Tracking and erosion resistance is one of the key properties of polymeric materials for high voltage outdoor applications and was standardized decades ago for AC stress using the inclined plane test (IPT), as per IEC 60587.
Collecting experience with DC stress began more than 20 years ago and one result common to all such investigations has been: if identical test parameters for both AC and DC are chosen, DC stress leads to more intense tracking and erosion than at AC. This is especially the case if positive polarity is chosen for testing.
This higher severity can result in too harsh testing of investigated materials and their disqualification, in a non-differentiable manner, which often contrasts with actual service experience.
Therefore, various modifications of test parameters such as reduction in test voltage or flow rate have been conducted to decrease test severity and evaluate and differentiate between materials. At present, a few national standards are available for HVDC tracking and erosion tests using the IPT set-up but no international IEC standard is yet available.
This edited contribution to INMR by C. Baer, J. Lambrecht and K. Hindelang of Wacker Chemie in Germany reports on recent research to compare erosion resistance of different silicone rubber materials under DC stress.
Recent work within CIGRE WG D1.72 has concentrated on basic investigations with the IPT to develop a standardizable test method in IEC with respect to representativeness, repeatability, reproducibility and cost efficiency.
The general aim of the IPT is an accelerated testing of tracking and erosion resistance by continuous discharge activity. Under AC, test parameters, i.e. voltage, flow rate and series resistance, are set such that continuous discharge activity is achieved. However such parameter studies have been missing for DC application. As such, parameters for DC set-up were defined during pre-investigation such that continuous discharge activity is achieved and overly severe test conditions are prevented.
In the case of severe erosion, formation of degradation products can influence test conditions by interrupting continuous discharge activity. This is not desirable.
Two round robin tests with constant voltage (one at 4.5 kV DC and the other at 3.5 kV DC), both at positive polarity and using a single silicone elastomer formulation were conducted at 7 test laboratories. What was observed is that test results between different laboratories and also within each test series showed a wide spread in results, e.g. from passing the test with only slight erosion to failing by ‘digging’ erosion and hole formation. As such, statistical evaluation showed a mixed distribution as illustrated in Fig. 1 for maximum erosion depth.
Further analysis showed that the degradation process is non-linear over time and accelerates once digging erosion is initiated. Therefore, further tests were conducted with reduced test durations of 2h and 4h (see Fig. 2) and most specimens failed between 2h and 4h of test time. Given this, testing with application of constant voltage was found unsuitable for any international material testing standard.
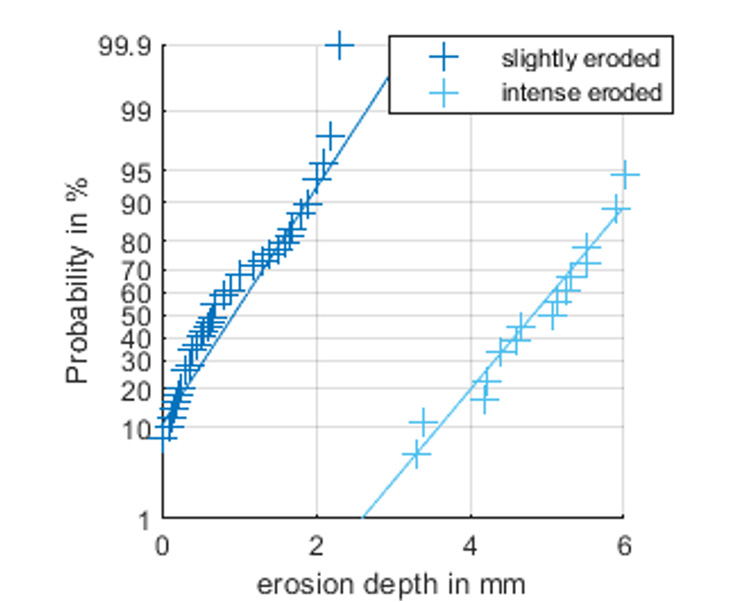
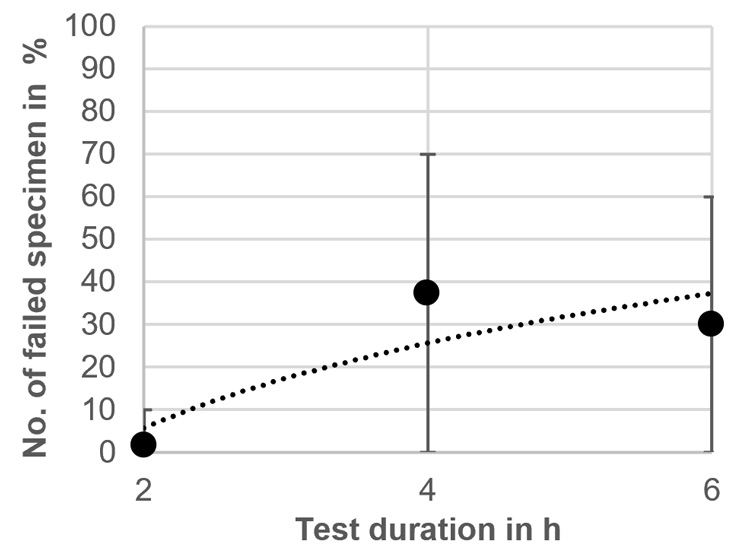
To reduce scatter and avoid a mixed distribution in test results, a stepwise increase in test severity was thought more advantageous to evaluate and rank different materials under DC voltage stress. The goal of this contribution is evaluation of the DC tracking and erosion resistance of different silicone elastomer formulations using a stepwise increase in test voltage. Results are then compared with investigations conducted under AC stress, according to IEC 60587. For a stepwise increase of test voltage, a utility step-test specification with up to seven voltage levels has been taken. Moreover, a simplified method with 3 voltage levels only has been applied.
