestimientos más prometedores, con pruebas de arco eléctrico por contaminación artificial y una prueba de niebla salina de 1000 horas realizada en aisladores de porcelana revestidos que tienen un perfil similar a lo que se necesitaría en la subestación Barsebäck. También se consideraron las especificaciones del proceso de aplicación en cada caso, el costo relativo y otros asuntos prácticos de la compra. Según los resultados de estas pruebas se decidió usar los mismos revestimientos para todos los proyectos similares de Svk a lo largo de la costa oeste de Suecia.
Evaluación & pruebas de revestimientos de silicona RTV
1. Pruebas de evaluación a pequeña escala Según la información disponible sobre la disponibilidad y la experiencia de servicio real, se eligieron 7 materiales de revestimiento RTV disponibles comercialmente para realizar pruebas de evaluación a pequeña escala, entre ellas:
• Una prueba de adhesión de acuerdo con la Norma ISO 2409,
• Una prueba de hidrofobicidad de acuerdo con la Norma IEC TS 62073,
• Una prueba de transferencia de hidrofobicidad de acuerdo con los principios establecidos (ver las Figuras n.° 3 & 4).
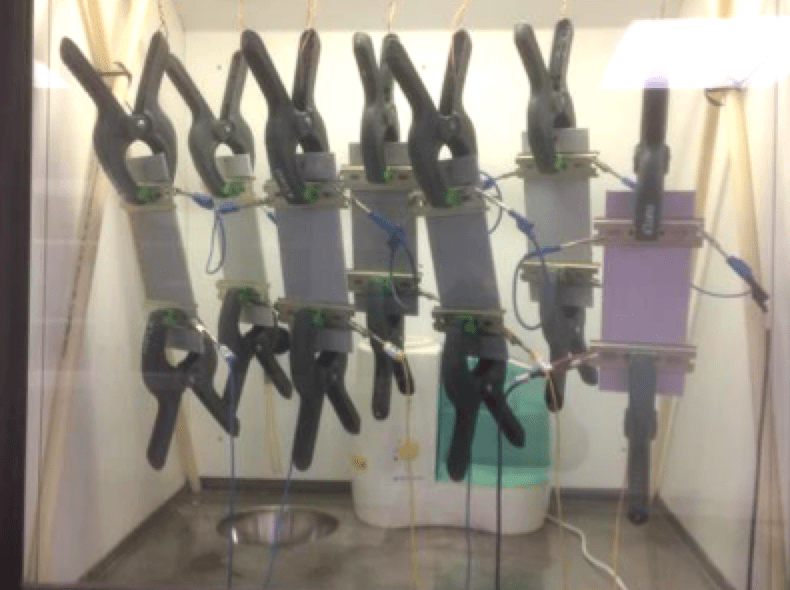
Se evaluó la propiedad de transferencia de hidrofobicidad de distintos revestimientos, aunque se realizaron una serie de mediciones de la corriente de fuga para estudiar cómo se transfiere la hidrofobicidad a la capa de contaminación que se acumula en la superficie del revestimiento. Esta es una característica importante ya que los componentes de peso molecular bajo en el material de revestimiento encapsulan sales en la capa de contaminación, lo que aumenta la resistencia y modera la corriente de fuga para reducir el riesgo de arco eléctrico.
Se aplicaron capas artificiales de contaminación en las placas de vidrio revestidas con RTV (de acuerdo a los principios de la CIGRÉ TB 555) para preacondicionar la superficie hidrofóbica con caolín seco y luego sumergirla en una suspensión de caolín, cloruro de sodio y agua. Se aplicó un nivel de contaminación según los procedimientos estándares y se eligió un valor promedio representativo de la costa oeste de Suecia, es decir, SDD/NSDD=0.05/0.1 mg/cm2. Se calculó la resistencia de la capa de contaminación en el tiempo con el voltaje aplicado y la corriente de fuga medida entre dos electrodos en placas revestidas con RTV, contaminadas y humedecidas. El voltaje entre los electrodos fue de alrededor de 200 V.
