Composite insulators have become common on overhead lines as well as at substations due to application advantages and their attractive acquisition costs. However, the nature of polymeric housing materials is that premature ageing can be a problem if insulators are incorrectly selected or not properly designed and manufactured. Similarly, composite insulators can be attacked by biological growths such as algae and fungi and in manners from minor to severe.
Theoretically, this can influence both pollution performance (in the short run) and ageing characteristics (in the long run). Another concern is whether the housing material can be consumed as a food source by the biological growth. It could also be that fungi penetrate into the insulator, even without consuming the base material.
The issue of dealing with biological growths on insulators has not yet been thoroughly resolved and a critical review of what is currently known is beneficial. At the same time, there are increasing reports of such growths – probably because more and more composite insulators have been installed in clean service areas as opposed to their historical driver, i.e. only polluted environments. Biological growths have been observed in hot and humid environments and also in temperate and cold environments and have been found on line insulators, cable terminations, bushings, arresters, breakers and RTV-coated station post porcelain insulators. However, colonization by biological growths is not something inherent only to composite insulators and has been observed as well on glass and porcelain insulators. There are also indications that different types of biological growths can be observed on different composite materials, e.g. HTV versus LSR silicone rubber material. Accumulated knowledge on biological growths today is limited. No IEC recommendations are available and only CIGRE Technical Brochure (TB) N. 455 provides a statement: “According to present knowledge, a biological growth is located only on the surface of the silicone rubber and in the worst cases reduces the hydrophobicity on the part of the insulator (usually the shaded part). The risk for flashover due to the biological growth is rather low because in order to lead to flashover, the resistance of the pollution layer should be relatively low. However, biological growth normally occurs in relatively clean areas leading to a situation where either insulator will be hydrophilic, but clean, i.e. with high resistance, or it will be contaminated but free of biological growth and therefore be hydrophobic (due to recovery of hydrophobicity) with high resistance.” This conclusion is echoed by recommendations in the EPRI Guide: “No actions required, long-term effects should be studied”
This past contribution to INMR by Igor Gutman, Andreas Dernfalk and Michail Yarmarkin offered an overview of issues related to biological growths.
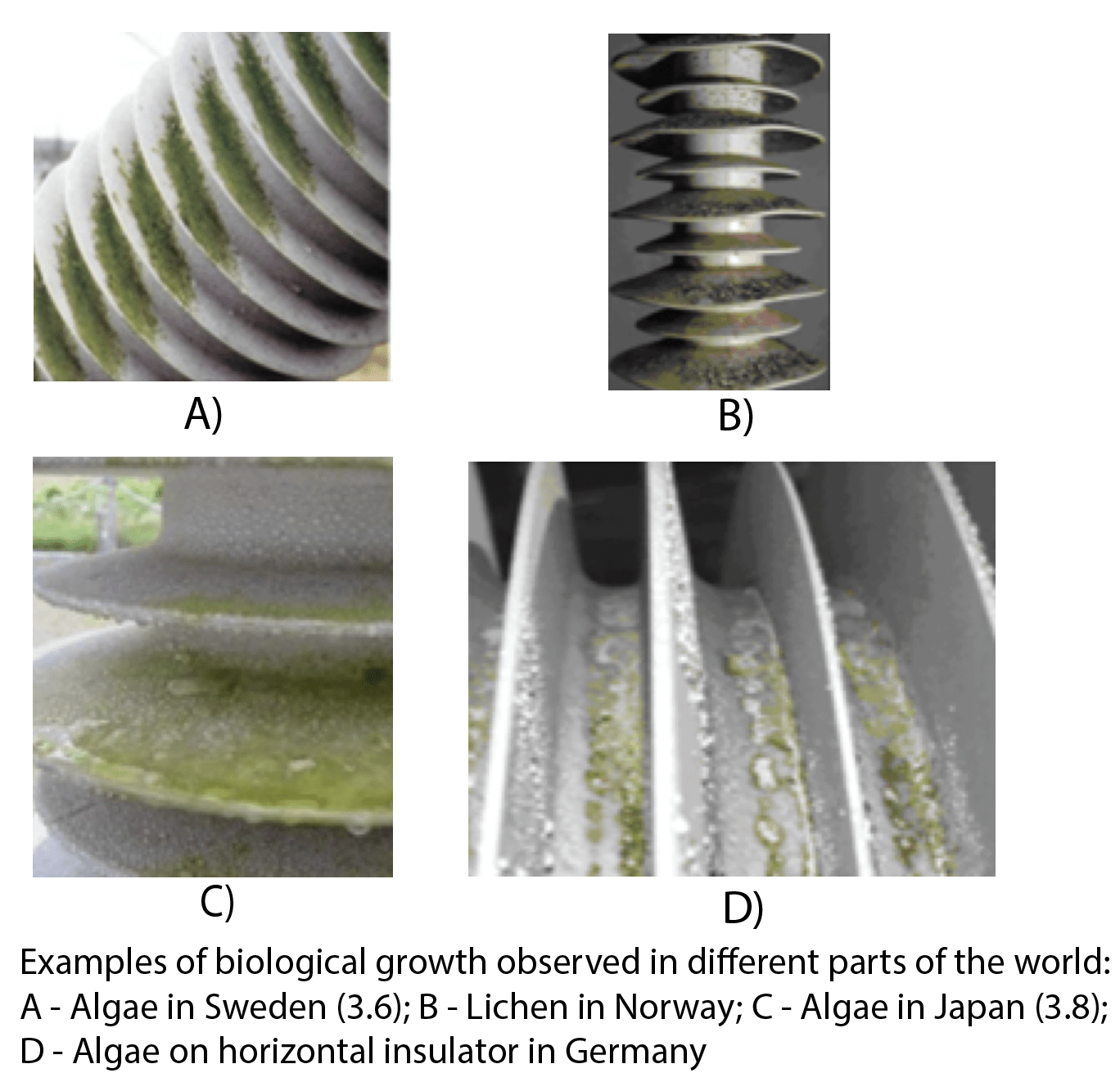
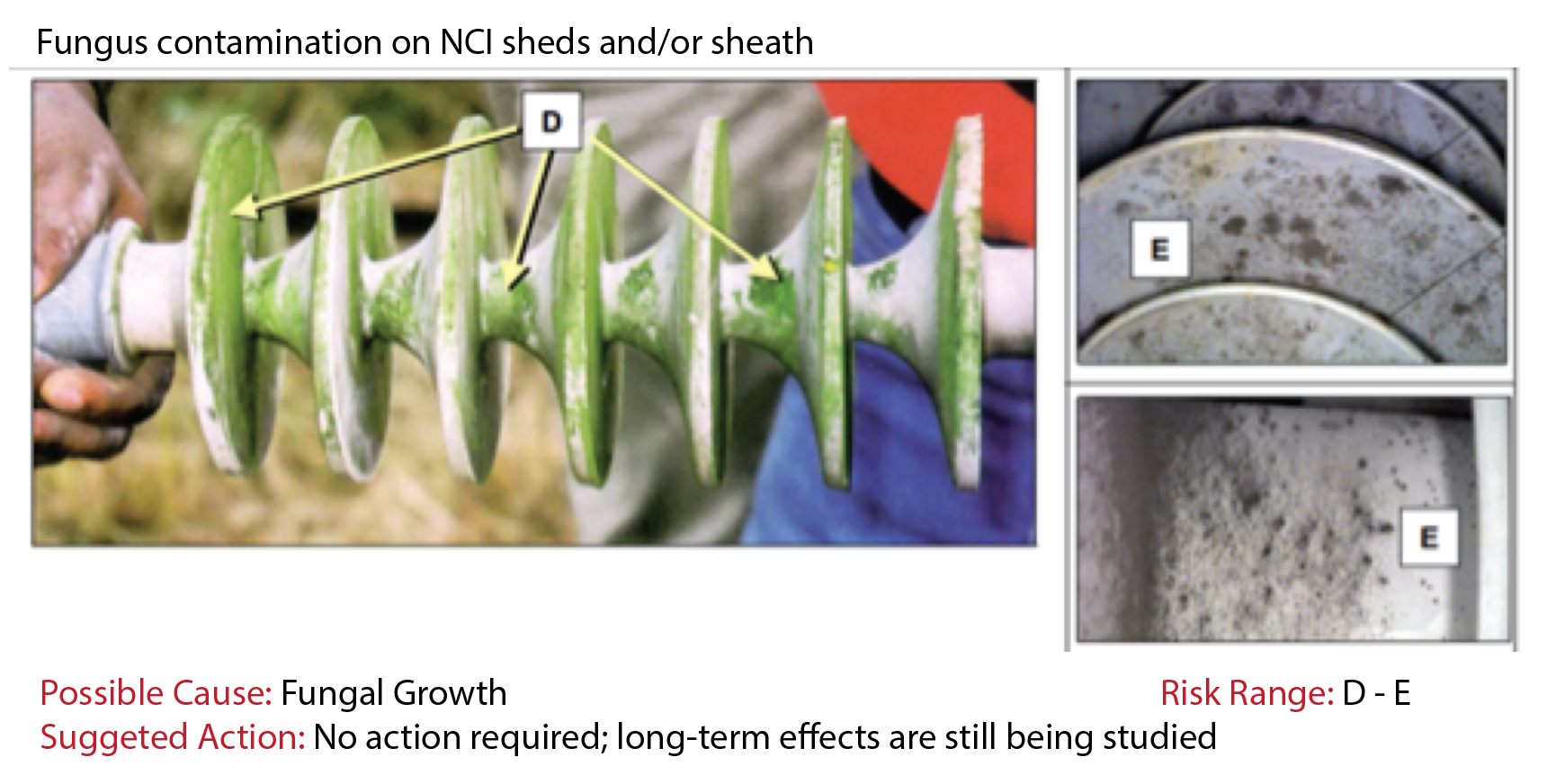
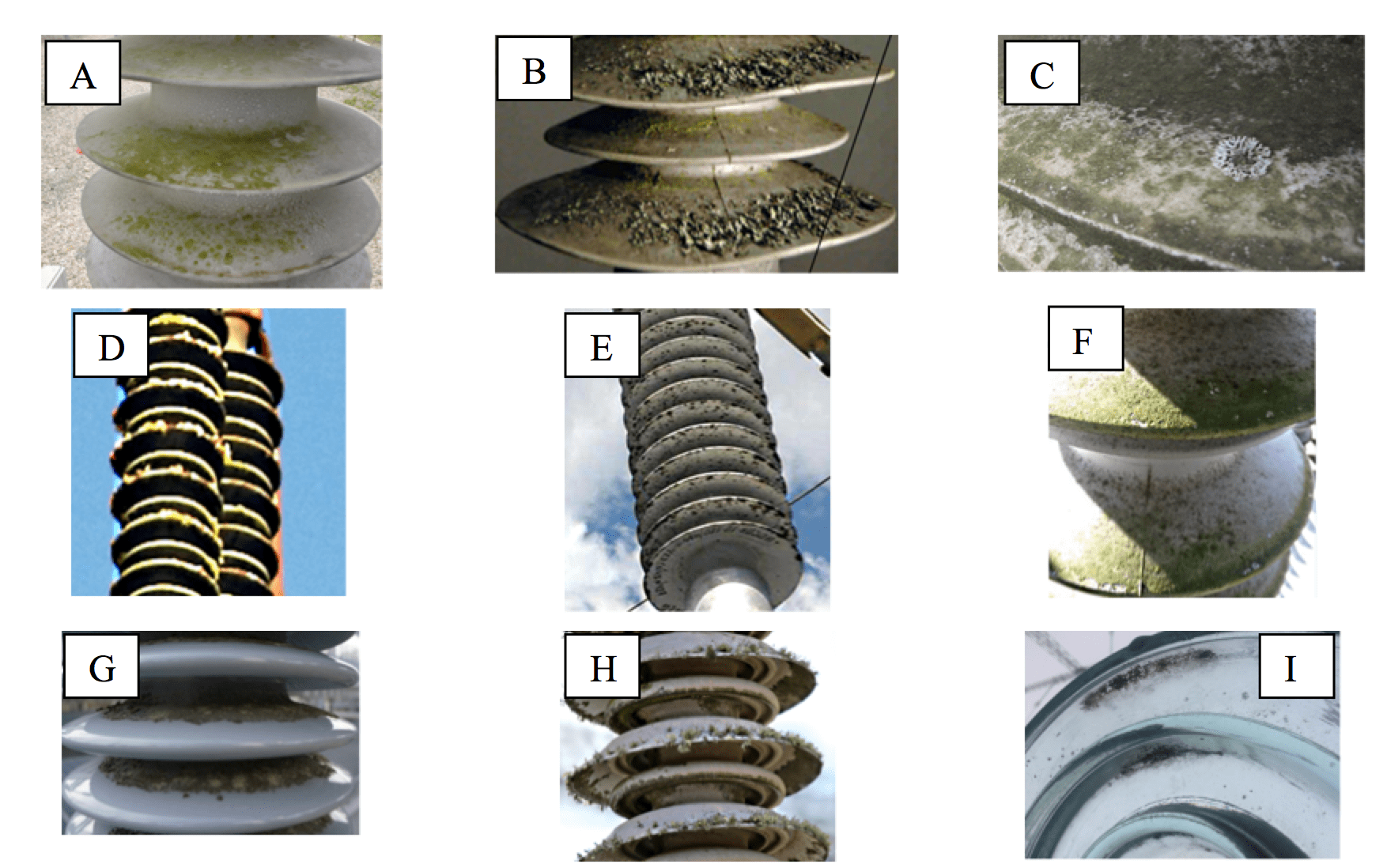
Types of Biological Growths
Biological growths are microorganisms that colonize polymeric materials by attaching to the surface and forming a biofilm embedded in a hydrated matrix of extracellular substances. The water content is 80-95% and cells comprise only a fraction of biofilm that could not have formed without presence of the microorganisms. The biofilm provides protection against desiccation, nutrients from the bulk water, protection against toxic substances and facilitated reproduction. In the literature, biofilms or biological/organic