A late December snowstorm in northern Japan 16 years ago led to one of the country’s worst outages, impacting 650,000 households over a duration of as long as 31 hours. For a country with one of the highest reliability levels this was extraordinary. The massive blackout was induced by wet snow mixed with sea salt that packed the sheds of porcelain long rod insulators on 66 kV and 154 kV lines. Conductor galloping along 275 kV lines contributed to the problem.
The wet snow accreted on insulators and filled the gaps between sheds due to strong winds. Because the snow contained sea salt, insulation strength of strings deteriorated rapidly and led to many flashovers, but in a different manner from the better-known phenomena of ice accretion or snow cover on insulators. While ice accretion and snow accumulation on insulators had already been carefully researched, knowledge on impact of wet snow containing sea salt contamination was then limited. Research needed to clarify failure mechanisms and establish suitable countermeasures. This edited past contribution to INMR by Manabu ‘Gaku’ Sakata (then at Tohoku Electric Power) and Hiroya Homma of Japan’s Central Research Institute of Electrical Power Industry discussed properties of wet snow accretion on insulator strings based on the results of artificial wet snow tests.
Sixteen years ago, a powerful low-pressure system from the Pacific moved south to north along the east coast of Japan’s main island while another similar system in the Sea of Japan crossed the island. Ambient temperatures in the Niigata Kaetsu area stabilized in the range of 0 to 2°C with heavy precipitation and wind. Total precipitation and maximum 10 min. average wind velocity were 26 mm and 14 m/sec respectively. Maximum wind speed was over 25 m/sec. Cascading electrical failures on 66 kV and 154 kV lines started just before 09:00 and resulted in numerous tripped lines. At the same time, some 275 kV transmission lines also began to trip out due to conductor galloping. Eventually, 30 transmission lines and 49 circuits were affected.
Maintenance workers discovered that many of the porcelain long rod insulators on affected 66 kV and 154 kV lines were packed with wet snow. Figs.1a and b show examples of this on insulator strings as well as on a gap-type arrester. Shape of packed snow on insulators in some cases was cylindrical and in other cases eccentric pennant into the wind direction. These shapes of snow on insulator strings were markedly different from those that result from simple ice accretion or snow cover. For example, volume density of the packed snow ranged from 0.54 to 0.94g/cm3 while maximum conductivity was approximately 0.2 mS/cm.
