Increasing challenges as well as opportunities for the expanding global power grid are promoting improved technologies over traditional practices. New options to address the ever-present challenge of corrosion on the critical high voltage transmission lines are proving effective around the world.
Use of thermal diffusion galvanizing (TDG) technology provides multiple benefits beyond traditional hot dipped galvanizing. This edited contribution to INMR by Jeff Butler, Principal Engineer, Transmission at Hubbell Power Systems explores the benefits and options available by using TDG for the effective improvement of extending the life of critical high voltage transmission line components.
Corrosion Problems Today
The ageing global power grid is under constant threat due to the devastating effects of corrosion. Utilities and line owners will therefore need to give earnest consideration to how they address the destructive nature of corrosion on their systems. The traditional practice is to coat exposed ferrous hardware with a process called hot dipped galvanizing (HDG). This process has become widespread in this and other industries to prevent corrosion and extend the life of critical components. The typical lifespan of HDG components can vary depending on the environment. Certain higher risk or heavily contaminated areas may require solutions beyond HDG such as stainless steel or special coatings or paints. These solutions can be costly both in material and labor. However, advancements in technology can provide more effective options that may not yet be well understood.
Search for Better Corrosion Protection Solutions
As the ageless battle against the destructive effects of time continues in so many aspects of our lives, those responsible for maintaining the critical infrastructure of the global power grid have found solutions of varying effectiveness and cost. It is generally accepted that corrosion issues become more concerning near areas of specific contamination exposure such as near the coast, industrial facilities, or heavy agricultural areas. Some of the solutions to combat this corrosion are more effective than others and can be quite exotic possibly involving complex studies, designs, installations, inspections, and high costs. There is no single solution to eliminate concern for corrosion on high voltage transmission lines nor would it be appropriate to apply a single solution in all cases. However, there is a technology that has proven effective in other industries with similar corrosion concerns and applications that could provide sound applications within the power utility sector. That solution, which is growing both in availability, economics, acceptance in the power supply industry, is using thermal diffusion galvanizing. TDG technology provides improved benefits versus HDG and can better protect some of the critical components of high voltage transmission lines from the damaging effects of corrosion.
Thermal Diffusion Galvanizing (TDG)
TDG is a process in which zinc powder vaporizes under controlled conditions and diffuses into the surface of iron or steel parts to provide enhanced corrosion protection over the traditional HDG process. The thermal diffusion process for application of zinc to metallic parts is not new. The basic idea was first referred to as Sherardizing and developed back in the early 1900s. Since then, countless applications of this technology have been effectively deployed in multiple industries where corrosion is a concern. These other industries include marine, automotive and military applications that have developed the confidence and experience on which the power utility applications can turn to for the limited applications in use today. The current TDG process (e.g. as used by Hubbell) has been approved and applied by major utilities worldwide. While there are similarities in the components of the process, applying TDG is different than HDG. The more familiar HDG process involves special preparations of components before they are dipped into a molten bath of zinc. In contrast, TDG parts are cleaned with a simple wash and blasting system before they are processed in a computer-controlled oven using proprietary zinc powder formulations. This process involves significantly greater control over the process so that the zinc sublimates and diffuses into the surface and sub-surface of the parts properly. The last step is the sealing process to finish the parts to finalize the long-term performance of the protection.
Advantages of TDG Technology
One of the most important advantages of TDG technology is the significant improvements in environmental impact of the process compared to traditional HDG. Back in 2006, the United States Environmental Protection Agency (EPA) performed an extensive study on the TDG technology. The outcome of that study was the process was awarded the EPA’s 2006 Most Valuable Pollution Prevention (MVP2) Award and stated the process “approaches zero discharge.” This is a significant contrast to the harsh environmental impact of the HDG process which contributes significant waste of energy and materials as a by-product of the process. Furthermore, the self-contained ovens and computer-controlled heat of the TDG process provide significantly reduced safety risks to personnel and facilities compared to HDG.
In addition to significant environmental impact improvements, the TDG process provides a superior level of protection against the constantly degrading effects of corrosion compared to HDG. At the microstructure level, the outcome of the TDG process provides improved mixing of the Zinc and ferrous materials to provide a thicker more durable corrosion resistant layer. When the HDG process is applied, the high-temperature zinc mixes with the ferrous substrate to create the layers shown in Figure 1. These layers form in predictable and distinct ways and determine the level of effectiveness of the corrosion protection of the process. The greater the mixing of the zinc and iron metals within each layer the better the corrosion protection. Therefore, in comparison between the TDG layers and those of the HDG process, the distinct difference is the lack of the Eta layer which composed of 100% zinc. In other words, there is no pure zinc coating on top of the metal surface, because all the zinc exposed to the surface of the part during the TDG process becomes impregnated within the iron. The zinc does not merely form a protective layer on top of the metal, it provides a more effective combination with the iron to increase the durability of the protection.

This effective impregnation of the zinc into the metal substrate results in additional benefits for TDG over HDG. The TDG process provides superior lubricity and anti-galling properties that may be a concern for use of certain stainless-steel hardware. Components that undergo the TDG process are more ideal for crimped applications as the process prevents flaking or erosion of the galvanizing layer unlike HDG. The mechanical strength of materials is not adversely affected such as the fatigue strength of spring or high tensile steel, including stainless alloys. The unique process does not expose the parts to the possible effects of hydrogen embrittlement, and in fact, it will enhance certain properties of steel components such as, rigidity, yield strength, tensile strength and breaking elongation. The TDG process enhances temperature withstand properties since coated components can operate at up to 650°C (1250°F) continuous service temperatures. Moreover, the process does not affect complex and threaded geometries, meaning no loss of dimensional accuracy and treated surfaces can be painted or coated after the application.