growths are often referred to as ‘mold’ or ‘moss’ when it is not clear to which group they belong. Here, the term ‘biological growth’ is a general name connoting an organic growth on insulators – in line with the definition in CIGRE TB 455. Reports of biological growths in service reveal three different types:
Algae
These can be seen as a simple plant, producing its own food from carbon dioxide and water by photosynthesis. They also need some mineral nutrients taken from the environment and can be found everywhere – in sea and fresh water, on rocks and in soil. They are spread by wind, water and animal migration and multiply under certain climatic conditions such as favourable temperature, humidity and solar radiation.
Fungi
Fungi are multicellular organisms composed of long, thread-like filaments. The body of the organism is called mycelium and they multiply by sending out spores. Fungi cannot produce their food by photosynthesis and instead absorb nutrients from the surrounding environment.
Lichen
These are a special plant group consisting of fungi and algae that live in symbiosis and adhere to rocks, stones and trees but can be found as well on insulators. In this case, the algae are dispersed in the fungi mycelium. Fungi take nutrients from algae whereas algae take nothing but water from fungi.
The appearance and types of biological growths can be quite different and some of them, found on insulators, are already identified in the literature. Considering available data, biological growths are considered mainly as surface phenomena and do not penetrate into the bulk material. Nevertheless, in one particular case, penetration up to 100 m was observed and this was probably related to the high porosity of the specific silicone rubber material involved.
