En todo el mundo, las empresas de servicios básicos experimentan contaminación inducida ambientalmente en los aisladores y esta puede llevar al deterioro rápido del desempeño a tensión de voltaje nominal. La magnitud de este problema varía de lugar en lugar, incluso dentro del mismo sistema, ya que se pueden experimentar contaminantes y mecanismos de transferencia distintos. Esto puede generar un impacto general único, especialmente cuando se toman en cuenta las propiedades de la aislación existente. Por lo general, el problema es más grave en las líneas de transmisión debido a la variedad de las condiciones de servicio que pueden experimentar a lo largo de su trazado. Incluso, se pueden detectar diferencias sútiles de torre en torre, como cuando una está en la cima de un cerro y la siguiente está ubicada en un valle más lejos.
Como parte de la lucha por mantener la instalación exterior operando sin falla y con contaminación ambiental, se han propuesto varios métodos. En este artículo editado para la INMR, escrito por el consultor Dr. Kiriakos Siderakis, se investigó el problema del mantenimiento en condiciones de contaminación para el caso de las subestaciones que tienen una experiencia de servicio que lucha contra este problema en la isla griega de Creta.
Subestaciones de Alto Voltaje
La subestación de alto voltaje es un nodo en el sistema de transmisión y cualquier apagón en ella, por lo general, corresponde a un impacto mucho más grave en un sistema eléctrico que lo que lo es un incidente correspondiente en una línea de transmisión. Por lo tanto, desde el punto de vista de la confiabilidad, el mantenimiento de una subestación tiene una importancia considerable, que solo crece con el correspondiente aumento en el número de circuitos de transmisión conectados. Afortunadamente, en lo que a contaminación respecta, en el caso de las subestaciones, existen dos ventajas importantes si se compara con el mismo problema en las líneas aéreas. Primero, una subestación es una instalación concentrada geográficamente y, por lo tanto, las condiciones ambientales que la afectan tienden a ser más uniformes. Segundo, la mayor parte de las subestaciones son supervisadas de manera local por el personal o de manera remota. En consecuencia, se puede detectar el desarrollo de cualquier problema de contaminación y se pueden aplicar a tiempo las medidas correctivas adecuadas. Esto explica por qué la incidencia de la contaminación relacionada con los apagones en las subestaciones es relativamente pequeña si se compara con las líneas de trasmisión.
Sin embargo, aún existen variables que pueden complicar cualquier esfuerzo por encontrar soluciones permanentes para las subestaciones. Una es el hecho de que puede haber un gran número de aisladores diferentes que se utilizan en aplicaciones de equipos diversos tales como CTs, VTs, manguitos aisladores, postes de estación, pararrayos, etc. Puede que cada uno tenga geometrías distintas y, por lo tanto, esté sujeto a un desempeño en condiciones de contaminación y requerimientos de mantenimiento diferentes. Además, hasta por lo menos unos años atrás, la amplia disponibilidad de cubiertas poliméricas para las aplicaciones de subestaciones aún era limitada.
Contaminación en el proceso de diseño
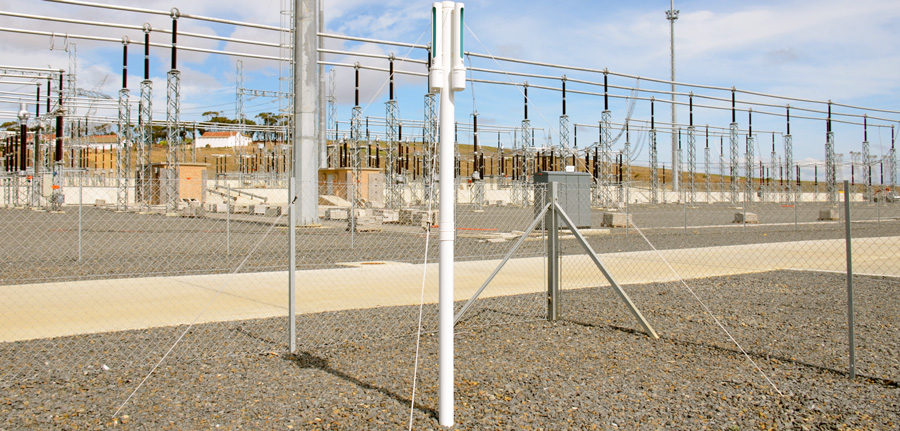
En el caso de la instalación de una subestación nueva donde es probable que los problemas de contaminación sean una preocupación, existen métodos y soluciones disponibles para restringir o incluso eliminar la posible influencia negativa del medioambiente. La Tabla n.° 1 resume los aspectos que, por lo general, se consideran durante el proceso de diseño.

El primer paso es la selección de los parámetros de aislación y la distancia de fuga. Los valores requeridos se pueden determinar con la Norma IEC 60815 que recomienda la distancia de fuga específica según el tipo y la intensidad de la contaminación ambiental. También es importante la geometría del aislador y la selección de un perfil adecuado debe apuntar al uso de mecanismos de autolimpieza. De lo contrario, aún se pueden experimentar problemas, incluso cuando se satisface el criterio de distancia de fuga básico. Por ejemplo,estas situaciones se han experimentado en Creta.
>El uso de materiales poliméricos de aislación que proveen una superficie hidrofóbica ofrece un desempeño mejorado en condiciones de contaminación que también se debería considerar. Pero entonces, la esperanza de vida útil de estos aisladores se convierte en otro factor que hay que considerar, en especial porque el costo de su cambio puede ser alto y la disponibilidad es otro problema. Más aún, incluso con esos materiales, aún se debe evaluar la geometría más adecuada para el aislador.
Por ejemplo, se monitorearon los aisladores tipo poste de silicona nuevos en una subestación de 150 kV en Creta luego de su instalación con un sistema de medición de corriente de fuga. A pesar de que es evidente que los aisladores demostraron un desempeño satisfactorio, se registró un aumento en la actividad cuando llovía y lo más probable es que esto se deba a su geometría. La Figura n.° 2b muestra una forma de onda de una corriente de fuga típica que demuestra este efecto.