Como se muestra en la Figura n.° 4, había una diferencia significativa en la propiedad de transferencia de hidrofobicidad entre las diferentes muestras usadas para realizar la prueba. De hecho, este método es altamente efectivo para diferenciar las propiedades de hidrofobicidad dinámica de un material de revestimiento, como también se muestra con los resultados similares de pruebas anteriores (ver las Figuras n.° 5 & 6). Además, el método es más fácil de realizar y más decisivo que la alternativa de medir el ángulo de contacto en el tiempo y, por lo tanto, ahora se considera dentro de la CIGRE.
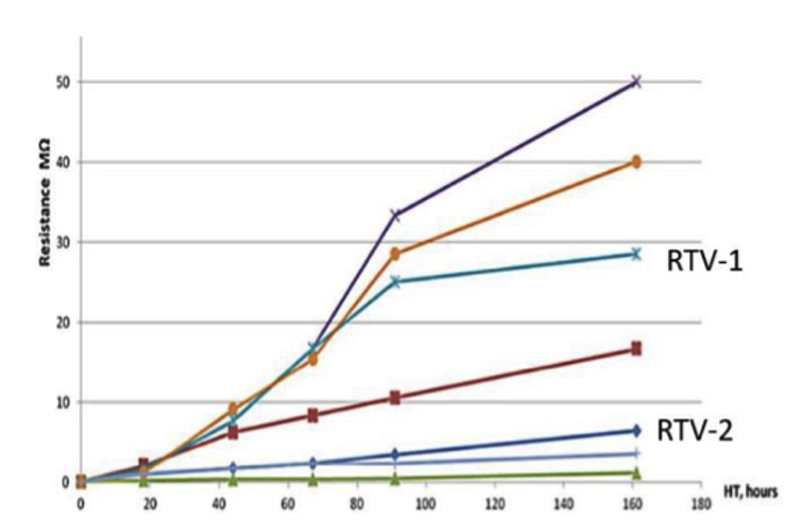
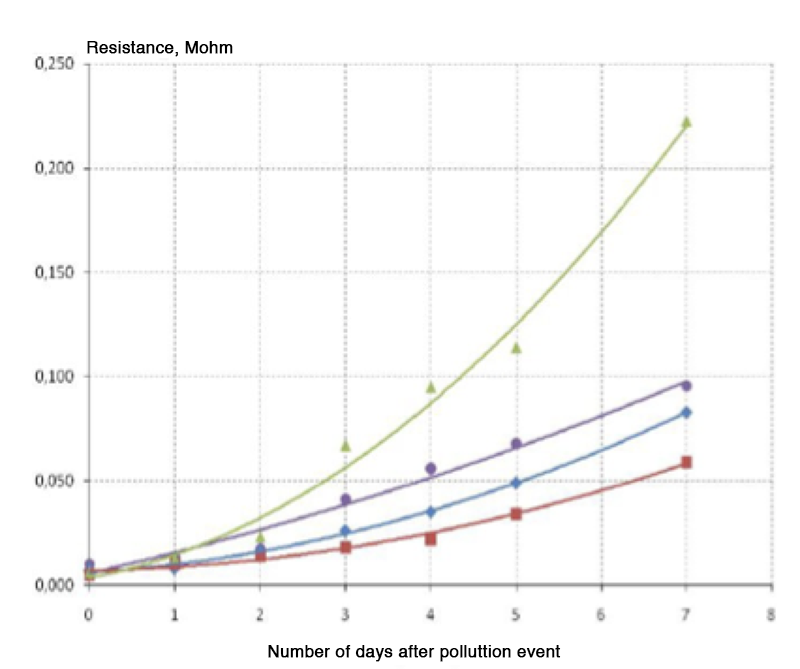
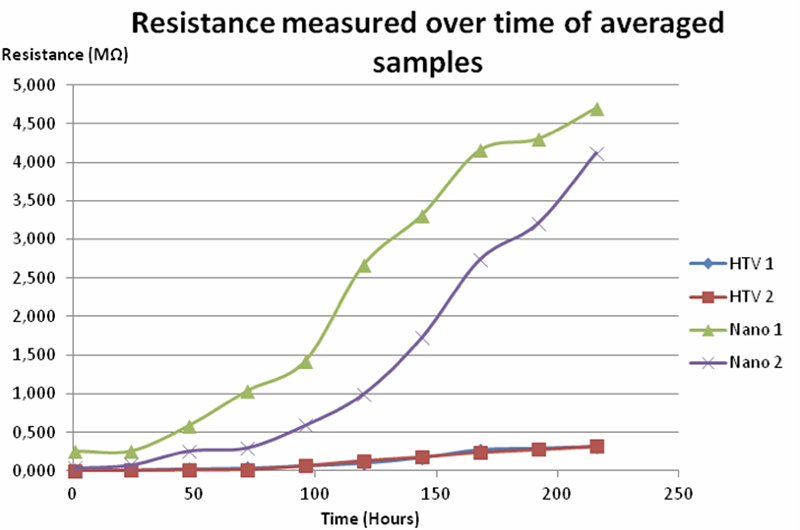
Según las pruebas de evaluación a pequeña escala y al revisar la experiencia de servicio disponible pertinente a las condiciones suecas, finalmente se eligieron 2 de estos 7 materiales de revestimiento para realizar más pruebas. El revestimiento con la tasa más alta de recuperación de hidrofobicidad fue llamado RTV-1 y el con la menor tasa de recuperación se llamó RTV-2 (ver la Figura n.° 4). Las pruebas a pequeña escala también confirmaron que la condición de la superficie, así como también la humedad y la temperatura, son todos parámetros importantes durante la aplicación de un revestimiento de RTV.
