Failure of a suspension or tension insulator is clearly something that any electric utility or insulator manufacturer wishes would never occur. However, it is unrealistic to expect that any network component can last forever without failing. It can therefore reasonably be assumed that some insulators will fail in service after a certain period of time. What both users and manufacturers hope is that this number be kept as small as possible, meaning that failure rate should be extremely low. Fortunately, most HV insulators available today have already reached such a level of reliability. But how low is this rate and is a particular failure rate meaningful taken only by itself?
To answer these questions, it is first necessary to define what insulator failure is and to examine the consequences. This 2006 contribution to INMR by the late Dr. Claude de Tourreil, who passed away that same year, remains useful reading since it provides valuable insight into this topic.
What Constitutes Failure?
A HV line insulator performs two basic functions. Mechanically, it holds the conductor at a certain distance from tower and ground. Electrically, it provides the necessary insulation to ground. Therefore, one way to define insulator failure is when either or both of these functions are no longer being fulfilled.
A less technical way to define failure is to say that an insulator has failed whenever it is removed from service because of unsatisfactory service experience. But this second definition can be misleading. For example, a past CIGRE survey of service experience with composite insulators applied this criterion to define failure. Unfortunately, this led to an unjustifiably high number of reported failures simply because some responding utilities had decided to remove all insulators of a particular design simply because a small number had already failed.
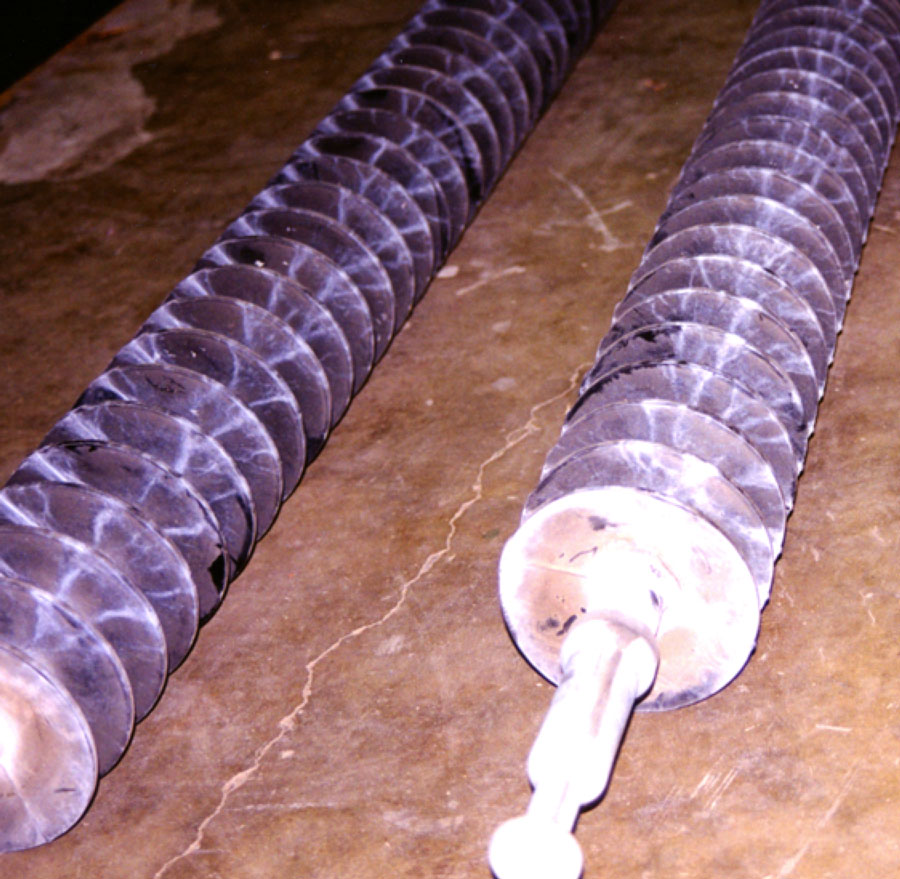
Moreover, different insulator types fail in different ways. The failure modes of toughened glass or porcelain insulators are quite different from the failure modes of composite insulators and this may have consequences on continuity of service. Because of this it is difficult to compare failure rates of different types of insulators.