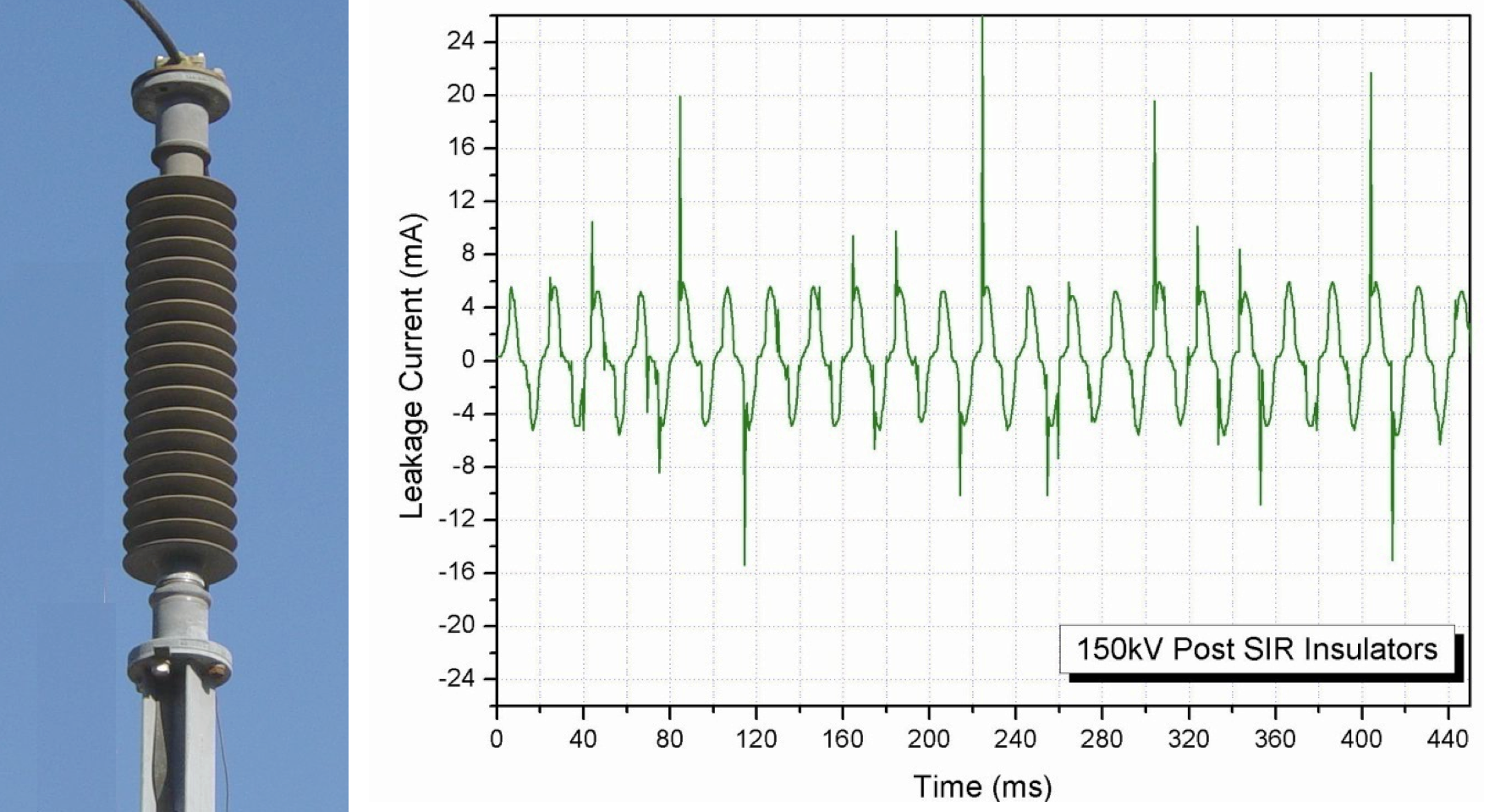
El esquema de la subestación también es un asunto que impacta la política de mantenimiento contra la contaminación. Por ejemplo, en Grecia, el lavado en vivo con agua no es una opción y, por lo tanto,debe haber disponible diferentes esquemas de suministro para evitar interrupciones importantes de energía y así, mantener los niveles de alta confiabilidad. Por lo general, el esquema implementado para lidiar con esta limitante utiliza sistemas bus múltiples e interruptores automáticos seccionalizadores.
Finalmente, si los problemas de contaminación esperados son graves e inevitables, se debería considerar la construcción de subestaciones indoor. La mayor parte de las subestaciones de 150 kV/20 kV en Creta están parcialmente indoor con solo el lado de 150 kV expuesto al ambiente exterior. Además, se encerró por completo una subestación aislada por aire de 66 kV particularmente problemática. A pesar de que en estos dos casos los problemas inducidos ambientalmente y que afectan a los aisladores son limitados, aún sigue siendo necesario algo de control de la atmósfera en las subestaciones encerradas debido al riesgo de fenómenos como la condensación.
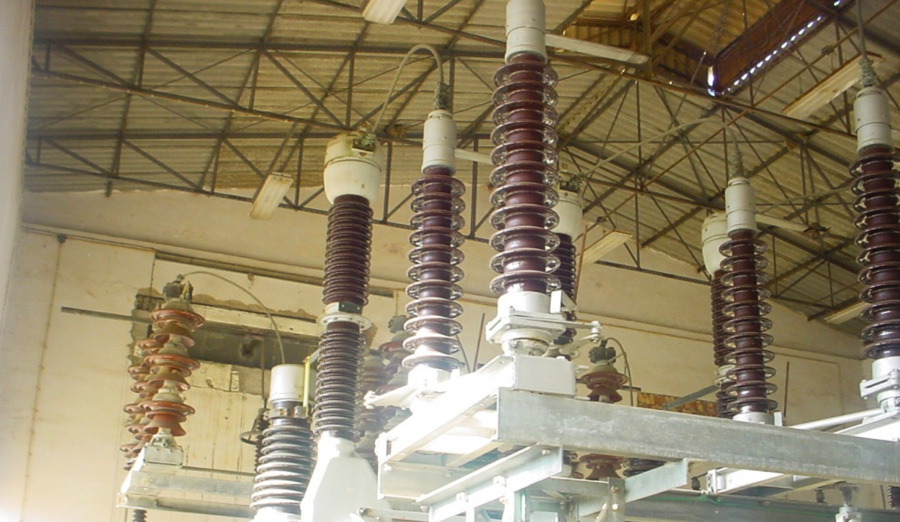
Un esquema de subestación que es completamente resistente al impacto medioambiental desde el inicio es una instalación GIS (es decir, completamente indoor en SF6). A pesar de que el riesgo de cualquier problema relacionado con la contaminación es virtualmente eliminado y que también hay un ahorro de espacio, otros temas que hay que considerar son, por ejemplo, los costos de mantenimiento e instalación.
