Considerable effort has been devoted to planning meshed, multi-terminal HVDC networks. One of the crucial components in such grids is the circuit breaker, which must be capable of clearing DC faults without de-energizing the DC side of the grid. A circuit breaker must deal with special requirements for interrupting direct current including extremely fast operation, creation of artificial current zero(s), generation of a counter voltage higher than system voltage and large energy absorption. While metal oxide surge arresters (MOSAs) are normally used in this application, the types of stresses to be dealt with are much different than for AC grids.
This edited contribution to INMR by then PhD candidate, Peter Hock, and Prof. Volker Hinrichsen of the Technical University of Darmstadt in Germany in co-operation with Nadew Belda and Rene Smeets of Kema Labs in the Netherlands, reviewed special requirements for MOSAs when it comes to application in an HVDC circuit breaker.
Background
Unlike for AC, DC current interruption is especially challenging due to:
• DC fault current does not have natural current zero crossings and, as such, the DC circuit breaker must create one to perform current interruption;
• In addition to creating artificial current zero, a DC circuit breaker needs to generate and maintain a counter voltage – known as transient interruption voltage (TIV) – higher than operational system voltage during current interruption;
• Absence of current zero crossings means there is always magnetic energy stored in the DC system so long as current flows. While generating and maintaining counter voltage, the DC circuit breaker has to absorb the system’s energy.
One peculiar feature of an HVDC circuit breaker’s current interruption capability is absorbing the magnetic energy stored in system inductances. In fact, all HVDC circuit breaker technologies include a dedicated component designed for this purpose and that constitutes a special metal oxide surge arrester (MOSA) bank. This bank is composed of metal oxide resistor blocks (also known as metal oxide varistors or MOVs) that are arranged in multiple columns to absorb large system energy yet without undergoing significant deterioration or possible destruction. The MOSA has two major functions in an HVDC circuit breaker: the first is to limit the TIV it produces during the current interruption process; the second is to absorb the energy stored in the system’s inductance. As such, the MOSA must maintain a TIV at a level higher than the source voltage but lower than the voltage that can be withstood by the opening contacts until the energy in the system is absorbed or the current suppressed. While MOSAs are used in all types of power systems, Table 1 highlights differences between their use for overvoltage protection in AC and DC applications versus for HVDC breakers.
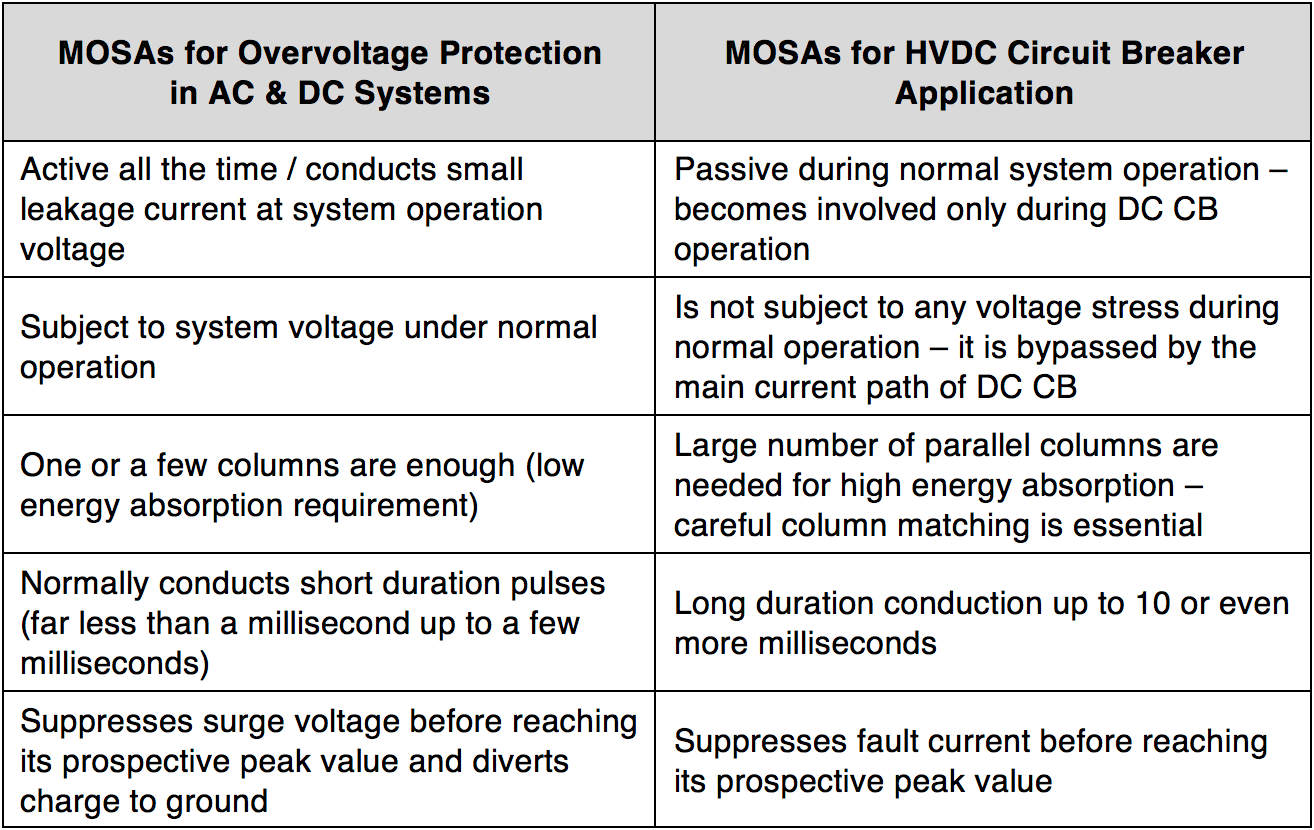
Leakage current does not have significant impact in an HVDC breaker application since the MOSA is normally isolated from the system, both during the closed state and the open state. When the HVDC circuit breaker is in the closed state, the MOSA is short-circuited by the normal current path. In the open state, a residual current circuit breaker that is connected in series isolates the HVDC circuit breaker from the system. Design of an HVDC circuit breaker can affect the stresses experienced by the MOSA.
In general, HVDC CBs are realized using a modular approach. The connection of the MOSA could be across the entire arrangement of modules or across each module, depending on designer preference. In the latter case, if for any reason one module fails to commutate current into its MOSA while the remaining modules operate normally, the MOSA across the remaining modules must be able to handle the entire energy. Also, in some designs of hybrid HVDC circuit breakers, MOSAs are placed in parallel to a few IGBTs of the main breaker, making a series connection of a large number of MOSAs overall. If a few IGBTs fail to commutate current into the MOSA while the remaining IGBTs operate normally, the MOSAs across the functioning IGBTs must be able to handle all the energy. Moreover, these two above situations lead to long duration current conduction of MOSAs since the TIV is reduced when some MOSAs are not conducting.