2. Pruebas a gran escala El desempeño de arco eléctrico por contaminación es un factor clave en cualquier aplicación de un revestimiento de RTV, si consideramos que influye el dimensionamiento de un aislador en condiciones de contaminación. Ya que la Norma IEC 60507 abarca solo los aisladores de vidrio y de cerámica, se aplicó un preacondicionamiento especial según las recomendaciones de la CIGRE TB 555. También se acordó probar los aisladores revestidos después de un tiempo de recuperación específico de aproximadamente 3 días. Las pruebas de contaminación se realizaron en muestras de aisladores tipo poste revestidos con RTV y de porcelana especialmente preparados con un largo total de alrededor de 1 metro. El procedimiento para aplicar la contaminación a los aisladores revestidos fue el siguiente:
• Limpieza suave,
• Preacondicionamiento con caolín seco en polvo,
• Aplicación de capa de contaminación con rociador (ver la Figura n.° 7).
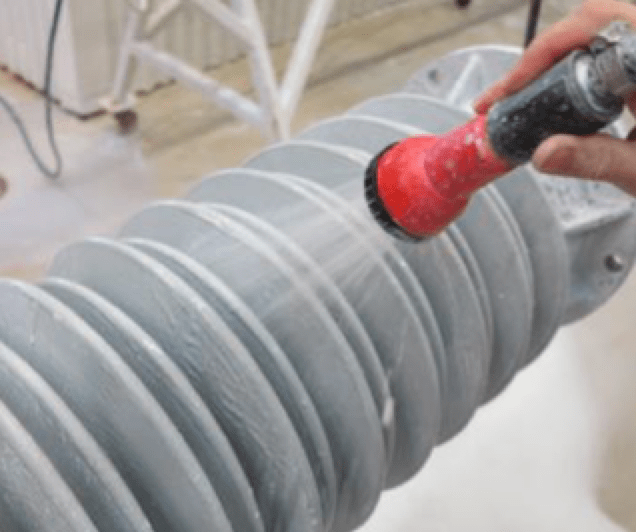
Para la prueba de arco eléctrico por contaminación, los aisladores contaminados y secos se llevaron a una cámara de prueba climática y se colocaron en aisladores tipo poste de porcelana de aproximadamente 2 metros de altura (ver Figura n.° 8).