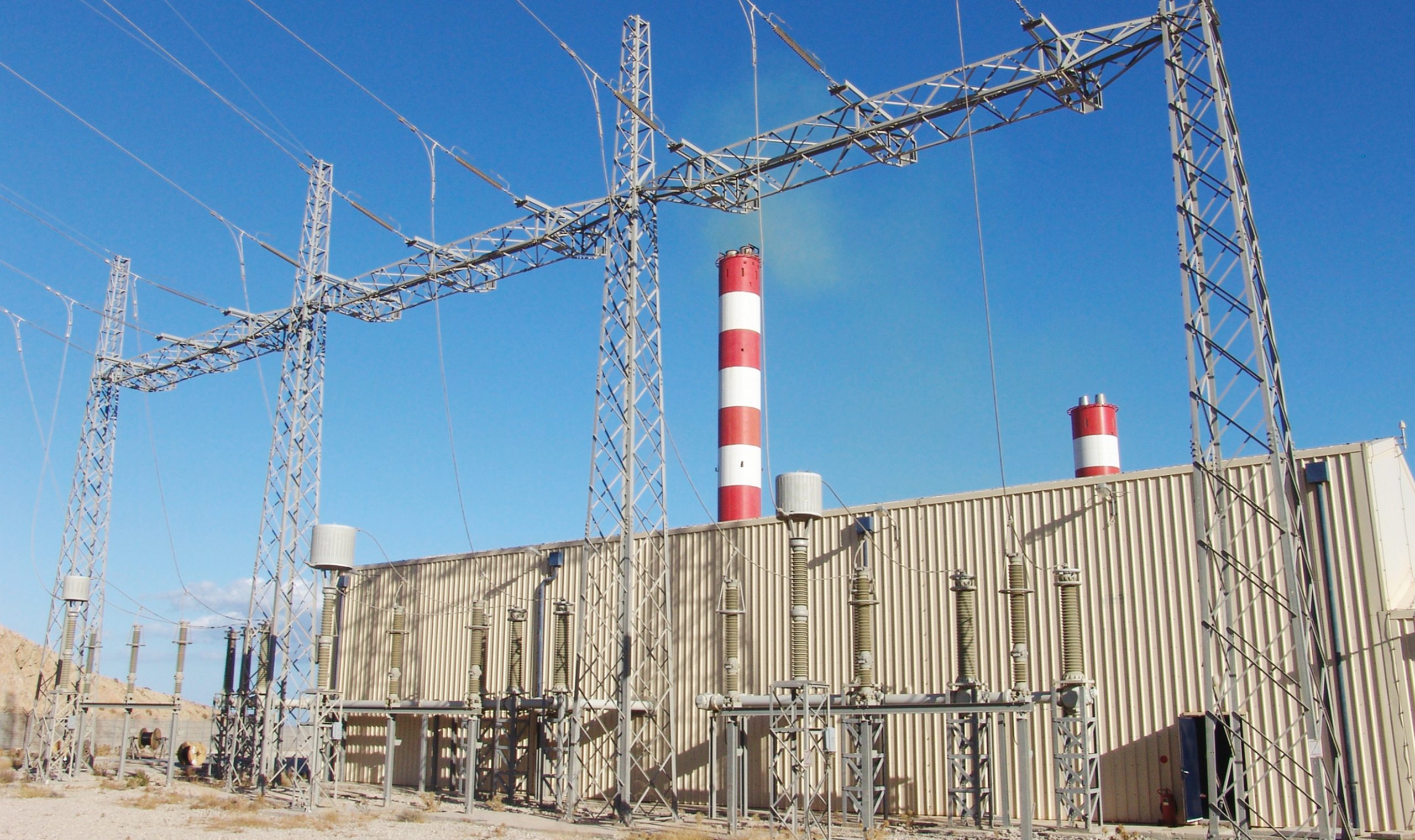
Mantenimiento en Condiciones de Contaminación en las Subestaciones existentes
En el caso del equipo que ya está en servicio en las subestaciones, la inversión gradual para aplicar las medidas correctivas descritas en la Tabla n.° 1 puede ser considerable. Por lo tanto, se pueden encontrar medidas alternativas para mejorar el desempeño de la aislación existente. Por lo general, la primera acción que se toma con respecto a esto es la limpieza de los aisladores afectados. La Tabla n.° 2 describe los distintos métodos de limpieza que luego se seleccionan según parámetros como el número de aisladores que se deben limpiar, los contaminantes específicos que se deben eliminar, los posibles subproductos y los costos de aplicación correspondientes. Estos métodos se facilitan por el hecho de que, por lo general, los aisladores afectados están ubicados relativamente cercanos entre sí.

Para todos los métodos de limpieza diferentes, el factor clave es la selección del tiempo óptimo para limpiar. Por lo general, este es un parámetro que se basa en la experiencia que depende de las condiciones locales del servicio. Si la limpieza se realiza antes de que sea necesario, aún puede ocurrir una acumulación crítica de contaminantes dentro de un tiempo relativamente corto y el problema básico seguirá existiendo. Por otra parte, mientras más se retrase la limpieza, mayor será la probabilidad de que la contaminación gatille un apagón.