Basics of High Voltage Direct Current Switching
Different techniques have been proposed for HVDC current interruption. Two technologies, namely hybrid HVDC CB and active current injection HVDC CB, are considered the most promising candidates with their respective pros and cons. The hybrid HVDC CB technology uses a small power electronics breaker in combination with fast mechanical disconnector(s) in the main current path and a large stack of power electronics elements serving as the main breaker, connected in parallel to the main current path. The active current injection HVDC CB uses mechanical interrupter(s) in the main current path and a counter current injection circuit composed of an RLC resonant circuit connected in parallel to the main current path, with or without a pre-charged capacitor depending on the breaker technology (gas type or vacuum type breaker). In both cases, the MOSA is connected in parallel to the RLC branch in active injection and to the main breaker in hybrid HVDC circuit breakers. The basics of HVDC switching with active current injection technology are demonstrated with a mechanical switch as main switching element in the CB. For that purpose, commercially available vacuum interrupters have been used in this project. Fig. 1 shows a parallel commutation path for creating an artificial current zero and energy absorbing path as necessary for this concept. The commutation path is designed as a series RLC resonant circuit. The capacitor, CC, of the commutation path has to be pre-charged by an external source. The polarity of the pre-charged capacitor is chosen such that a current zero of the main current is enforced during the first half‑cycle of the capacitor discharge current. This facilitates fast and reliable current breaking. The energy absorption path protects the capacitor, CC, from being overcharged and is typically made up from a MOSA.
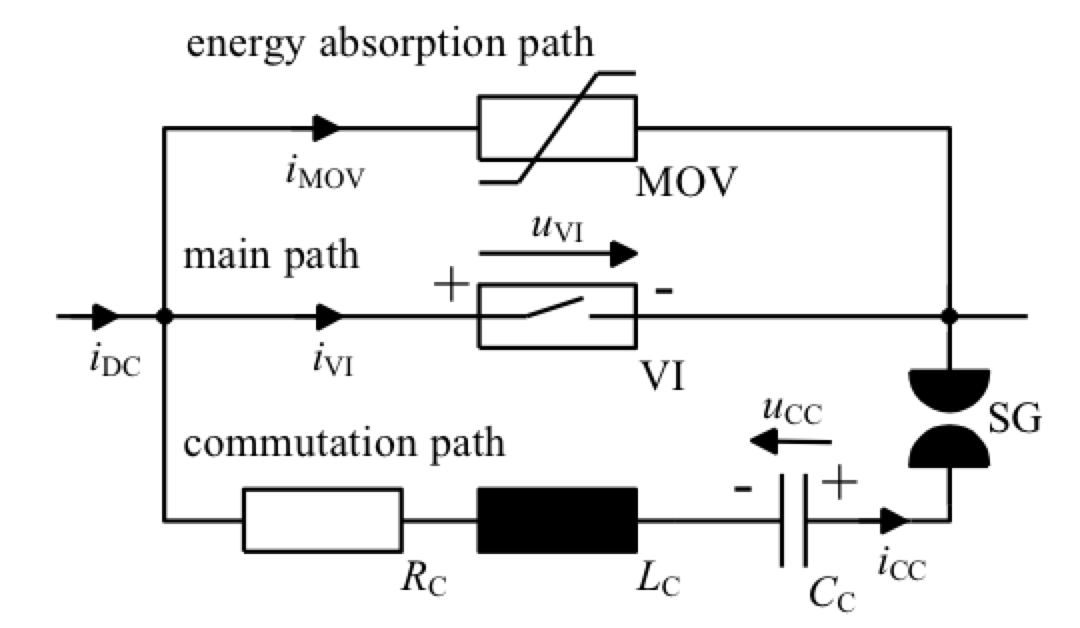
switch in main path, active commutation path.
In the ‘on-state’, the vacuum interrupter contacts are closed and the DC main current flows with only negligible on state losses. At the beginning of a switching process, the contacts start to separate, which leads to ignition of an arc. As soon as the gap distance between the contacts is large enough, the commutation path in this example is activated by triggering a spark gap (SG). But a high-speed mechanical switch or a semi-conducting switching element would also be possible and a high-frequency sinusoidal oscillating current is then superimposed on the DC main current. Due to the chosen polarity, the main current is forced to zero within the first half cycle of the oscillation. Under proper conditions, the arc in the vacuum interrupter is extinguished and the current in the main path is interrupted. Then the current commutates into the parallel commutation path, charges the capacitor CC, and the voltage appears across the vacuum interrupter. As soon as the capacitor voltage, uCC, exceeds the protection level of the MOSA in the energy-absorbing path, the MOSA becomes highly conductive and limits the voltage. Now, the current commutates into the energy absorption path, resulting in the energy absorption of the system, and the current is finally suppressed to zero.
MOSA Design for HVDC Circuit Breaker Application
The MOSA is a crucial component for limiting the peak value of the TIV and for absorbing the magnetic energy of the system inductance. For HVDC circuit breaker applications, several columns of varistor blocks, in parallel, are needed to absorb a large amount of energy. Given a specific energy requirement, the required number of varistor blocks will depend on the energy per volume that can be injected to a varistor for safe operation. These varistors need to be arranged in several columns in parallel while taking the residual voltage of columns into account. The largest varistor blocks with the greatest energy handling capability that can be manufactured are preferred in order to limit number of columns. When designing a MOSA for an HVDC circuit breaker application, the following circuit breaker and system related parameters need to be specified:
Transient Interruption Voltage (TIV)
Corresponds to the residual voltage of the MOSA at rated interruption current. This is determined by the height of the active part (varistor column). To suppress the fault current, this voltage must be higher than the system nominal voltage for which the breaker is designed. So far, a factor of 1.5 to 2.0 is assumed to be sufficient with regard to system insulation coordination and current interruption time.
Current
This is determined by the maximum interruption capability of the HVDC circuit breaker in which the MOSA is installed. After all, electric field strength (i.e. voltage per unit height) across the varistors is determined by the current density. By increasing the cross-sectional area of the active part, electric field strength decreases and hence the overall residual voltage. Therefore, it is important to consider the impact of increasing the number of varistor columns on final residual voltage, which equals the TIV.
Listen to Other Online Lectures on Arresters
Nominal Energy
This is the maximum energy that the MOSA can absorb without mechanical/electrical degradation. The volume of the active part determines the maximum energy absorption capability. Although the literature mentions that energies up to 400 J/cm3 can be absorbed by MOSAs, a nominal energy value of 200 J/cm3 during a single absorption period is considered safe for durable service. The MOSA can operate reliably in a temperature range of 100 … 300°C. For an energy of 3.3 J/cm3, the MOSA temperature increases by about 1°C, based on specific heat capacitance. Thus, 200 J/cm3 energy injection results in a temperature increase of about 60°C. Fig. 2 shows an experimental DC circuit breaker set up to investigate the energy absorption capability of MOSAs in a laboratory test supplied by AC short-circuit generators operated at low power frequency.
