The growth of high voltage power networks worldwide has been driving a proliferation of new transmission and distribution components as well as new manufacturers. Before installing such new T&D components in their power networks, utilities must be confident they are reliable and will function as intended and minimize risk of potentially costly outages. However, according to industry tracking data, the second most common cause of outages is faulty components. This means failures can be substantially reduced by adequate asset management and by selecting only components with proven technical performance.
Type testing per international (IEC) standards is the best way to verify technical performance. For example, as explained in this edited contribution to INMR by Floris Schulze, Bas Verhoeven and Uberto Vercellotti of KEMA Labs – Testing & Certification Division, long-term experience indicates that some 25% of T&D components initially fail to pass IEC type test requirements. In the case of power cables and their accessories, this number is even higher. Remarkably, this failure rate has not decreased over the past 25 years, suggesting that experience as well as improved materials and manufacturing techniques have not necessarily improved the quality of T&D components.
But even when compliance of cables and their accessories with standard requirements has been proven at the end of production, there is still a long way from factory to installation and final operation. This process includes critical phases such as storage, transport, handling, laying and assembly. These activities are mostly performed on-site and sometimes under adverse ambient conditions and are therefore susceptible to causing failures, which must be identified and solved before commissioning of a circuit. As such, so-called On-site Commissioning tests are critical to guarantee the safe and smooth operation of cables under the rated operating conditions to which they have been designed.
The transmission and distribution sector faces a constant challenge to deliver reliable and cost-effective electricity. Equipment certification through testing can guarantee the quality of components installed in the network and contribute to power system reliability, representing a fundamental step in reducing probability of disturbances and outages.
In addition to type tests and qualification tests (PQT), which allow the nominal performance and durability of cable systems to be verified, Onsite Commissioning tests, together with diagnostic tests such as partial discharge (PD) measurements, also need to be considered.
In light of stringent international regulations, electricity supply companies and transmission system operators must emphasize evidence-based approaches to demonstrate due diligence when specifying electrical equipment. This requirement becomes even more important when considering the growing number of substations and electrical installations located near populated areas, as well as the consequent goal of reducing their ‘fingerprints’.
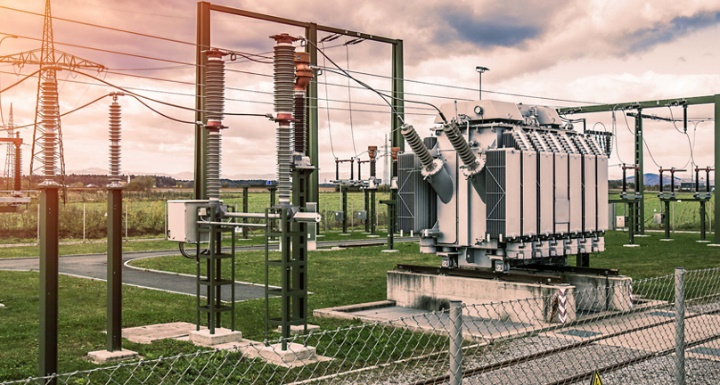
Both trends not only raise concerns related to public safety but also elevate the economic stakes associated with potential catastrophic failures.
Outages in Power Networks
Power system interruptions or outages are caused by various incidents. The Eaton Black Out Tracker, for example, shows the distribution of recent outages affecting the U.S. power grid, which experiences an average of about 3600 outages annually. Fig. 2 shows the distribution of the causes of these outages, many of which are caused by external influences such as weather, wildlife and vehicle incidents. Still, the main internal cause, accounting for about 22% of outages, is Faulty Equipment or Human Error.
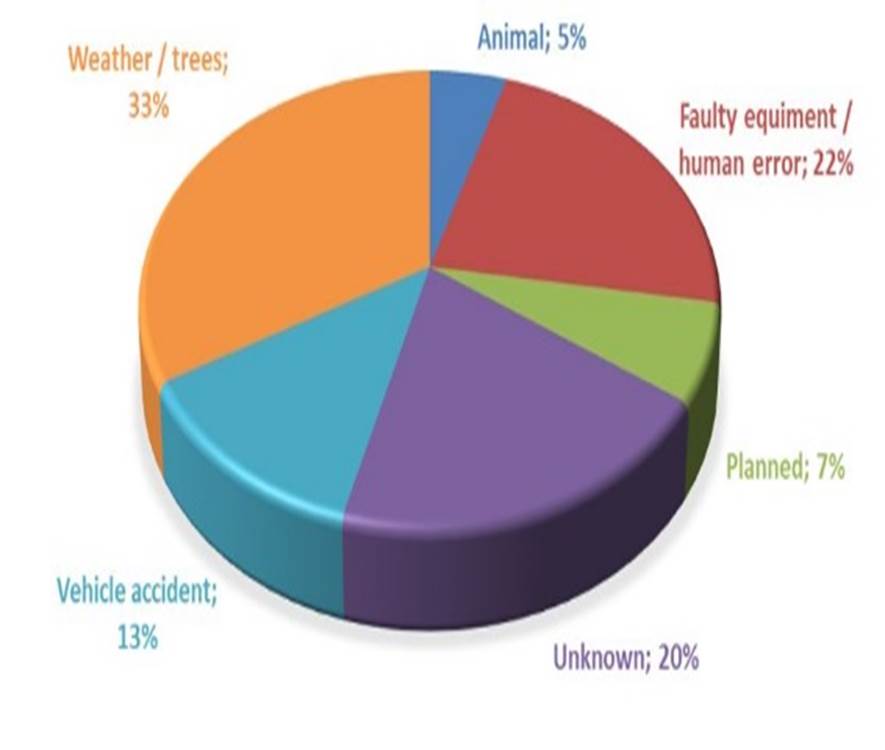
This can be reduced by adequate maintenance and, more importantly, by ensuring that components installed in the network have been successfully type tested against the relevant international (IEC) standards.
International Standards for Testing Power Cables
The IEC publishes standards for all components used in the power sector. In the case of medium and high voltage AC cables and cable systems, the relevant standards include:
• IEC 60502-2 for Cable 6 kV – 30 kV,
• IEC 60502-4 for Cable Accessories 6 kV – 30 kV,
• IEC 60840 for Cable & Accessories 30 kV – 150 kV,
• IEC 62067 for Cable & Accessories 150 kV – 500 kV.
The IEC standards include 2 distinct groups of tests: the first group is Type Testing, where a cable or cable system is tested to verify design and manufacturing. A cable system also includes accessories such as joints, open-air terminations, and SF6 or oil plug-in terminations. Typically, the cable or cable system is tested in a laboratory with various electrical tests followed by heat cycle testing to simulate the ageing and loading pattern of a cable during normal use. The test for non-electrical properties of the cable is also part of the type test.
In the second group, Pre-Qualification testing is applicable only for high and ultra-high voltage power cables. After successful completion of the type test, a cable system is installed under realistic outdoor conditions that mimic normal installation methods such as directly buried in the ground as well as sections installed in a tunnel. A voltage of 1.7 Uo is applied to the cable and 180 heating cycles are applied, one every 2 days. A pre-qualification test has duration of one year.
Plan to participate in the 2023 INMR WORLD CONGRESS in Bangkok to listen to a presentation on the important topic of cable testing in the laboratory and on-site by Uberto Vercellotti, a long-time expert in the field of cable testing and condition monitoring. He will be joined by many other experts discussing experience and methodologies used in this regard, including:
[inline_ad_block]