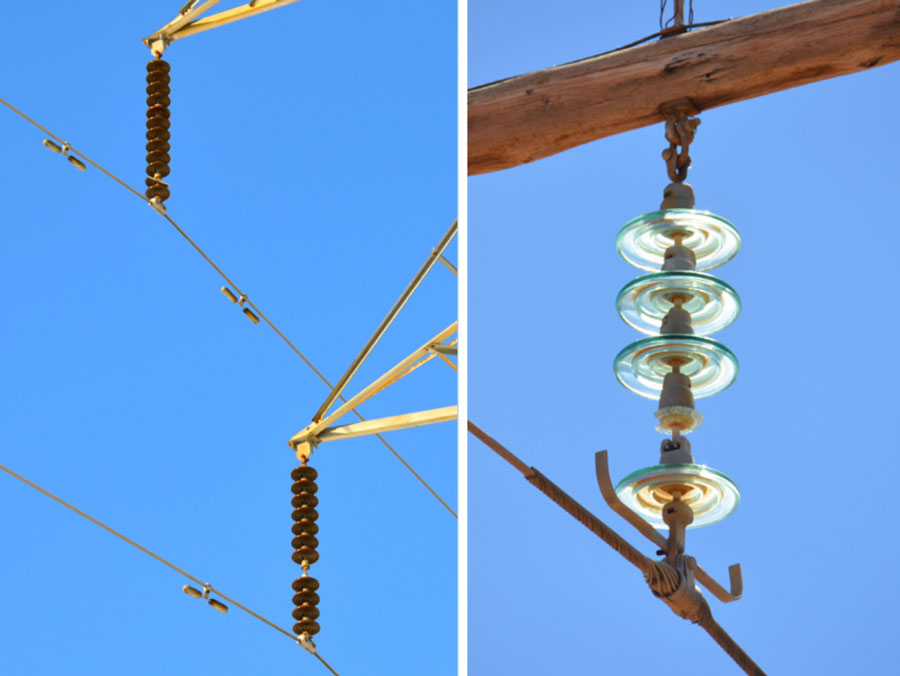
Causes & Modes of Insulator Failure
Many factors can bring about the failure of an insulator. For example, the insulator can contain a tiny manufacturing defect which over time will grow and lead to failure. That defect can be located within the dielectric part of the insulator, the metal fittings or in the materials used to bond the dielectric and metal end fitting.
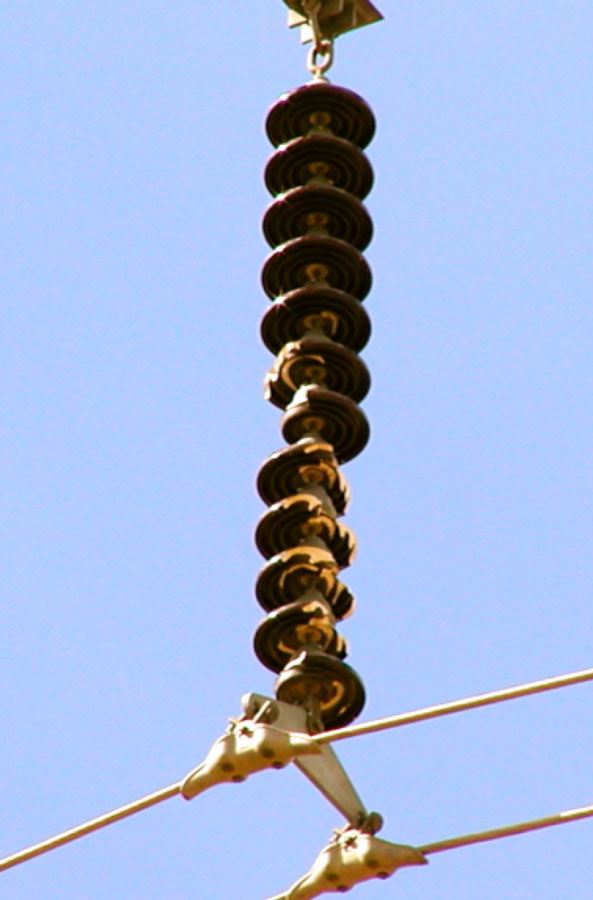
Failure of an insulator could also be caused by unusually severe service conditions. For example, an insulator can separate when abnormally high ice accretion or heavy wind conditions cause the mechanical load applied to exceed its rated value. Similarly, extreme pollution levels can cause degradation of the dielectric or corrode the metal fittings, thereby preventing the insulator from fulfilling its electrical or mechanical functions. A flashover leading to a power arc of extended duration can also bring about failure of the dielectric or of the metal fittings. Finally, acts of vandalism can also cause insulator failure.