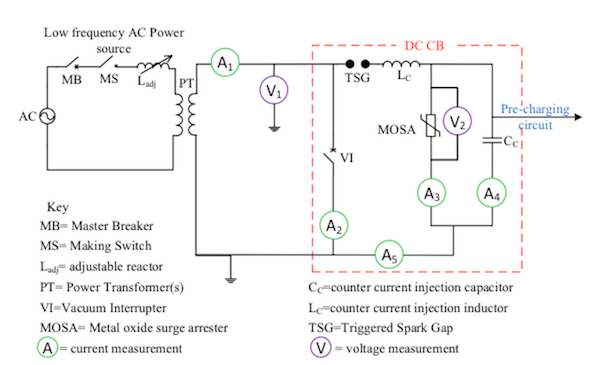
The experimental DC circuit breaker is based on the active current injection DC current interruption principle. It consists of a vacuum interrupter in the main current path and a charged capacitor and inductor in parallel to the main current path. This single break active current injection experimental DC circuit breaker has the following specification:
• Rated interruption current 16 kA
• Maximum interruption current 20 kA
• Rated energy 2 MJ
• TIV (40…45) kV
Based on this information, Fig. 3 shows a 12-column MOSA module design, consisting of 72 MOVs. If more than 2 MJ energy absorption is needed, two or more of these modules can be connected in parallel to share the energy. As discussed, current and voltage are related to each other through electric field strength and current density. The higher the current density, the higher will be the electric field strength. This must be therefore taken into account when designing a multi-column MOSA, since, for any given rated current, the higher the number of columns, the lower will be the current density and, hence, the residual voltage. Depending on the energy absorption requirement, several tens of MOV columns might be needed. Fig. 4 shows the impact of number of columns on residual voltage at a discharge current of 10 kA. As can be seen, a single column has the highest residual voltage whereas a 12-column MOSA has about 17% lower residual voltage. Thus, proper adjustment in height of the active part must be considered if a large number of columns are used in order to account for such reduction in residual voltage.
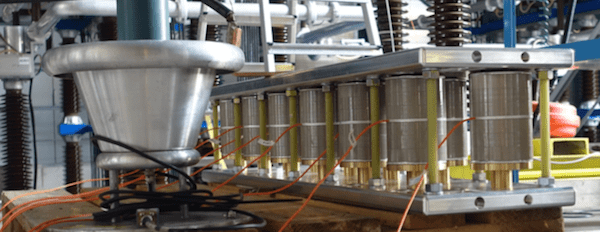
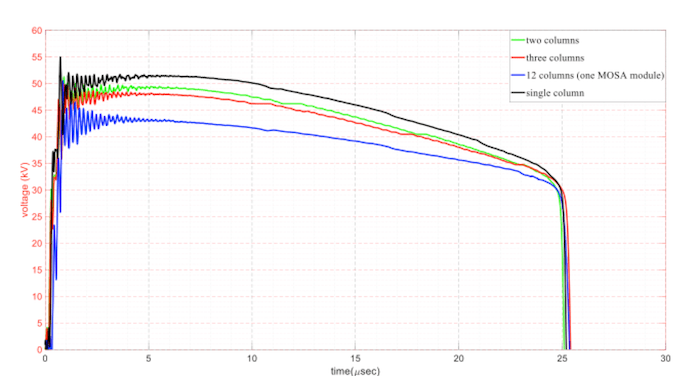
Stresses on MOSAs During DC Fault Current Interruption
Fig. 5 depicts a typical test result of current interruption by an HVDC circuit breaker. Two MOSA modules, connected in series, were used to double the voltage rating since two vacuum interrupters were also connected in series. The electrical stresses, namely current and voltage, of the 12-column MOSA are presented and the black trace in the chart at the top shows the current through the MOSA. The transient overshoots observed were due to interaction of the charged capacitor of the breaker and stray inductance in the MOSA circuit.
From the bottom chart in Fig. 5 it can be seen that the MOSA maintains a TIV of about 77 kV during system current suppression. Unlike in a conventional AC application where MOSAs conduct impulse currents for a short duration (less than a millisecond), it can be seen that the MOSA in the HVDC circuit breaker conducts current for about 9.5 ms. During this period, the current must be equally distributed across the cross-sectional surface of the varistors so as to avoid local overheating, which could lead to failure. Note that the TIV across the vacuum interrupter is slightly higher than the voltage across MOSA due to some stray inductance in the loop. To avoid this difference, the DC CB must be designed compact. For the case shown in Fig. 5, about 5.3 MJ energy is being dissipated in the two series connected MOSA modules, resulting in a temperature rise of about 72°C. Note that the voltage across the MOSA is more or less constant even though system current (through the MOSA) is being reduced. This is due to the fact that, at the start of current suppression, the capacitor (CC) of the breaker is charged to the same voltage as the MOSA voltage and remains charged during the rest of the current suppression period. When MOSA voltage tends to decrease following reduction in system current, the capacitor slightly discharges into the MOSA through LC. However, this discharge is minimal since the voltage difference between the two is also very small. Thus, it does not affect the voltage across the capacitor.
Fig. 6a shows a typical current distribution among the MOSA columns measured during energy absorption. Even if great care is taken in matching the columns, it is still difficult to ensure equal current sharing. The matching criterion in this case, for example, is ±3% current deviation from a reference column. It can be seen that the column with the least current conducts 68% of the current in relation to that of the highest conducting column (see the black trace and the dashed blue trace in Fig. 6a.
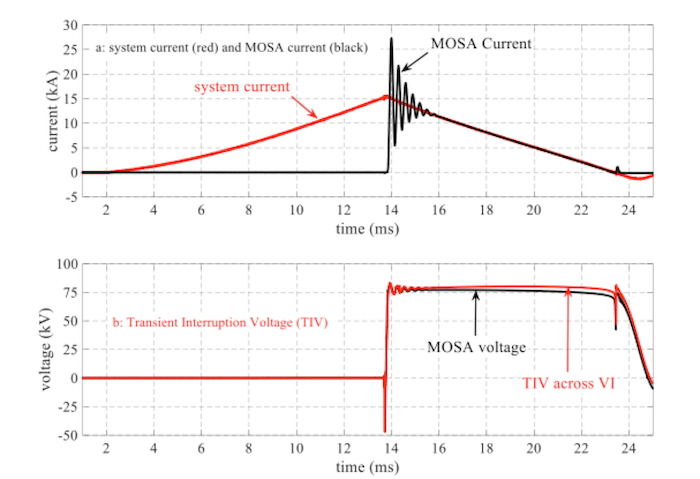
Similarly, the MOSA columns are heated unequally if equal current sharing is not guaranteed. Fig. 6b shows MOSA column temperature measured during energy absorption in DC fault current interruption. For an energy absorption of about 1 MJ into the 12-columns, temperature increases by about 26.5ºC. Energy is injected successively every 5 to 10 minutes to investigate performance of the MOSA at elevated temperatures. Different energy levels (ranging from 70 J/cm³ to 220 J/cm3) are injected at temperatures as high as 200°C. The MOSA performs reliably when the energy injection does not exceed 200 J/cm3. The slight temperature deviation observed in Fig. 6b is due partly to unequal current sharing and partly to the differences in cooling as a result of the column arrangement. The energy absorbed by the MOSA at each test is also labeled. In order to investigate the performance of the MOSA at elevated temperatures, several tests were performed successively. Fig. 6b depicts temperature rise during each current interruption.