During development of this process, Hubbell investigated the TDG process applied to a range of different high voltage components, including:
• Pole line hardware (e.g. bolts, nuts, washers, etc.);
• Assembly hardware (e.g. anchor shackles, chain eyes, hot links, etc.);
• Insulator fittings (e.g. distribution and transmission suspension fittings, distribution and transmission line post fittings);
• Disconnect switch (i.e. moveable components);
• Helical anchors (e.g. plates, rods, etc.).
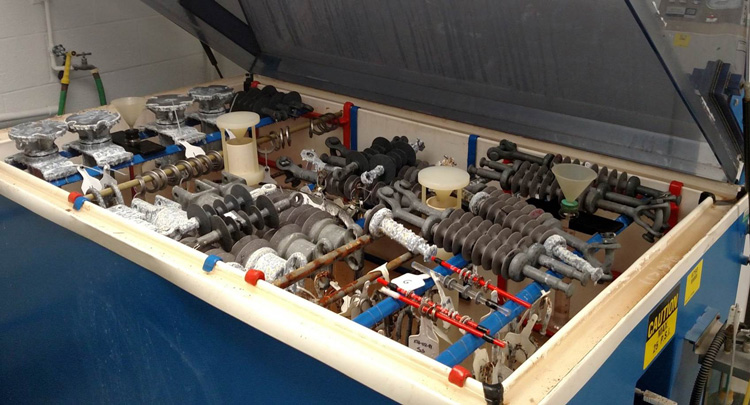
These components were evaluated using the test methods defined in ASTM B117 Salt Fog Testing. In all cases, the TDG product significantly outperformed the HDG product. From the testing there were certain consistent trends observed. TDG treated components experienced corrosion similar to stainless steel grades of 304 or 316. For threaded components, there was still movement along the threads up to 5000h as well as components maintained their geometry and dimensional accuracy. In all cases, the TDG components far exceeded the corrosion protection of their HDG equivalents.
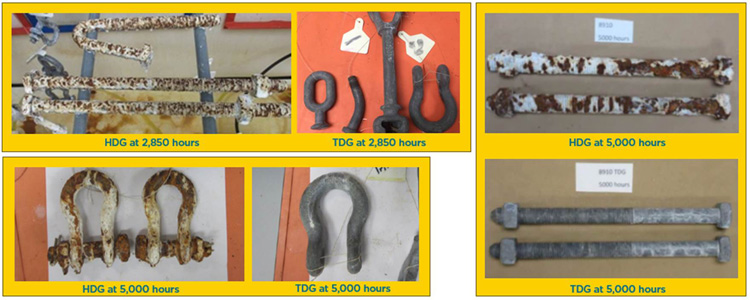
Industry Standards & Acceptance of TDG
There is an ASTM standard that provides guidance relative to TDG. This is ASTM A1059 – “Standard Specification for Zinc Alloy – Thermal Diffusion Coatings (TDC) on Steel Fasteners, Hardware, and Other Products”. However, there is no inclusion of TDG process parameters into other IEC, ANSI, or other standards related to components and hardware for use in applications related to the power utility industry. In the U.S. market, there is slow progress aside from certain utilities that are in varying stages of acceptance of TDG. Some have integrated specific wording to their specifications while others have allowed quoted alternatives based on supportive test results or achievement of certain performance requirements.
Globally, there seems to be slightly more interest and acceptance of TDG with guidance provided by ISO 17413-3:2009 that is a standard referencing the process of sherardizing. Moreover, there are multiple country specific standards from England, Russia and Israel. While there may be other activity that has not been captured here, there is still a lack of a concerted effort to engage within the power utility industry to provide effective guidance on the proper implementation of TDG coating technology for application on high voltage transmission lines.
Summary
The effects of corrosion on the critical components of the power grid is a challenge that must be addressed. However, this challenge requires attention as the grid moves into the future. The traditional method of HDG may not be effective for some of the more demanding applications of high voltage transmission lines. Other options exist of varying effectiveness and cost, but the power utility industry could be well served to increase our understanding and implantation of TDG technology that has proven to significantly extend the life of metallic components in other industries. Hubbell, for example, is one manufacturer that has embraced and developed the TDG process into its product offering across many different components being manufactured.
In addition, there is a critical lack of industry support to address the challenge of corrosion and properly evaluate possible solutions such as this important technology that is emerging into our industry. In that regard, there is a call to action needed. As the professionals responsible for the stewardship of enduring critical infrastructure of the global power grid, it is our charge to explore these technologies as they become available. It is our responsibility to provide the proper guidance to the industry in support of such aims. There are multiple options to get involved in the efforts against corrosion in this industry. Rightfully, it is of utmost importance for those of us that are impacted by the ever-present effects of corrosion to get involved. These effects are universal whether on the systems that fall under our responsibility through employment or for the systems that provide the means of power and comfort to electrify our lives. I encourage the reader to look for ways to get involved, whether through CIGRE, IEC, IEEE, or other groups, there are organizations that can help to advance technology for our common goal to better prepare the operation and performance of the global power grid for the next century.
1 Reference: https://uscorrosion.com/index.php/thermal-diffusion-galvanizing-tdg/
[inline_ad_block]