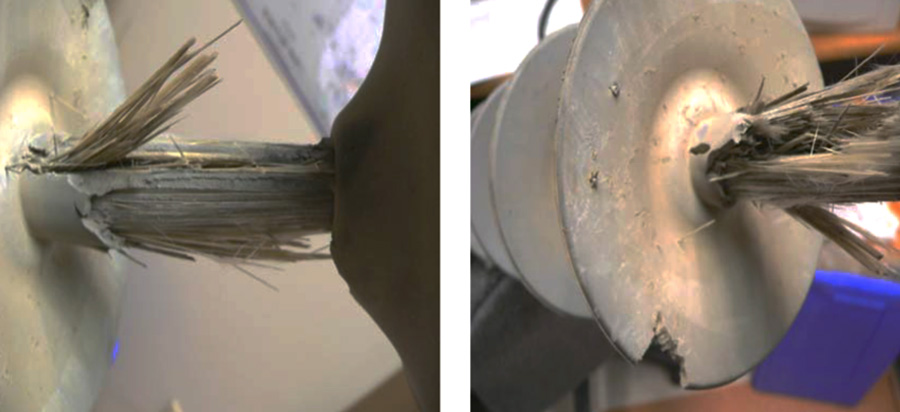
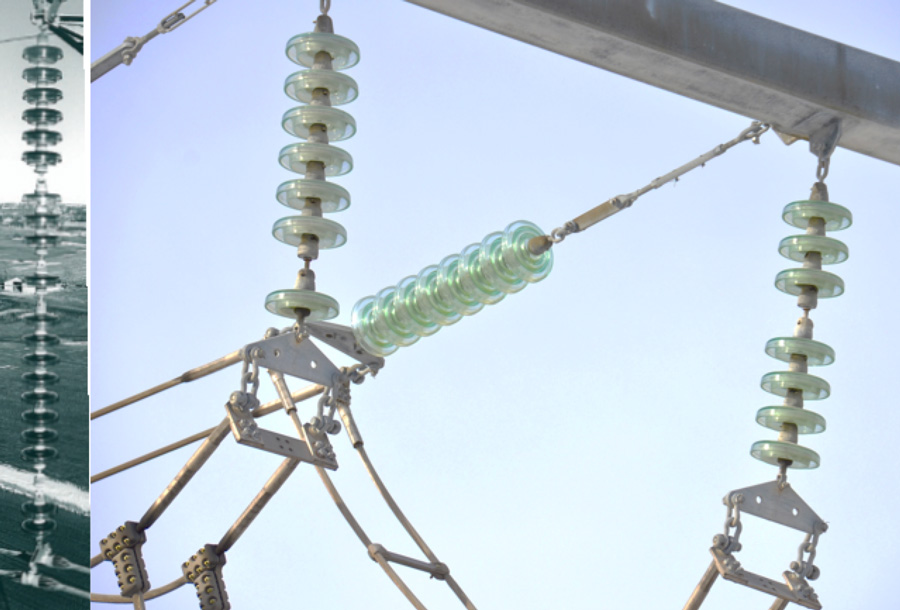
Fig. 5 shows examples of failed toughened glass insulators which are part of insulator strings supporting conductors. Only close examination of these insulators can determine actual cause of failure. For example, in the case of the top suspension string, analysis found that the high incidence of shattered discs on many strings of this ±350 kV DC line were due to excessive leakage current due to insufficient pollution design.