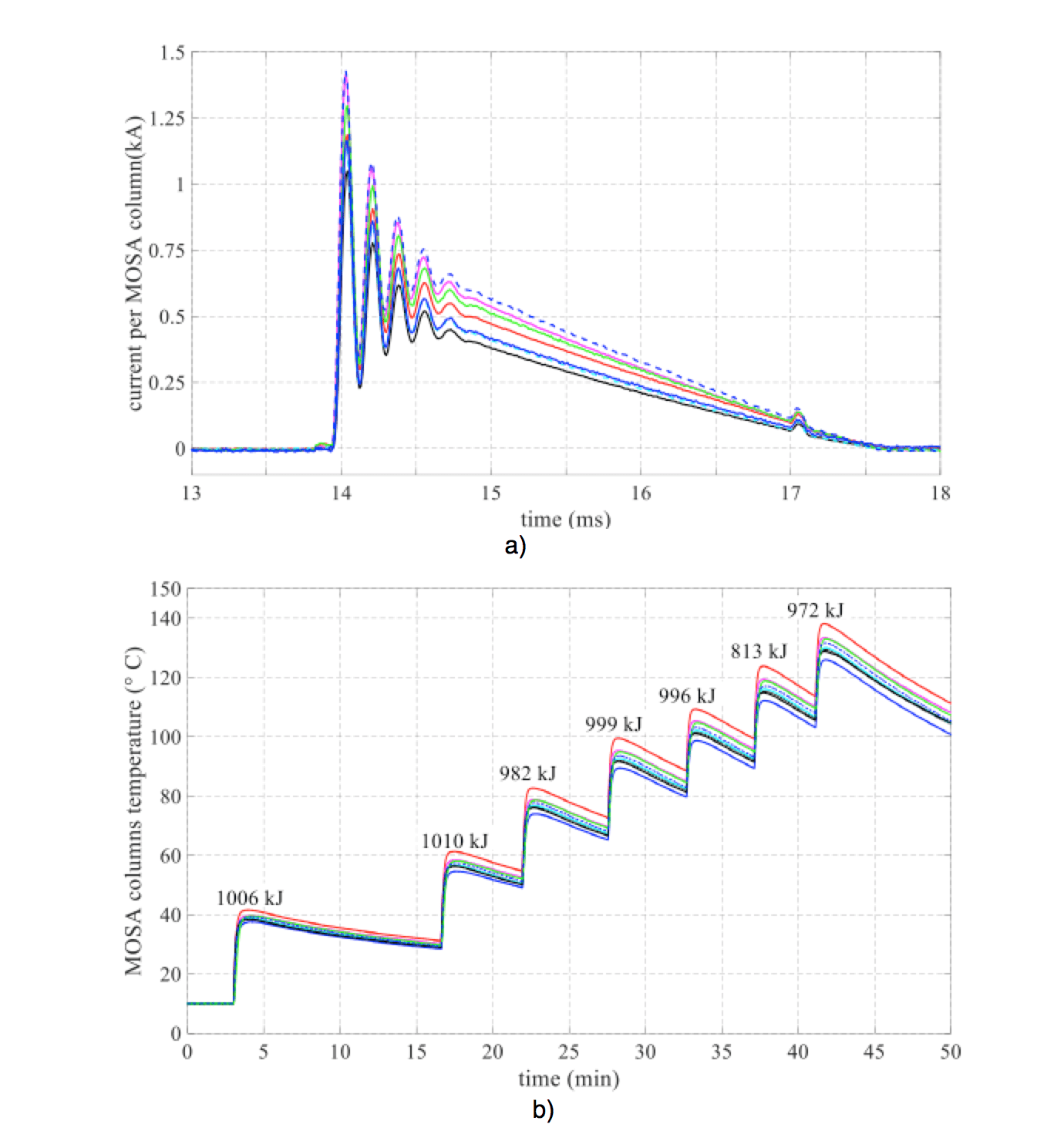
b) Temperature measurement during successive energy absorption by MOSA.
Figs. 7a and b show thermal images of MOSAs after energy absorption. Fig. 7a shows the thermal image after successive energy absorption to the model MOSA arrangement. Fig. 7b shows, as an example of a MOSA with higher voltage rating, the impact of typical unequal current sharing among columns and thereby unequal heating of columns. This MOSA is from a different project but included here just for the sake of offering a comparison. In Fig. 6b, it can be seen that one of the columns is drawing more current than the others and, as a result, heats up to higher values. This is an observation at much lower energy absorption and such an effect could cause failure if a nominal energy higher than 200 J/cm3 is rated and that energy injected.
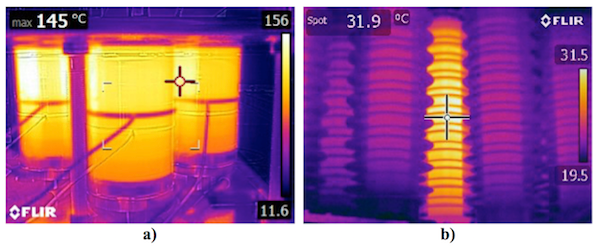
Ageing Phenomena of MOSAs in DC Circuit Breakers
Aging phenomena of MOSAs in AC grids are now generally well understood and experienced manufacturers know how to control the various parameters of their designs to change the properties. However, the stresses experienced by a MOSA used in an HVDC circuit breaker application are different, as described above, with their main task being energy absorption during the current interruption process. When the DC CB is in the ‘on-state’, the MOSA is short-circuited by the main current path (the VI shown in Fig. 1). This allows the MOSA to de-polarize and there is no leakage current under normal conditions. After the DC CB turns into ‘off-state’, the MOSA is exposed to an impulse with fast rise time and a long time to half value (these impulse values will be discussed below). In general, a DC CB should be operated in series with disconnect switches but during the time period of its operation up to the opening of the disconnect switch, the MOSA must withstand the DC voltage.
Ageing: Test Set-up & Test Cycle
To systematically investigate ageing phenomena of MOSAs in DC circuit breaker applications, an endurance test circuit for testing individual MOVs was set up (see Fig. 8). Test samples were stressed by up to 15,000 impulses and a DC voltage was applied for a short time directly after impulse injection. The test circuit was designed to fulfill requirement for the current impulse, as described above, and the equivalent circuit of the set-up consisted of:
• switch S2 is for depolarization of the MOV;
• capacitor C, the resistor R, the inductance L and the switch S1 are generating the impulse;
• DC source and the switch S3 are generating a DC stress after the impulse current.
