Silicone elastomers have come to represent most of the housing materials used for all types of composite insulators as well as silicone-housed arresters, switchgear and similar equipment. However, the variety of silicone products available for application as electrical insulation materials has become far wider. This edited contribution to INMR by Dr. Konrad Hindelang and Dr. Jens Lambrecht of Wacker Chemie offers a condensed overview of some interesting new materials.
In contrast to most other polymeric materials, silicones consist of an oxygen-silicon-chain rather than a carbon-carbon backbone. In the simplest case, the quadrivalent silicon contains two methyl groups, each as side chains, forming a molecule called poly(dimethylsiloxane). Fig. 1 shows a ball-rod-model of this linear molecule.
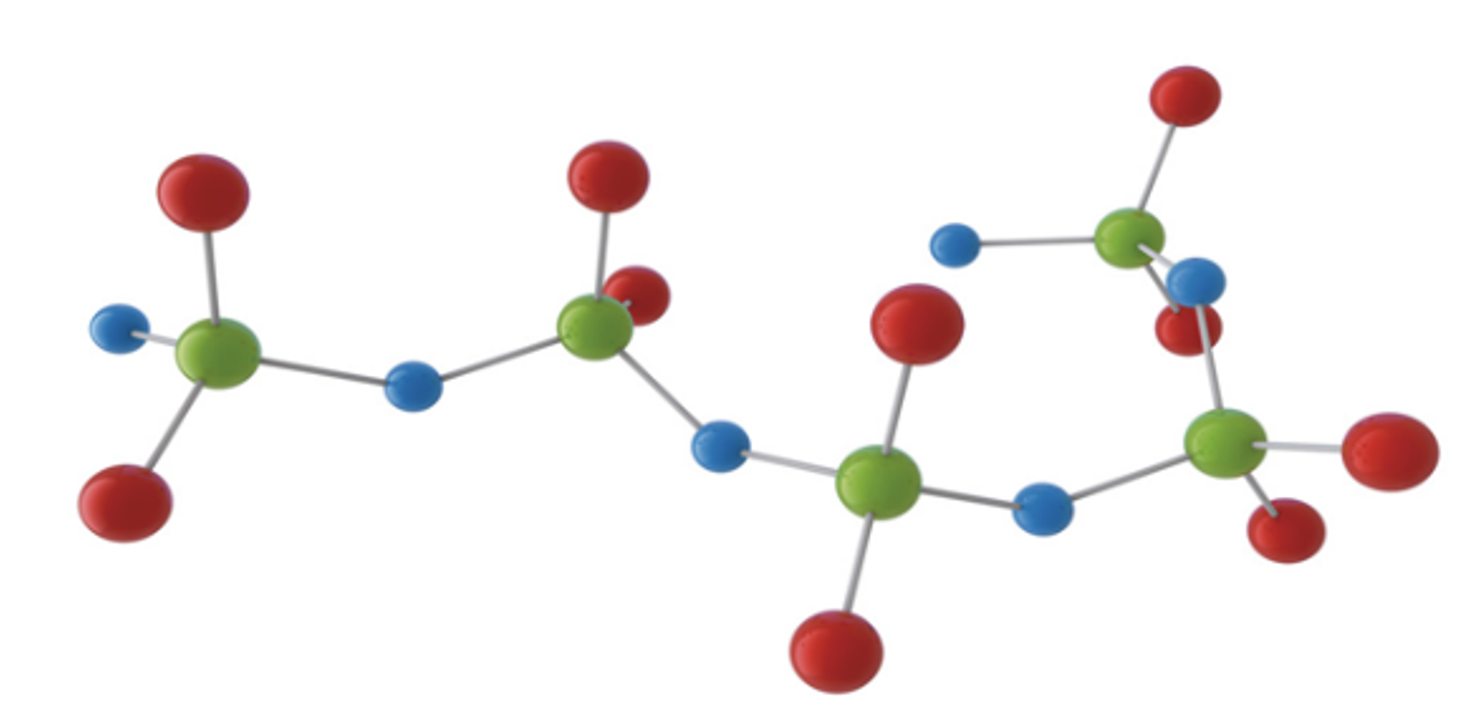
Increasing the length of this Si-O-chain leads to increasing viscosity, which can range from 1 mPa s to 106 mPa s. For example, these materials can be used as sliding agents in their liquid form or as pastes when mixed with thickening agents.