Test Methods & Procedures
Additional tests under DC voltage of positive and negative polarity involving different silicone elastomers were conducted according to the following parameters:
• Test setup and test parameters according to IEC 60587 (see Fig. 3);
• Flow rate of 0.3 ml/min for any voltage level
and procedures:
• Stepwise increase in test voltage in seven steps, starting from 2.15 kV DC+ and increasing every 60 min for 0.25 kV until 420 min of test duration (10 samples per material formulation);
• Stepwise increase in test voltage in seven steps, starting from 2.90 kV DC- and increasing every 60 min for 0.25 kV until 420 min of test duration (10 samples per material formulation);
• Stepwise increase in test voltage in three steps, starting from 2.45 kV DC+ and increasing every 120 min for 0.5 kV until 360 min of test duration (5 samples per material formulation).
As reference, an AC test was carried out with constant voltage application at 4.5 kV for a maximum of 360 min with parameter selection according to IEC 60587. This was done for the material formulations chosen as well (i.e. 5 specimens per material formulation).
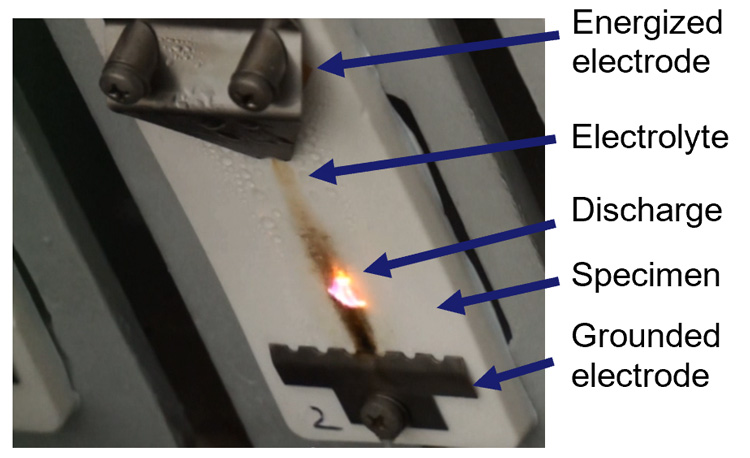
As reference, an AC test was carried out with constant voltage application at 4.5 kV for a maximum of 360 min with parameter selection according to IEC 60587. This was done for the material formulations chosen as well (i.e. 5 specimens per material formulation).
Table 1 shows the different silicone elastomer formulations tested (VMQ, vinyl-methyl silicone elastomer).
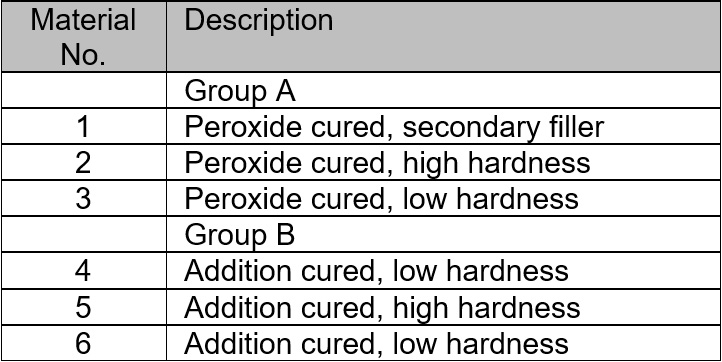
Materials were selected such that erosion resistance weakens within Groups A and B, i.e. from material VMQ 1 towards VMQ 3 and VMQ 4 towards VMQ 6.