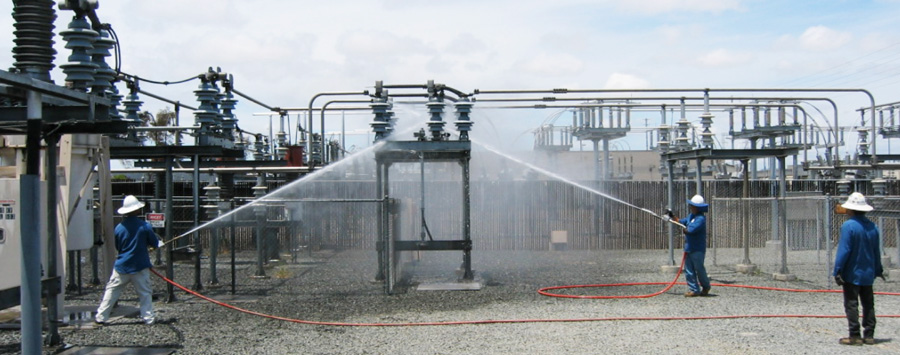
Por lo general, la mayor parte de los procedimientos de limpieza tiene un costo considerable, especialmente si no se pueden aplicar en vivo. En este caso, se requiere la interrupción del suministro. Esto corresponde al deterioro en la disponibilidad del sistema ya que una parte de la subestación se deja fuera de servicio. También puede que haya alguna pérdida financiera ya que puede que sea necesario interrumpir el suministro de energía a un número de consumidores. Cabe destacar que esta pérdida puede aumentar de manera significativa en el caso de las subestaciones elevadoras, por ejemplo, si debido a la interrupción del suministro una o más unidades eléctricas se deben sacar de operación por varias horas. Un caso como ese se registro en Creta a principios de los años 2000 cuando se hizo necesario limpiar una subestación al menos dos veces cada verano. Además, también se deben tomar en cuenta las horas hombre totales requeridas, si se considera que la limpieza del aislador se realiza durante las horas de carga baja, es decir, durante la noche o temprano en la mañana.
Si bien la limpieza de los aisladores es por cierto una manera de asegurar el rendimiento en condiciones de contaminación,la selección del tiempo de limpieza óptimo es crítica (ya que es una reacción y no una medida preventiva) y se deben calcular todos los costos asociados, especialmente si no se aplican en vivo. Por estas razones, un enfoque más avanzado apunta a mejorar el desempeño superficial correspondiente de los aisladores en condiciones de contaminación. Existen distintos tipos de revestimientos para los aisladores, sin embargo los tipos más comunes son los revestimientos de grasa de silicona y de silicona RTV. Su uso constituye un método preventivo ya que se pueden aplicar en un momento conveniente para la empresa de servicios básicos. Durante su vida útil operacional, estos revestimientos son capaces de suprimir el impacto de la contaminación y eliminar cualquier problema relacionado con la aislación. En ambos casos, la supresión de la corriente de fuga se logra con una superficie repelente al agua que no permita la formación de una capa superficial de contaminantes conductores. La diferencia principal entre los dos, es el método que utilizan para mantener la repelencia al agua, incluso a medida que los contaminantes se depositan en la superficie.
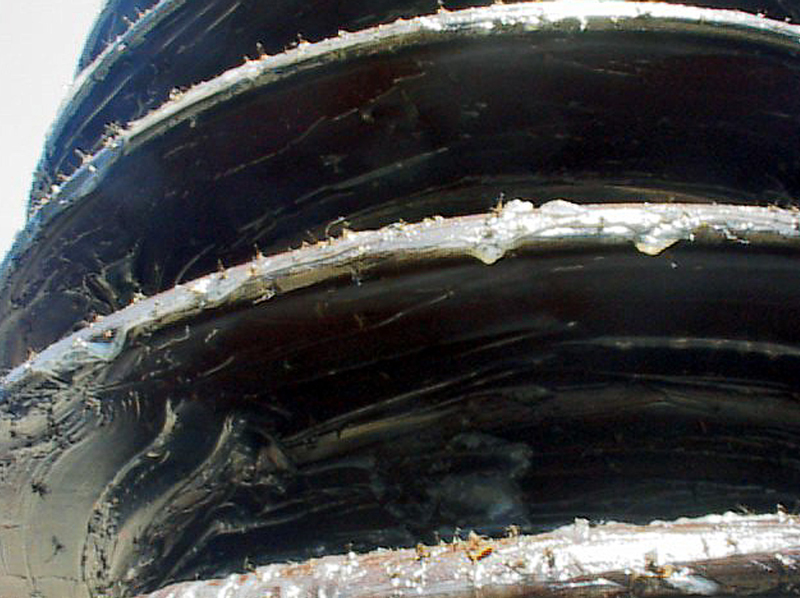
En el caso de la grasa de silicona, toda la contaminación depositada se encapsula dentro del volúmen del material y, como resultado, la superficie del aislador se mantiene limpia. Sin embargo, este proceso sugiere que existe un punto de saturación donde no se pueden encapsular contaminantes adicionales. Este punto marca el fin de su vida útil efectiva y, entonces, se debe retirar el material. De lo contrario,existe un riesgo de un desempeño incluso peor en condiciones de contaminación que con un aislador con grasa. Por ejemplo, en Creta, se ha demostrado que la vida útil promedio de los revestimientos de grasa de silicona es de solo unos 6 meses y que se deben aplicar y luego retirar dos veces por año. Esto tienen una aplicación limitada principalmente al equipo crítico.
Una superficie repelente al agua también es la característica principal de los revestimientos de silicona RTV. Sin embargo, a diferencia de las grasas, no tienen la característica de encapsulación, sino que más bien tienen una capacidad de transferencia de hidrofobicidad que es suficiente para cambiar el comportamiento hidrofílico inicial de la capa de contaminación depositada por uno hidrofóbico. Como resultado, aunque se mantengan los contaminantes depositados (es decir, sin encapsulación), la superficie sigue siendo hidrofóbica. Esto ofrece una mejora considerable en comparasión con la grasa ya que la contaminación acumulada aún está expuesta a varios mecánismos de limpieza, como por ejemplo, a la lluvia y no se alcanza ningún nivel de saturación. Además, la vida útil puede exceder los 5 años y, en algunos casos, más de 10 años. Por lo tanto, los revestimientos RTV se deberían considerar una contramedida eficiente para la contaminación en la mayor parte de las subestaciones. Estos se pueden aplicar en un momento conveniente para la empresa de servicios básicos en cualquier aislador, sin importar el material, el tipo de equipo ni la geometría de la pollera. En el caso de Creta, el costo total de la aplicación de todos los revestimientos de RTV en uso al 2010 fue menos que el costo correspondiente al lavado de la subestación más problemática en un periodo de solo tres años.