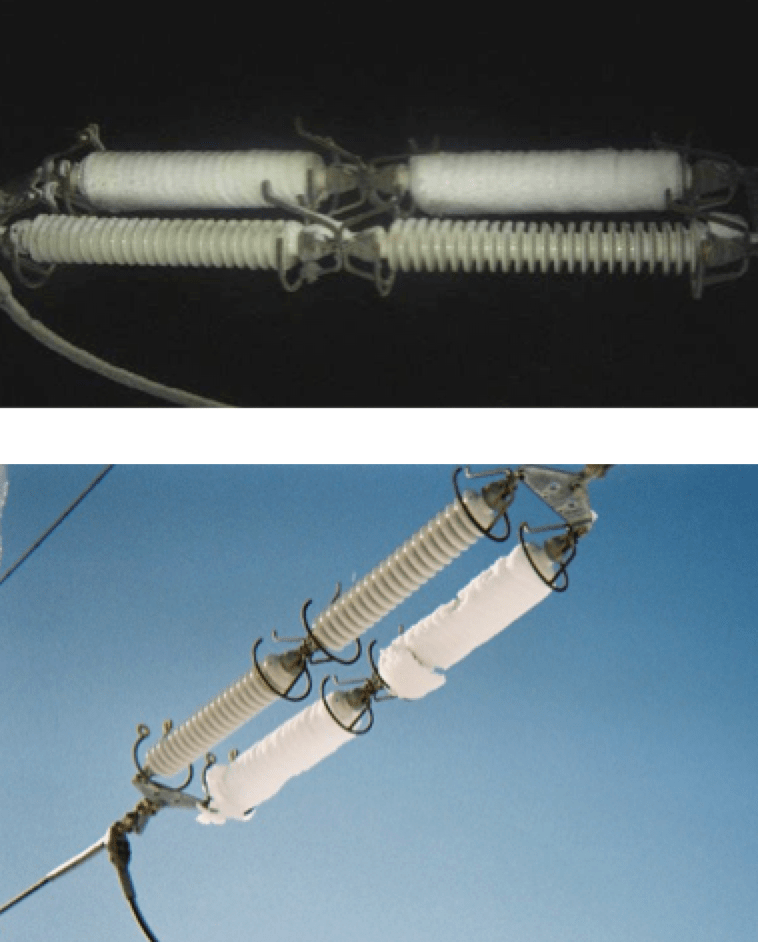
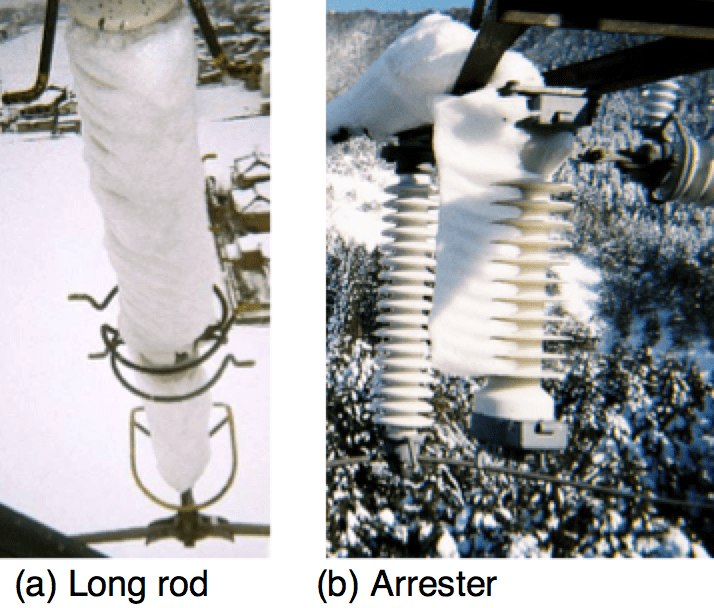
The worst of the weather ended before nightfall and restoration work began at midnight. More than 2500 workers climbed towers and removed the packed snow from insulator surfaces by hand. This proved difficult since the wet snow had by then nearly transformed into ice and it took many hours for the affected electrical system to again be fully operational. During restoration, numerous traces of power arcs on insulator surfaces and hardware were observed on both horizontally and vertically mounted insulators, including V-strings. These were found over a broad area, even as far as 30 to 40 km inland. In fact, measured conductivities of the packed snow were actually highest in this area since sea salt was apparently carried inland by the powerful winds. Tohoku Electric Power Co. completed change-out of the long rod insulators to cap & pin strings of one circuit in the affected area and have since adopted the same countermeasure in other regions where similar events seem possible.
Impact of Wet Snow with Sea Salt
This blackout was induced by heavy, high conductivity snow combined with strong winds – a different climatic event from that which usually deposits ice accretion or snow cover. Similarly, affected lines ran along coastal and inland plains instead of traversing snow-covered mountains. Moreover, electrical failures occurred during the snow accretion process itself whereas failures due to simple ice accretion and snow cover usually take place after sunrise as ambient temperatures begin to increase. It can therefore be concluded that the phenomena behind this event are distinct from the better-known ice accretion or covered snow that occurs on insulator strings. Table 1 summarizes the features of wet snow packed with sea salt compared with simple ice accretion and covered snow.
Since dealing with this type of problem requires an understanding of the basic properties of the process, an artificial wet snow accretion test was carried out to clarify the mechanism of failure caused by wet snow packed with sea salt. The purpose of the test, which took place at a wind generator test station in Niigata, was to evaluate the basic properties of wet snow accretion on insulators having different shed profiles. Since experience with packed wet snow is still limited, the test was performed qualitatively.
Figs. 2a and b show a schematic of the wind generator and test set-up.