VMQ 1 and VMQ 4 are established material formulations with good resistance to tracking and erosion and positive long-term service experience. VMQ 2 and VMQ 3 as well as VMQ 5 and VMQ 6 are modified variants, respectively with high and low hardness of peroxide addition curing systems, and were developed for these investigations only.
A voltage level is considered ‘passed’ if the leakage current does not exceed 60 mA for 2s, there is no deep erosion with formation of a hole and the samples do not start to burn.
For better comparison of the materials being tested, time to failure, mass loss and maximum erosion depth were measured. Since silicone elastomers do not show typical tracking characteristics but rather only erosion, it was decided not to evaluate their track length.
Test Results for Silicone Elastomer Formulations Investigated
Reference results (4.5 kV AC stress acc. to IEC 60587) and results of all DC step tests are presented and discussed:
• time to failure (see Fig. 4);
• mass loss (see Fig. 5);
• maximum erosion depth (see Fig. 6).
Evaluation of AC Test Results
As expected, at 4.5 kV AC, VMQ 1 and VMQ 4 passed the tracking and erosion test by showing low average values of mass loss and only moderate values for maximum erosion depth. These materials are classified as tracking and erosion resistant with class 1A4,5.
In contrast to these results, the other material formulations did not pass the 4.5 kV AC tracking and erosion test and failed (at least for one sample) by exceeding the leakage current criterion with a switch-off before the full test duration of 360 min was reached. Additionally, VMQ 5 and VMQ 6 show severe erosion with high mass loss and formation of a hole.
Evaluation of DC Test Results
Under DC voltage, most of the materials showed more severe erosion for the test procedures selected compared to tests performed under AC voltage.
Comparing the three different DC test procedures, that with 7 different voltage levels with positive voltage resulted in the most severe erosion, followed by testing with 3 voltage levels at positive DC voltage stress. Tests conducted under negative DC showed less severe erosive degradation than tests at positive polarity. This is consistent with previous investigations.
The test procedure with 3 voltage steps at positive polarity was conducted in an attempt to reduce the required effort, test severity and spread of results. This was achieved for the majority of material versions tested and allowed for better differentiability between these materials.
Although the silicone elastomer formulations did not show exactly the same performance and ranking compared to AC voltage, both VMQ 1 and VMQ 4 showed highest time to failure, lowest mass loss and lowest maximum erosion depth within their material groups, especially with respect to the DC step test with 3 steps.
Material formulations VMQ 5 and VMQ 6 showed quite different performance at AC and DC stresses. While both materials performed poorly under AC stress with respect to mass loss and maximum erosion depth, they performed better under DC stress (also compared to VMQ 2 and VMQ 3). The root cause for this is not yet clear and needs further investigation to avoid unsuitable selection of material.
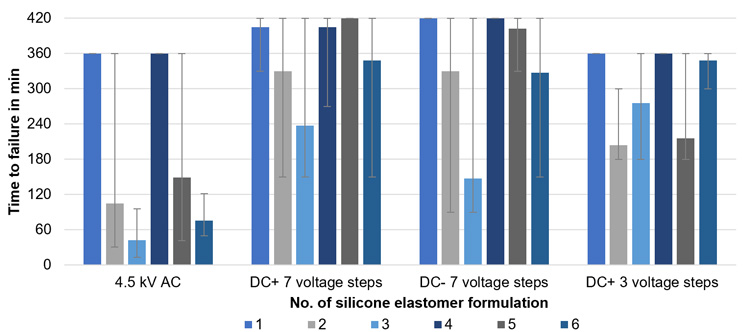
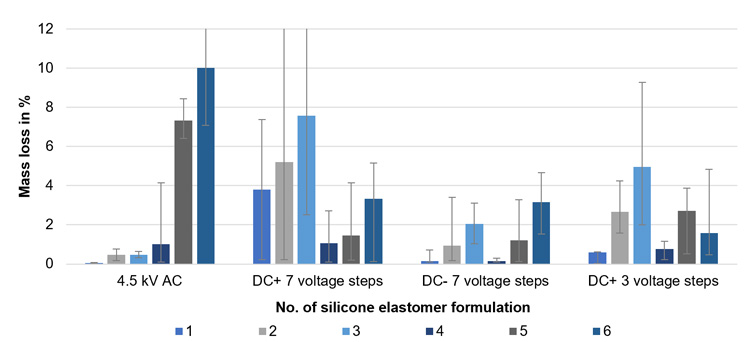
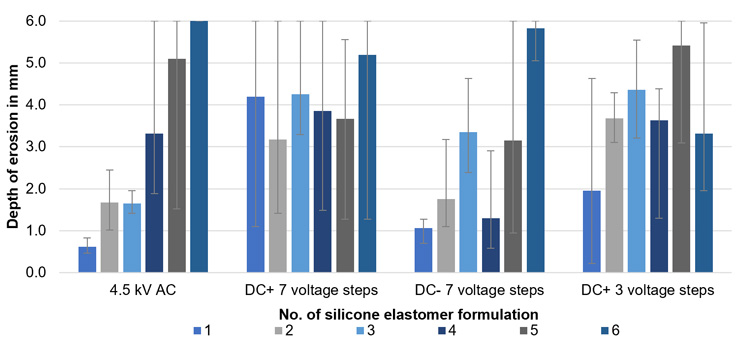
Summary & Conclusions
Based on this investigation, and in line with previous investigations, a separate DC tracking and erosion test is seen as required to properly select and rank materials for high voltage DC outdoor applications. This is because test results conducted under AC stress cannot be transferred to DC applications.