Siloxanes are produced by a hydrolyzation process of chlorosilanes. Putting the appropriate mixture of special chlorosilanes into this process makes it possible to create what are referred to as silicone resins. These materials represent the other extreme of the network density of siloxane-based materials since the silicon can be bound to up to 4 oxy-gen atoms (see Fig. 2).
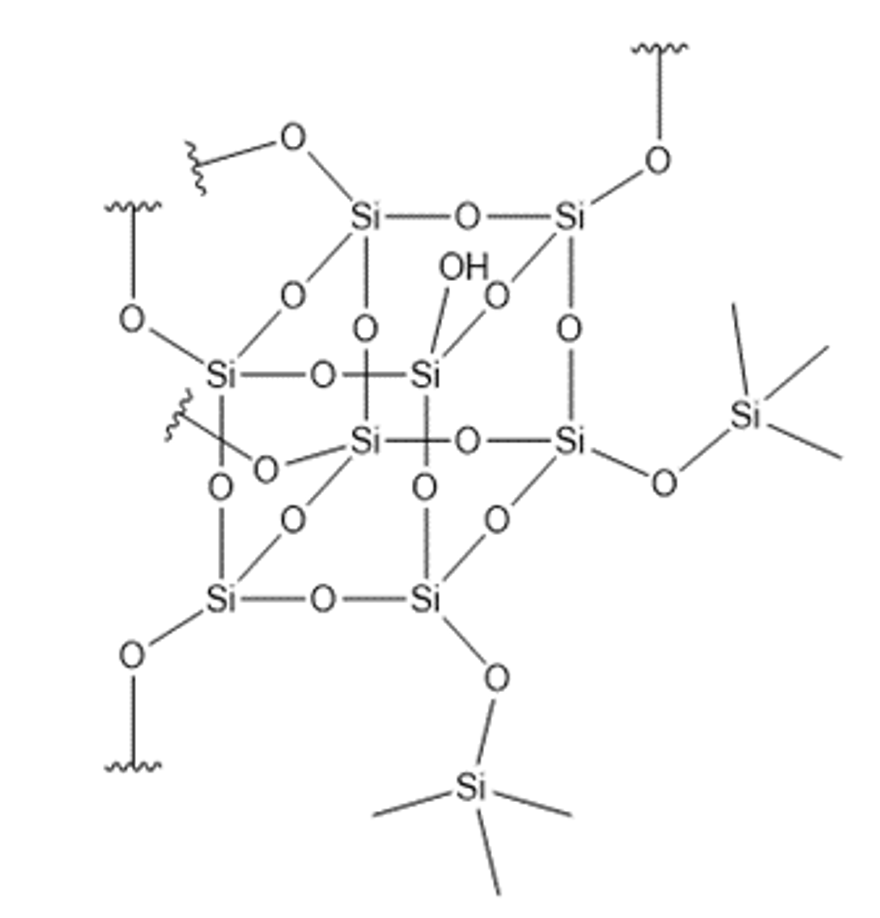
Silicone elastomers, on the other hand, need to be slightly crosslinked in a controlled way. Therefore, these materials are made from modified PDMS, a so-called gum that contains a defined amount of vinyl groups or ethylene groups – CH = CH2 (see Fig. 3). The double bond in that group allows well-defined curing by peroxides as well as by platinum-catalyzed hydrosilylation.