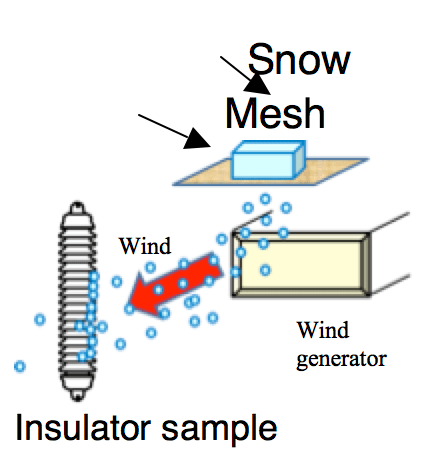
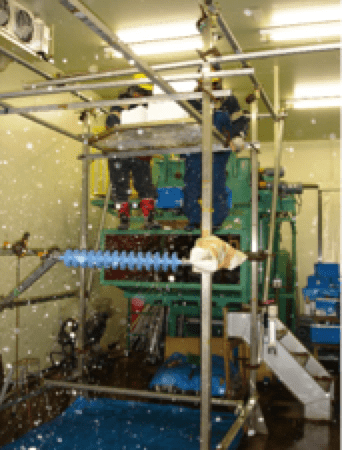
Both dry and wet types of snow were used for the test, with the difference between the two consisting only of its liquid water content. LWC was adjusted by putting natural snow into a test room where ambient temperature was kept around 2°C. While the LWC of natural snow is about 0%, the LWC after adjustment was approximately 5 to 8%. Table 2 shows the types of insulators used. The 66 kV porcelain long rod, cap & pin and polymeric insulators were all tested in both horizontal and vertical configurations and their snow accretion properties studied and compared.
Results
Fig. 3 shows a horizontally mounted long rod porcelain insulator after the test. Although a small number of snow particles were attached to its surface, these never grew into a large-scale accretion. This finding agrees with service experience that indicates outages caused by snow packed with sea salt are induced only by wet snow.
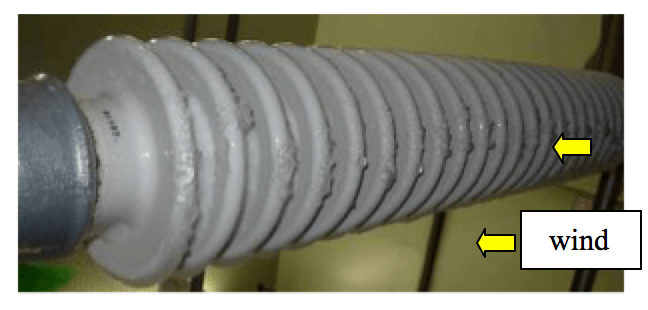
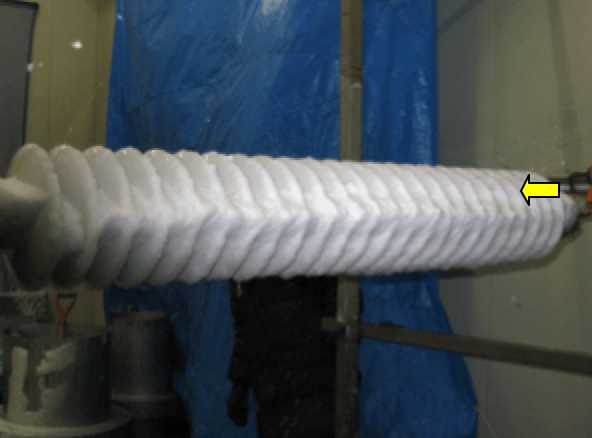
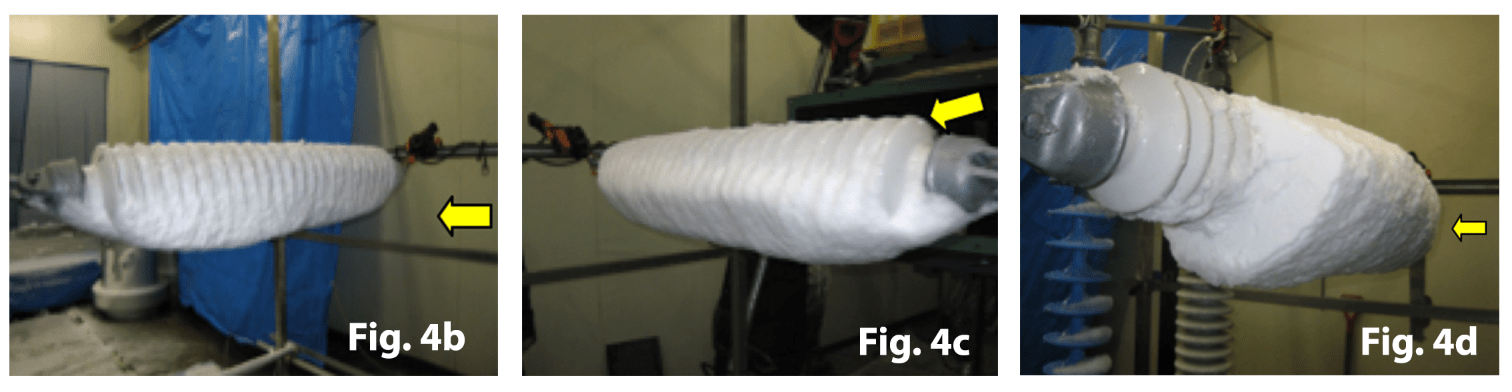
