Power system engineers all face a similar dilemma at one time or other when trying to identify which product offers the quality they require – especially in today’s global market with its many competing suppliers. Yet making the right decision can prove vital to reliability and is even more important in the case of a surge arrester, whose function is to prevent costly damage to assets from lightning or switching surges.
How quality is defined depends on the specific type of arrester under consideration. For a distribution arrester, its ability to disconnect from the system if overloaded is critical. This is also high on the list when assessing the quality of a transmission line arrester. By contrast, other factors entirely are relevant when evaluating the quality of a station arrester.
Designing and manufacturing quality arresters requires testing and characterization beyond what is indicated in the standards. In fact, additional checks and tests are often necessary to guarantee the quality of any arrester that is put into service. This edited past contribution to INMR by industry expert Jonathan Woodworth, presented his views on which factors are most important when purchasing surge protective devices.
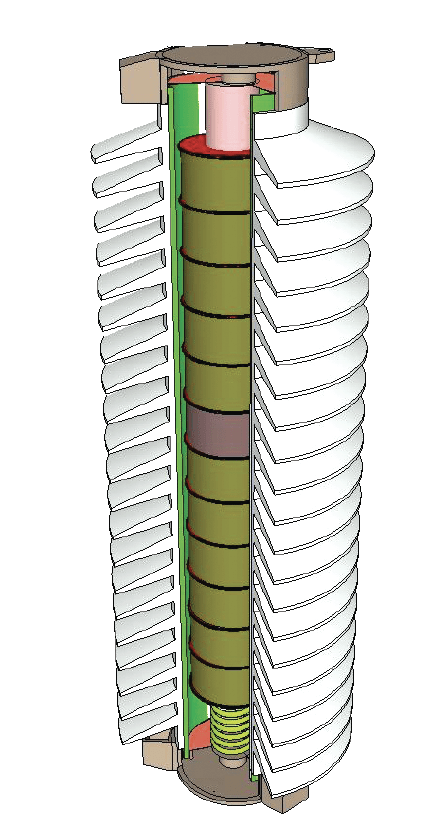
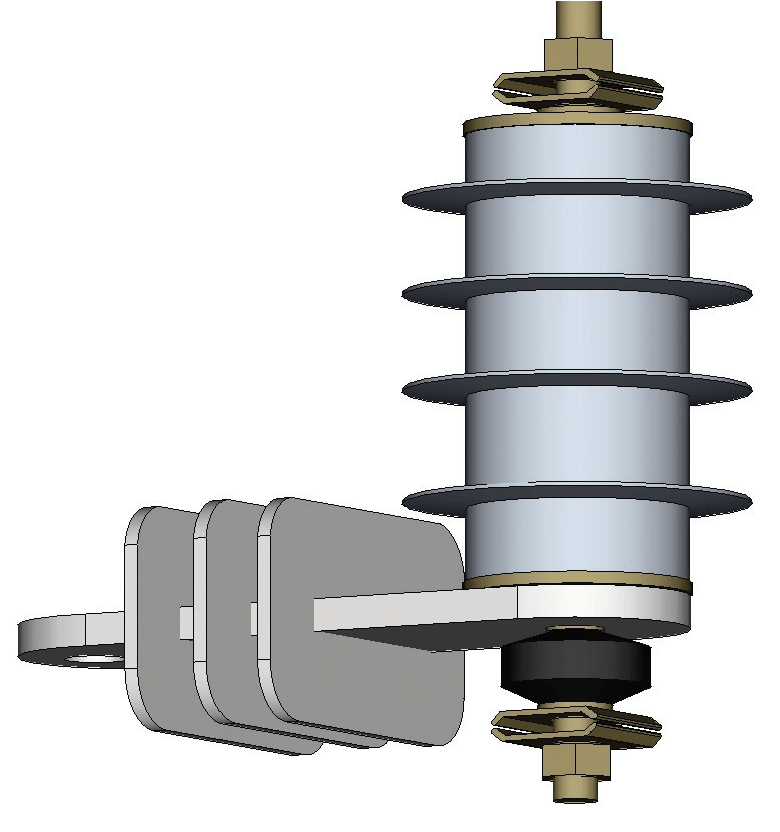
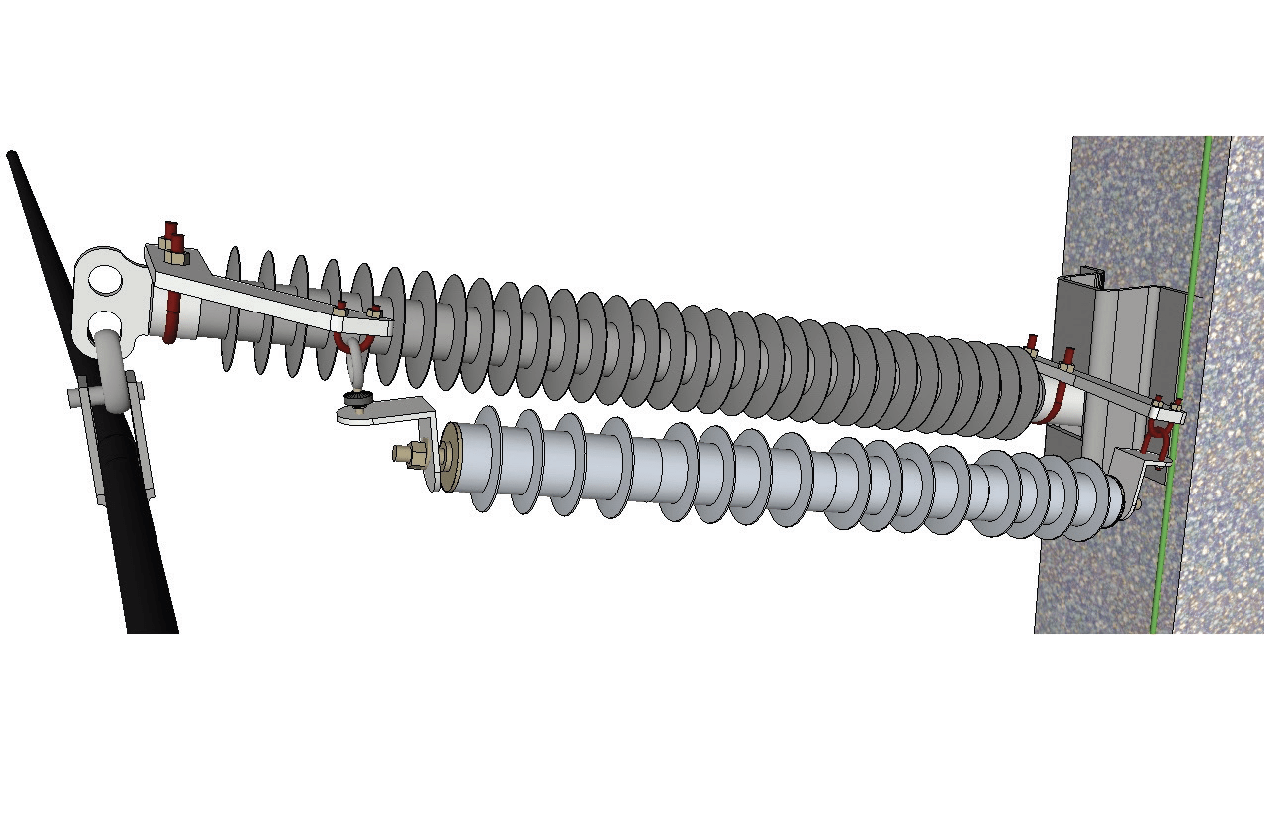
Station class arresters protect the highest value assets at a substation and are part of a grid that serves millions. It is therefore vital they are produced to the highest level of quality possible. The latest design to join this family is the composite hollow core arrester, which combines the benefits of polymer-housed and porcelain-housed designs. The various elements that comprise such a product are shown in Fig. 1 and critical characteristics start with a rubber housing material that can withstand years of stress, no matter the environment.
The distribution type arrester differs from the station arrester in that it is installed only for lightning protection. This small yet key component of a power system protects lines that directly serve end customers. Similarly, the principal function of a transmission line arrester is to protect the HV system from lightning damage. A vital component on both – but not on station class arresters – is the disconnector. If not for the disconnector, an arrester that fails would short out the system and lead to a sustained outage. The disconnector removes the failed unit from the system should it become a short circuit, causing no more than a system ‘blink’.
Common Features of Quality Arresters
Robust Materials with Proven Service Record
A quality housing is perhaps first on the list if an arrester is to function for decades without problem. Different polymeric housing materials are not all equal in performance, so it is vital to select one that has demonstrated good service history, even under severe environmental conditions. Arrester suppliers must be able to provide technical support to demonstrate, through testing and field experience, that the materials they use will perform over the long term.