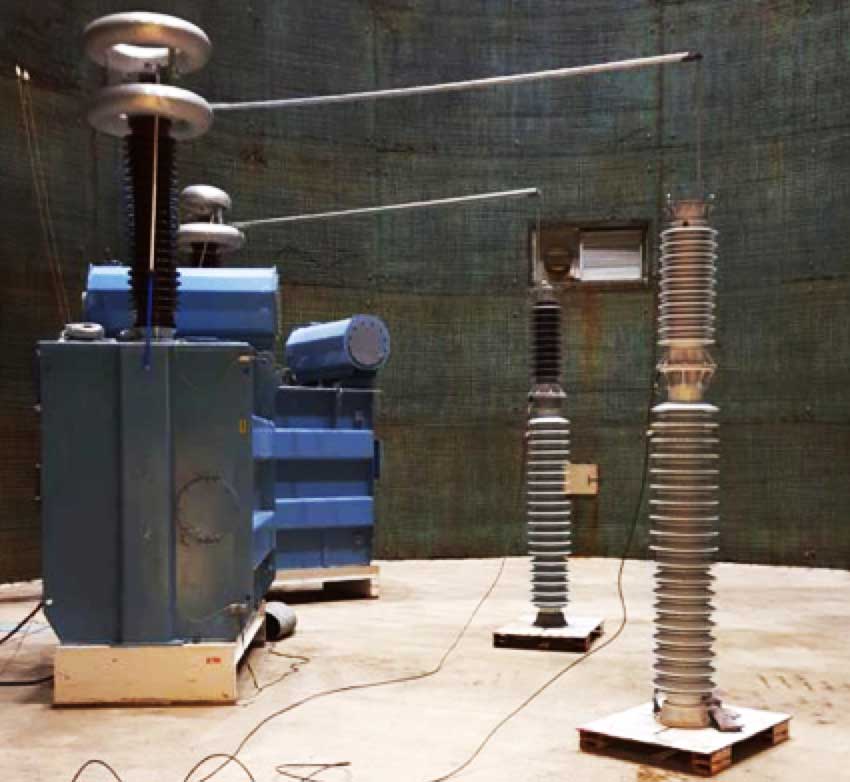
Estas pruebas de arco eléctrico por contaminación artificial se realizaron con el procedimiento “arriba y abajo” estándar y mostró que los aisladores revestidos tenían un voltaje de arco eléctrico significativamente más alto comparado con la porcelana desnuda (en un 50 %). Por ejemplo, a un nivel de contaminación de SDD=0.06 mg/cm2 (considerado representativo de la severidad del lugar en Barsebäck), el voltaje de arco eléctrico fue más de 40 % más alto que el de la porcelana sin revestimiento. Los resultados de la prueba se finalizaron como curvas de desempeño versus tensión por contaminación (SDD) para los distintos revestimientos de RTV y la porcelana sin revestir. Por lo tanto, estas se pueden usar para seleccionar los largos requeridos de aisladores en las subestaciones Barsebäck y Ringhals, así como también para otros lugares similarmente contaminados en Suecia.
El desempeño del envejecimiento a largo plazo de los revestimientos de RTV seleccionados se evaluó con una prueba de arrastre y erosión con niebla salina de 1000 horas. Ya que actualmente no existe ninguna norma para evaluar los revestimientos de RTV, se seleccionó la prueba de arrastre y erosión para los aisladores poliméricos por la similitud de las superficies (es decir, goma de silicona). Como se indica en esta norma, la prueba de 1000 horas no se considera una prueba de envejecimiento acelerado ya que no simula exactamente las condiciones de servicio reales y no proporciona factores de aceleración para estimar la vida útil. Más bien, depende de la tensión continua para detectar cualquier debilidad potencial en el material o el diseño que podría comprometer el desempeño a largo plazo. De acuerdo a la norma, los aisladores se deberían probar a una tensión correspondiente a una distancia de fuga específica unificada (USCD) de 34.6 mm/kV.
Se probaron dos secciones simultáneamente con la aplicación de voltaje en el medio del aislador (ver la Figura n.° 9). El voltaje de prueba seleccionado fue de 20 kV, que genera tensiones reales de 36.4 mm/kV en la parte superior y 34.5 mm/kV en la parte inferior. La salinidad del agua utilizada para la generación de la niebla fue 2 kg/m2 de acuerdo con la norma y también se tomaron en cuenta las dimensiones del aislador (es decir, el diámetro promedio).
