Analysis of findings from all type tests performed at KEMA Labs – an organization that tests and certifies components used in power transmission and distribution networks – shows that about 1 out of every 4 type tests performed fail to initially meet the requirements of the applicable standard. Moreover, this 25% initial failure rate has remained stable over decades. Such a finding is clearly unexpected given the improvements in materials, calculation methods and production technologies achieved over the years.
This edited contribution to INMR by Bas Verhoeven, Executive Vice President at KEMA Labs, reviews some key lessons learned from extensive data on past failures of cables and accessories during laboratory testing. It also argues that ensuring low in-service failure rates requires that type-testing and independent certification must remain an important tool to distinguish products that are well designed and manufactured from those that are not.
Outages in Power Networks
Power system interruptions can be caused by a variety of incidents. The Eaton Black Out Tracker, for example, has reported on the distribution of all outages across the U.S. power network which totalled 3,525 in 2017. Fig. 1 shows how the causes of these outages were distributed. While most were caused by ‘external’ factors such as weather, animals and vehicles, the leading ‘internal’ cause (covering 22% of all reported outages) came from faulty equipment or human error. Moreover, over the span from 2008 to 2017, this category showed year-on-year increases in absolute numbers of incidents, due mainly to increasing power network load.
Reducing the impact of this ‘internal’ component can be accomplished through proper and adequate maintenance. But ensuring that the components installed on the network have been properly type tested against the relevant international standard is even more important.
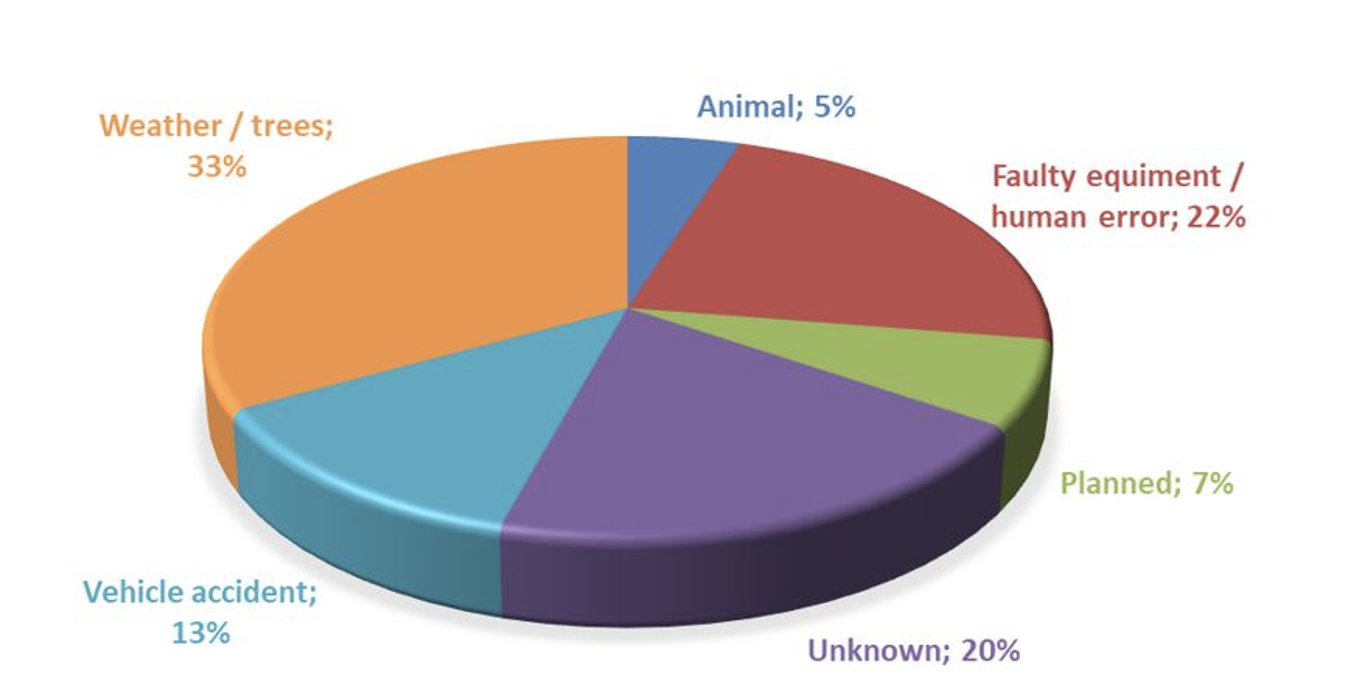
International Standards for Testing Power Cables
The IEC publishes standards for all components used in the power sector and relevant standards for medium and high voltage AC cables and systems include:
• IEC 60502-2 for Cables 6 kV–30 kV
• IEC 60502-4 for Cable Accessories 6 kV–30 kV
• IEC 60840 for Cable & Accessories 30 kV–150 kV
• IEC 62067 for Cable & Accessories 150 kV–500 kV
In 2022, the STL Guides to IEC 60840 and IEC 62067 have been revised. The aim of these guides is to harmonize execution and interpretation of IEC standards and they focus on pre-qualification testing since this area is not that detailed within IEC standards.
