Attitudes toward composite insulators have gone through several distinct phases since the 1970s, when researchers first began exploring a technology based around the unique properties of materials such as silicone rubber. Engineers of that era had ‘grown up’ alongside porcelain and glass insulators and the large majority initially regarded this innovation as no more than a ‘sideshow’ – a novelty, yes, but one that carried deep uncertainties about possible premature ageing and sudden catastrophic failure. Few power utilities at the time were willing to experiment with composite insulator technology since the risks seemed to far outweigh the benefits.
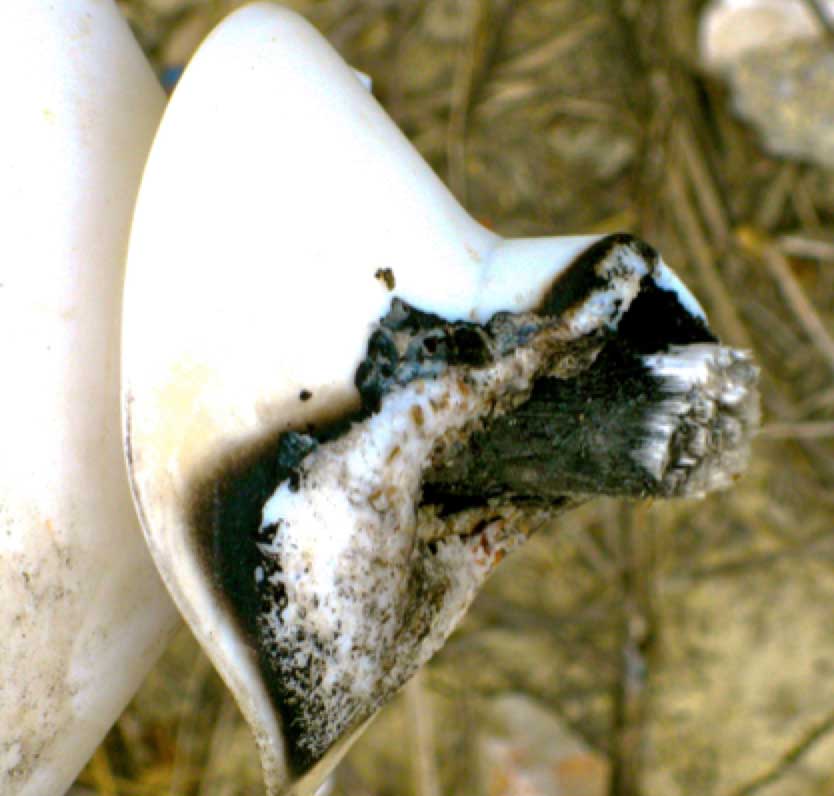
CLICK TO ENLARGE
During the 1980s, polymeric insulator technology had progressed in the minds of many line design professionals from ‘risky novelty’ to ‘unique problem solver’. Whenever specific issues had to be resolved, such as pollution flashover, vandalism or difficulty handling heavy ceramic insulators, polymers offered an interesting though more costly alternative. The ±500 kV Intertie running along the U.S. west coast was a good example of one project where superior pollution performance was key in the selection of composite insulators. Similarly, initial applications of these insulators in countries such as Morocco and Brazil were aimed at overcoming problems related to chronic vandalism.