Por supuesto que existen posibles desventajas que también se deben considerar. Estas incluyen el envejecimiento, el mantenimiento y el encontrar el momento óptimo para realizar el cambio, además del costo correspondiente (mano de obra y materiales). Aún así, sus características preventivas y la posibilidad de una aplicación a gran escala, son ventajas considerables que distinguen esta alternativa de manetenimiento de otras. Desafortunadamente, los revestimientos no pueden contrapesar completamente la falta de una distancia de fuga apropiada en los aisladores que se han dimensionado de manera inapropiada dado el ambiente de contaminación.
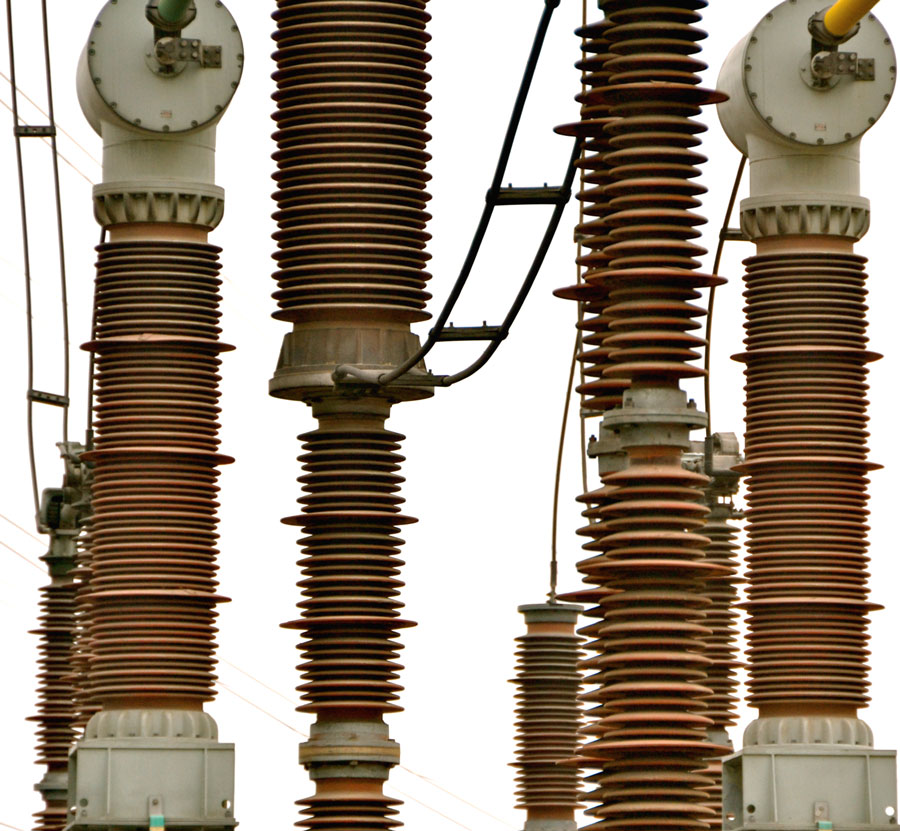
Si la distancia de fuga específica no es suficiente, podría ser obligatorio el uso de extensores elastoméricos de la distancia de fuga. Al igual que con los revestimientos de RTV, los extensores se puede aplicar en cualquier tipo de aislador, pero deben estar especificamente diseñados para la geometría de la unidad: algo que limita la aplicación a gran escala y también aumenta los costos de aplicación. Por lo tanto, es un método que usualmente se adopta para las condiciones severas o cuando los métodos mencionados anteriormente son insuficientes si se utilizan solos.
Aplicación de los Revestimientos de RTV en las Subestaciones en Creta
La primera aplicación de revestimientos de RTV en Creta comenzó en 1998 en la subestación elevadora de 150 kV de Linoperamata, que quedo completamente revestida unos pocos años después. Otras de las subestaciones de la isla se han revestido desde entonces y miles de kg de revestimientos ya están en servicio en las subestaciones de 66 kV y 150 kV en las islas de Creta y Rodes. Desde la aplicación inicial, la actividad superficial provocada por la contaminación se ha visto sustancialmente suprimida y no han ocurrido arcos eléctricos, incluso aunque se suspendió todo lavado en los aisladores revestidos. Por lo tanto, en cualquier caso, la aplicación se puede considerar un éxito. Sin embargo, con los revestimientos que exceden una vida útil de 5 años y, a menudo, cercana a 10, ha habido ciertas preocupaciones sobre cómo evaluar la confiabilidad continua del material y luego decidir cualquier acción de mantenimiento. En condiciones normales de servicio, la evaluación de los revestimientos se hizo principalmente con observaciones empíricas como las descargas superficiales, el ruido y los efectos visuales de la corona durante la noche. También se realizaron mediciones de la corriente de fuga y estas verificaron la mejora alcanzada al aplicar los revestimientos.