IEC standards include 2 distinct groups of tests:
The first is Type Testing, whereby a cable or cable system is tested to verify design and manufacturing. A cable system includes the cable as well as accessories such as joints, open-air termination and SF6 or oil plug-in terminations. In this regard, a cable or cable system is tested in the laboratory with various electrical tests followed by heat cycle tests to simulate the ageing and loading pattern during normal use. The test for the cable’s non-electrical properties is also part of the Type Test.
The second group, Pre-Qualification Testing, is only applicable for high and ultra-high voltage power cables. After successful completion of the Type Test, a cable system is installed under realistic outdoor conditions that mimic normal installation methods, such as being directly buried in the ground or with cable sections installed in a tunnel. A voltage of 1.7 Uo is applied to the cable and also 180 heating cycles, one every 2 days. A Pre-Qualification Test therefore has a duration of a year.
International standardization for DC cables is presently less developed than for AC and construction, technology and voltage levels for HVDC cable applications are undergoing rapid development. DC cables have specific test requirements for temperature gradient over the XLPE insulation material and also include load cycling tests as well as superimposed DC and LI tests. A newly introduced test is the Temporarily Overvoltage Test. Existing standards for DC cables include:
• CIGRÉ 496;
• IEC 62895:2017;
• Client special specification, e.g. GTSO;
• CIGRÉ TB 852 (for extruded cables);
• TB 853 (for mass impregnated cables).
Failure Statistics From Type Testing AC Cable
All components used in a power system are type tested and KEMA Labs, for example, has performed numerous such tests for manufacturers from across the globe. Among the main equipment and components type tested are transformers, all types of switchgear, instrument transformers, insulators and power cables. In this context, statistical analysis has been performed to determine how many type test sequences initially failed to meet the requirements of the applicable IEC standard.
The outcome of this analysis showed an initial failure rate of approximately 25%, independent of type of equipment/component being tested. In other words, every 4th Type Test sequence fails, which is a high proportion compared to other industries. It can therefore be concluded that components for power networks cannot be treated as ‘catalogue items’ purchased at the lowest price. Fig. 2, for example, provides details on failure rate during Type Testing of medium and high voltage cables and accessories and covers experience with over 1,100 such tests.