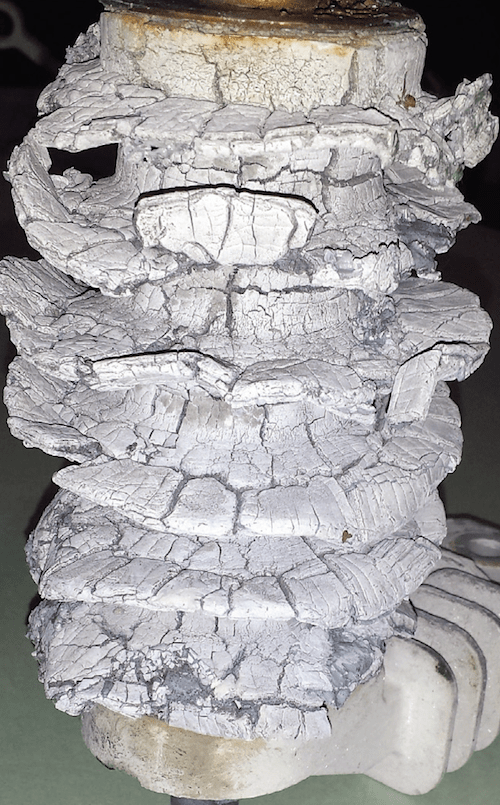
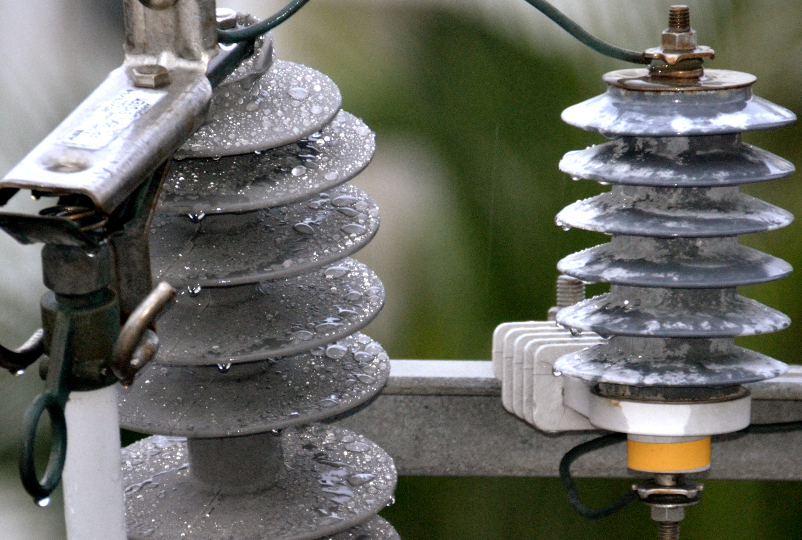
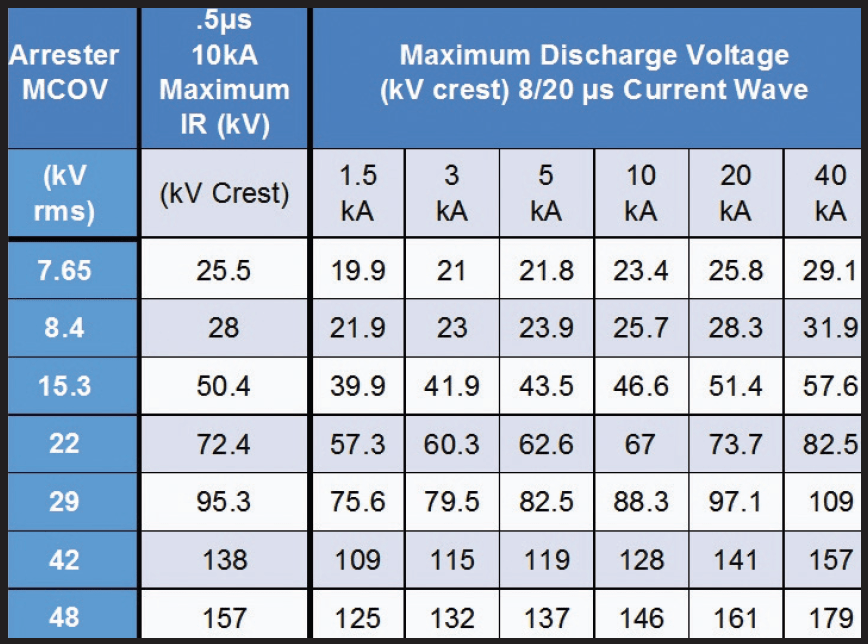
Protection Levels
Effective lightning and switching protection are what is required most when purchasing an arrester. Discharge voltage and sparkover values are measures of this protection and the lower these are, the better. Consideration of this critical parameter should be paramount when selecting an arrester. Additionally, a quality supplier will always have an audit trail to verify all the characteristics published for its arresters.