The initial switch positions were: S1 open, S2 closed and S3 open. During charging time of C, switch S2 was closed and the MOSA could then de-polarize for about 60s. Once the capacitor was fully charged, switch S2 opened and switch S1 was closed, thereby generating the desired impulse for the MOV. Impulse parameters are determined by R, L and the MOV itself. After the impulse, S1 opened and S2 remained open. S3 was closed and the MOV was subjected to DC stress from the DC source for 2s. After opening S3, the cycle starts again. During the whole test cycle, capacitor voltage and MOV temperature were monitored constantly while impulse current and voltage were measured with an oscilloscope. Oscilloscope data was transferred to LabVIEW for further calculations and test stand control.
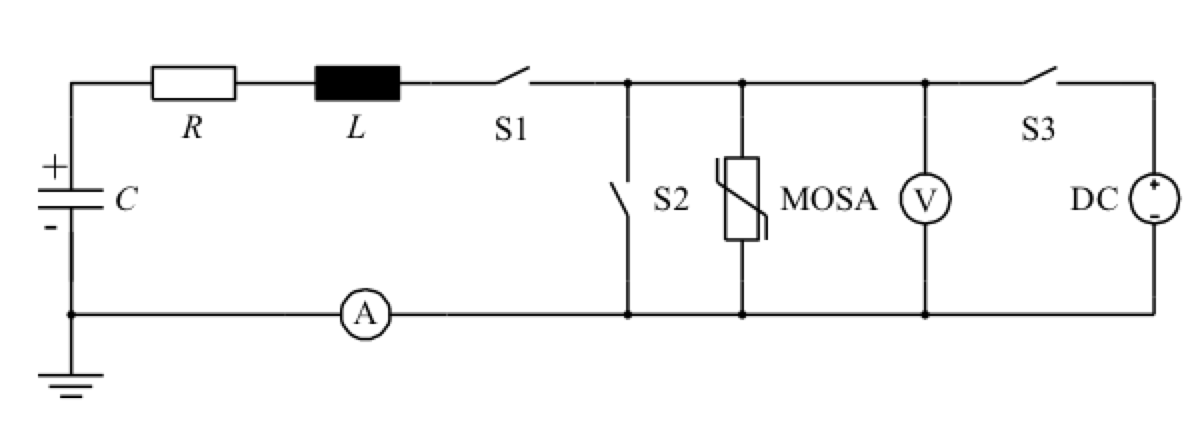
The charging voltage of the capacitor, C, and the residual voltage of the MOV determine the amount of energy injected into the MOV. The values of R, L and the characteristics of the MOV itself determine rise time and time to half value. Test samples were exposed to open air and their temperatures kept below the limit of 65°C due to the critical value 75°C, i.e. below 75°C ensures that the MOV ages only electrically while above 75°C there might also be thermal ageing processes. The endurance test stand was able to produce two types of high current impulses. The first investigations were performed with 50/1500 impulses. This impulse shape represented the parameters and stress of a MOSA determined in this project based on consultation with an industrial partner and also on an earlier investigation. Important parameters for the impulse were: values of the RLC circuit in the commutation path; MOSAs residual voltage in comparison to system voltage; and conduction mechanism of the MOSA.
After testing 8 MOV samples, impulse shape was changed to a 20/900 impulse. This higher current rate-of-rise and amplitude, imposed more severe stress on the MOV in terms of electrical ageing. While rise time was decreased from 50µs to 20µs and time to half value from 1500µs to 900µs, current peak values increased from 730A to 1330A. Figs. 9 & 10 compare the two impulses, with blue indicating the 50/1500 impulse and green the 20/900 impulse. Table 2 shows parameters of these impulses.
Due to experimental restrictions of the endurance test stand, the energy stored in capacitor, C, could not be too high and specimens with small dimensions (i.e. small volume) therefore had to be used. Specimens for this test series were manufactured from the same DC stable type as the larger MOVs and specifications of the varistors being investigated were:
• Type: DC-stable
• Nominal energy handling: 200 J/cm3
• UC = 1 kV DC
• Iref = 1 mA DC
• Uref = 1.33 – 1.5 kV DC
• U10 kA = 2.25 kV
• In = 10 kA
• h ≈ 6.35mm
• D ≈ 70mm
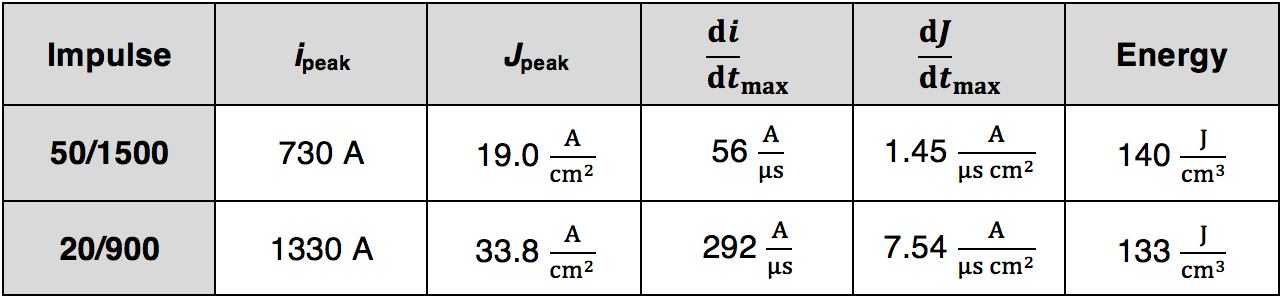
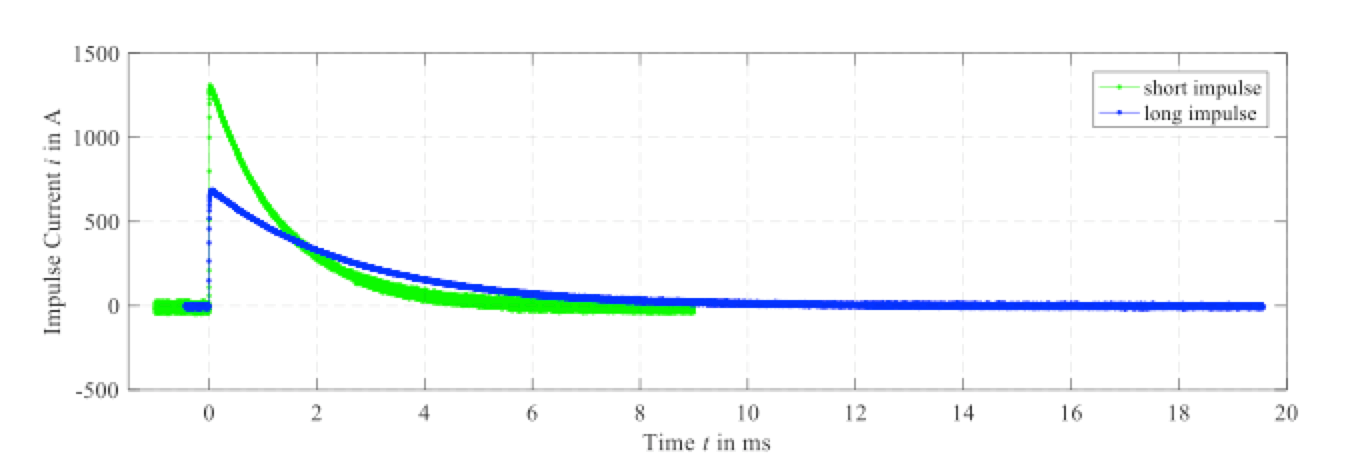
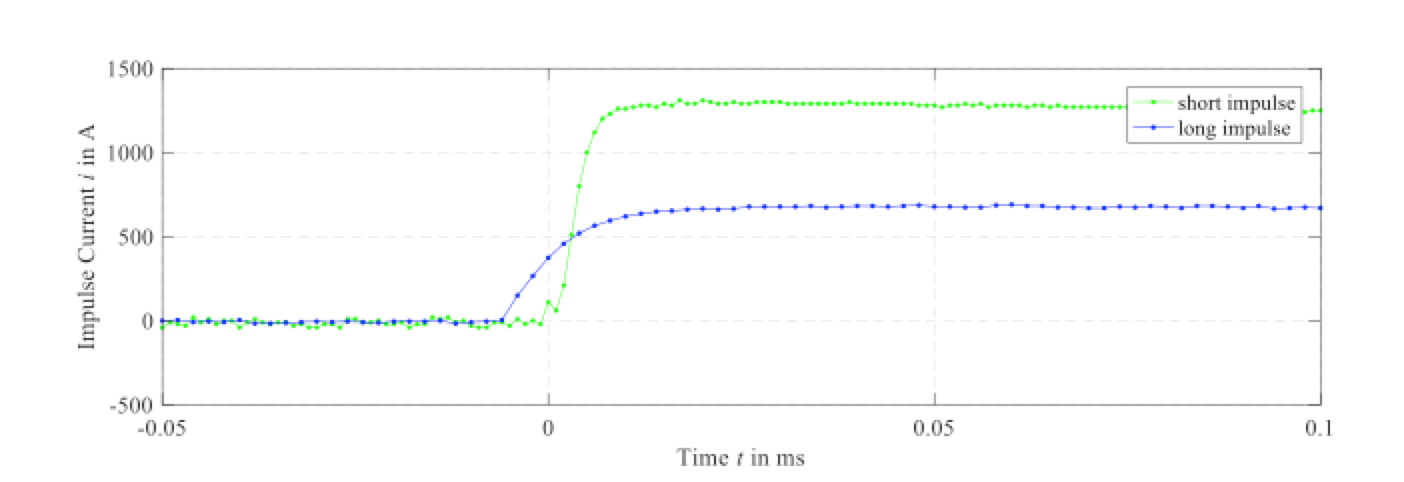
Endurance Test Procedure
The endurance test procedure requires interruptions for intermediate electrical characterization of the MOV. The overall test procedure for an MOV is performed as follows:
• Electrical characterization of new MOV;
• 5000 Impulses;
• Electrical characterization after 5000 impulses;
• 5000 Impulses;
• Electrical characterization after 10,000 impulses;
• 5000 Impulses;
• Electrical characterization after 15,000 impulses;
• Determination of failure energy (destructive test);
• Procedure completed.
Characterization of the MOV was performed for two regions of its voltage-current-characteristic: the leakage current region; and the protection level current region. The leakage current region was measured with an automated DC test stand. Because of the small DC voltage applied to the MOSA and small current magnitudes, leakage current measurements were performed at 35°C to eliminate any effect of temperature. Current ranged from 10nA up to 10mA. Applied voltage steps were pre-determined during preceding investigations on dummy MOVs.