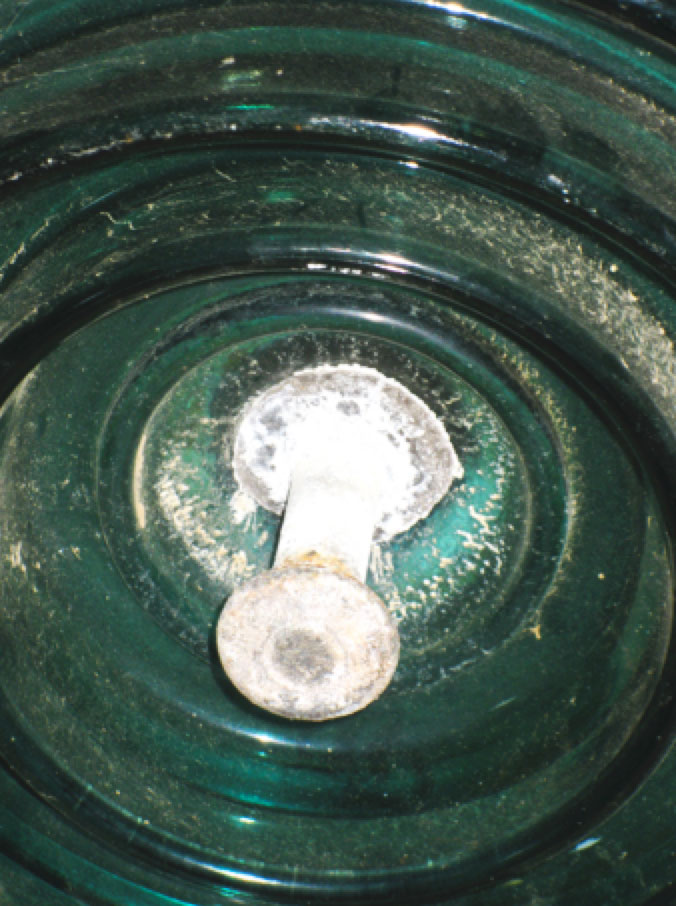
Fig. 7 shows failure of a UHV composite insulator in Korea about 10 years ago. The failure occurred close to the live end and only several sheds as well as the field grading device remained connected to the live end fitting. Here the failure was linked to puncture of the housing and subsequent internal tracing.
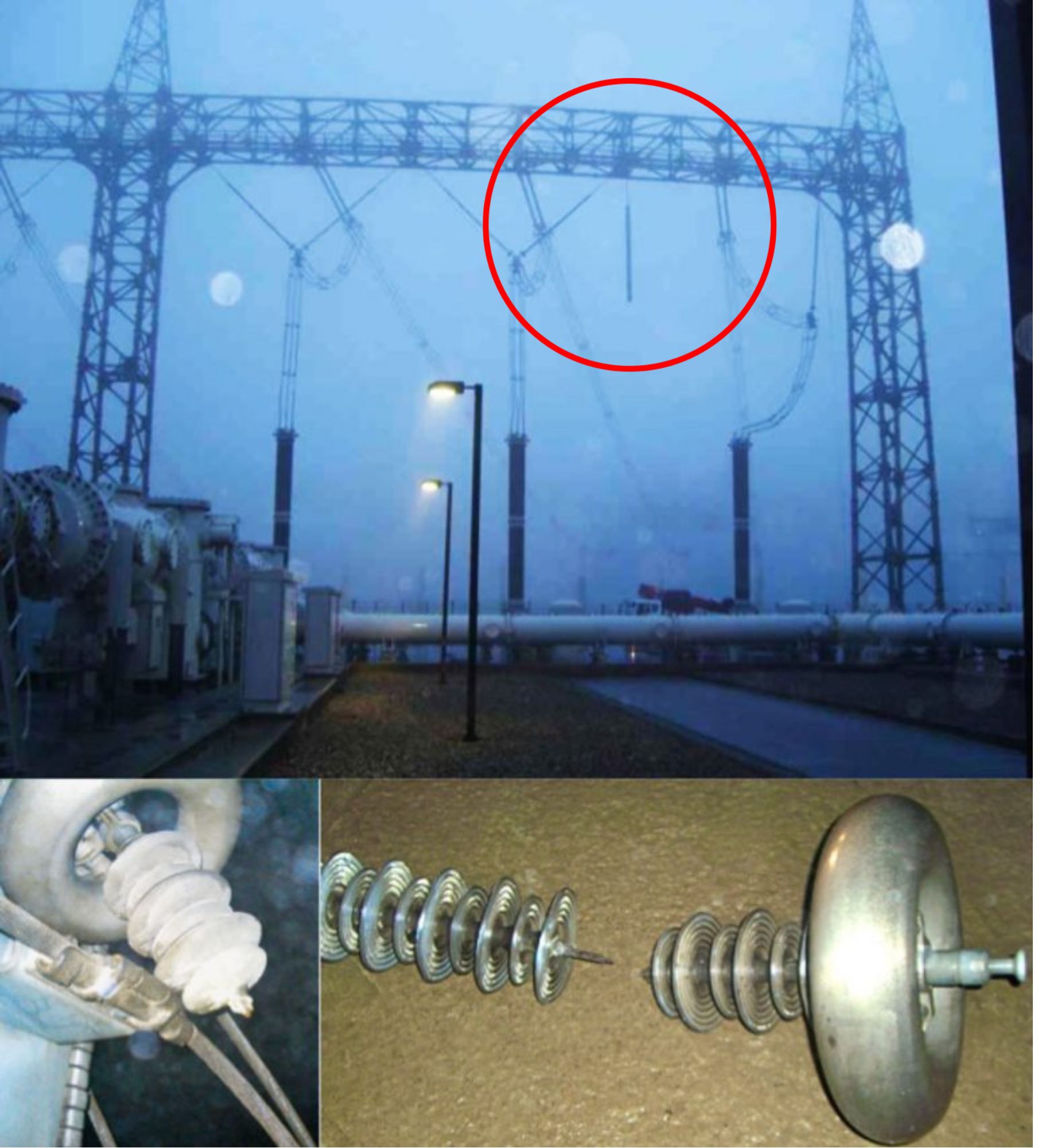
While the insulators in Fig. 5 failed electrically, they still fulfill their mechanical duty. The insulator in Fig. 7 first suffered an electrical degradation which subsequently led to mechanical failure.
Effect of Insulator Failure on Electrical System
When an insulator fails mechanically, it no longer seems relevant to consider any electrical function. By contrast, when an insulator fails electrically, it may lose its mechanical function or, in many cases, still offer the mechanical strength required to allow normal operation of the line for an extended period of time. These different scenarios are usually a consequence of the inherent characteristics of various types of insulators.
The effect of insulator failure on the operation of an electrical system also depends on tower design. The mechanical failure of a composite insulator, a glass or porcelain cap & pin or porcelain long rod insulator will in all cases cause a drop of the conductor if no other insulator is utilized in parallel. The conductor associated with the failed composite insulator in Fig. 7 did not fall to the ground because it was held by two insulators in a V configuration.
The situation becomes more complex when an insulator fails electrically but not mechanically. It is assumed that a porcelain long rod cannot fail electrically without also failing mechanically. By contrast, a composite insulator which has failed electrically may still have sufficient mechanical strength to hold the conductor (as in Fig. 4). But if there is only one insulator between conductor and tower it may no longer hold the service voltage.
