Polymeric insulators have been applied on overhead lines and at substations as far back as 1960. Several different polymers have been tried over the years, often with different results. For example, polytetrafluoroethylene (also known as Teflon) seemed promising at the start and was used in insulators made in Italy starting about 1965. But this material was soon abandoned as not suitable. Other polymers that have claimed superior pollution performance versus porcelain and glass include ethylene propylene rubber (EPR), ethylene propylene diene monomer (EPDM), silicone rubber (SR) and various ‘alloys’ of these polymers. In this edited 2015 contribution to INMR, T&D expert Alberto Pigini discussed some of the factors to consider when selecting the most suitable polymeric housing material for an outdoor insulator application.
While each family of polymeric materials has usually been referred to on the basis of its main bulk polymer, it is important to note that each insulator material is formulated using its own unique ‘recipe’. Specific ingredients such as fillers, colorizers and other additives are added to the main bulk polymer to optimize it from the viewpoints of cost, production and performance. In fact, one issue that remains only partly resolved is establishing the best means to obtain a reliable ‘fingerprint’ of each polymeric material. This is regarded as the best way to assure customers that the insulators shipped to them are exactly the same as those for which type test certificates and field experience have been provided.
EPR, EPDM and SR (in their various proprietary formulations) have been found to be the most suitable polymers with different orders of merit from the standpoint of resistance to electrical, chemical, environmental and mechanical stresses. SR, for example, is a hydrophobicity transfer material (HTM). This means that it not only exhibits intrinsic hydrophobicity but also the unique ability to restore hydrophobicity at the surface with low ‘recovery time’ should hydrophobicity be temporarily lost due to service conditions such as heavy wetting. It is mainly because of this advantage that SR has prevailed over other polymers and indeed has become the de facto ‘standard’ for most HV applications in both AC and DC – especially whenever enhanced pollution performance is demanded. Field experience with this family of polymers has generally been positive for both line and substation applications, thereby reinforcing the strong market preference.