To ensure high repeatability, recording of current measurement started automatically with a delay of 10s after voltage was applied. Due to extremely low measurement amplitudes, the test stand was equipped with a reference MOV that served only to monitor the DC test stand, with no other stress applied. No changes in reference MOV characterization measurements could be observed over the entire test duration. It could therefore be concluded that the DC test stand resulted in reproducible results, with no impact on possible ageing phenomena. Characterization in the protection level region was measured with a double exponential current impulse generator and an impulse of 8/20µs. Measurements were taken at room temperature. Residual voltage was measured at 2.5 kA, 5 kA and 10 kA peak current. Moreover, the voltage-current-characteristic in the current range between 150A and 750A was investigated using the 50/1500 impulse.
Evaluation of Measured Data
Fig. 11 shows the typical electric field current density (E J) characteristic of one of the MOVs during the ageing process for the different number of impulse applications. Characterization was always performed in positive and negative current flow directions through the MOV. Only the positive direction, however, is shown here. Ageing phenomena of the MOV can clearly be seen in the leakage current region. The new and the aged characteristics cross one another at a certain point, i.e. they are rotated counter-clockwise around a center at about 188 V/mm by the impulse stress. The crossing is representative of the specific MOVs used. This behavior can usually be accepted since MOSAs used in a HVDC CB application are not continuously stressed by an applied voltage and leakage current is typically not an issue. Ageing of the MOV can be observed as well in the protection level region. Ageing results in an increase in protection level, in this case by about 5.5% maximum after 15,000 impulses. This is slightly above the 5% increase generally tolerated in IEC arrester standards.
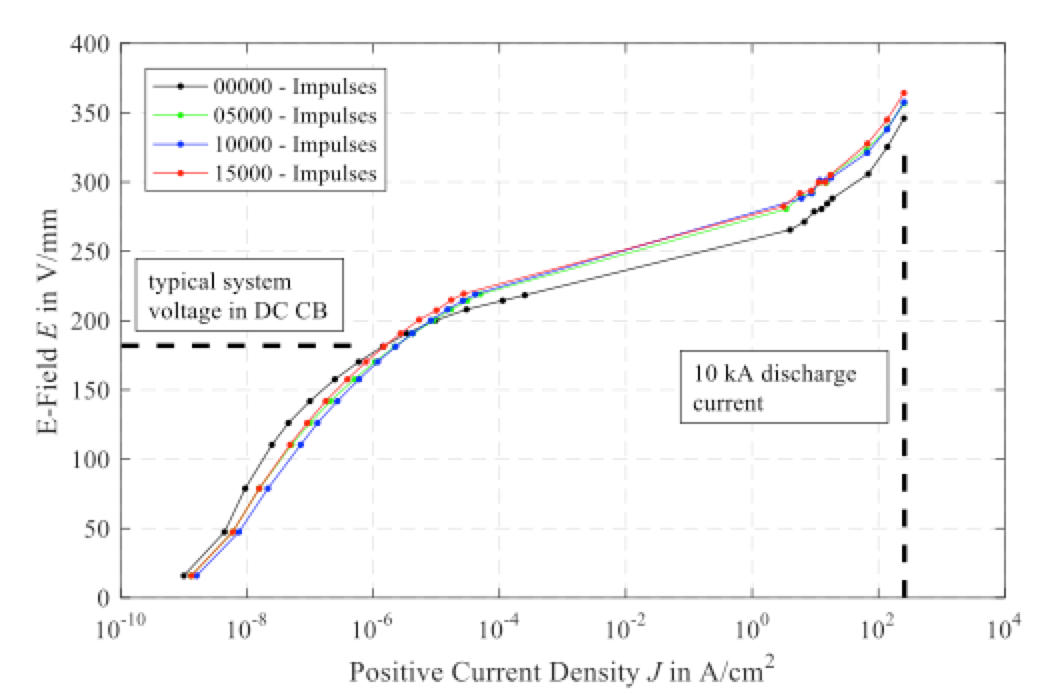
Figs. 12 & 13 summarize results for all 11 specimens for the two characteristic values in the voltage-current-characteristic. The broad bars show average values of the test series while the small black bars show the range of variation. The color coordination in Figs. 12 and 13 has the same orientation as Fig. 11. The residual voltage change at 10 kA discharge current determines if the MOV is still working properly, in other words if it can still fulfill its protection task. According to [9] and [11] the MOV would fail a test if the change of the residual voltage is higher than 5 %. For comparison of the leakage current in Fig. 12, the measuring results are normalized to the initial leakage current value of the unstressed MOV. At a given operating voltage level the leakage current is increased, for the measurements in negative direction more than in positive direction. However, this finding is less important for the HVDC CB application, as there is no continuous flow of leakage current. The evaluation of the residual voltage at 10 kA shall be discussed in more detail. The endurance test setup with 15,000 impulses produces more severe stress to the MOV than it normally has to handle in a DC CB during its lifetime. A CB should be able to handle 2 000 to 10,000 switching events, a number classified for mechanical switching. Electrical stress during these switching events can vary, from mostly small load currents up to rare large short-circuit currents.