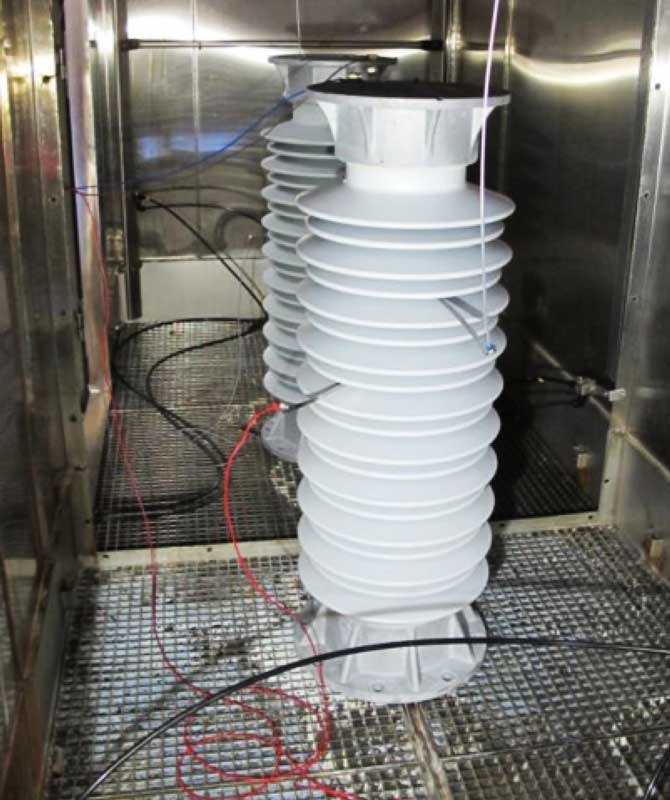
Ambos revestimientos de RTV preseleccionados pasaron la prueba de niebla salina de 1000 horas. Sin embargo, los resultados fueron diferentes y de manera correspondiente con los resultados de la prueba de transferencia de hidrofobicidad presentados en la Figura n.° 4, es decir el revestimiento RTV-1 con la recuperación de hidrofobicidad más rápida proporcionó mejores resultados durante la prueba de 1000 horas que el revestimiento RTV-2. Por ejemplo, al final de la prueba, la hidrofobicidad era HC 1-2 y 3-4 y la corriente de fuga máxima era de 20 y 240 mA, respectivamente, para las muestras RTV-1 y RTV-2. Luego, se limpió el aislador RTV-1 con agua desionizada y se inició una nueva prueba de 1000 horas al día siguiente. Luego de finalizar la segunda prueba, no se encontraron signos de deterioro y se volvió a confirmar el alto nivel de hidrofobicidad, particularmente en el tronco y el lado inferior de las polleras (ver Figura n.° 10).
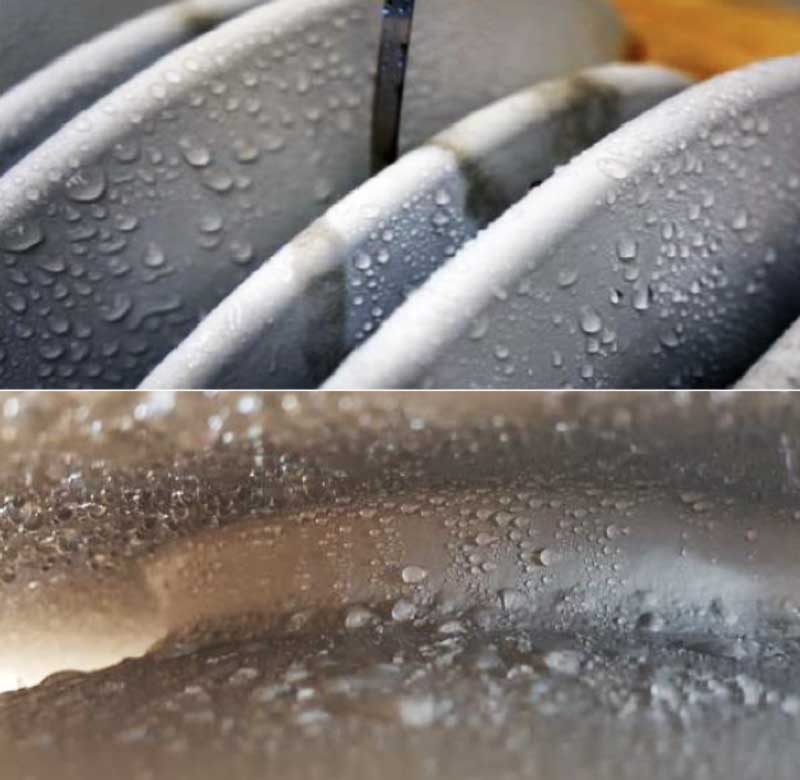
Selección final del aislador
Las Figuras n.° 11 a 14 muestran los resultados de los cálculos estadísticos del largo requerido para la distancia de fuga del aislador según los resultados de la prueba de contaminación y que se realizaron con el software Insulation Selection Tool (IST – Herramienta para la selección de la aislación) que se basa en el principio de