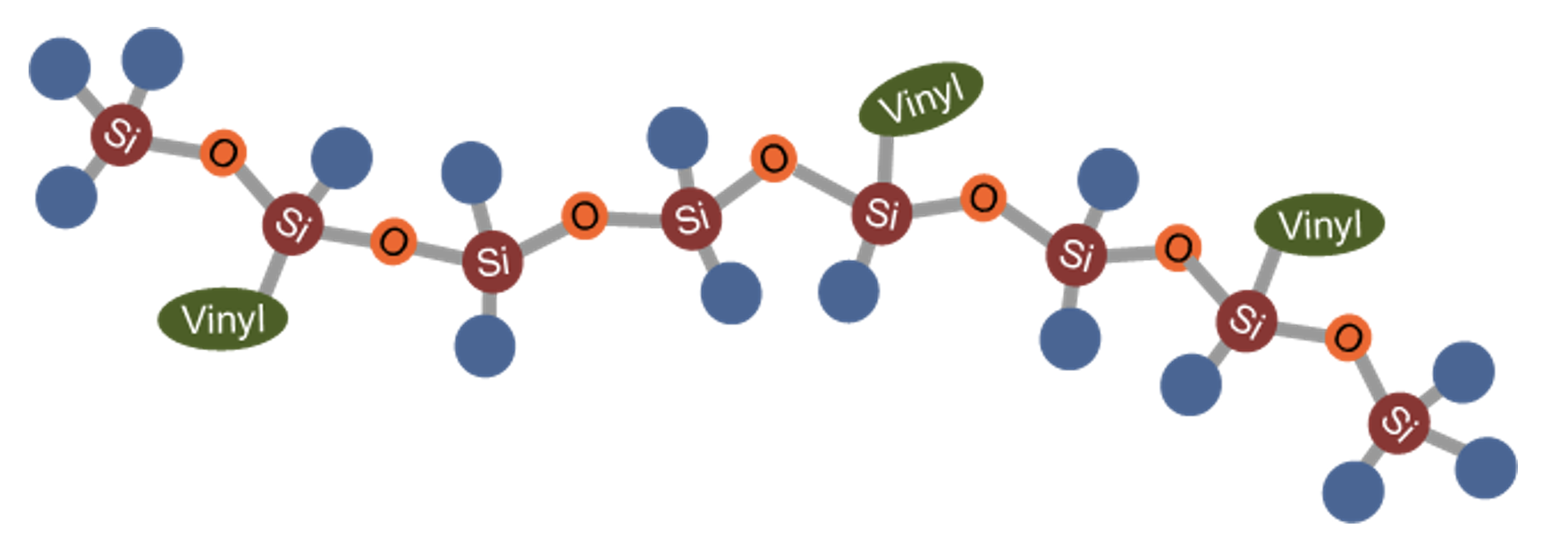
In order to achieve mechanically stable and lasting elastomers, this gum needs to be reinforced by adding highly dispersed (i.e. fumed) silica. For advanced materials with special properties, mixtures with hydrophilic and hydrophobic modifications can even be used (see Fig. 4).
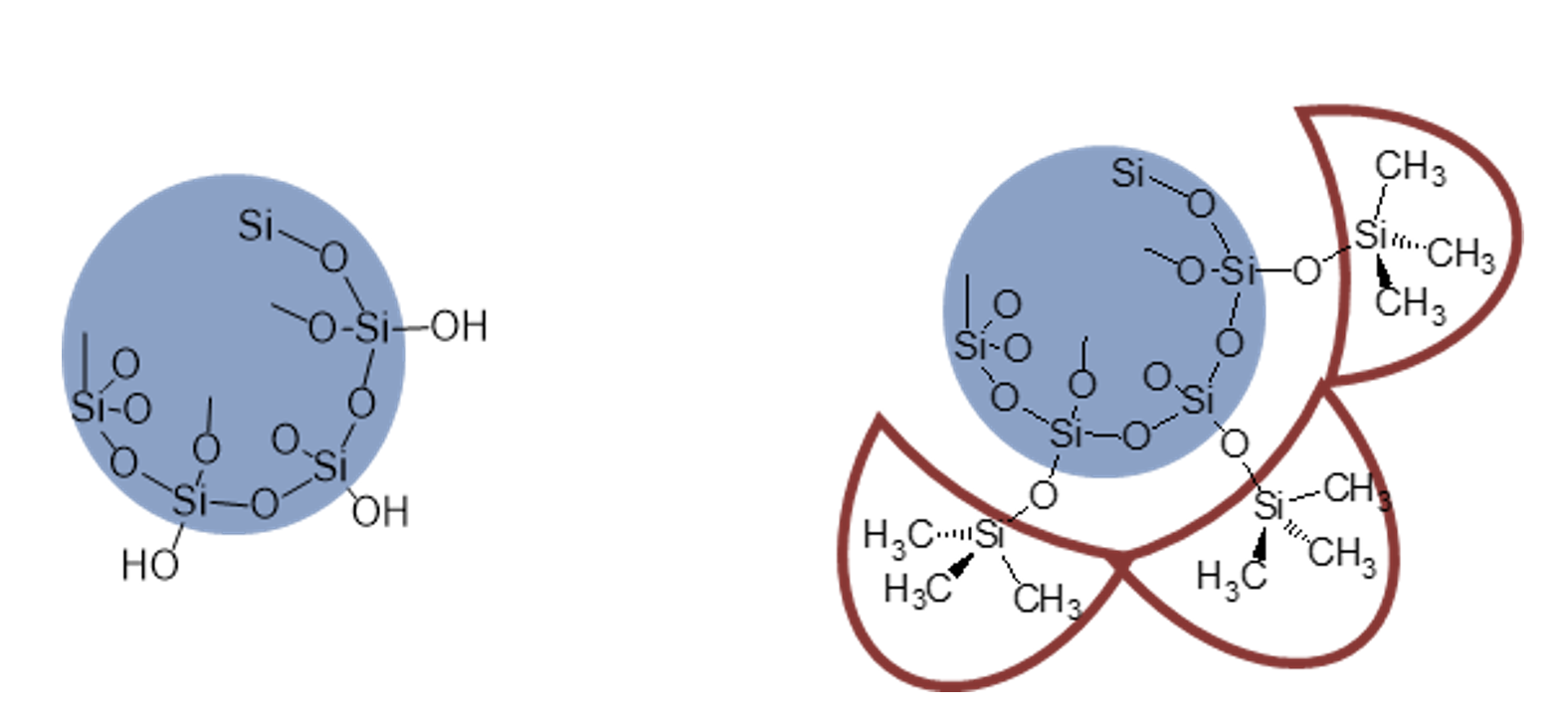
Apart from the reinforcing primary filler, other functional fillers can also be added, such as hydrated aluminum oxide to achieve good electrical erosion resistance, carbon black for electrically conductive materials, color pastes, etc. The mixture of reactive gum, fillers as well as coloring and curing agents can be termed silicone rubbers (caoutchouc), as for their natural counterpart. Depending on