The process of snow accretion on conductors is well known and the result of two different combined mechanisms: one sees the snow accreted onto the conductor surface sliding slowly along the strands from its weight; the other sees the conductor rotate due to the weight of accreted snow. In the case of insulators, the process is basically the same although, since insulator strings are fixed to towers, the latter mechanism does not apply. Fig. 5 depicts the mechanism by which wet snow accretion forms a cylindrical shape.
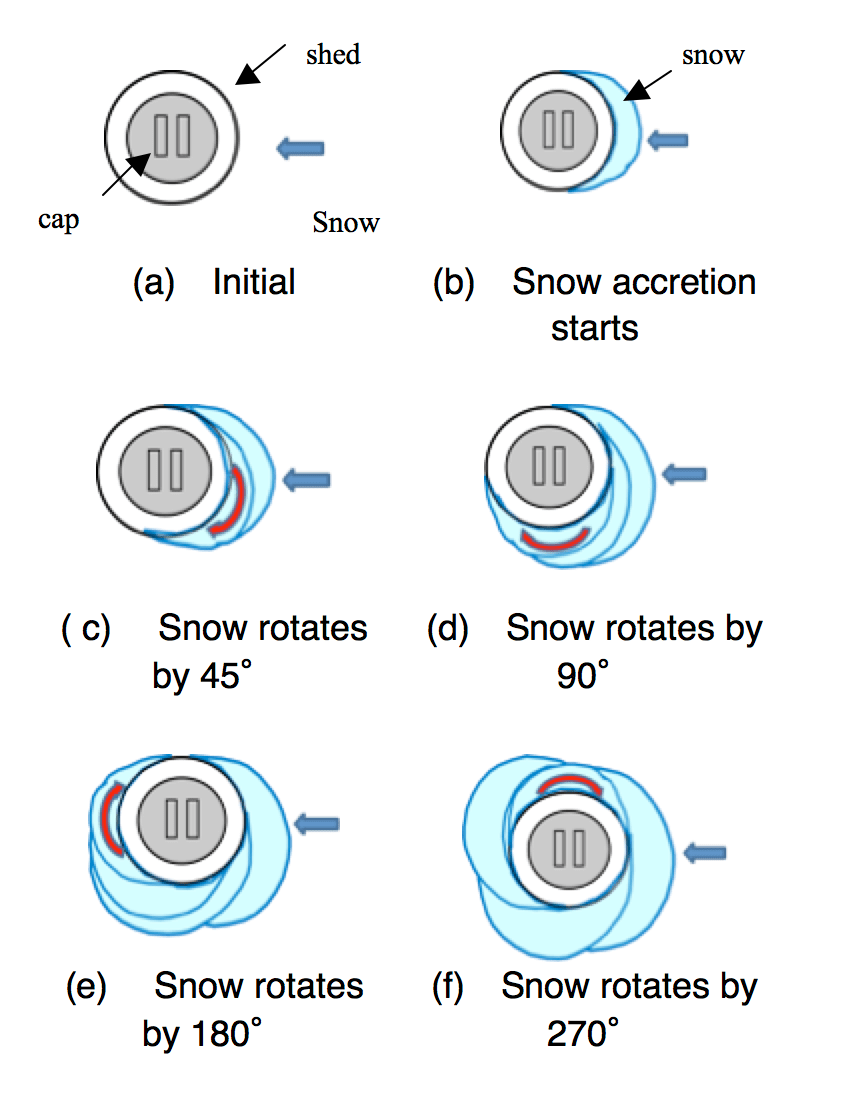

In the case of the wet snowstorm, the cylinder-like shape of packed snow was observed on both horizontally and vertically mounted long rod insulators. The shape of packed snow in this test, however, was developed on only the windward side of the insulator and therefore did not exactly reproduce the shape of packed snow observed in the field. On the other hand, the eccentric pennant shape of packed snow into the wind direction was also found on a polymeric gap type arrester during the Nstorm. The differences in formation conditions and processes between the cylindrical shape and the eccentric pennant into the wind was not clear at the time.