The endurance test set-up simulates electrical stress of short circuit energy absorption on the MOV. Fig. 13 therefore indicates increase in residual voltage after 5000, 10,000 and 15,000 impulses in percentage terms with reference to the measured value of the unstressed MOV. Results after 15,000 impulses are caused by an unrealistically high stress but are interesting for investigating ageing of the MOV and to determine design limits. After 5000 impulses, none of the specimens is above the 5% margin. After 10,000 and 15,000 impulses only very few specimens slightly exceed the 5% level. But the average value of the test series is still below the critical margin. By comparing the E J characteristics of all specimens, the characteristics after 5000 impulses is very close to the characteristics after 15,000 impulses. The curve after 10,000 impulses is even closer. It has to be discussed if the threshold according to IEC 60099-9 can actually be used for DC CBs and also how many switching operations under high current stress the MOSA shall be able to withstand without notable degradation. Pass criteria do not take an impulse stress of several thousand impulses into account. Rather, only a few tens of impulses. From this point of view, the test result (maximum increase of <5 % after 5000 impulses, and an average increase of <5 % after 10,000 and 15,000 impulses) seems promising.
The TIV during load current and a short circuit current switching event reaches the same amplitude. However, due to the larger magnetic energy of the short-circuit event, the MOSA has to deal with much higher energy absorption (e.g. its full rated energy handling capability). If this high-energy absorption happens less than 5000 times during the life of a DC CB, all MOVs are within the so far tolerated increase in clamping voltage. But switching such high currents 5000 times in any DC grid seems unrealistic. The main task of a MOSA in a DC CB application is not to limit to a certain voltage and the slight increase in residual voltage of the DC CB should therefore not be viewed as critical. The main requirement is to absorb large amounts of energy and, as shown in Table 3, energy absorption capability becomes even better after impulse current stress.
[caption id="attachment_42307" align="aligncenter" width="511"] Fig. 12: Normalized changes of leakage current at typical system voltage in DC CB after 5000, 10,000 & 15,000 impulses. a) Positive current direction, b) Negative current direction.[/caption]
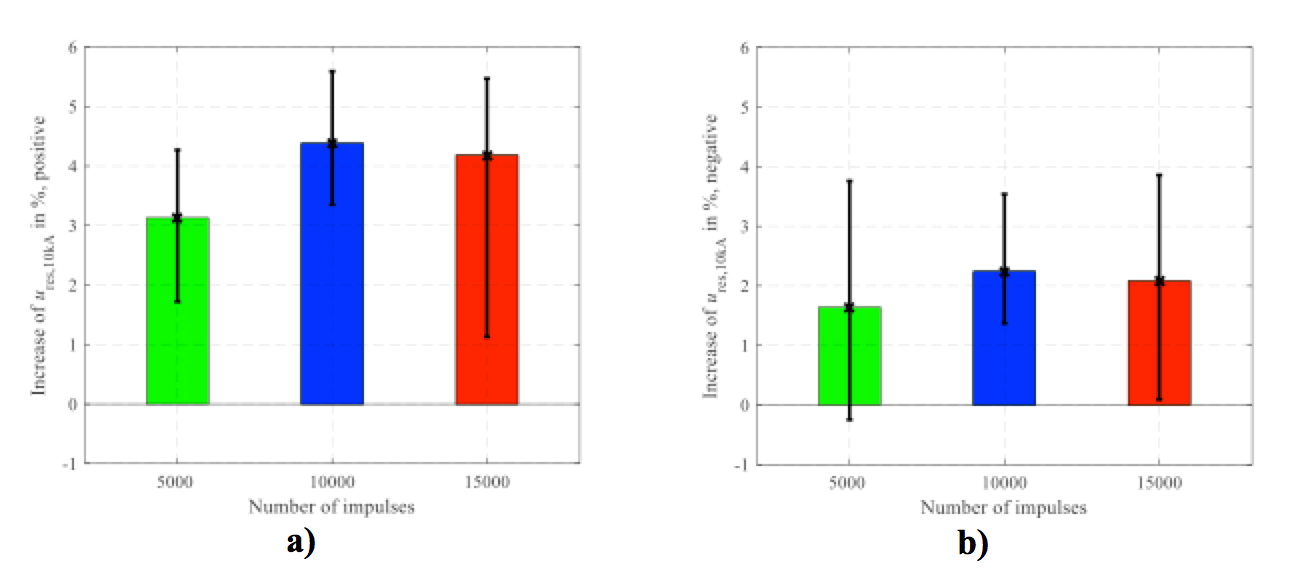
Comparing each individual change in leakage current, residual voltage and characterization curves between the 50/15,000 and the 20/900 impulse, the 20/900 should be the more critical for the MOV. But results show that specimens stressed with 20/900 impulse behave like all others and there is no significant higher stress for the MOV. This leads to the assumption that the current rate of rise and amplitude are manageable and the injected amount of energy seems the main factor in ageing.
The final investigation of MOVs is the failure energy test. This is performed with alternating current in the range of 200A peak value since this is an effective way to quickly determine changes in failure energy. Current flows until mechanical damage of the specimen. Failure energy was measured for 12 unstressed MOVs as well as the 11 MOVs stressed in the previous endurance test procedure and Table 3 lists the findings.