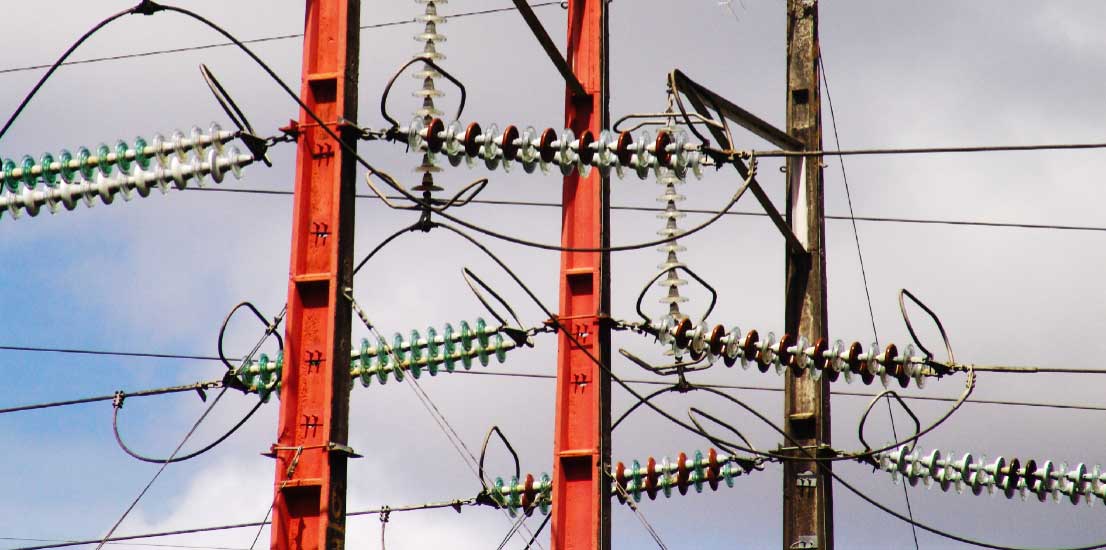
CLICK TO ENLARGE
By the 1990s, attitudes toward composite insulators had evolved yet again. Now, their range of applications continued to expand as more and more engineers looked to them as first choice for tower compaction projects or when upgrading lines using existing tower windows and right-of-ways.
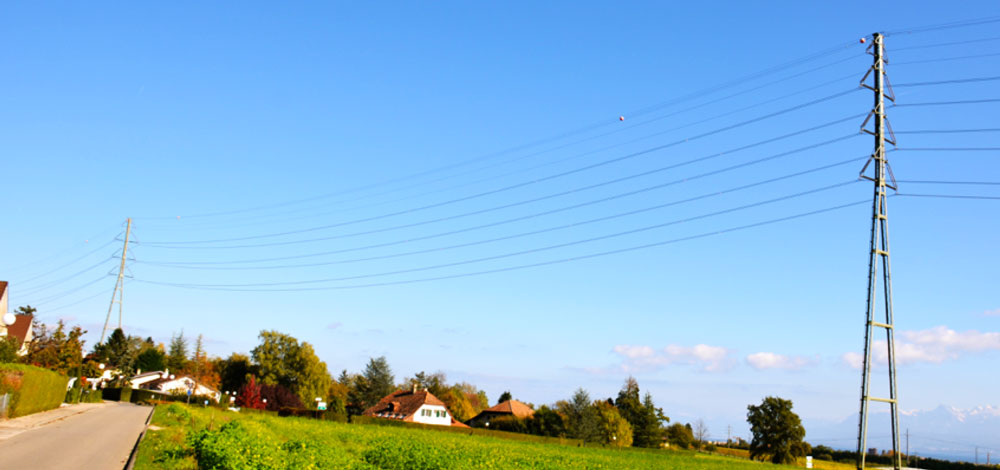
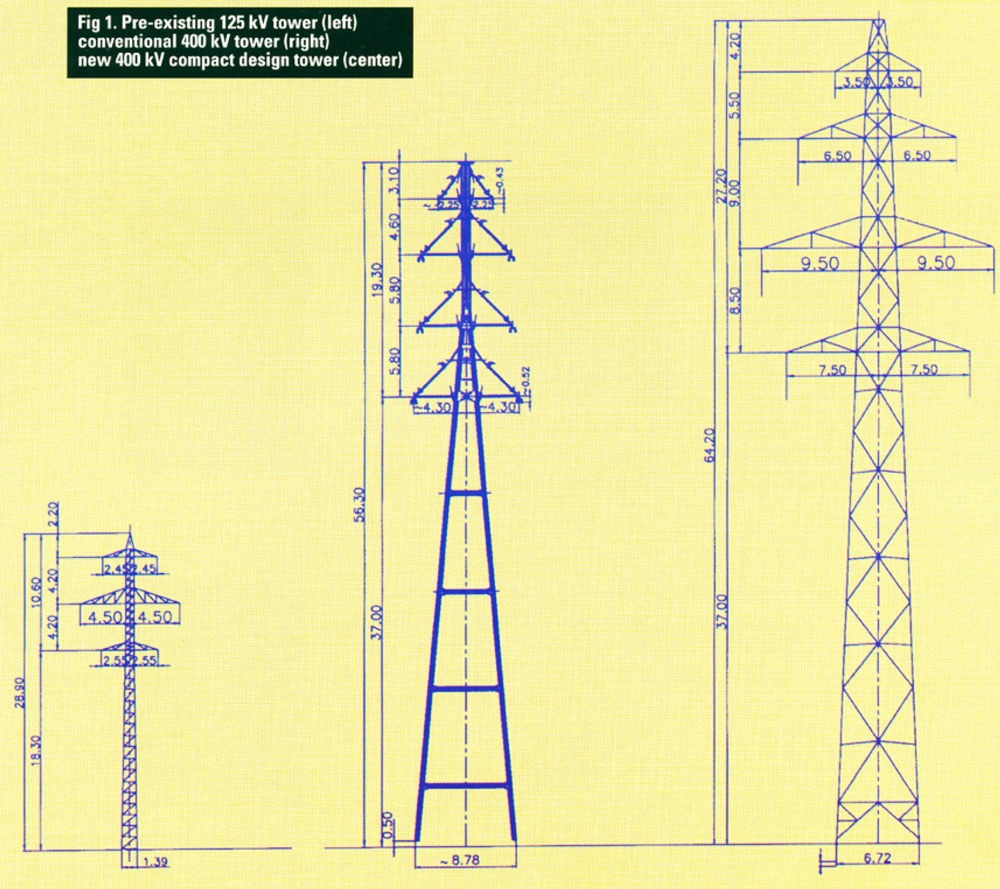
CLICK TO ENLARGE
By the turn of the millennium, the composite insulator technology ‘genie’ had been ‘unleashed from the bottle’. Now, this technology, which had once been restricted to only a handful of major insulator suppliers, was available to anyone who had an interest to enter this business. Hundreds of new suppliers, particularly in China, started to manufacture composite insulators.