Three points were confirmed during the test:
1. The time for vertically mounted insulators to be bridged between the sheds was shorter than for horizontally mounted ones. In the vertical arrangement, the upper parts of sheds are quickly covered with snow and the sheds are easily bridged. This suggests that I-strings may be more prone to failure than either tension or dead-end strings. At the same time, many traces of power arcs were also found on horizontal insulator strings during the wet snowstorm. In this respect, field experience does not agree with test results and electrical failures may be related not only to wet snow accretion but also to various flashover mechanisms that still need to be clarified.
2. Movement of water to the bottom of packed snow was seen in this case (see Fig. 7a and b) and could be related to the subsequent flashover mechanism.

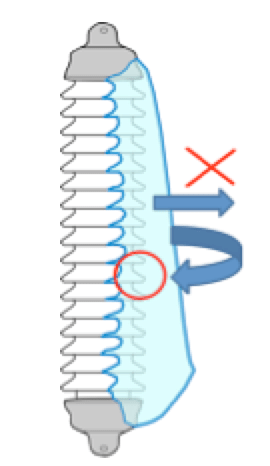
3. Once snow does bridge sheds, the packed snow cannot easily be removed from the insulator surface whereas before bridging the snow tends to be blown away by wind. Nevertheless, snow accretion progresses quite slowly along the insulator’s axial direction and this effect can be explained by the fact that the adhesive tensile strength of snowflakes is greater than their adhesive shear strength. Long rod insulators are not only more easily bridged by snow but the accreted snow is at the same time not easily removed by wind-induced vibrations in the field.
A test with wet snow (LWC 5% and volume density 0.3 g/cm3) was also carried out for a horizontally mounted cap & pin insulator. In this case, the snow accreted on the cap parts first but tended to be easily removed by its weight so that it never grew to bridge the sheds. Figs. 9 a & b show the snow accretion after the test. Since a cap & pin type insulator has a relatively larger shed diameter and spacing, snow accretion cannot easily grow to bridge sheds and tends to be removed by its weight.