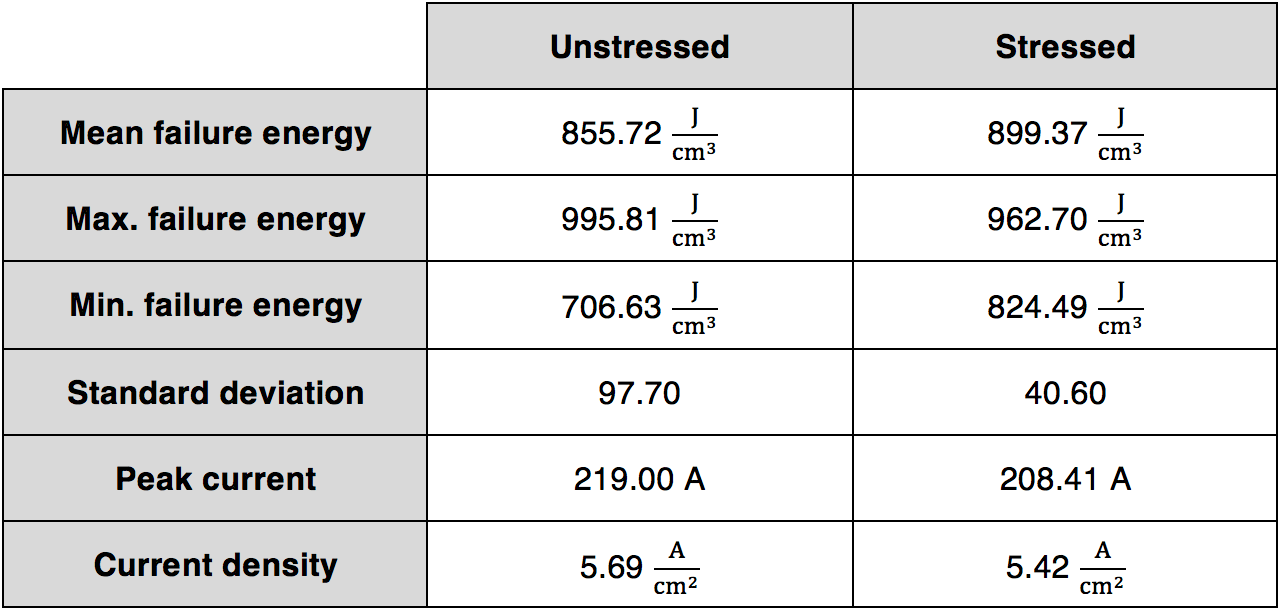
Mean failure energy of stressed MOVs is 5.1% higher compared to unstressed MOVs. While an actual increase in failure energy seems questionable, it can however be concluded that failure energy is definitely not decreased by the endurance test. In particular, the standard deviation is remarkable, i.e. reduced by a factor of 0.41. This suggests that conditioning of the MOVs by the endurance test has some ‘leveling’ effect. The material of stressed MOVs might be more homogeneous after repeated energy stress. This could be a positive for large MOSA banks in DC CBs since high energy stress might be better distributed between the columns after several switching events.
Conclusions
Ongoing research on HVDC CBs is crucial for multi-terminal, meshed HVDC grids and the MOSA is an essential component of this equipment. Most papers focus on fundamental functionality of the DC CB and deep investigations into their sub-components are therefore still rare. This research has dealt specifically with the duties and stresses of the MOSA in this application as well as differences between it as a protection unit and its use in DC CBs.
The main task for the MOSA in a DC CB is to handle the TIV stress and the energy to be consumed during a DC switching event. A basic introduction into DC switching using the example of a DC CB with mechanical switching element (VI) and active commutation path has been provided to allow better understanding of MOSA stress. Due to the large energy consumption the MOSA has to deal with, several design issues with respect to energy handling, current distribution and TIV have been discussed. In summary, the energy handling and the TIV determine the amount of paralleled MOSA columns to be used. But it also has to be noted that, with more MOSA columns in parallel, the TIV drops slightly.
A large MOSA set-up was investigated during several HVDC switching tests and temperature as well as current distribution through each column was monitored. Differences in temperature rise and current distribution were discussed and maximum energy and temperature handling investigated. Moreover, ageing of MOVs used in the MOSA was investigated using a customized endurance test stand allowing all the stresses in a DC CB to be simulated. As a result, the MOSA is expected to withstand the stresses over the service life of a CB. The E-J-characteristic was measured before, during and after the ageing process. Criteria from CIGRE TB 544 and IEC 60099-9 were used for comparison of the unstressed and stressed MOSAs. Only one specific MOV brand could be investigated in this project and, to allow more comprehensive data on MOSA behavior in a DC CB application, more brands will need to be investigated.
Acknowledgments
The works on surge arresters in an experimental DC CB in this paper are supported by funding from European Union’s horizon 2020 research and innovation program under grant agreement No. 691714. References
[1] N. A. Belda and R. P. P. Smeets, “Test Circuits for HVDC Circuit Breakers,” IEEE Transaction on Power Delivery, vol. 32, no. 1, pp. 285 – 293, 2017.
[2] C. M. Franck, “HVDC Circuit Breakers: A Review Identifying Future Research Needs,” IEEE Transaction on Power Delivery, vol. 26, no. 2, pp. 998 – 1007, 2011.
[3] T. Heinz, Gleichstromschalten in der Mittel- und Hochspannungstechnik unter Einsatz von Vakuumschaltröhren, Darmstadt, Germany: TU Darmstadt, 2017.
[4] V. Hinrichsen, Metal-Oxide Surge Arresters in High-Voltage Power Systems, Berlin and Darmstadt: Siemens, 2011.
[5] M. Tuczek, Experimental Investigations of the Multiple Impulse Energy Handling Capability of Metal-Oxide Varistors for Applications in Electrical Power Engineering, Darmstadt, Germany: TU Darmstadt, 2015.
[6] W. Bassi and H. Tatizawa, “Early Prediction of Surge Arrester Failures by Dielectric Characterization,” IEEE Electrical Insulation Magazine, vol. 32, no. 2, pp. 35-42, 2016.
[7] N. A. Belda, C. A. Plet and R. P. P. Smeets, “Full-Power Test of HVDC Circuit-Breakers with AC Short-Circuit Generators Operated at low Power Frequency,” IEEE Transactions on Power Delivery ( Early Access ), pp. 1-1, 2019.
[8] CIGRE TB 544, “MO Surge Arresters – Stresses and Test Procedures,” CIGRE, Paris, 2013.
[9] IEC 60099-9, Surge arresters – Part 9: Metal-oxide surge arresters without gaps for HVDC converter stations, IEC Standards, 2014.
[10] M. Bröker and V. Hinrichsen, “Testing Metal-Oxide Varistors for HVDC Breaker Application,” IEEE Transaction on Power Delivery, vol. 34, no. 1, pp. 346 – 352, 2019.
[11] IEC 60099-4, Surge arresters – Part 4: Metal-oxide surge arresters without gaps for a.c. systems, IEC standards, 2014. [12] IEC62271-100, High-voltage switchgear and controlgear – Part 100: Alternating-current circuit-breakers, IEC Standards, 2008.