Many in our industry predict the future will bring greater blending of technology and hybridization. But what does hybridization mean in power systems? And what are its implications for testing? To answer, it is important to recognize that the key enablers of transformational change in electric power systems are digitalization, information technology and power electronics.
Technological and societal developments are accelerating the rate of change in interconnected electricity systems, which make up humanity’s largest technical construct. As a result, experts are unanimous that electricity’s role as ‘the fuel of choice’ will more than double over the next 35 years as it becomes greener, more affordable and more accessible than ever.
Electricity increasingly comes from variable renewables in all scales, from vast solar fields and offshore wind generation to simple rural wind turbines and even solar panels on home roofs. Huge amounts of renewable sources are deployed across the world and we are nearing or already at the tipping point. Today, there is about 40 Watt-peak (Wp) of installed solar photovoltaics (PVs) per person. That is expected to rise to 1000 Wp within 20 years. To accommodate this new way of producing electricity, the grid must become more flexible. It needs to work with and for renewables rather than demanding that renewables adapt to mimic the behaviour of traditional power plants.
Going Underground
Electricity is transported from where it is generated to where it is needed through a network of overhead lines and underground cables. In recent years, interest in high-power underground cables has risen, driven by space limitations, public opinion, availability and reliability. Increased availability and reliability are particularly true for the distribution grid since cable connections can be easily monitored and diagnosed, for example with Smart Cable Guard technology. Most important, underground cables are not as vulnerable to extreme weather events. Despite the high cost, undergrounding power systems has become a trend. There are, however, technical challenges to be addressed when undergrounding large parts of the high voltage transmission network. New qualified types of high transmission capacity power cables will be needed. Reliability of long sections with many joints is also an issue.
Being Direct
Power transmission has undergone significant development through the implementation of HVDC systems that enhance bulk power capability and enable long-distance transmission. This then allows interconnection of regions having different grid frequencies and supports integration of large-scale renewable energy sources. HVDC systems can also improve flexibility and controllability of AC systems, in some cases minimizing overall environmental impact.
Contrary to the view of some experts, the AC power grid will likely not be converted to a DC system. Instead, the power system will gradually hybridize to deliver the best of both. We can already see a trend to embed HVDC systems into transmission grids in Europe, China and, to a lesser extent, the United States. This signals the end of the single frequency system since parts of the grid can and will operate at (slightly) different frequencies. While bringing numerous benefits, a hybridized transmission grid will be more complex to operate and will exhibit different, perhaps unexpected, behaviour.
However, in spite of increased complexity brought by variable renewables, new technology and digitalization, we can guarantee safe, stable and reliable power system operation, at all levels, through a suitable ‘mix of control’. In addition, there are more interfaces and interactions with other infrastructure such as telecommunications, sensor networks for monitoring and prediction and the suite of actuators that range from (slow) transformer tap changers to (fast) grid connected inverters.
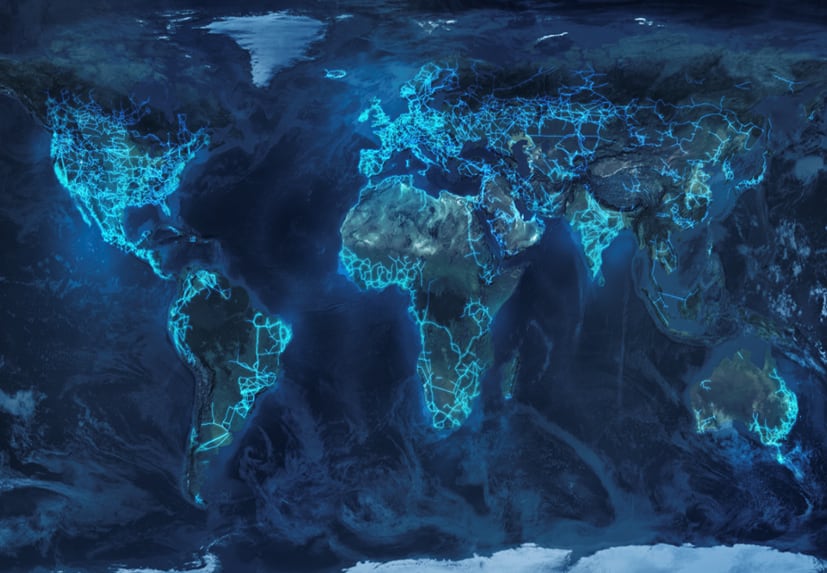
CLICK TO NLARGE
New Technology, New Testing
Software increasingly determines the functionality of power system equipment and its interaction with the grid and that means new, unforeseen error modes can emerge. This calls for new ways of testing. Aside from essential traditional testing of individual components for compliance with appropriate standards, we will also need “fit for (grid location) purpose” testing of software-driven equipment. This will best be accomplished through (control) hardware in the loop testing, whereby the real environment in which components function is simulated (using a simulation that has been validated to behave like the real power system). Signals from the simulated grid are fed into the component under test and the response is fed back into the simulated grid. This way, the behaviour of software – the equipment’s ‘brain’ – is tested to prevent risk of rogue software entering that could jeopardize power system operation.
[inline_ad_block]