Failure Mode
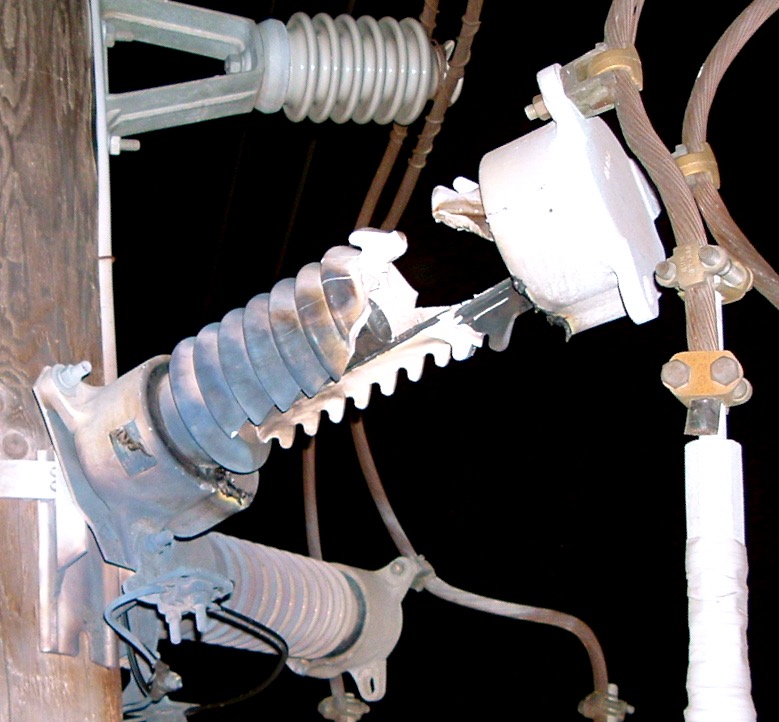
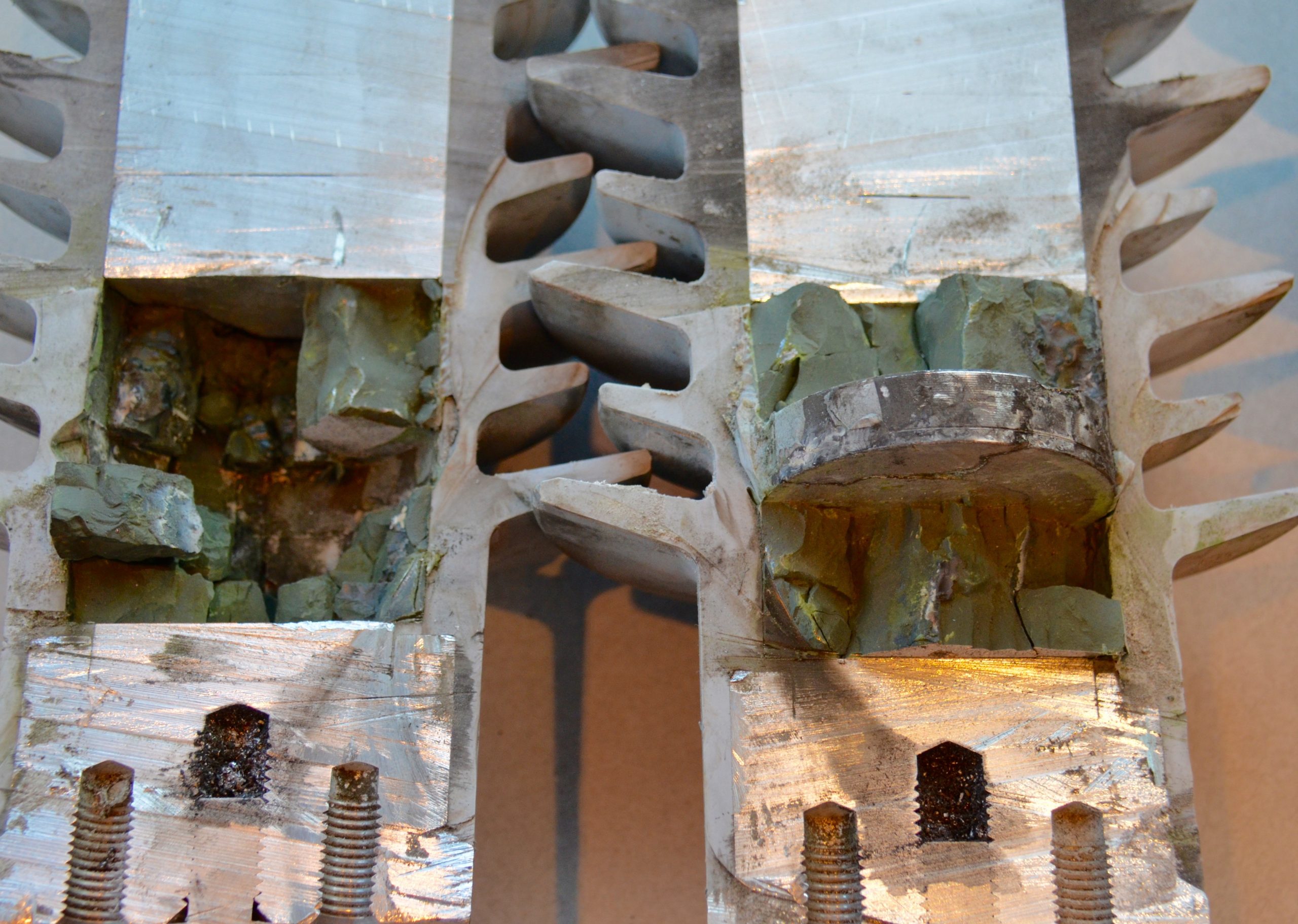
If an arrester is overloaded beyond its design capability and fails, it is important that it does so in a manner that does not jeopardize nearby high value assets. To ensure that the failure mode claimed for an arrester is as published, a certified test report should be made available, ideally from an independent and reputable laboratory. These tests are complex and running them improperly can result in arresters that pass yet are not capable of a safe mode of failure.