dimensionamiento estadístico como se define en la Norma IEC 60815-1. El criterio fue un tiempo medio entre arcos eléctricos (MTBF) de 50 años. Como se ilustra en estos gráficos, la porcelana sin revestimiento siempre requiere la USCD más larga en comparación con los aisladores revestidos con RTV. Esto es válido incluso en aquellas situaciones donde los aisladores revestidos con RTV no tienen tiempo para la recuperación de la hidrofobicidad después de la exposición a la contaminación (ver Figura n.° 11). Además, se debería notar que el RTV-2 (con menor recuperación) tenía un mejor desempeño comparado con el RTV-1 (con recuperación más alta) durante la etapa inicial de la prueba (es decir, sin simulación de recuperación). Sin embargo, el efecto de la recuperación fue significativamente más alto para RTV-1 que para RTV-2 a pesar del, de algún modo, mayor nivel de NSDD (ver comparaciones en las Figuras n.° 12 & 13). Esta observación concuerda con los hallazgos de las pruebas a pequeña escala y las pruebas de niebla salina. De hecho, después de un periodo de recuperación de tres días, ambos revestimientos (RTV-1 y RTV-2) tenían características similares (ver Figura n.° 14).
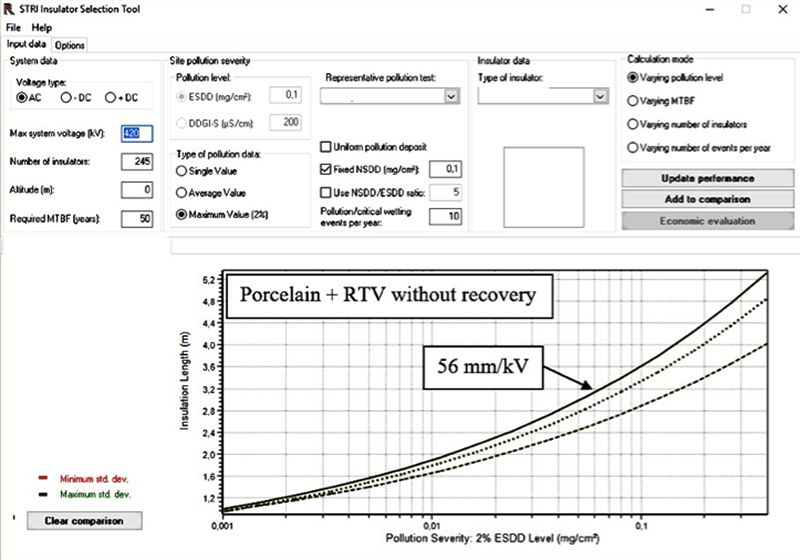
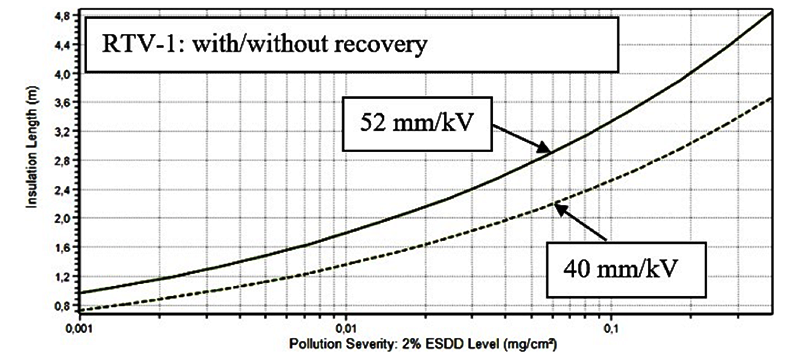
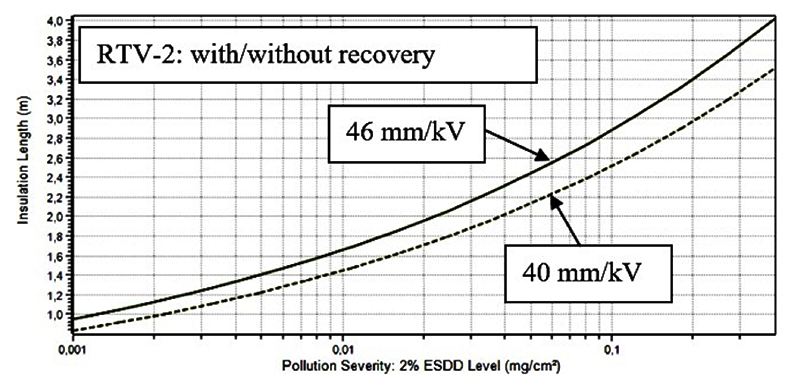
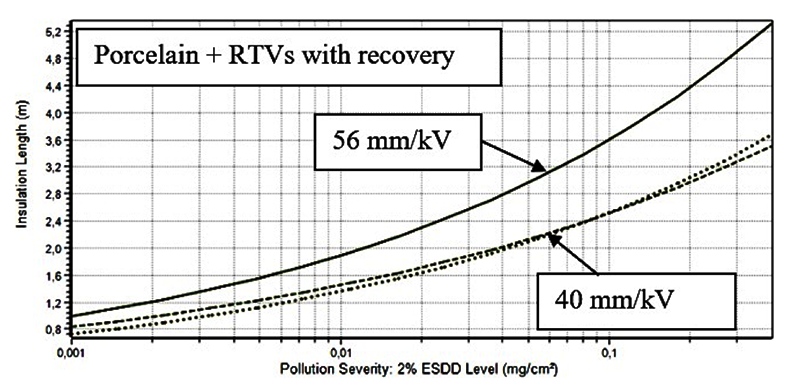