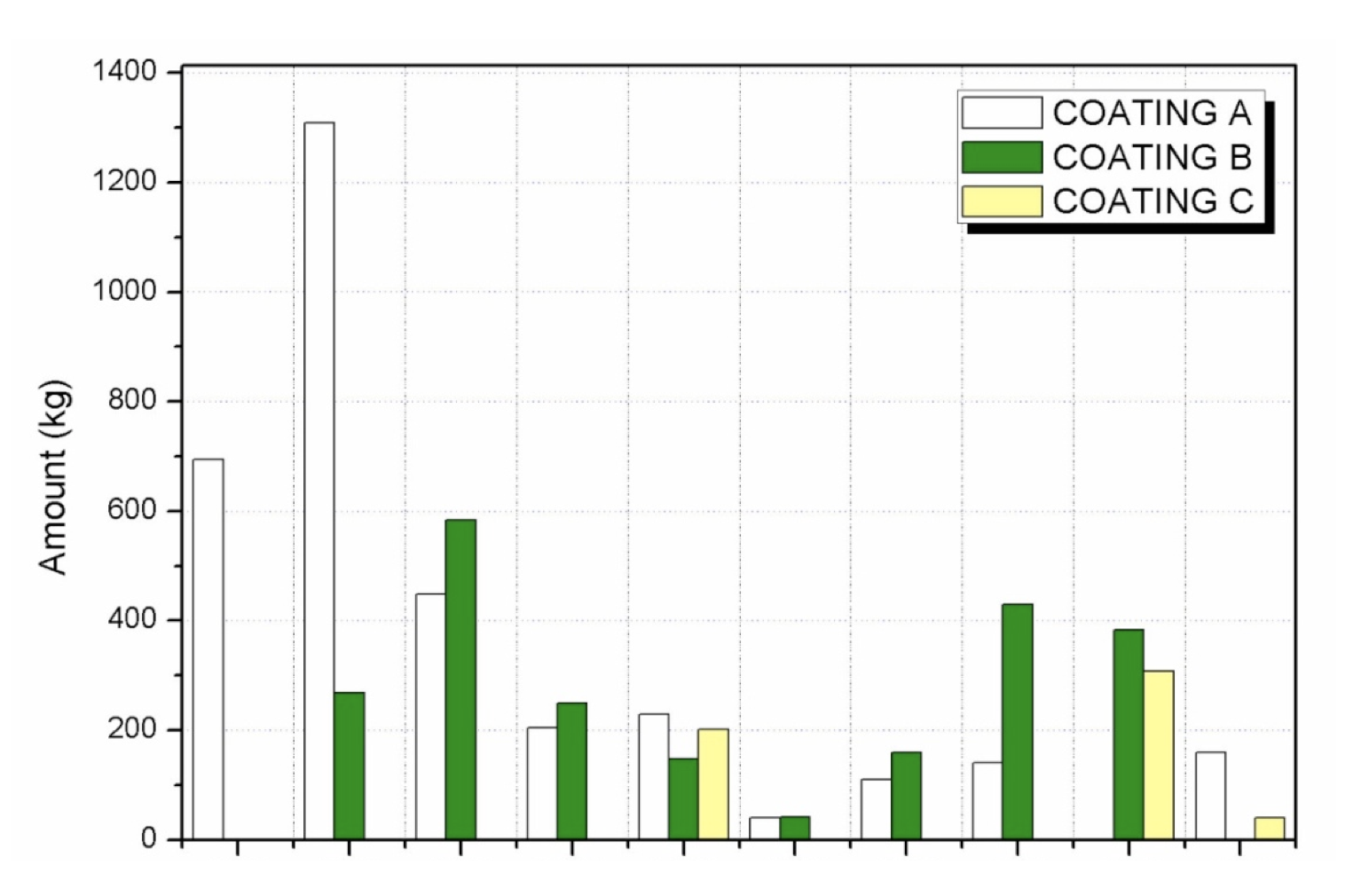
En los gráficos de la Figura n.° 9 se puede ver una comparación. En el primero, se ilustra la distribución mensual de la carga acumulada registrada en la superficie de los aisladores tipo poste de porcelana de 150 kV monitoreados (es decir, comportamiento promedio). Es evidente que ocurre actividad superficial, como se esperaba, principalmente durante los meses secos del verano y de manera más especial desde agosto a octubre. En el segundo, se muestra la misma distribución, pero esta vez para los aisladores revestidos con RTV que tienen la misma geometría, durante el mismo periodo e instalados en el mismo lugar. Por lo tanto, los valores de la carga acumulada (eje vertical) son indicadores de la mejora lograda.

Cabe destacar que el periodo de actividad es distinto en cada caso. Aunque el problema principal de contaminación se experimenta durante el verano, para los revestimientos de RTV la actividad superficial aumento principalmente durante los meses de invierno, en especial desde noviembre a marzo. Este fenómeno se ha relacionado con la influencia del mecanismo de humedecimiento, que es diferente para las dos estaciones. Durante el verano, el mecanismo de humedecimiento principal es la condensación, mientras que en el invierno es la lluvia. La Figura n.° 10 ilustra un ejemplo típico de la influencia de estos mecanismos de humedecimiento alternativos en las dos superficies de aisladores diferentes. En el caso de la condensación, se observa actividad superficial solo en el aislador de porcelana. Por otra parte, durante los periodos de lluvia, se ve actividad en ambos tipos de aisladores. Para el primer incidente, la actividad en el aislador revestido fue considerablemente menor que en la porcelana. Pero en el caso del segundo incidente de lluvia, se observaron los mismos niveles de actividad. Finalmente, en el tercer incidente, no se presentó actividad.
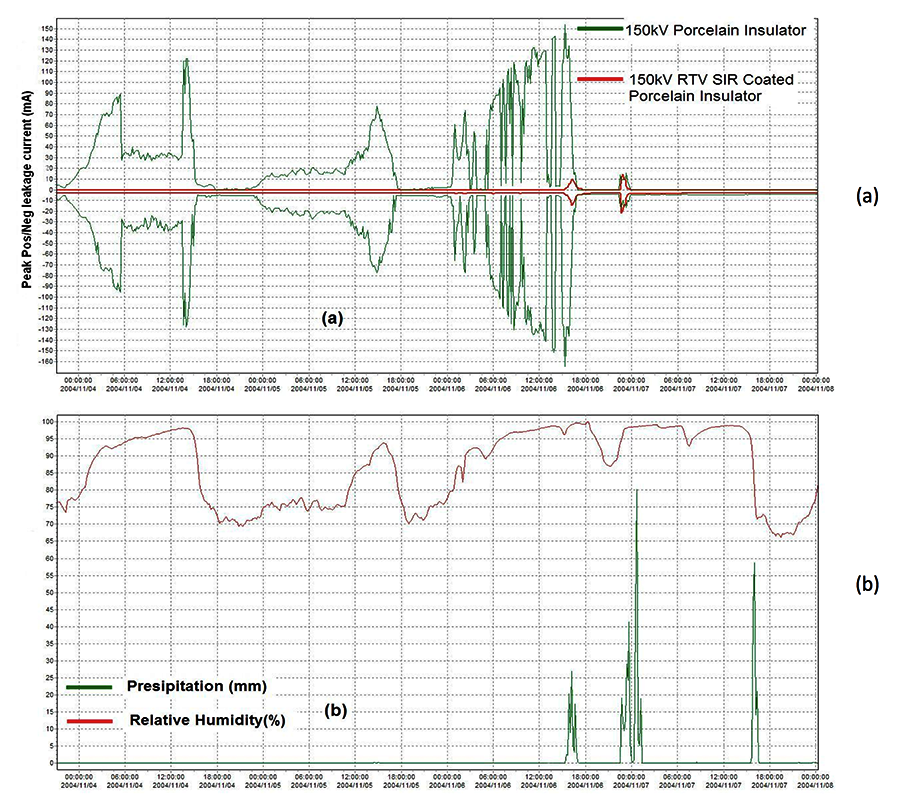
A pesar de que el monitoreo de la corriente de fuga es una herramienta valiosa para entender a cabalidad el comportamiento de los revestimientos de RTV en esas condiciones de servicio, por si solo no es suficiente para respaldar la evaluación completa de la condición del revestimiento. Se verificó la mejora del rendimiento, pero estas mediciones no fueron capaces de detectar el impacto total de algún fenómeno de envejecimiento.