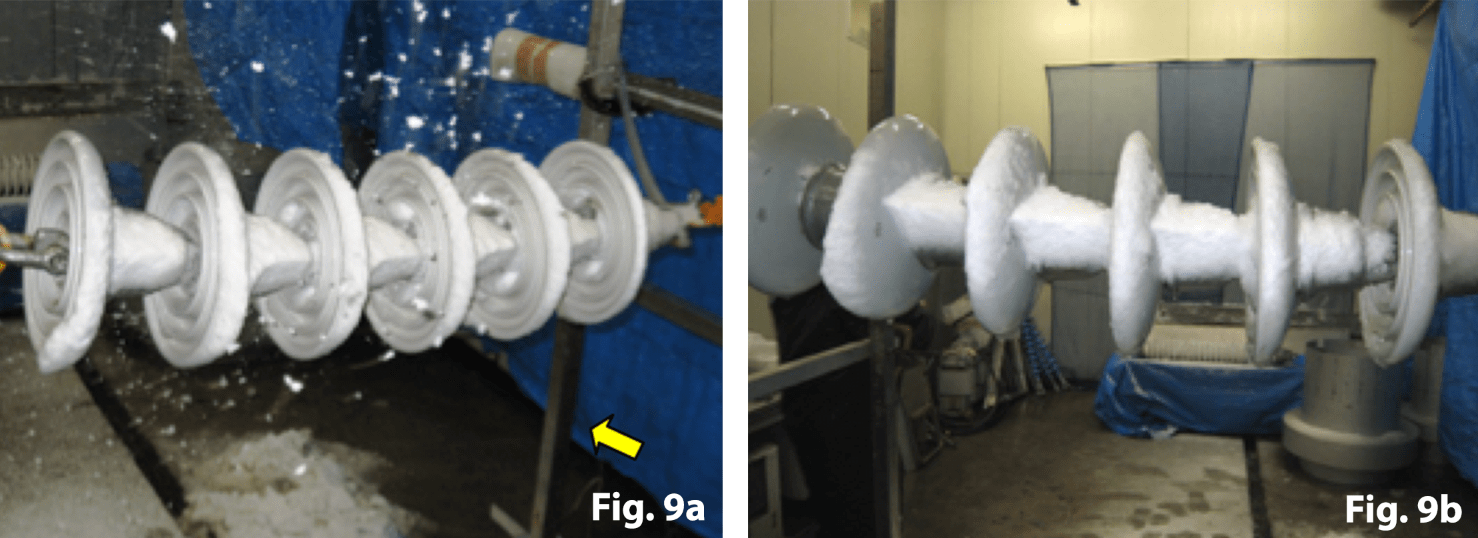
A vertically mounted cap & pin insulator string was also tested (LWC 7% and volume density 0.4 g/cm3). At first, the snow accreted on the upper parts of the sheds and finally bridged the sheds in a packed condition. Fig. 10a shows the snow accretion just before bridging while Fig. 10b shows the comparison between the cap & pin and the porcelain long rod insulator tested at the same time. The time needed to bridge the cap & pin type was about 50 minutes but only about 10 min for the long rod.
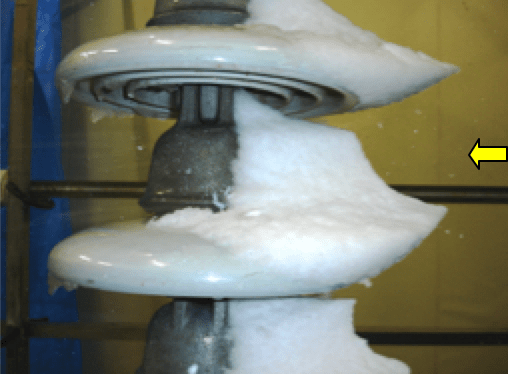
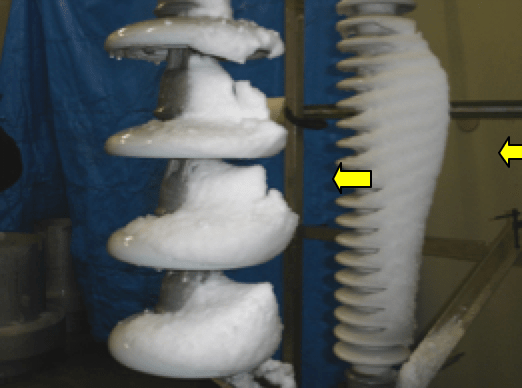
Finally, tests were performed involving wet snow (LWC 7% and volume density 0.3 g/cm3) on a horizontally mounted polymeric insulator over 30 minutes. The snow accreted on the core rod first and then gradually became packed, followed by bridging between the sheds. Figs. 11a & b show the snow accretion after the test. The shape of packed snow was like eccentric pennants into the wind. However, the snow tended to be easily blown off by wind in comparison with the porcelain long rod insulator. This might be the result of a smaller core rod for the polymer in comparison with the long rod insulator – which results in a smaller area of contact between the surface and snow particles. As a result, in the case of polymeric insulators the shape of accreted snow was not cylinder-like but rather eccentric perpendicular into the wind.