Estos resultados también son concordantes con las observaciones de servicio presentadas, por ejemplo, en la Figura n.° 15. Estas son mediciones de corrientes de fuga en condiciones muy altamente contaminadas en la estación de prueba de aisladores Koeberg en Sudáfrica ubicada en la costa del Atlántico cerca de Ciudad del Cabo (es decir, ESDD máxima de alrededor de 0.7 mg/cm2). Durante un año se probaron varios aisladores de idéntico perfil y largo, pero hechos de distintos materiales y el aislador revestido con RTV mostró el segundo mejor desempeño después del aislador con esmaltado semiconductor.
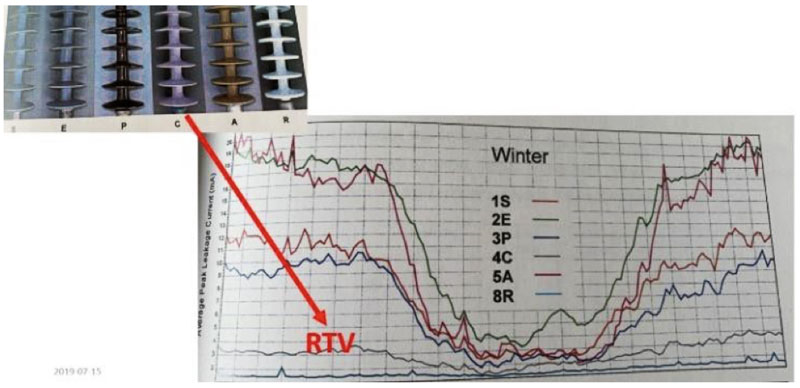
Conclusiones
Se realizó un estudio integral de los revestimientos de RTV comerciales con el objetivo de ya no seguir dependiendo del lavado costoso en las subestaciones expuestas a contaminación costera. Ya que aún no existen requerimientos normativos para estos revestimientos, TSO Svk, respaldada por un equipo de investigación, desarrolló una matriz de prueba para identificar el material de revestimiento óptimo para estas condiciones. Esta matriz de prueba incluía pruebas de evaluación en muestras a baja escala que, junto con una revisión de la experiencia de servicio, redujeron los revestimientos evaluados originalmente de siete a dos. Para la selección final, también se consideraron las especificaciones de la aplicación, el costo y otros asuntos prácticos de la compra.