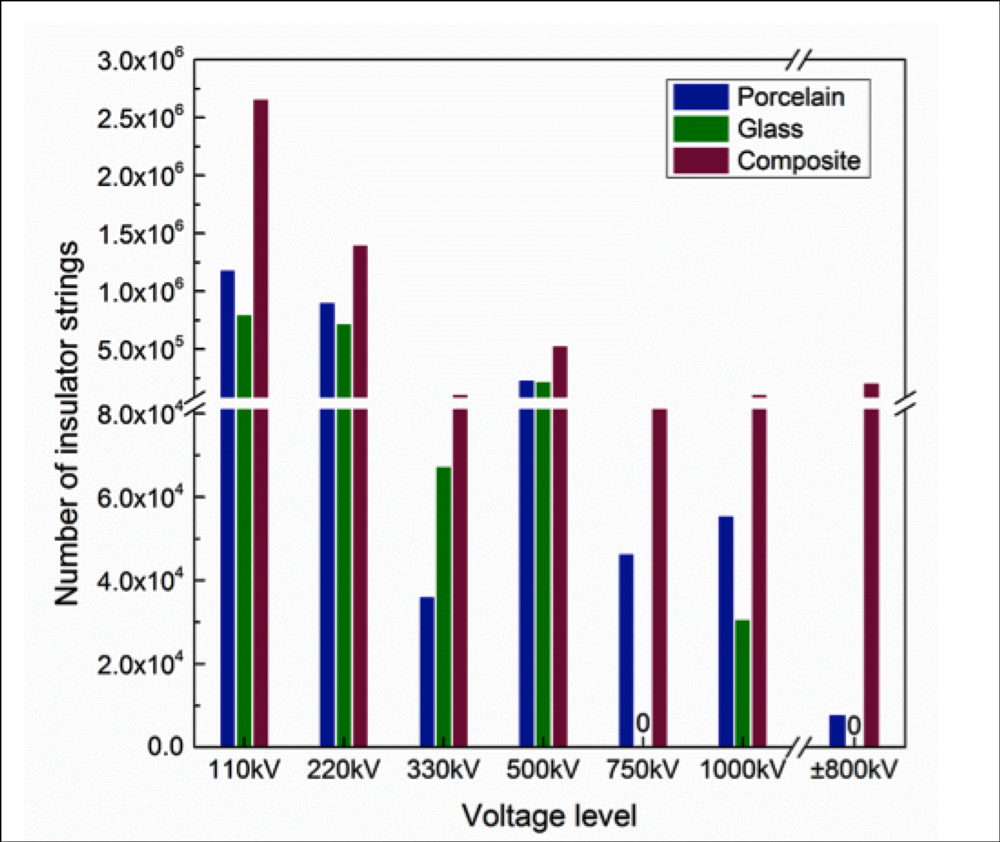
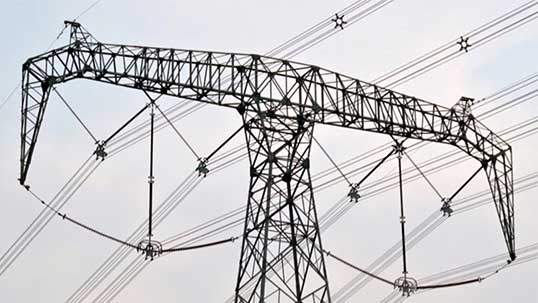
Composite insulators, which in the 1980s had a market share of less than 1 percent and in the 1990s less than 5 percent, had by 2010 already began to challenge porcelain for market dominance. Projection of this trend has continued into 2021 such that composite insulator technology is now the most commonly used on overhead line projects worldwide. There is also rapid growth for substation applications to the point where certain applications, such as DC, and certain system voltages, including EHV and UHV, see composite housings specified in equal or greater measure to porcelain.