Por lo general, la aplicación de esta metodología se limita solo a un número pequeño de aisladores debido a los costos. Es más, a menudo no es posible monitorear el rango completo de corrientes con la exactitud requerida. En este caso, por ejemplo, las corrientes menores a 1 mA no se pudieron registrar y esta fue una de las razones por las que no había datos confiables para comprar los revestimientos ofrecidos por distintos fabricantes. Finalmente, la propiedad de mayor interés en este caso es la hidrofobicidad de la superficie y su mecanismo de recuperación correspondiente. Ambos se correlacionan estrechamente con las propiedades del material y solo se pueden evaluar en una escala macroscópica al mirar solo la corriente de fuga.
Para mejorar la información disponible sobre la condición de los distintos revestimientos instalados en Creta, se realizaron mediciones de hidrofobicidad según la Guía STRI. Estos hallazgos demostraron que, incluso para los revestimientos más antiguos, aún se podía observar un comportamiento superficial hidrofóbico. Sin embargo, estos tipos de mediciones solo evalúan la condición superficial existente del aislador revestido y no ofrecen ninguna información con respecto a la pérdida y la recuperación de la hidrofobicidad (es decir, la estabilidad de esta propiedad clave). Además, es principalmente un método subjetivo y a veces las mediciones sucesivas puede que no coincidan.
Según la mayor parte de las mediciones, la aplicación de los revestimientos de RTV en Creta resultó exitosa, especialmente dado que el periodo de retorno de la inversión correspondiente fue menor a tres años. Sin embargo, desde entonces se ha entrado a una era diferente, ya que ha surgido la preocupación de cuál es la mejor manera para evaluar la vida útil residual de los revestimientos y decidir cuáles son las necesidades futuras de mantenimiento.
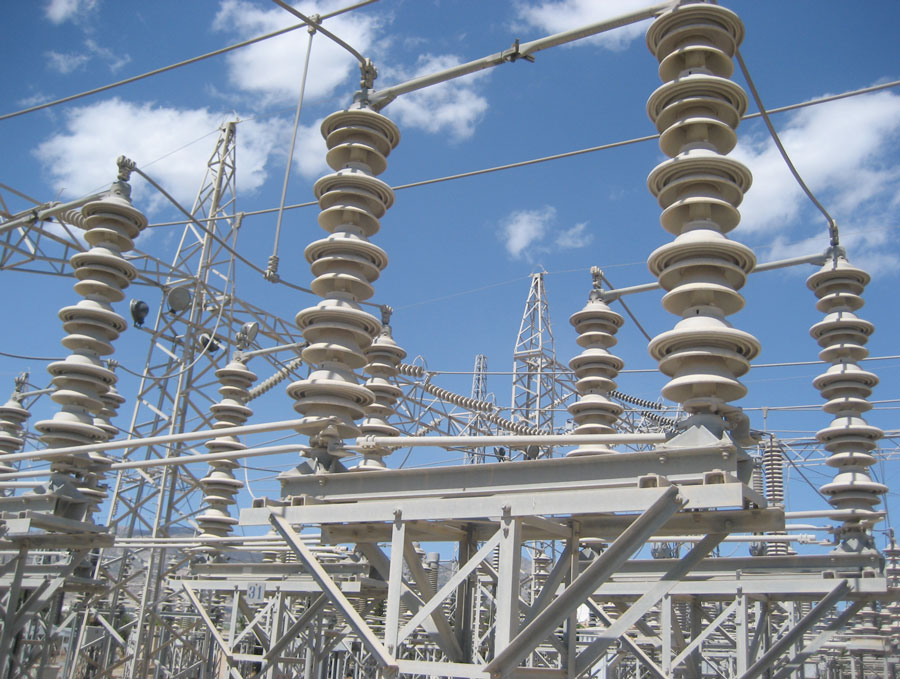
Preocupaciones con respecto a la Aplicación de Revestimientos de RTV
La primera preocupación para estos tipos de revestimientos es la selección del material. Ya que existe un número creciente de distintos fabricantes en el mundo, desde el punto de vista del usuario existe una necesidad de normas con métodos relacionados y criterios bien definidos para evaluar la calidad de cualquier revestimiento RTV en condiciones de laboratorio, antes de la aplicación. Luego, después de la aplicación, la metodología requerida para monitorear la condición y el desempeño de estos revestimientos se convierte en el tema principal. A pesar de que se pueden hacer las mediciones de corriente de fuga e hidrofobicidad, la experiencia que se gana con la aplicación de estos métodos en Creta ha sugerido que no son suficientes para entregar una imagen completa.
Es evidente que también se requiere algún análisis del material y surge la pregunta de qué parámetros se deben evaluar y qué técnicas se deberían emplear. Luego, si estos métodos detectan algún envejecimiento, el siguiente tema pasa a ser qué acciones correctivas se requieren para proteger los revestimientos y prolongar su vida útil. Probablemente, en algunos casos se podría limpiar el aislador con lavado a alta presión (como se muestra en la Figura n.° 8). En otros, puede que sea necesario volver a aplicar el revestimiento. Sin embargo, puede que no sea lo suficientemente claro cuál se debería emplear y cuándo se logra una mejora en el rendimiento del revestimiento sin riesgo de un mayor deterioro.