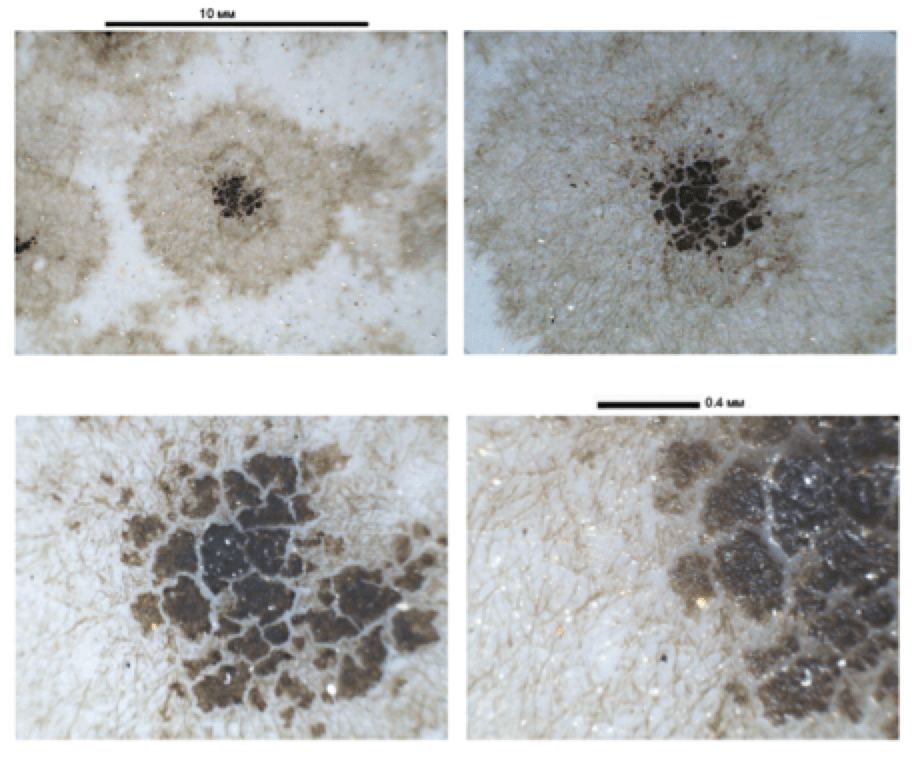
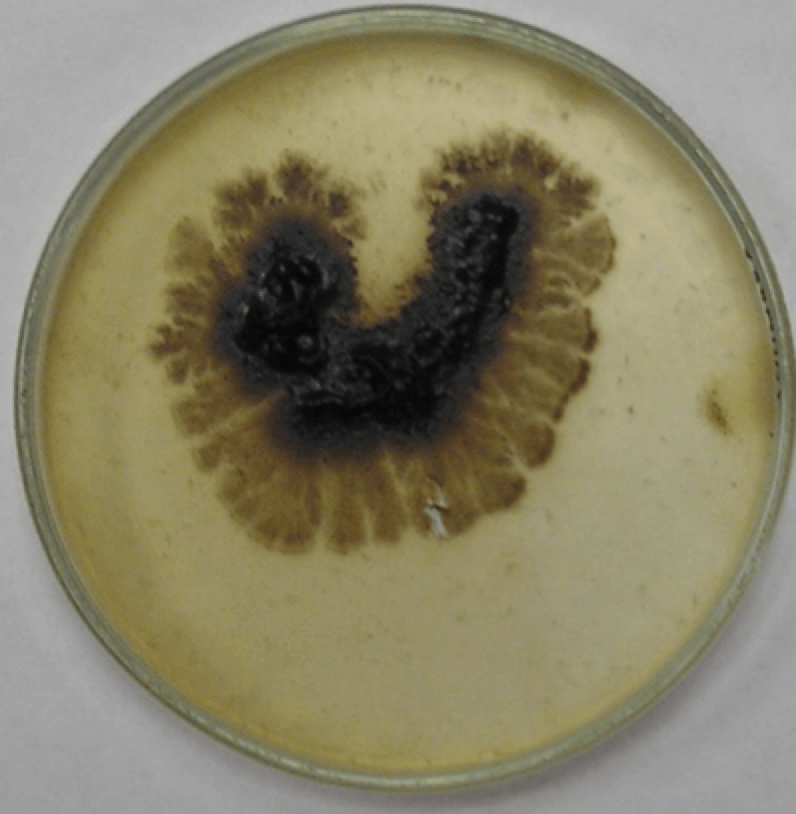
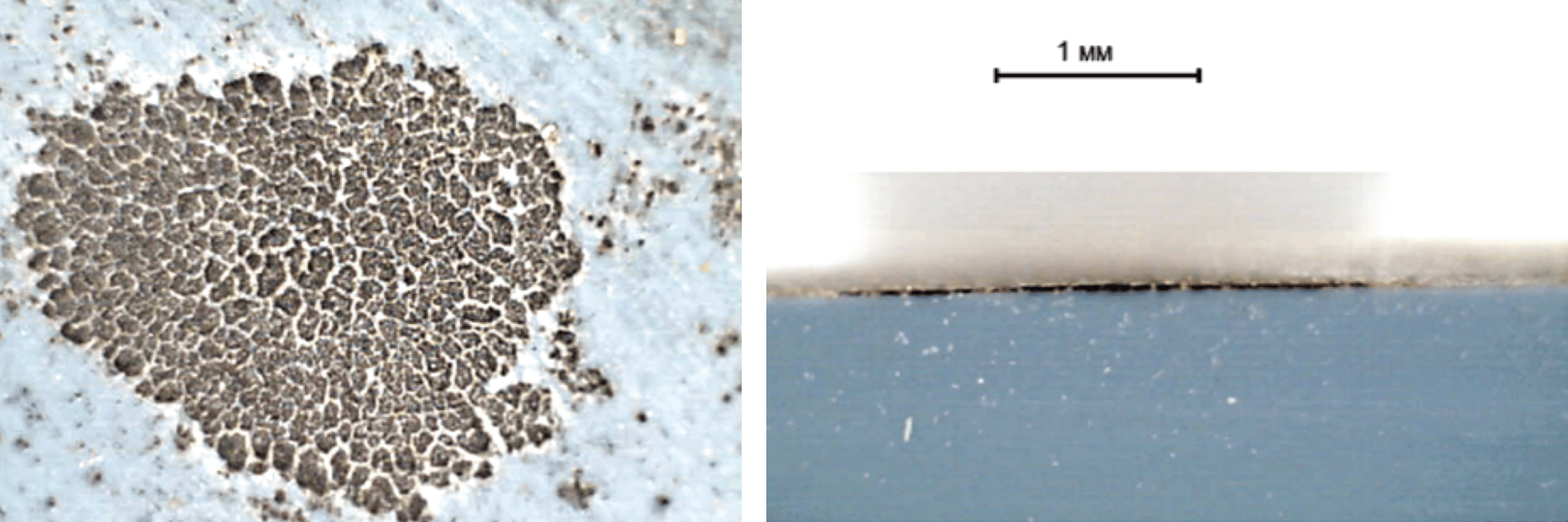
Reduction in Pollution Performance
Observations of composite insulators with biological growths in the field as well as in the laboratory show that these can partially reduce surface hydrophobicity. But this does not normally cover the entire insulator due to the fact that shaded areas are preferential for development of biological growths. Another observation is that the environmental conditions most likely to promote biological growths are clean and humid environments (both hot and moderate). There are also indications that locations mostly affected by biological growths are not near seacoasts, where direct sea spray or salt fog can adversely influence them. Rather, areas more likely to be impacted are further inland but not too distant from high humidity environments. It is also important that the area should be clean since, if there is industrial contamination present, biological growths tend not to develop. Although there have been no reports of flashovers in service due to the biological growths, one important question is how much a reduction in hydrophobicity can adversely influence short-term pollution performance of composite insulators. For example, direct comparisons were performed on polymeric-housed arresters with biological growths removed from service in Norway versus an identical new reference arrester. Upon arrival at the laboratory, it was clear that hydrophobicity had been significantly reduced on arresters removed from service (see Fig. 7 right).