Los dos revestimientos RTV seleccionados se aplicaron en aisladores de 145 kV y se evaluaron con pruebas de contaminación de corta duración que permitían la selección de la distancia de fuga y del largo de la aislación apropiados para los aisladores de interés. También se verificó el desempeño a largo plazo de estos revestimientos de RTV con pruebas de arrastre y erosión de 1000-2000 horas. Es interesante observar que todos los resultados de la prueba de transferencia de hidrofobicidad, de la prueba de contaminación con simulación de recuperación de hidrofobicidad y de las pruebas de niebla salina de larga duración resultaron ser coherentes para los revestimientos RTV que tienen distintas tasas de recuperación de hidrofobicidad.
Entre las lecciones aprendidas están que es un desafío complejo para las empresas de servicios básicos eléctricos distinguir entre los distintos revestimientos comerciales y que realizar un estudio como este, de manera interna, es costoso. Como dueño de las subestaciones involucradas, Svk preferiría evaluar y seleccionar un revestimiento cuyas características básicas y esperanza de vida útil se puedan verificar con métodos estandarizados. Es de esperar que la investigación realizada dentro de la CIGRE WG B2.69 proporcione los requerimientos técnicos mínimos para los revestimientos de RTV. De acuerdo con la investigación mencionada anteriormente, se considera que son cuatro las pruebas básicas que son importantes y por lo tanto, se deberían considerar cuando se evalúa un material RTV: una prueba de adhesión, una prueba de transferencia de hidrofobicidad, una prueba de contaminación y una prueba de “envejecimiento” a largo plazo.
Referencias
[1] M. Radosavljevic, T. Lindquist, I. Gutman, A. Dernfalk: “Refurbishment of 400 kV AC substation in polluted environment: pros and cons for different modern insulation options including composite/RTV/hybrid”, CIGRE SC A3 & B3 Joint Colloquium, Nagoya, Japan, 28 September – 2 October 2015, paper 236
[2] IEC 60815-1: “Selection and dimensioning of high-voltage insulators intended for use in polluted conditions – Part 1: Definitions, information and general principles”
[3] M. Radosavljevic, A. Dernfalk, I. Gutman: “Development of requirements for testing and verification of RTV-coated substation support insulators for AC application”, CIGRE-2018, A3-109
[4] ISO 2409: “Paints and varnishes – Cross-cut test”, Ed. 3, 2013
[5] IEC TS 62073: “Guidance on the measurement of hydrophobicity of insulator surfaces”, Ed. 2, 2016
[6] I. Gutman, A. Dernfalk, A. Nefedov, J. Seifert: “Pollution test methods for composite insulators: simulation of coastal environment and recovery of hydrophobicity”, 16th ISH-2009, Cape Town, South Africa, 24-28 August 2009, E-4
[7] I. Gutman, J. Seifert, C. Greyling: “Recovery of Hydrophobicity of a New Nano-composite Coating for Ceramic Insulators”, IEEE ISEI-2012, paper 12, p.p. 48-52
[8] CIGRE Technical Brochure 555 “Artificial Pollution Test for Polymer Insulators”, October 2013
[9] IEC 60507: “Artificial pollution tests on high-voltage ceramic and glass insulators to be used on a.c. systems”, Ed. 3, 2013
[10] IEC 62217 “Polymeric HV insulators for indoor and outdoor use – General definitions, test methods and acceptance criteria”, Edition 2.0, 2012-09
[11] W. Vosloo: “A Comparison of the Performance of High-voltage Insulator Materials in a Severely Polluted Coastal Environment”, Dissertation, University of Stellenbosch, March 2002