Although composite insulators today are characterized by modern and established technologies, many utilities still find it challenging to accept composite insulators the same way as they do glass and porcelain insulators. The primary reason for this is lack of reliable experience as well as sufficient documentation to ensure their long-term performance. This can be explained in part by the fact that the main IEC standards for this type of insulator are still fairly new. Another reason is that much of the service experience to date is still acquired mainly within CIGRE and not yet reached the IEC level.
Many utilities these days are using a pre-qualification process to ensure the quality of insulator suppliers. Theoretically, a well-designed composite insulator that is also properly dimensioned and quality-controlled during manufacture should have a lifespan comparable to that of porcelain or glass insulators, namely, 40-50 years. But at present no accelerated ageing test procedures are available that can predict the service life of composite insulators. Given this, documented service experience together with analysis of any possible reduction in performance across various environments are the only means to predict lifespan. Such information in turn provides the basis for creating and updating the documentation needed to ensure correct dimensioning, manufacturing and handling of composite insulators.
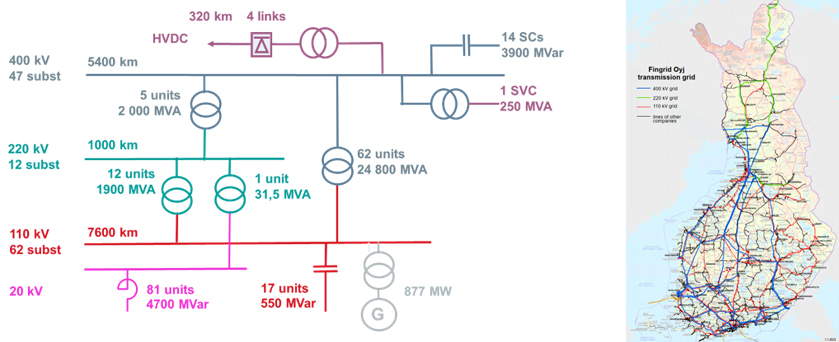
Fingrid, the TSO in Finland, has been using composite insulators at substations and on transmission lines for about 20 years and there have not been any issues as of yet. Fingrid designs its lines for at least a 50-year lifespan but actual life expectancy is closer to 70-80 years. However, like other power utilities, Fingrid has not yet received any guarantee from composite insulator manufactures for a 50-year lifespan, but rather promises for 30-40 years. Moreover, it is not clear if all requirements in the technical specifications will support the longest possible lifespan of composite insulators. Application of composite insulators in a relatively clean environment is not economical if insulators need to be replaced several times during the line’s service life.
In view of the above, a key question becomes: What kind of requirements should be included in specifications, what tests should be carried out and how can a user ensure that a manufacturer is competent to produce high quality products? Fingrid has tried to find answers to this question together with seven other European transmission companies by way of a combined R&D and benchmarking project led by the Independent Insulator Group from Sweden.
The project consisted of a survey of service experience, tests both on new and after-service composite insulators, electric field calculations and factory audits. The results of the project have been reported and some tests developed to be added to existing standards.
Attend the 2023 INMR WORLD CONGRESS to benefit from a comprehensive lecture by Mikko Jalonen, Transmission Line Maintenance Manager at Fingrid. His presentation will summarize the results achieved in this important benchmarking project and explain the value gained for TSOs and other electricity supply utilities from an asset management perspective.
[inline_ad_block]