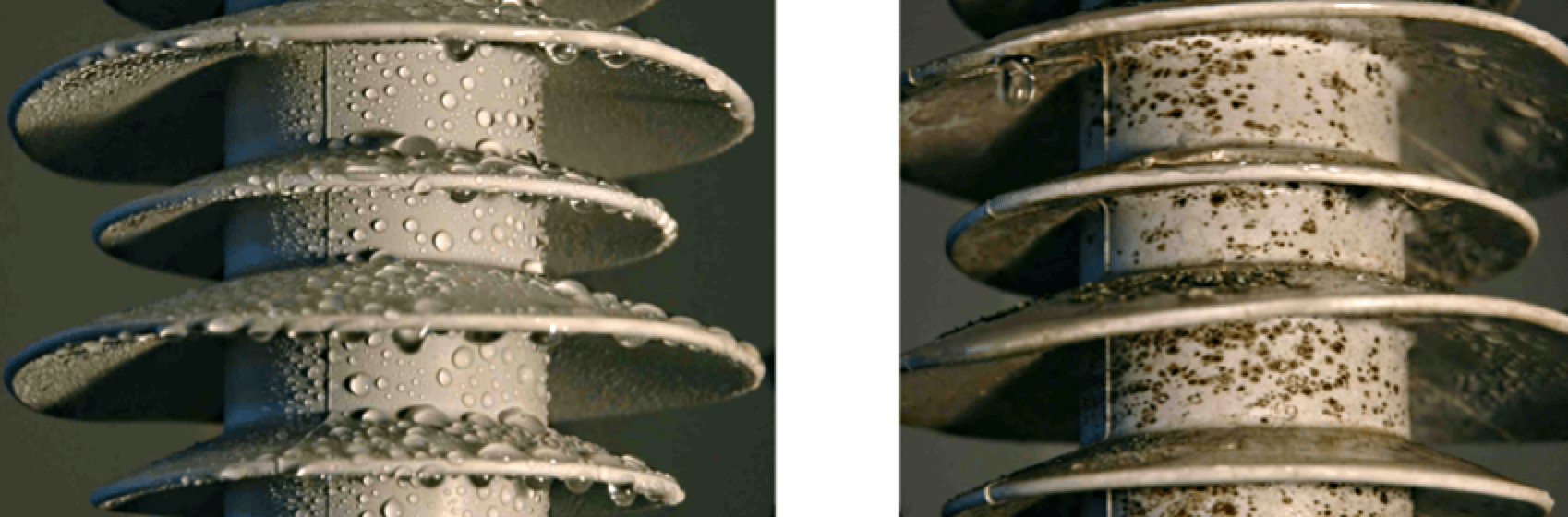
All arresters (four from service and one new reference unit) were then artificially contaminated without preliminary cleaning using the same dipping method and same contamination suspension. The ESDD/NSDD for the new arrester was 0.03/0.1 mg/cm2 (estimated as the typical pollution level in the area of interest), while for the arresters from service ESDD/NSDD were 0.04÷0.05/0.2÷0,6 mg/cm2. Thus, difference in ESDD/NSDD levels was considered as related to surface properties. It is clear that arresters with biological growth attract more pollution measured in ESDD and especially in terms of NSDD (i.e. their surface is probably much rougher than when new). The arresters were then tested in parallel at operating voltage level for 2 hours in a climatic chamber (see Fig. 8). Test results were as follows:
• Maximum currents during the test on all arresters were below 30 mA and thus far from flashover mode;
• On arresters with biological growths, maximum current during the test was slightly higher than on the new reference arrester and this confirms that the test meets the criterion of being representative. However, the difference between peak values of the reference and the average for the biologically-polluted arresters was only 5 mA.
The conclusions from this test and field observations included:
• Biological growths are located only on the surface of the silicone rubber and in the worst case just reduce hydrophobicity on part of the insulator, often in the shaded part under sheds;
• Risk for flashover due to the biological growth is negligible since it is known from field tests that, even if a silicone rubber insulator has become completely hydrophilic, its flashover voltage is still higher than for a ceramic insulator of the same profile. In the case of line insulators, the profile gives a huge advantage for composite insulators in comparison to a string of cap & pin insulators. In order to obtain insulator flashover, resistance of the pollution layer must be relatively small. However, biological growths normally develop in clean areas. Therefore, either in the worst case the insulator will be hydrophilic but clean (i.e. with high resistance) or it will be contaminated but free of biological growths and therefore partially hydrophobic and with high resistance.