the combination of gum and silica used, curable silicone rubbers can appear relatively low in viscosity and be castable or be very high in viscosity such that they are a highly consistent and stiff material (see Fig. 5).
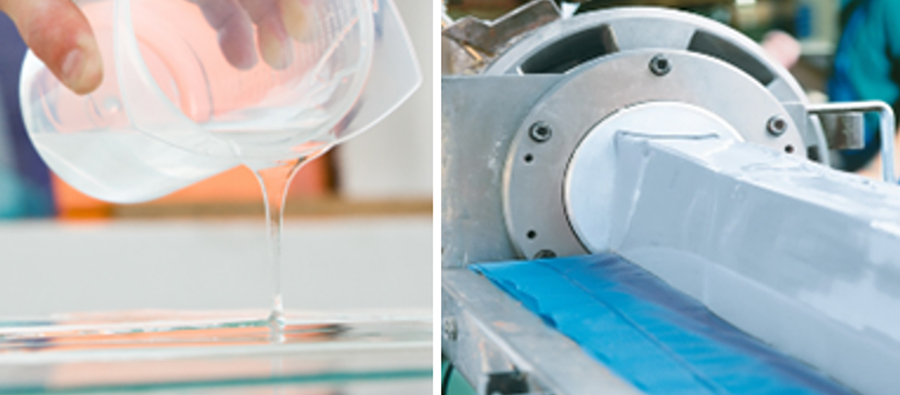
Fig. 6 helps to summarize all these materials. Silicone gels are only slightly crosslinked silicones, typically without any reinforcing filler. Hardness of silicone gels is evaluated by measuring their penetration. Hard gels reach a level of Shore 00. Below this, fluids and gels can be differentiated based on viscosity. Above, in the Shore A-level, one can find the elastomers. As mentioned, their hardness is influenced both by gum type used and by type and amounts of primary and secondary fillers.