As observed through recent CIGRE WG D1.72 activity (with high scatter of test results within one test series and also between different laboratories), the current approach with constant voltage application is not sufficient to satisfy the requirements needed to become a standardized IEC test method.
A potential solution lies in application of a stepwise voltage increase, which also increases test severity and reduces high test scatter. This contribution presented 3 different test procedures for stepwise increase in DC test voltage of both polarities. While testing with 7 voltage levels at positive DC voltage resulted in the most severe erosion, much less severe erosion was observed for the negative polarity. From this perspective, it is concluded that testing with negative polarity may not be necessary and that testing only at positive polarity may be sufficient. This is consistent with past investigations.
In addition, it could be shown that testing with 3 DC voltage levels and positive polarity reduces testing effort, test severity and scatter of test results. It may therefore better allow for differentiation and ranking between the material formulations being investigated.
Further work based on stepwise increase in DC test voltage, as presented here, is planned in a future CIGRE D1 WG. This will include international round robin testing and eventually preparing a recommendation for an internationally standardized test method in IEC.
References
[1] IEC TR 62039:2021 – Selection guide for polymeric materials for outdoor use under HV stress, March 2007.
[2] IEC 60587:2007 – Electrical insulating materials used under severe ambient conditions – Test methods for evaluating resistance to tracking and erosion, Mai 2007.
[3] G. P. Bruce, S. M. Rowland, A. Krivda: “Performance of Silicone Rubber in DC Inclined Plane Tracking Tests”, IEEE TDEI, Vol. 17, No. 2, pp. 521-532, 2010.
[4] C. Bär, R. Cervinka et al.: “On a Comparative Evaluation of the Retention of the Hydrophobicity and the Tracking Resistance of Silicone Elastomers under AC and DC Stresses”, 17th International Symposium on High Voltage Engineering, Hannover, 22nd -26th of Au-gust 2011.
[5] R. A. Ghunem, S.H. Jayaram, E.A. Cherney, “Inclined Plane Initial Tracking Voltage for AC, +DC and –DC”, Conf. Record of the 2012 IEEE Int’l. Sympos. Electr. Insul. (ISEI), pp. 459-463, 2012.
[6] J. V. Vas, B. Venkatesulu, M. J. Thomas: “Tracking and Erosion of Silicone Rubber Nanocomposites under DC Voltages of both Polarities”, IEEE TDEI, Vol. 19, No. 1, pp. 91-98, 2012.
[7] R. A. Ghunem, S. H. Jayaram and E. A. Cherney, “Erosion of Silicone Rubber Composites in the AC and DC Inclined Plane Tests”, IEEE Trans. Dielectr. Electr. Insul., Vol. 20, No. 1, pp. 229- 236, 2013.
[8] CIGRE WG D 1.27, TB 611: “Feasibility Study for a DC Tracking and Erosion Test“, 2015.
[9] DLT 810-2002 – Technical specification for ± 500 kV D.C long rod composite insulators, 2002-09-01.
[10] “IEEE Guide for DC Inclined Plane Tracking and Erosion Test for Outdoor Insulation Applications,” in IEEE Std 2652-2021, vol., no., pp.1-22, 7th of October 2021
[11] S. Kuehnel, S. Kornhuber, J. Lambrecht, K. Hindelang: Evaluation of the Tracking and Erosion Resistance at DC-Stress using the Example of Silicone Elastomers, 8th Conference on Silicone Insulation, Burghausen, Germany, 2022.