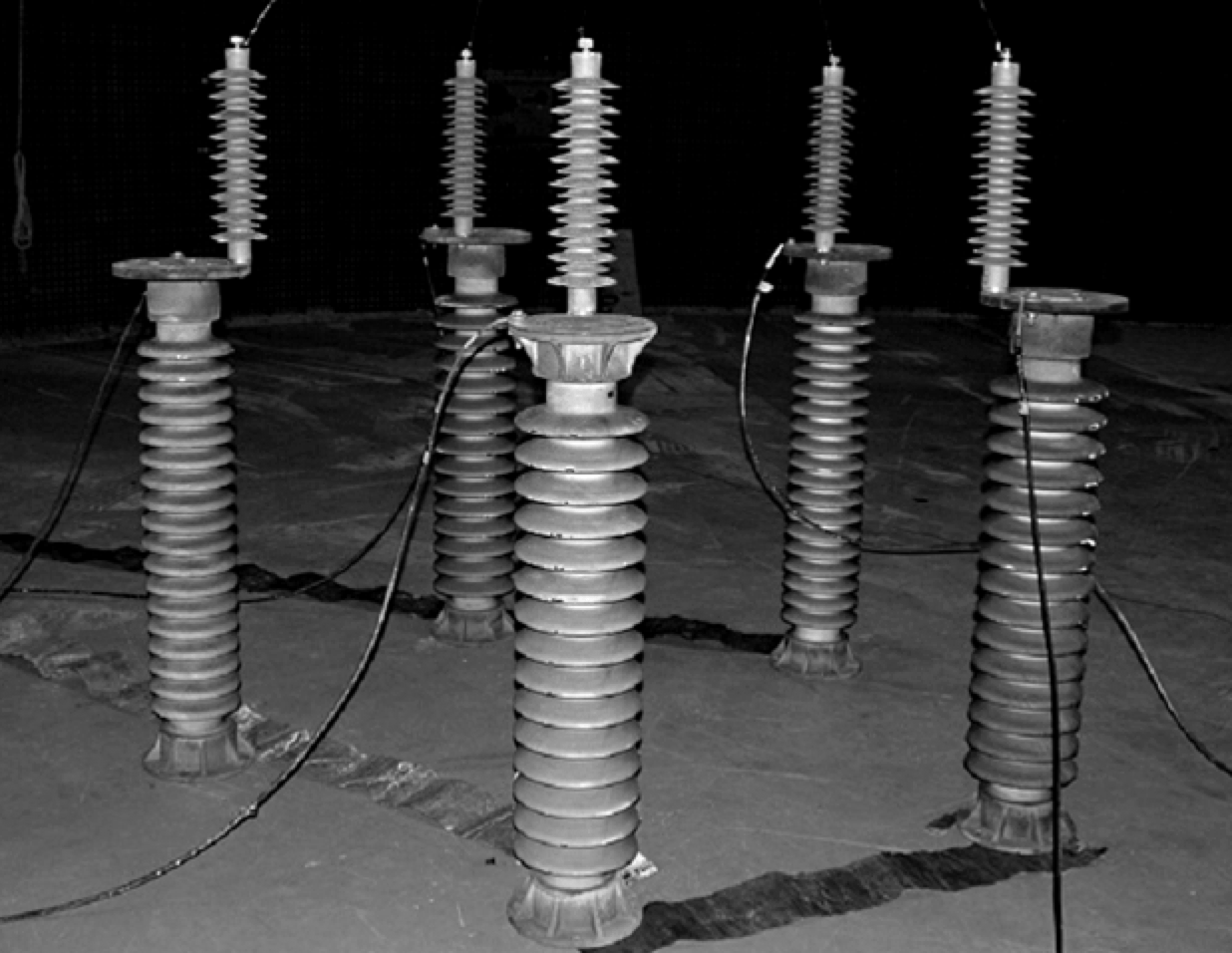
Reduction in Ageing Performance
The risk of reduction in ageing performance is also small due to the dominant form of surface biological growths that occur throughout the world. So far, for example, there have not been any reports of penetration of biological growths into the bulk polymeric material. The present level can be characterized as ‘change in surface properties’, as illustrated in Fig. 9. Thus, there is no need for quick removal of biological growths from in-service insulators and these can be relatively easily removed, as needed. Typically, this will be a management decision based mostly on appearance.