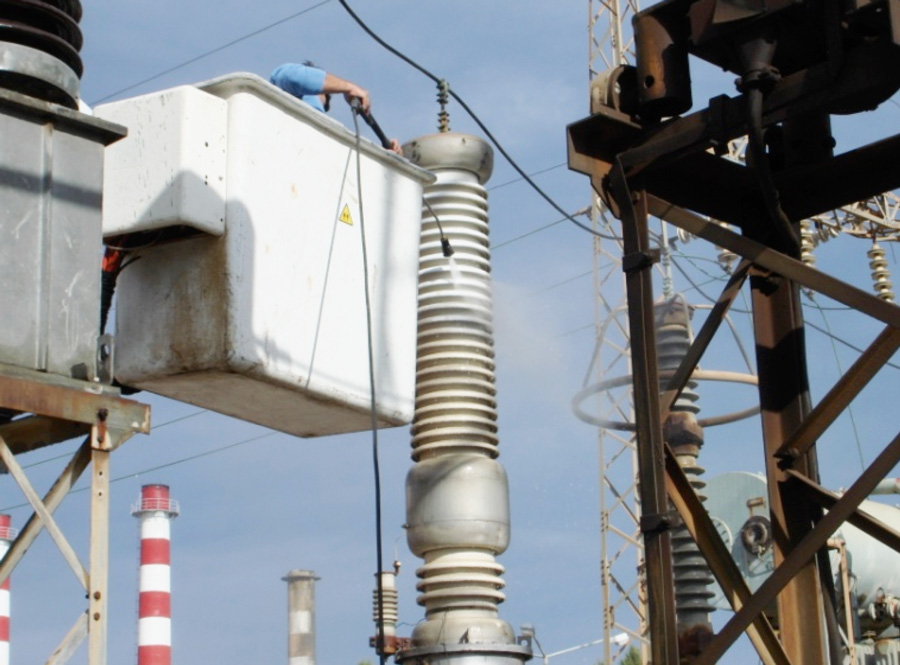
Finalmente, es necesario establecer criterios bien definidos sobre el fin de la vida útil para que los usuarios puedan seleccionar el tiempo óptimo para realizar un cambio o volver a revestir. En este caso, se hace importante desarrollar métodos estandarizados para retirar la capa anterior de revestimiento, si además se considera que lo más probable es que si se vuelve a revesitr, esto sea una solución temporal. En otras palabras, se debe establecer una estrategia de monitoreo y mantenimiento completa desde el momento en que se selecciona y aplica el revestimiento. Solo de esta manera será posible evaluar a cabalidad la condición del revestimiento y determinar cuándo es el momento correcto para realizar más acciones correctivas.
Conclusiones
El mantenimiento anticontaminación de los aisladores en las subestaciones de voltaje alto es un tema que deben enfrentar, virtualmente, todas las empresas de servicios básicos en el mundo. El principal factor que distingue la situación para las subestaciones de las líneas de transmisión son las condiciones de servicio relativamente homogéneas en cada estación y el alto costo correspondiente del equipo que se quiere proteger.
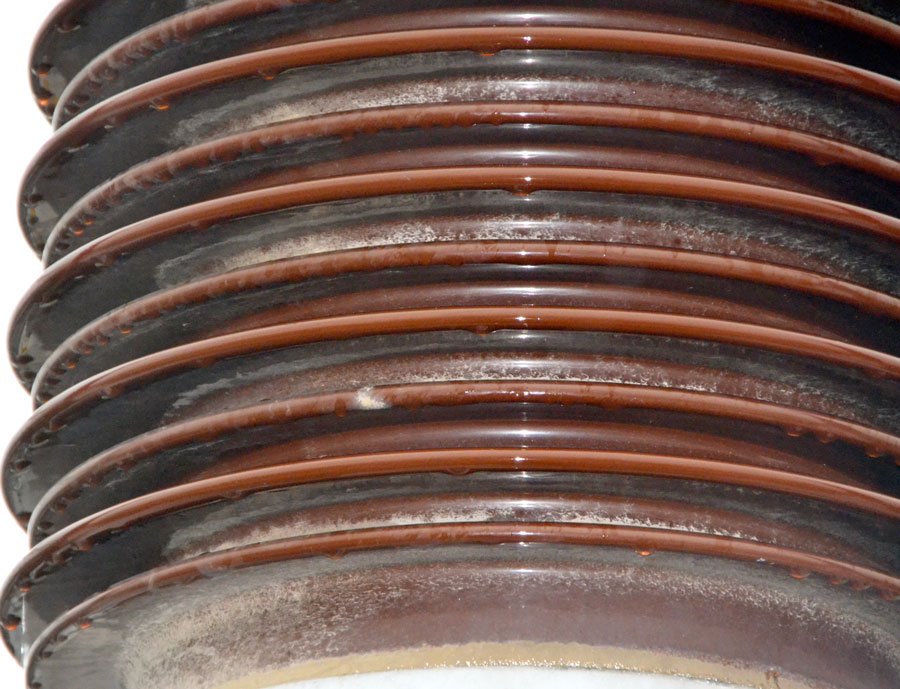
En el caso de los equipos ya instalados, debe haber disponibles medidas correctivas para mejorar el rendimiento en condiciones de contaminación de la aislación existente, ya que el costo del cambio puede ser considerable. Hay disponible varios métodos, pero los revestimientos de RTV parecen ser los más prometedores, ya que entregan una solución protectora con una vida útil larga. En Creta, la aplicación a gran escala de estos revestimientos ha permitido mejorar el desempeño de la aislación, como se puede verificar con las mediciones de la corriente de fuga y por el hecho de que no es necesario aplicar acciones correctivas adicionales. No obstante, aún existen preocupaciones que se deben abordar cuando se trata de la selección de revestimientos de distintos proveedores, el monitoreo y mantenimiento que puede que necesiten y finalmente, el momento y método óptimos para el cambio.