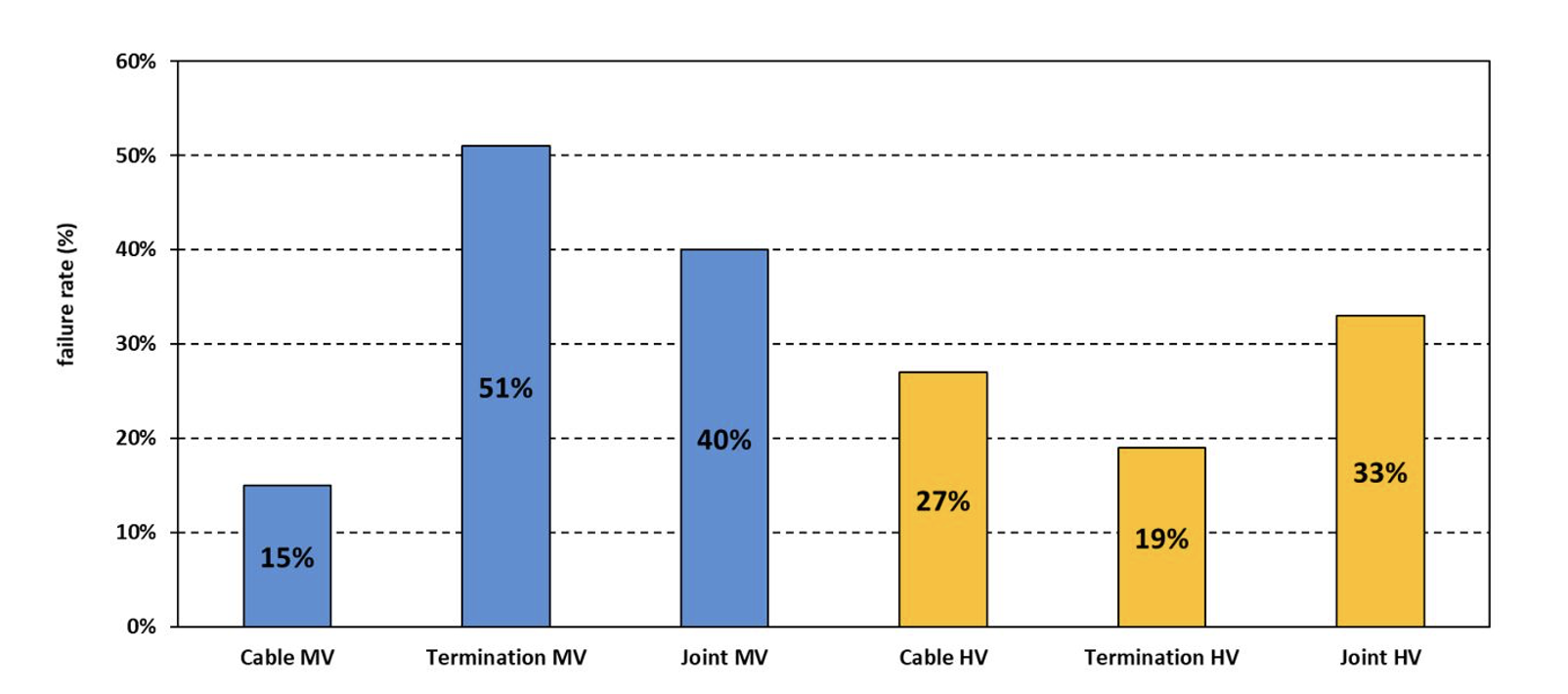
As evident from this chart, medium voltage terminations and joints show relatively high failure rates, caused mainly by improper selection of the materials used for their heat shrink technology. Heat shrink tubes that are able to withstand voltage stress in combination with moisture and pollution are slighly more costly than tubes that do not handle these stesses. Unfortunately, focus on cost reduction is presently a key driver in this market and this has been forcing some manufacturers to select lower quality heat shrink tubes.
In regard to high voltage cables, Fig. 2 shows that these have higher failure rates compared to medium voltage cables. One of the reasons is that a growing number of manufacturers of MV cable are entering the HV market, likely seeking higher profit margins. But some of these companies soon encounter quality issues since their production and technical know-how remains at the ‘MV level’.
Fig. 3 shows year-on-year initial failure rates for MV and for HV cables and accessories. The linear trend lines in both cases have a positive inclination and this means that initial failure rate is actually increasing over time. This in spite of the expectation that failure rate should decrease due to improved production technology, materials, know-how, and experience. It is believed that the main reason for this disturbing trend is market pressure on cost reduction which seems to have gone too far and is affecting the quality of cables and accessories being produced. Over time, this situation can only lead to increasing incidence of outages in power networks.