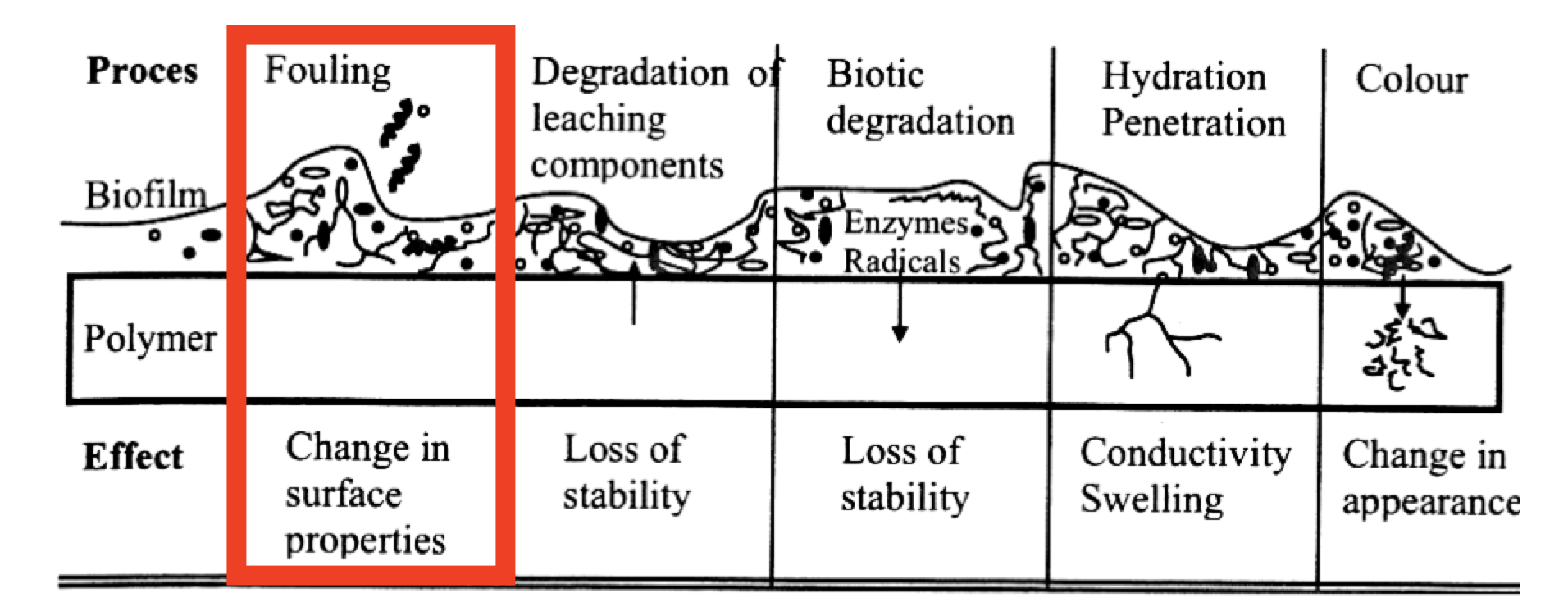
Countermeasures
Some material and insulator suppliers have started to look into the possibility of using additives called biocides that either eliminate microorganisms or inhibit their reproduction. It should be noted, however, that there are an enormous number of different microorganisms in environments surrounding insulators. Therefore a biocide has to guarantee broad-spectrum effectiveness as well as long service life, since insulators should ideally perform without maintenance for 30-50 years. To cope with such a requirement, the biocide might be present in high concentration, which in turn may influence the properties of the original material. One should also consider possible ecological restrictions. Nevertheless, experiments carried out in Russia with anti-fungal biocides were positive. Four samples of different silicone rubbers with and without filler were placed in Petri dishes filled with Czapek broth contaminated by spores of Penicillium cyclopium or Ulocladium. The samples of silicone rubber with 0.5-5% of biocides in heir mass were placed on top of the broth. Before the start of the test all samples were heated to 160°C for 15 min., which simulated the vulcanization process. This was done to ensure that the biocides would not disappear from the material after vulcanization. Development of fungi took more than 7 weeks and, after this period, the peripheral part of the Petri dishes was covered by a complete layer of fungi. However, the samples and the space around them were completely free of fungi (see Fig. 10).
Another possible idea to eliminate development of biological growths originated from laboratory salt fog tests. It is known that microorganisms can create problems during 1000-hour salt fog tracking and erosion tests. For example, analysis of the water in the supply tank, if not changed, sometimes showed high concentrations of microorganisms. At the start of the salt fog test, when leakage current levels are not high and do not yet kill microorganisms, these rapidly increase in number and create a jelly-like, highly conductive hydrophilic layer (i.e. biofilm) on the insulator surface. It has been proven experimentally that microorganisms can be eliminated by adding a certain volume of Cu2+-ions. Indeed, analysis of water with CuCl2 additive (at 12 g/m3) showed absence of microorganisms. Also, their density was lower than 10 colonies per cm2 if the samples were taken directly from the insulator surface, whereas less than 45 colonies per cm2 is defined as ‘clean’. This same idea can be used against biological growths in service, e.g. by placing a copper band at the top fitting of an insulator. Under natural rain conditions, Cu by-products would probably wash the insulator surface and kill any microorganisms.
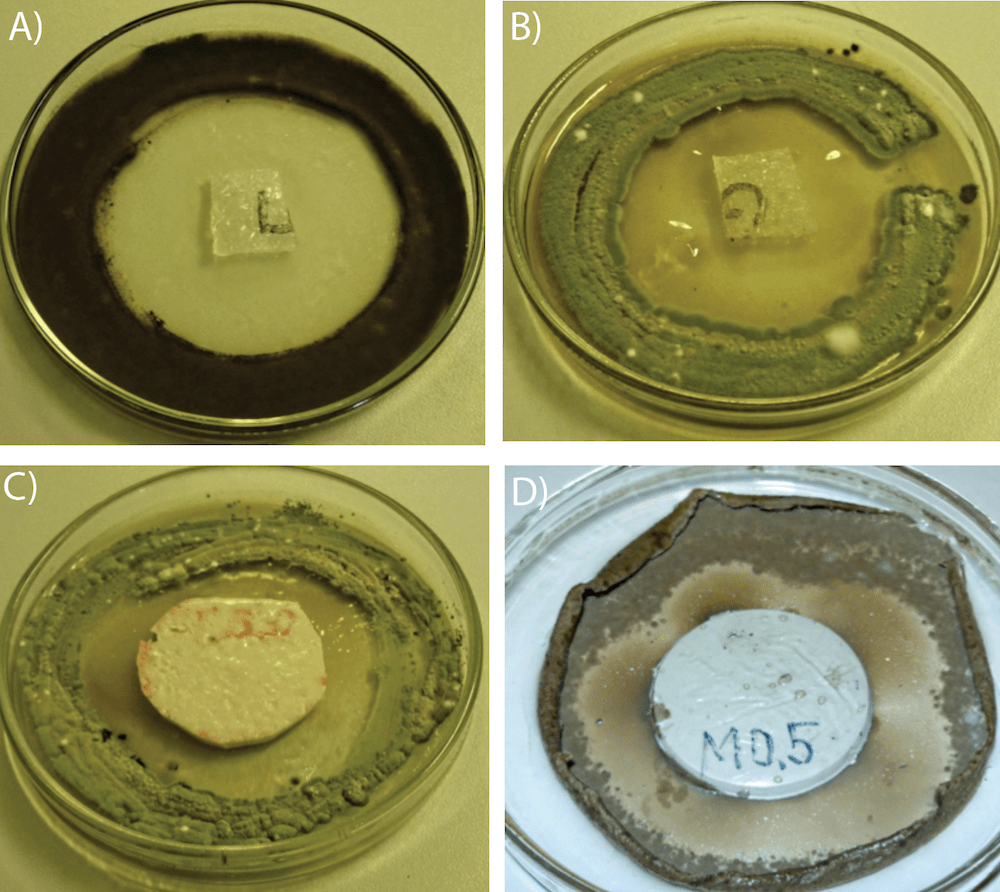
Removing Biological Growths
It is often a management decision whether or not to clean insulators with biological growths due mainly to cosmetic appearance. This is done even though electrical performance has not been reduced. A typical cleaning procedure includes two steps: one where the physical stability of the biofilm is weakened; and the next where it is removed from the surface. Carefully selected detergents are useful in the first step while flushing, brushing or similar methods are useful for the second. Washing energized insulators has to be performed using remote techniques with minimum safety distance depending