High voltage ZnO surge arresters play the important role of protecting equipment at power substations against lightning and switching overvoltages. Given this, it is important to regularly monitor their condition to ensure reliable operation. Although many power utilities use resistive leakage current measurement and thermographic inspection as part of their arrester maintenance strategies, these can present difficulties. For example, it is not always possible to obtain a clear diagnosis that integrates all the data while also dealing with possible uncertainties and contradictions.
To overcome such issues, engineers and experts at Itaipu Binacional in Brazil and Paraguay developed a new approach to diagnose ZnO arresters using Annotated Paraconsistent Logic of two values, based on both above techniques as inputs. Results confirm the advantage of this approach, especially in supporting Maintenance Engineering teams in decision making and managing the fleet of surge arresters over the course of their service lifetimes.
Several factors can lead a surge arrester into a degradation process that compromises its performance. Keeping a degraded arrester in service can pose serious risks to the installations in which it is in operation.
Firstly, a degraded surge arrester can have a higher residual voltage value than that for which it was originally designed, to the point that it can exceed the basic insulation level of the installation and associated equipment. In severe cases, the surge arrester can present an energy dissipation that exceeds its limits, even under normal operating voltage. This can initiate a thermal runaway process that culminates in its failure, often accompanied by explosion and projection of fragments of the housing. If made of porcelain, these fragments usually cause serious damage to adjacent equipment and even have the potential to cause injuries or fatalities to anyone in proximity.
Fig. 1 for example shows the catastrophic failure of a 420 kV ZnO surge arrester that occurred at the Itaipu Hydroelectric Power Plant in 2010. This ultimately impacted additional maintenance costs, revenue losses for non-transmitted energy and especially safety risk to personnel.
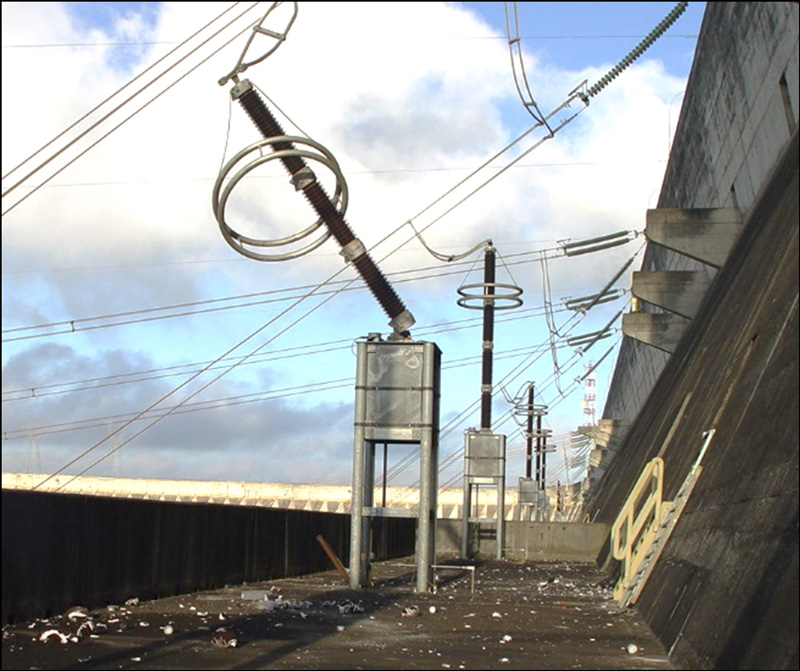
At Itaipu Binacional, the company that operates and maintains the Itaipu Hydroelectric Power Plant, a total of 174 outdoor high voltage surge arresters are in operation at 500 kV, 220 kV and 66/69 kV. There are also 114 indoor GIS high voltage arresters operating at 500 kV. All are ZnO type and their average age is about 27 years, with some reaching up to 39 years – a duration that exceeds their estimated useful life, as cited by Gomes in 2013.
Two predictive maintenance techniques have been used for these surge arresters:
1. Measurement of the third harmonic component of the resistive leakage current (using an instrument based on the B2 method according to IEC 60099-5); and
2. Qualitative thermographic inspection (only for outdoor surge arresters).
Both techniques are performed every 6 months and try to cover the most common failure modes reported in the literature, e.g.
• degradation under the influence of operating voltage;
• degradation caused by current impulses; and
• degradation due to chemical reaction with the environment and atmosphere (Heinrich, Hinrichsen 2001).
By far, the most common of these is degradation related to ingress of moisture into the surge arrester due to sealing defect in its flanges. In fact, in 2014 Gumede and d’Almaine cited that 80% of all surge arresters failures that occurred over the past century were due to moisture ingress.
Initially, resistive leakage current measurements generated a significant amount of data that had to be analyzed in a manual process of evaluating current growth between present and previous measurements. Qualitative thermography, on the other hand, only sought to identify any visible thermal abnormalities in a surge arrester, but without registering temperature values. This made it unfeasible to use this conjunction with leakage current to obtain an integrated diagnostic.
Faced with these difficulties, engineers in the Maintenance Engineering Dept. began to seek a methodology that integrates both techniques and to develop a computerized tool to execute this. Moreover, it also became clear that there was a need to change the thermographic approach from qualitative to quantitative.
Attend the 2023 INMR WORLD CONGRESS, this November in Bangkok, Thailand, to listen to a technical presentation by Mario Augusto Caetano dos Santos. He will explain the innovative approach developed by experts at Itaipu Binacional’s Maintenance Engineering Team based on Annotated Paraconsistent Logic of two values (APL2v), using resistive leakage current and thermographic inspection as inputs.
[inline_ad_block]