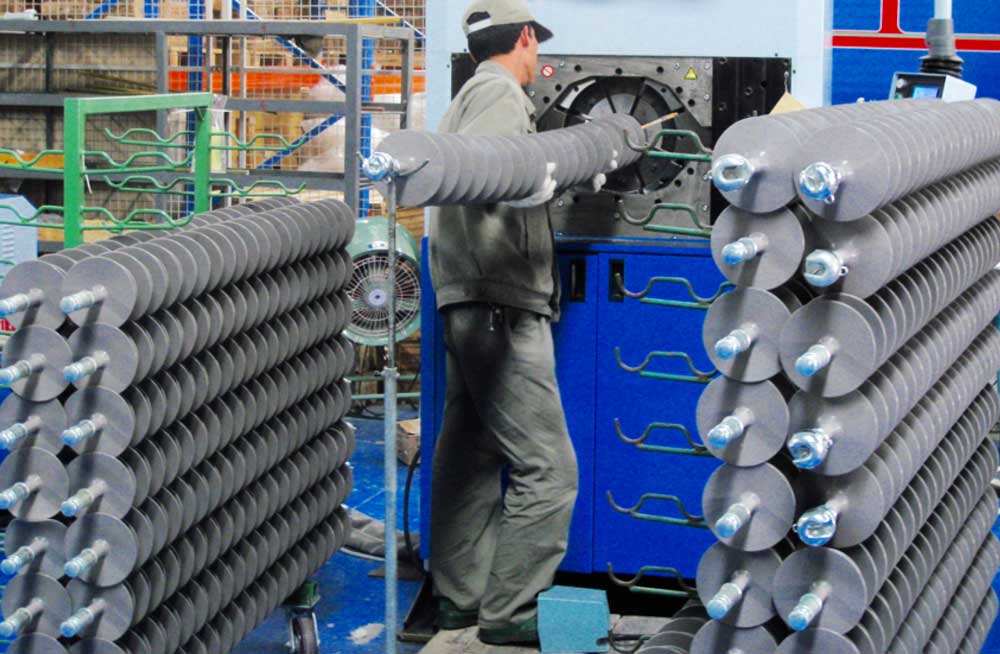
CLICK TO ENLARGE
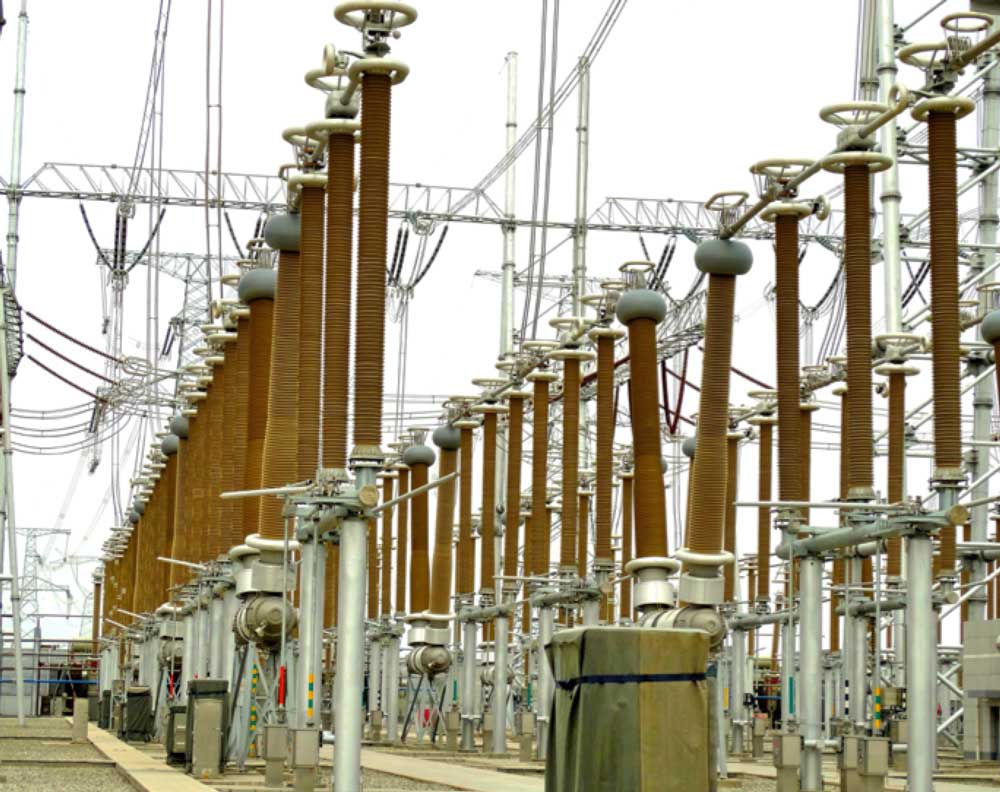
CLICK TO ENLARGE
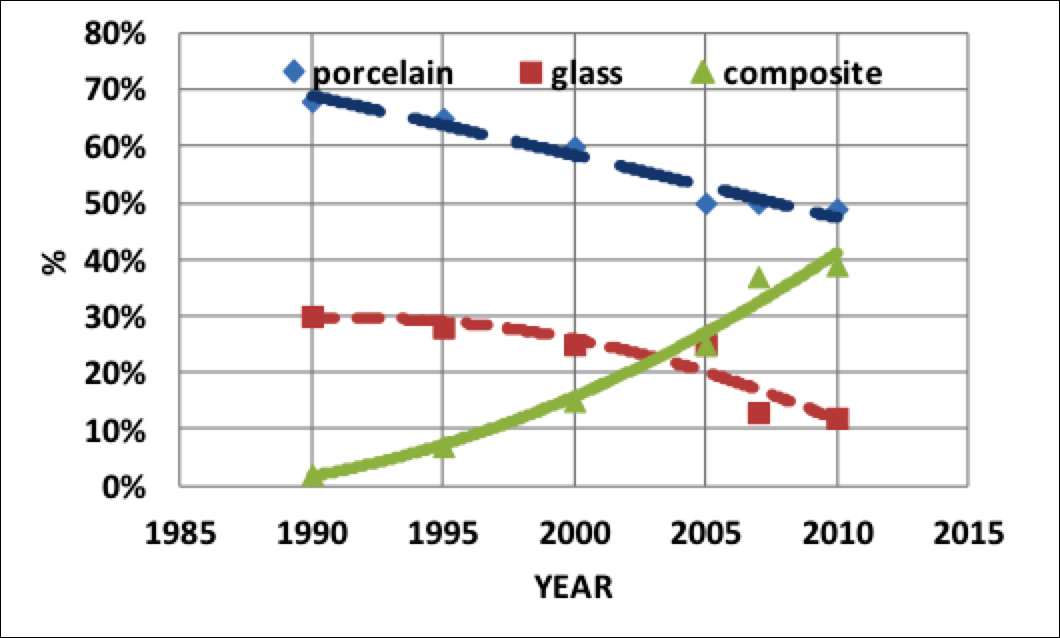
Several years ago, the 750 kV Shazhou Substation in Northwest China offered an interesting milestone along this fascinating ‘journey’ of composite insulator technology. Like a smaller substation in Switzerland that had been designed two decades earlier using mainly composite insulators, Shazhou saw composite insulator technology used on every piece of equipment and in every support application. This milestone must have felt highly satisfying for the many experts worldwide who worked tirelessly for decades to develop and refine this technology.
Yet it seems counterintuitive to ever make decisions based around using only a single insulator technology across all applications. In fact, the real benefit of all that has been achieved in optimizing porcelain, glass and polymeric insulation over the past 50 years is that engineers today have the option to select the most suitable technology for the specific requirements, environment and economic constraints of each application.