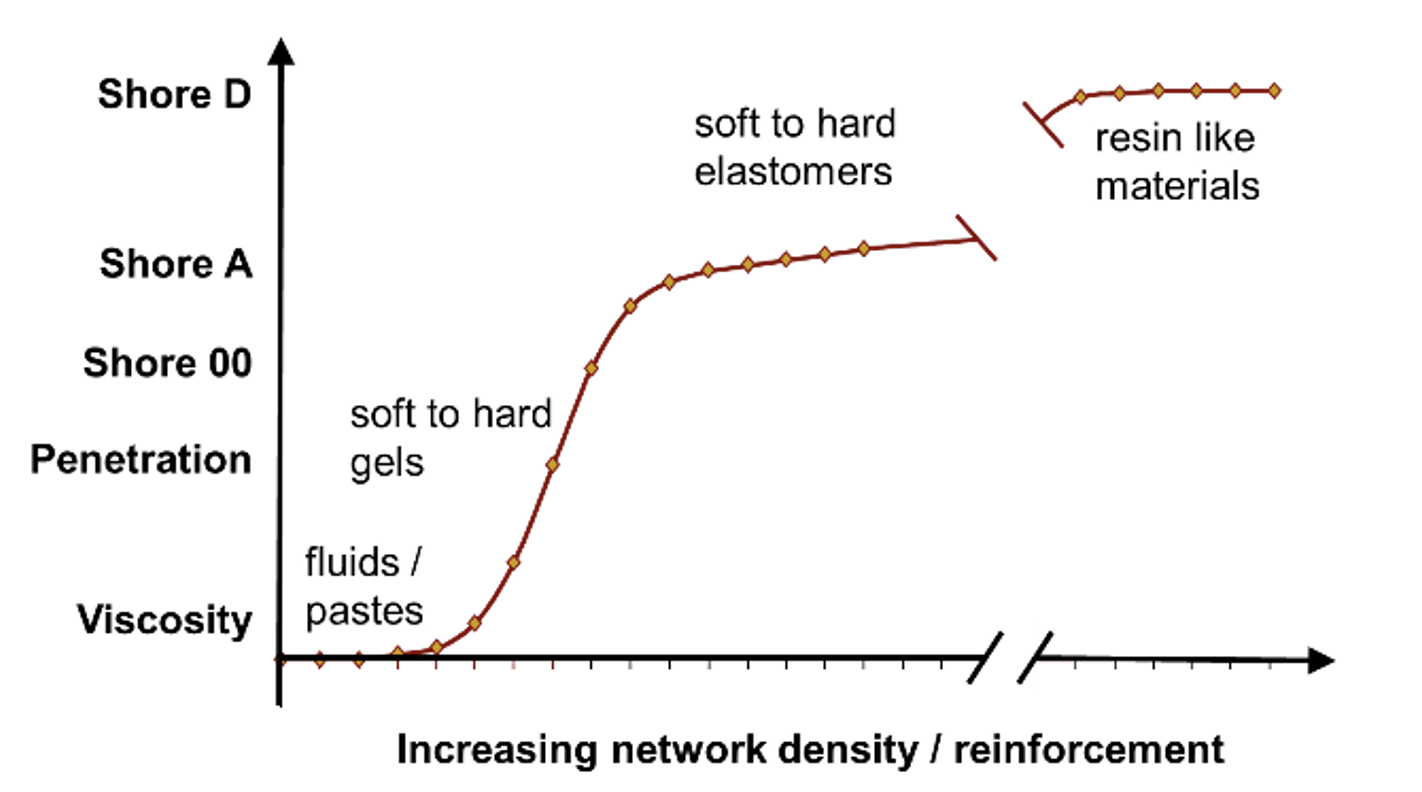
One group of materials that has not yet become the focus for molding applications is silicone resins. Resin ‘moldings’ are usually made by machining laminated blocks. It seems likely that direct molding applications for silicone resins will soon find their way into the market, especially since these materials show extremely high stability to thermal stress.