Moisture Resistance
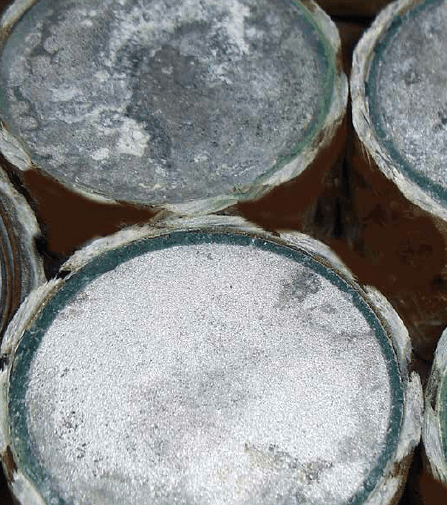
Resistance to moisture ingress is among the most significant features of a quality arrester. Products designed and manufactured without proper testing and verification of this capability will probably not survive long under demanding environmental stresses. A common misconception is that polymer-housed arresters are intrinsically moisture resistant; in fact they are not. The arrester sealing function should therefore be primary in design and also during the manufacturing process. To assure good quality, it is advisable to request proof that the arrester will withstand all expected environmental conditions and also how this has been verified. IEEE standards offer a minimum set of tests that must be passed, but high quality arresters are usually tested beyond normal standards.
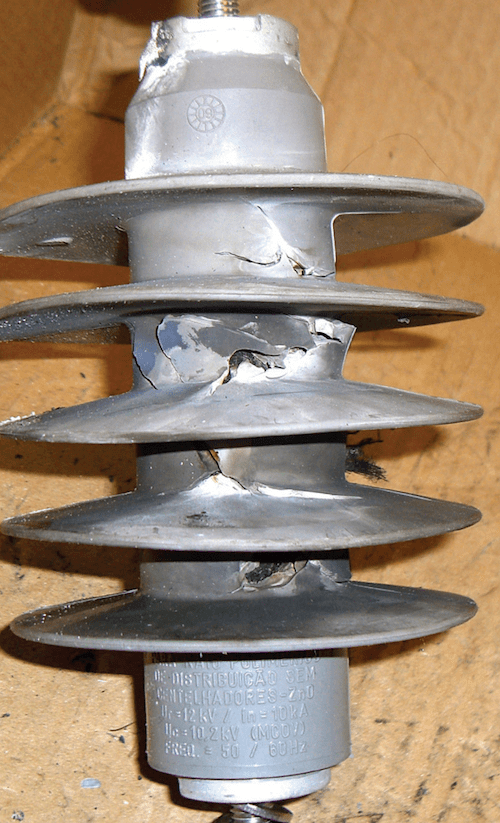
Quality Disks
The MOV disk is the ‘heart’ of an arrester. Without quality disks that perform as specified, an arrester will simply not provide the desired level of system protection.
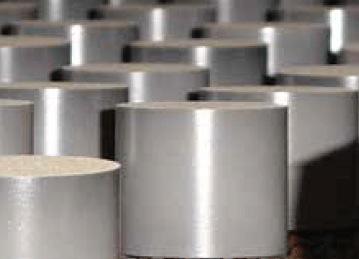
Durable Terminals
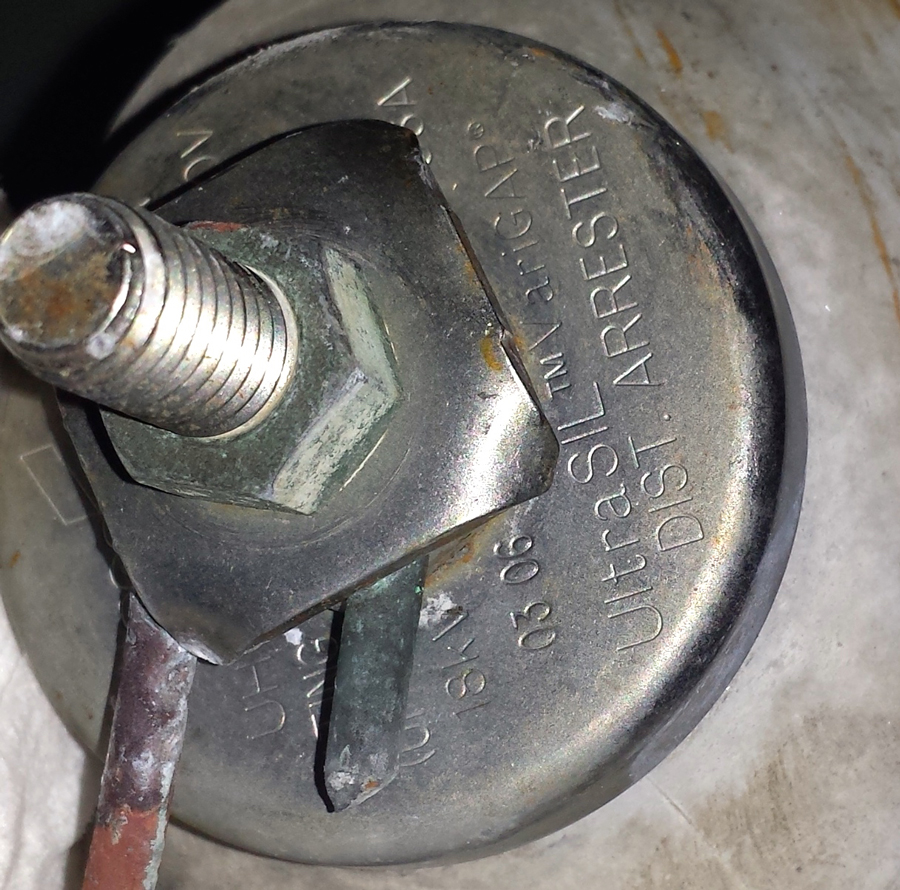