on voltage level and type of cleaning method used, i.e. the same requirements as for standard live-line washing. Care should be taken when spraying silicone rubber insulators contaminated with biological growths. As in the case of clean insulators, the pressure shall be limited and not exceed that normally recommend by manufacturers. Fig. 11 shows examples after high-pressure washing. From another point of view, in one study it was considered that washing was not effective even at pressures up to 3.5 bars. This remains an open question that needs further investigation and standardization. To remove growths, some abrasive method could be considered in combination with water spraying. Again, it should be tested first to ensure it does not damage the insulator surface. Wiping the insulators seems to be an effective countermeasure given the surface characteristics of biological growths. Sources suggest wiping insulators after preliminary washing as an effective procedure. Some residue can be left after cleaning. It is also possible to use detergents containing alcohol to weaken the biofilm and then flush the surface with water. While this method may wash away some of the low molecular weight silicone species located on the surface and temporarily reduce hydrophobicity, eventually the silicone rubber will recover. Thus, how best to clean insulators with biological growths requires further investigation.
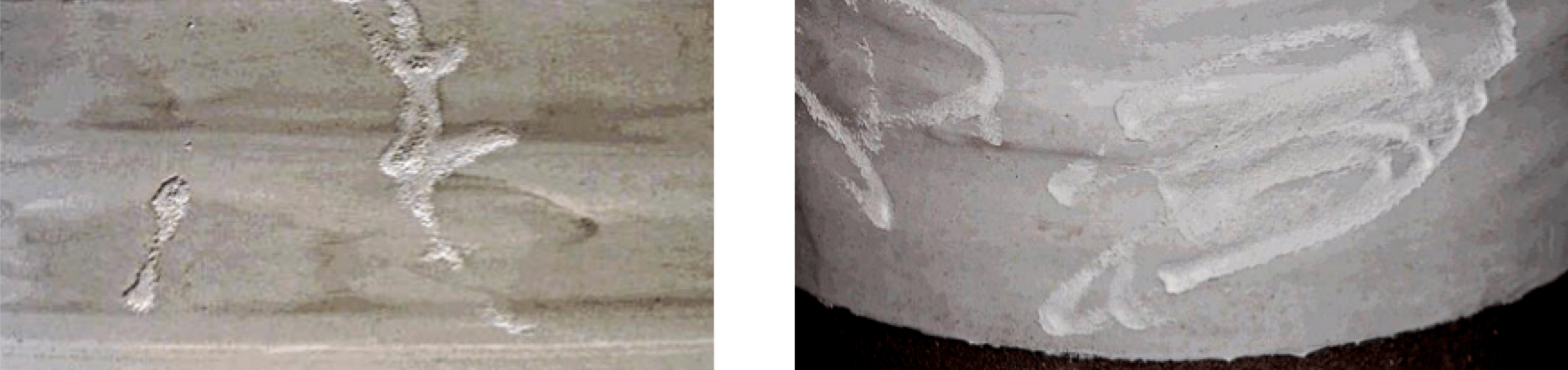
Unresolved Questions
Based on the above review, a number of questions remain to be answered:
• Can it be observed from service that biological growths are an issue for reliability of composite insulators?
• Can any difference in biological growth rate be observed for insulators without voltage versus on those already energized?
• Can a criterion be established for the critical level of biological growth that would influence electrical performance of an insulator?
• Can critical environments be defined where biological growths are most likely to develop so as to take actions to prevent such growths after installation?
• Is there any correlation between types/levels of biological growths and type of insulator material?
• Is it possible to introduce some special additives into the material or apply any other countermeasures to suppress biological growths?
• Can recommendations be made for the most efficient and cost-effective procedure to clean affected insulators?
Conclusions
Biological growth can appear on different types of insulators (composite, porcelain and glass), especially in relatively clean areas with high humidity. It can be assumed that, because of higher surface roughness and lower thermal conductivity, composite insulators might be more susceptible to such a phenomenon than ceramic insulators. Due to growing application of composite insulators in clean areas, there is an indication of larger numbers of observations of biological growths being reported from many countries. So far, no flashovers in service attributed only to biological growths have been reported. The risk for critical reduction in pollution and ageing performance of composite insulators is considered low. Based on present knowledge, biological growths are mainly a surface phenomenon and thus can be easily removed by wiping or cleaning. However, some standardized optimal procedures still need to be developed and accepted by the international community. A number of open questions still need to be resolved.