There is typically a wide gap between the highest level of hardness of silicone elastomers (in the range of 90 Shore A) and the hardness of cured silicone resins (in the Shore D range). There are no materials between these groups and that explains the gap in Fig. 6.
There has been satisfactory progress in development of new silicone molding materials that show thermal stability of >220°C and hence fulfill thermal class R. Due to the chemical nature of the resinous binder, reinforcement with silica alone does not work. A combination of fiber-like materials, quartz, and special silica (see Fig. 7) led to sufficient static and dynamic behavior of moldings, as shown in Fig. 8.
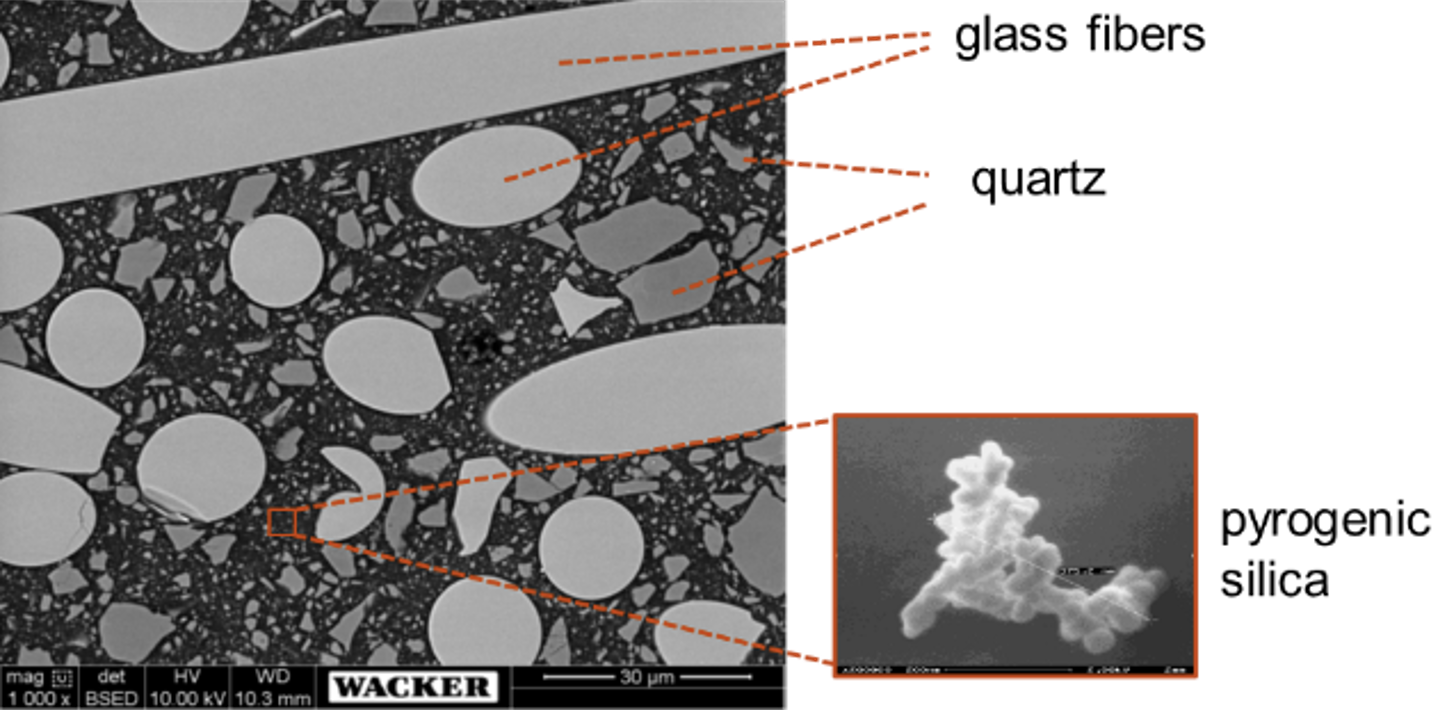
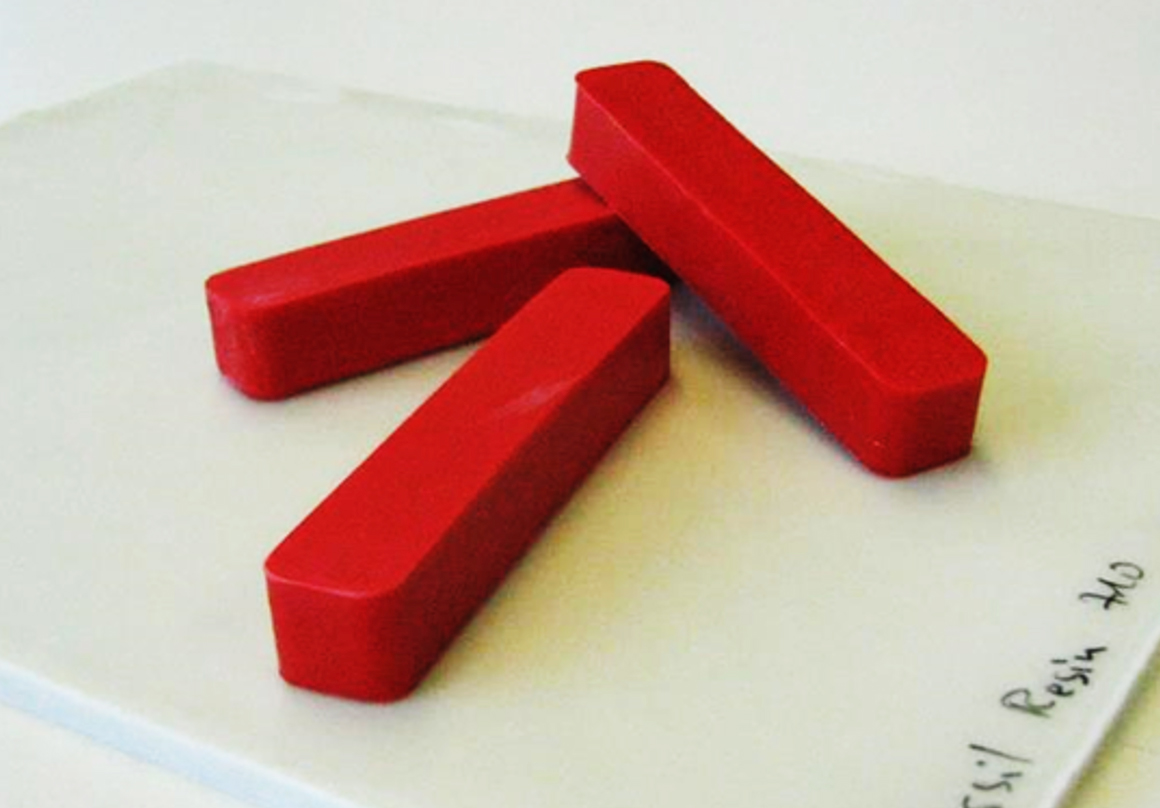
Literature
[1] Lambrecht, J; Winterer, M. New Silicone-Resin-Compounds for Casting and Molding Applications, 22. Symposium Ver-bundwerkstoffe und Werkstoffverbunde, Kaiserslautern, 2019
[2] Tomanek, A: Silicones and Industry, Hanser Fachbuchverlag, 1991, ISBN 978-3446172647
[3] Lambrecht, J; Hindelang, K.: Silicone Gel: More Than Gap Filler, 2019 INMR WORLD CONGRESS, Tucson, Arizona October 2019
[inline_ad_block]