‘Durable’ here means not easily damaged by mishandling during installation. These parts must therefore be made of materials that will last the full service life of the unit and not cause installation problems such as cross threading, partial discharge or breakage. A second aspect of robust terminals is long-term resistance to weathering. Rust that forms on a connector, for example, can eventually wash down the housing and reduce its wet flashover capability.
Dependable Disconnector
The disconnector can be equal in value to the arrester itself if its successful operation helps avoid the cost of a long-term outage.
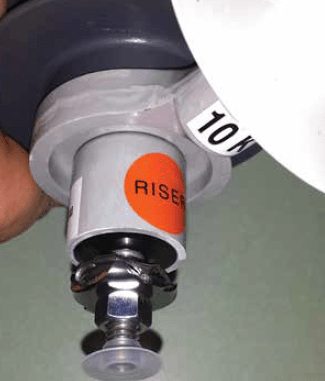
For this reason, it is important to know the service history of the disconnector. Questions to ask in this regard include: how long has the design been in use; what is the principle of operation; how low and how high in current will it operate; and how has performance been verified during production. A quality arrester will also have a disconnector that is approved as non-hazardous for transport by public regulatory agencies. This means that, if involved in a fire, it must not explode and endanger first responders.
Reliable Venting
In the event an arrester becomes overloaded, it is essential that it vent internal gases rapidly and efficiently to avoid complex fracture and potential collateral damage to nearby assets. Polymer and porcelain-housed arresters must both perform flawlessly under such a scenario.
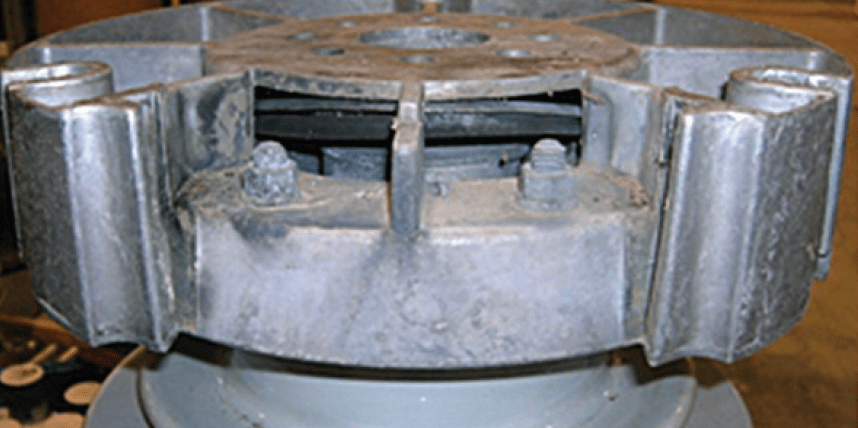
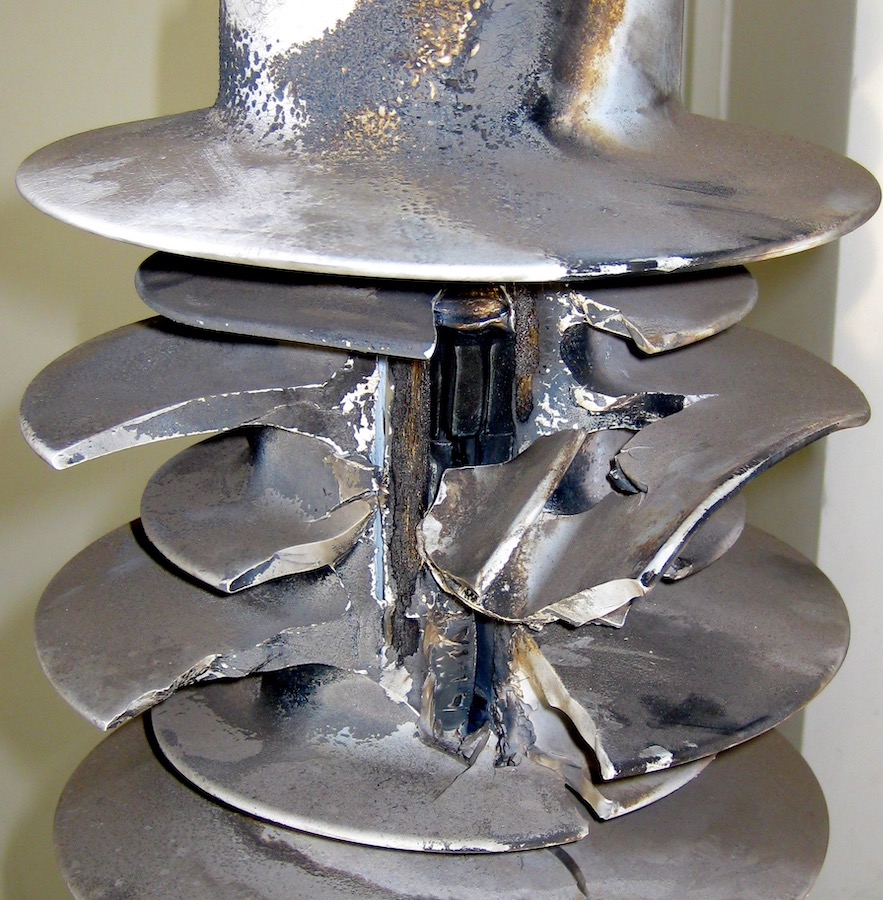
Proven Dielectric Materials
The materials comprising an arrester need good dielectric properties, depending on where they are used. For example, good dielectric is required wherever the material experiences voltage stress during the arrester’s long service life. Dielectric materials with a proven history in high voltage applications should be well known to manufacturers and only these are to be used in a quality arrester design.
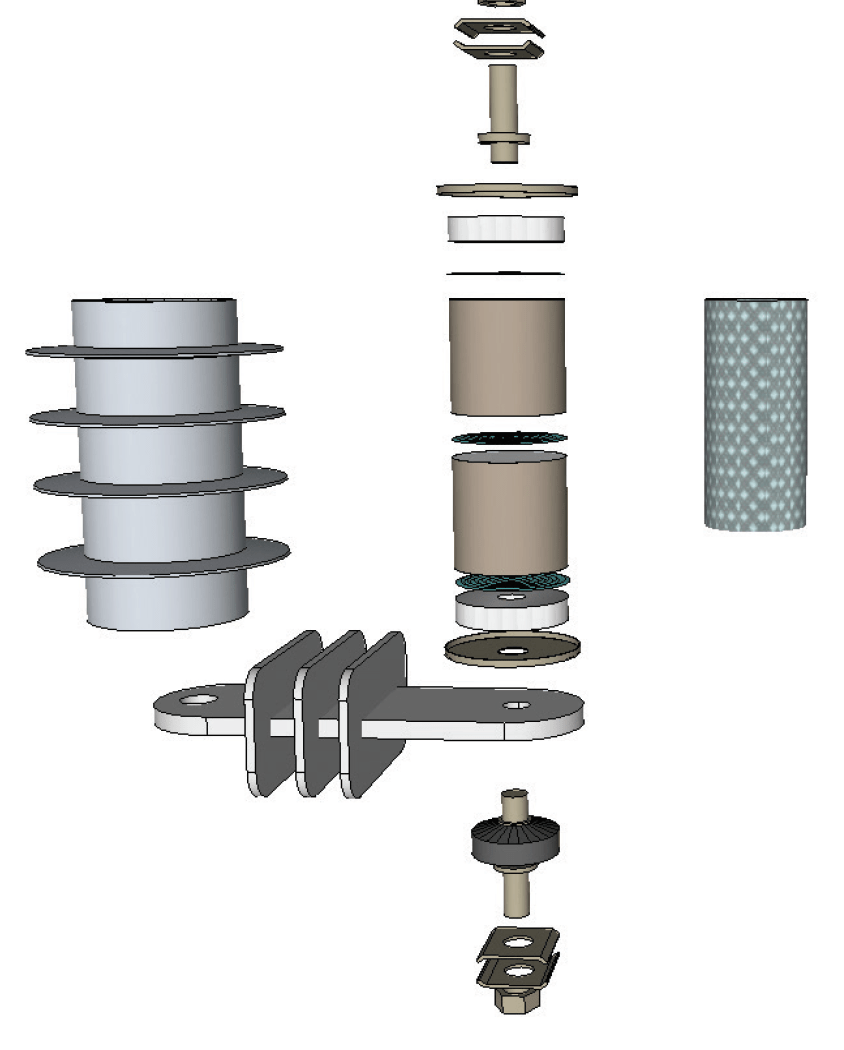
Clear & Complete Certified Test Reports
The quality and design of any arrester can be determined by looking at the certified test report and arrester manufacturers should always have this data available to customers. Reports need to be clear, concise and accurate, with tests that follow IEEE C62.11 or IEC 60099-4. Data presented should be self-explanatory and easily understood.