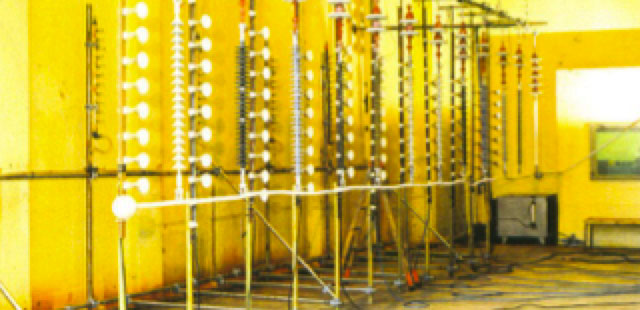
CLICK TO ENLARGE
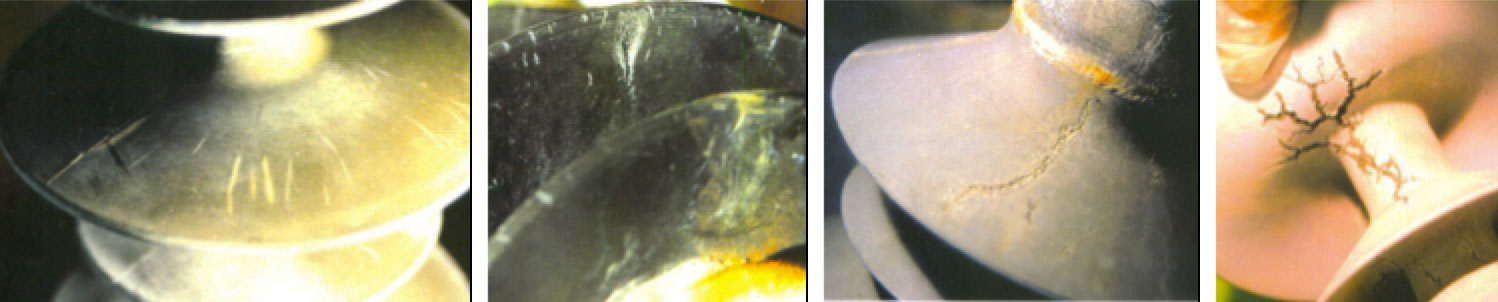
CLICK TO ENLARGE
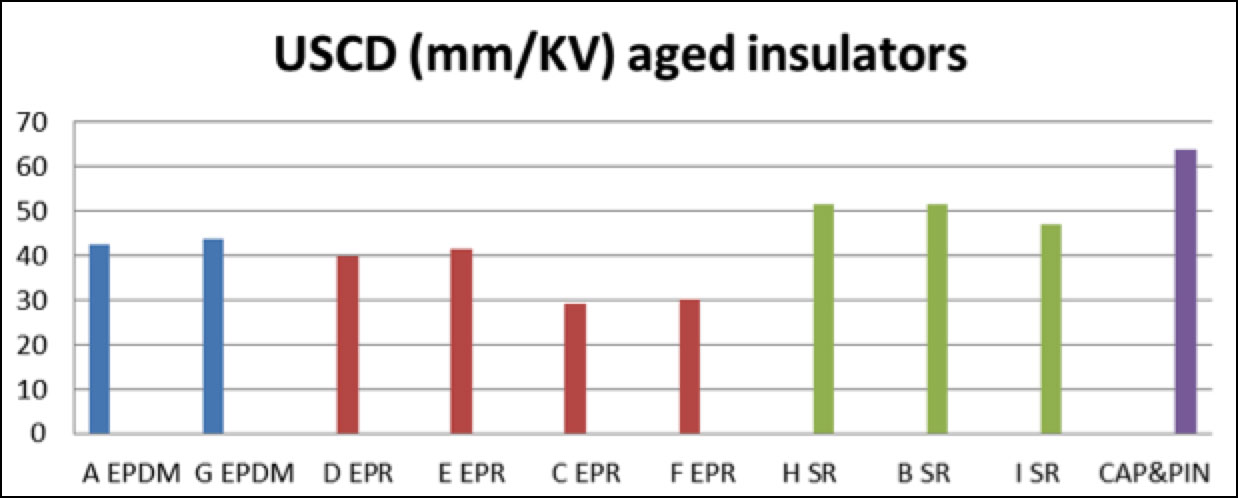
CLICK TO ENLARGE
At the same time, it is important to point out that experience suggests that SR insulation may not always meet user expectations in extremely harsh service environments (e.g. those having high soluble as well as non-soluble deposits on insulators and with frequent wetting by fog). Under such challenging conditions, hydrophobicity recovery may not be fast enough, effectively nullifying the benefit. This behaviour was confirmed in recent years by severe (perhaps overly severe) laboratory ageing tests where different insulator designs and materials were exposed for thousands of hours to different stress conditions including salt fog, rain, clean fog, drying periods and UV (see Fig. 1). Fig. 2 shows examples of degradation experienced under DC. To get an indication of insulator condition after ageing, pollution withstand was determined using the ‘quick flashover’ method at a salinity of 80 kg/m3. Fig. 3 shows a comparison of insulators in terms of unified specific creepage distance (USCD) required under DC. Under such simulated extreme conditions, it was found that the performance of EPDM and EPR insulators was actually superior to that of SR. This was probably due to the fact that resistance to tracking and erosion by any polymeric material is more important than hydrophobicity transfer in these types of extreme environments.
Finally, there are situations where adopting composite insulators has been dictated not by superior pollution performance but rather by other considerations, such as improved safety. In fact, this has increasingly been the case for housings for AC substation applications in relatively clean environments, where electrical design is dominated more by switching impulse performance than by pollution. While it is possible that silicone insulators also offer the best solution in this case, technical and economic comparison of the ‘standard SR approach’ with alternative polymeric options not mentioned above should not be automatically discarded. Too much standardization limits innovation.