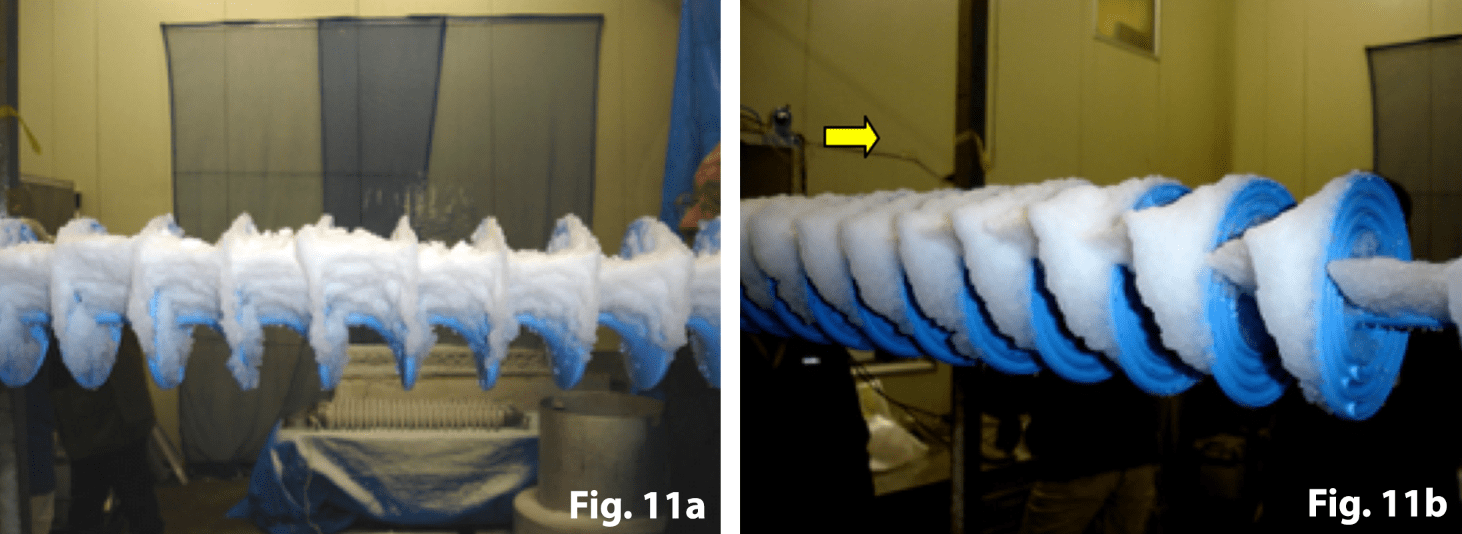
The same test with wet snow (LWC 4% and volume density 0.3g/cm3) was then carried out for a vertically mounted polymeric insulator for 50 min. A porcelain long rod insulator was also set in parallel for comparison. At first, the snow accreted on the upper part of the sheds, (Fig. 12a) and finally bridged and packed between the sheds. The time needed to bridge the polymeric insulator was about 20-30 min. versus about 10 min. for the porcelain long rod. Since shed spacing for the polymeric type is larger than for the porcelain long rod, the time to bridge it is about two to three times longer.
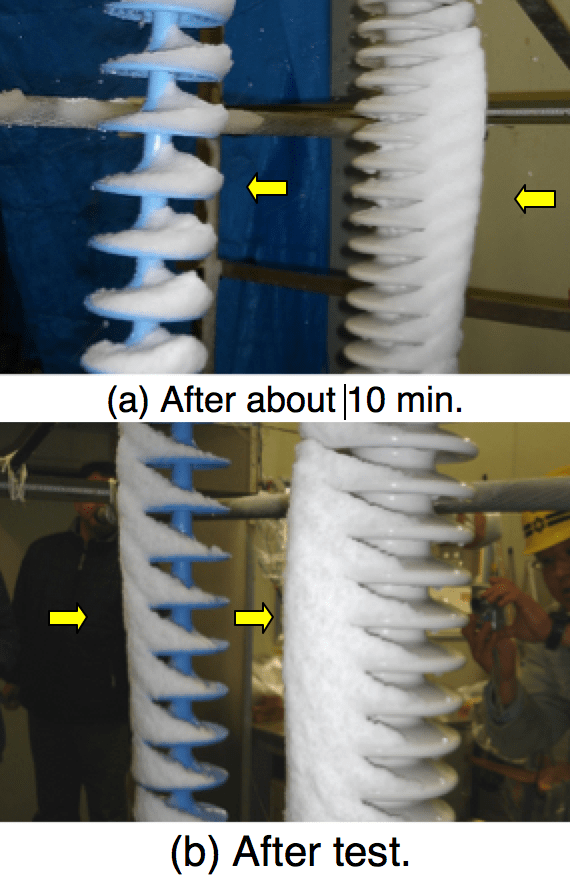
During the test, the polymeric insulator maintained high hydrophobicity (see Fig. 13), but this property seemed to have little effect on snow accretion. In this regard it can be concluded that shed profile appears to be more important than shed material.