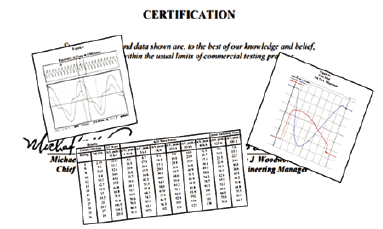
High Power Frequency Withstand Capability
High power frequency withstand (TOV withstand) capability is not necessarily a given in any arrester. In fact, some arresters may offer only poor temporary overvoltage withstand capability and fail during a single line to ground fault. It is advisable to only install arresters with high TOV withstand capabilities, as verified by the TOV curve in either catalogue literature or certified test reports. It is also vital that this characteristic be tested routinely during production.
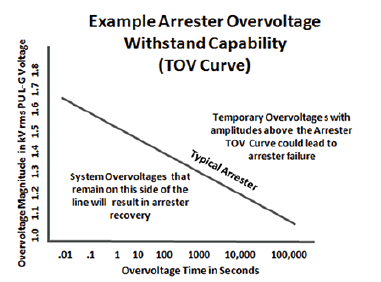
Safety Label
Differently rated distribution arresters can appear similar at first glance and the practice of using a safety label was therefore adopted in the 1990s. Such a label is essential to line personnel installing arresters should a lower rated arrester accidentally be packaged in a carton containing higher rated units. If a 10 kV arrester was packed in an 18 kV carton, for example, its installation could pose a hazard. A large label makes it easier for the installer to see the rating and reduces risk. This is the 3rd arrester label found on quality arresters and should ideally be a mandatory requirement by the user.
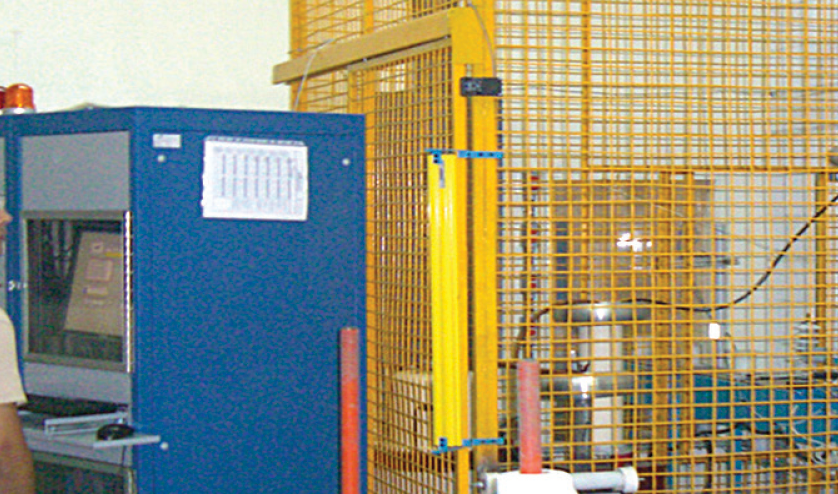
Dependable & Reliable Routine Tests
Routine tests on arresters and their components are critical during production. Discharge voltage, TOV, watts loss, leakage current and partial discharge are all critical parameters that should be monitored to be within manufacturer specifications.
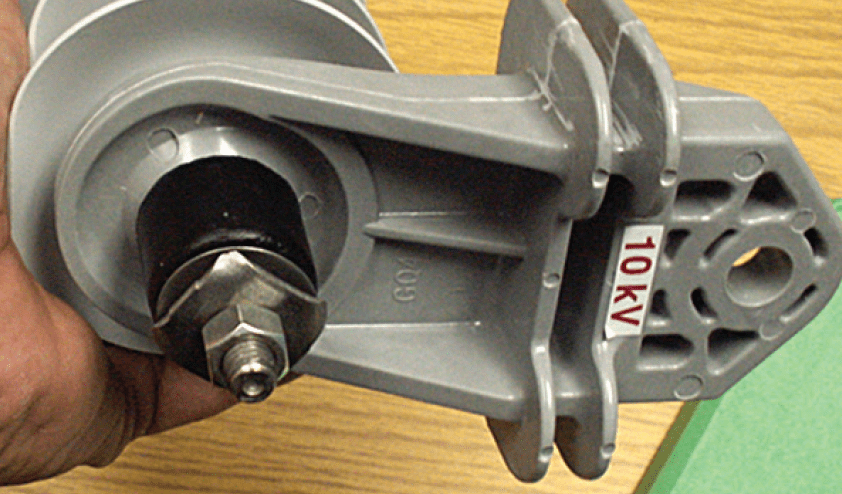
[inline_ad_block]