Ongoing developments in cable accessories have been influenced mainly by the continuing technological shift from paper to polymeric-insulated cables. But the impact of this shift is not the same for AC as for DC. At the present, the large majority of power transmission and distribution is still handled by AC systems due to comparative ease of transformation at different voltages. However, for submarine as well as lengthy land cables, HVDC systems offer important advantages including higher capacity, reduced losses, no need for capacitive charging currents and better control over load flow as well as reactive power transmission.
Looking at AC, cable accessory designs and requirements have depended primarily on whether they were to be used for low, medium or high voltage applications. For example, when it comes to LV cables, the wholesale changeover from paper to PVC or PE-insulated cables took place 50 to 60 years ago and there has been little new to report. Accessories here employ mainly heat shrink technology for straight joints and cast resin technology for branch joints.
At the MV level, the ascendancy of polymeric cable technology has taken place over a more recent time frame. XLPE and EPR cables began to be widely installed before the 1980s though in some countries this process started later. One especially notable feature at this voltage level has been the huge diversity of alternative types of polymeric cable. While for the first 80 years only four basic paper cable constructions seemed sufficient (i.e. belted, metalized paper screened, three-core single lead sheath and single-core), once polymeric MV cables began to appear on the market at least a 100 different types of construction soon came to be offered. Indeed, the numbers were so large that efforts were mounted with the goal of dramatically streamlining this high number.
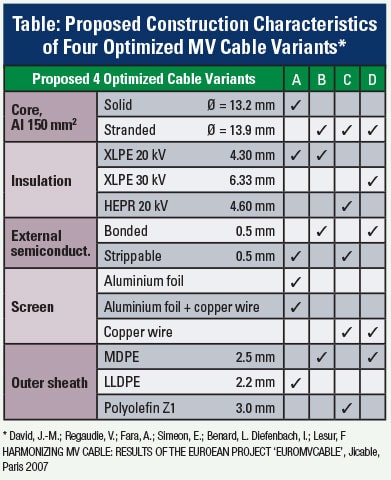
After analysis of the many available MV cable designs, four optimized cable construction variants were proposed. Unfortunately, response to this proposal across different countries was not uniformly positive. As a result, a large number of different cable types and accessories are still being applied over this voltage range, whether using heat shrink, slip-on or cold shrink technologies.
When it comes to HV, XLPE cables are presently used up to as high as 500 kV and EPR cables up to 150 kV and together these are increasingly replacing older paper technology. Comparing two alternative 110 kV cable constructions, for example, the cost-savings offered by XLPE become readily apparent. Accessories for HV polymeric cables are based mainly on silicone because of its hydrophobic properties when applied to terminations and its softness and gas penetration rate when used in manufacture of joints.
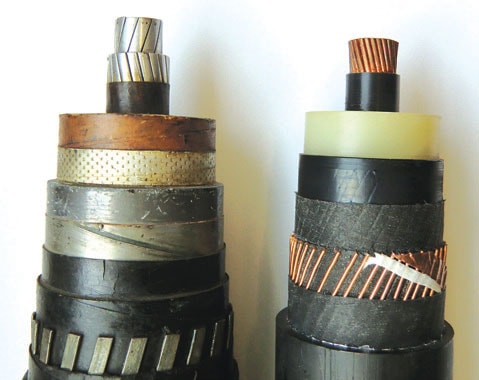
CLICK TO ENLARGE
In the case of DC cable systems, the HV range is really the only application area and here the major problem for XLPE cables is formation of space charges in their insulation material. This can then lead to eventual breakdown due to modification in electric field distribution, especially in the case of traditional line-commutated converters (LCC) that change load flow by reversing voltage polarity. This remains the reason why paper-insulated cables still offer performance advantages for HVDC. While a changeover to maintenance free and more environmentally friendly polymeric cables is clearly ongoing, this will apply mainly for DC systems that use modern voltage source converters (VSC). Here, change of load flow is accomplished rather by inversion of current direction without changing voltage polarity and this results in much lower stress on XLPE type cables. Nevertheless, the space charge problem remains an important element in design of DC XLPE cable accessories and this is leading to application of EPDM for joints in place of the marked preference for silicone in most AC applications.
So, while classic paper cable is being phased-out with a corresponding influence on the types of accessories needed, specialized applications for this technology remain. The most important of these are line-commutated converters where currently available XLPE cables are still not able to offer superior performance.
Prof. Klaus-Dieter Haim (from 2012)
University of Applied Sciences Zittau-Görlitz, Germany