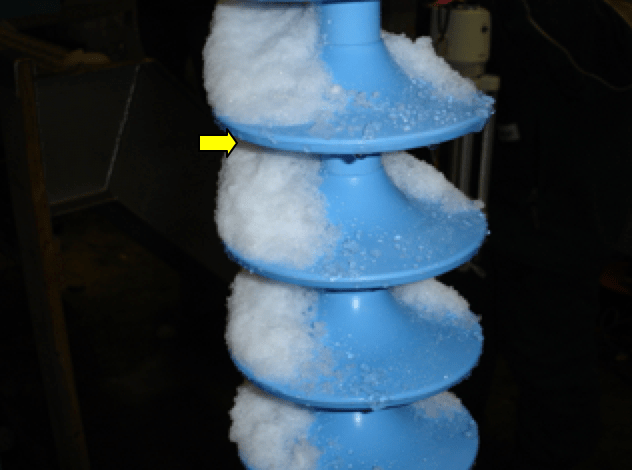
Conclusions
1. Electrical failures of insulators by wet snow packed with sea-salt can be induced by unusual climatic events involving a great deal of wet snow with high conductivity combined with heavy winds. This phenomenon is distinct from the more commonly observed ice accretion or covered snow on insulator strings.
2. In order to clarify the failure mechanisms and establish effective countermeasures, the basic properties of the packed snow need to be better understood. To this end, artificial snow accretion tests have been performed on a qualitative basis as a first step toward future quantitative studies.
3. In these tests, several basic properties of packed wet snow were demonstrated and issues for future research identified, including:
4. The packed snow was reproduced on insulators using wet snow (LWC of 5-8%) whereas no snow accretion was seen using dry snow (LWC of 0%). This corresponds well with service experience that indicates that such outages are caused by packed, wet snow laden with contamination, such as sea salt.
5. The cylinder-like shape of packed snow occurring in Niigata and triggering the widespread blackout of 2005 was reproduced on horizontally mounted long rod insulators and the mechanism of such a snow pack process was demonstrated. This mechanism – whereby snow grows by rotating along the insulator surface to become cylindrical – is basically the same as with snow accretion on conductors.
6. The shape of packed snow on vertically mounted long rod insulators in this test was eccentric pennant into the wind. While this shape shows some similarity with the packed snow on the polymeric arresters in Niigata, the cylinder like shape seen on many long rods was not reproduced. Test methodology or conditions may therefore have to be improved for any future research.
7. Shed profile affects the properties of wet snow accretion. Wider shed diameter and larger shed spacing results in lesser amounts of snow accretion and reduced possibility of bridging sheds. Therefore, cap & pin insulators perform best and polymeric insulators are the next choice. Porcelain long rod insulators are the most vulnerable to packed snow. Bridging of the sheds can more easily occur on vertical than on horizontally mounted long rod insulators. This suggests that V-strings are most vulnerable and I-strings also become vulnerable as they sway due to winds.
8. Hydrophobicity of polymeric insulators seems to play little role in snow accretion. Shed profile is more important than shed material.
9. Once snow bridges the sheds and becomes packed, it cannot easily be removed from the insulator surface. The adhesion tensile strength between the snow particles and between the insulator surface and snow particles is strong.
10. Water inside the packed wet snow tends to move downward and accumulate near the bottom of the insulator, making the LWC at the bottom larger than on other sections or even that of the original snow. Water migration may play a role in this process.