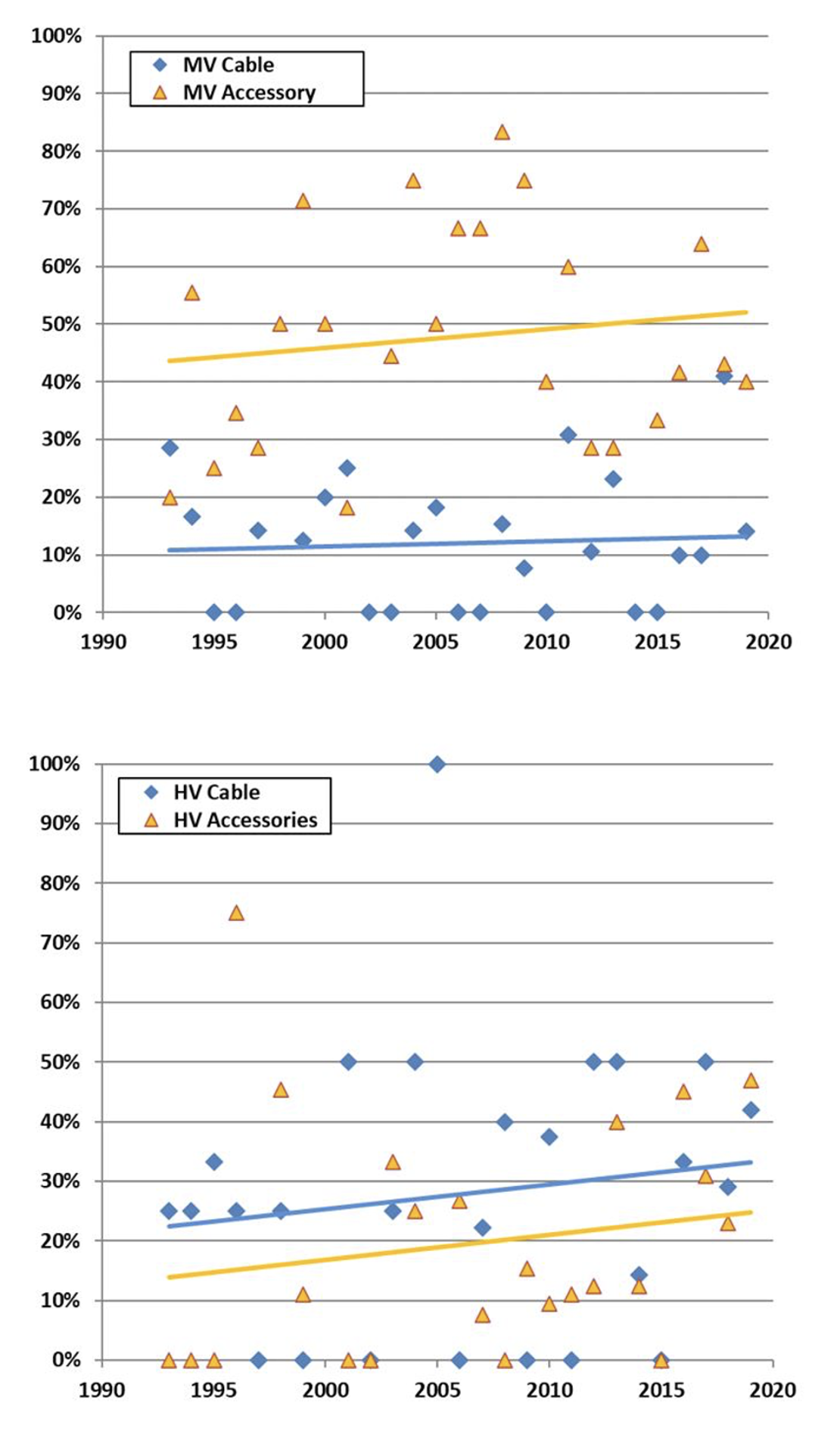
While failure statistics for HVDC cables are not yet available, a first indication from recent testing performed at KEMA Labs shows that initial failure rate is even higher than 25%. HVDC technology is still relatively new and important developments are ongoing, especially at 320 kVdc and 525 kVdc.
Conclusions
Improvement in materials, calculation methods and production technologies has been ongoing but this has not necessarily resulted in decreased failure rate during Type Testing, which for over decades, continues to remain in the range of 25%. Fortunately, in-service failure rate of power system components is much lower and this is because Type-Testing serves to verify their compliance to the standards, which cover about 90% of practical applications. In order to maintain low service failure rates, type-testing and independent certification remains a key ‘de-risking’ tool to identify well-designed and well-manufactured products.
References:
1. Eaton, Blackout Tracker, United States Annual Reports, Power outage annual report. https://www.eaton.com/us/en-us/products/backup-power-ups-surge-it-power-distribution/backup-power-ups/blackout-and-power-outage-tracker.html
2. IEC International Electrotechnical Commission. Website iec.ch
3. Testing Extruded Cable Systems Up to 525 kV DC: Laboratory Experience & Latest Requests from the Market, Heiko Jahn & Uberto Vercellotti, KEMA Labs, INMR Conference 2022
[inline_ad_block]