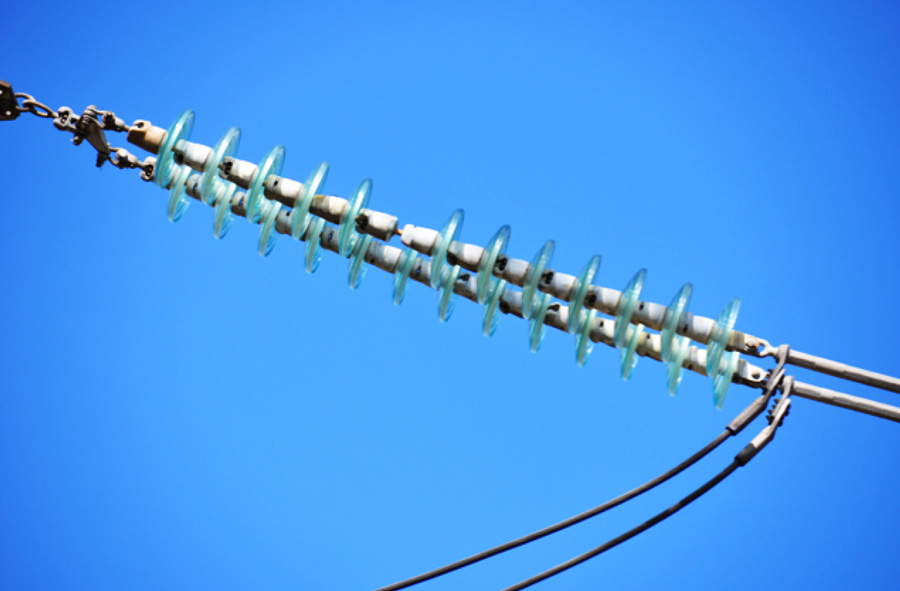
The most favorable case is for cap & pin glass or porcelain insulators. Since strings are usually made up of more than two insulators, the failure of only one usually allows the string to still hold the nominal voltage of the line. This is clearly illustrated in Fig. 8. The failed glass insulator has practically no detrimental impact on performance of the string. The same would be true if the string consisted of porcelain cap & pin insulators. However, as seen in Fig. 9, failure of glass discs can also result in line drops, depending on root cause of failure.
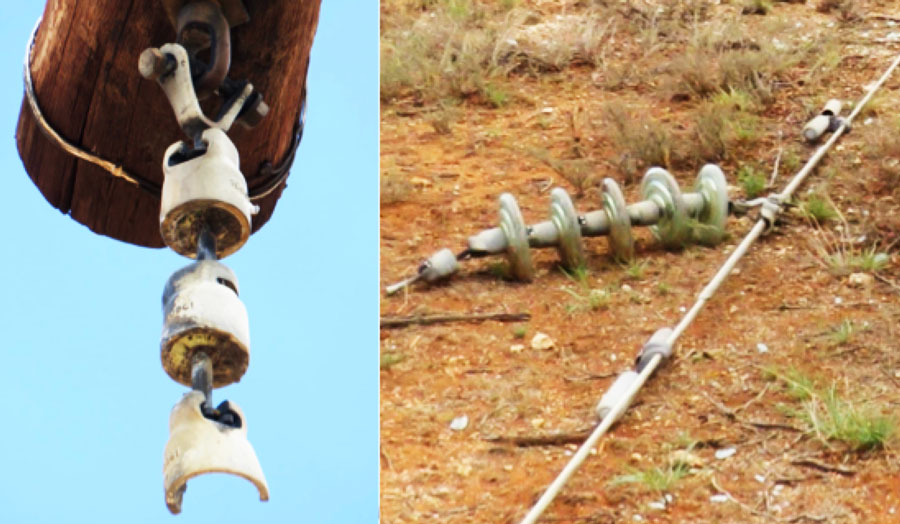
Detection of Failed Insulators
Determination of failure rate of insulators requires knowing both the total number of insulators which have been installed and the number that have failed. It is usually simple to determine number of insulators of any type which have failed mechanically. As indicated above, it is most unlikely or even impossible for a porcelain long rod insulator to fail only electrically.
Detection of glass cap & pin insulators that have failed electrically is based only on visual examination. In the string shown in Fig. 8, all insulators are electrically sound except for that whose glass shell is clearly missing. Should this cap & pin string have been of a porcelain, however, it would be more difficult to locate any defective units even though methods for such detection are available. At the same time, electrical failure of a single cap & pin insulator is generally not critical since it usually does not lead to service interruption. Therefore, it is usually sufficient to detect failed cap & pin insulators only once failure of the entire string has occurred.
Since electrical failure of a composite insulator will affect continuity of service, it is highly desirable to be able to foresee such failure early enough to avoid a service interruption. Electrical degradation of these types of insulators takes place over a period of time which, in most cases, is long enough to permit line inspection to locate the defect before it creates a service interruption. Different methodologies have been proposed for doing this.
Insulator Failure Rates
The failure rate of any given type of insulator is really something which can only be assessed by the utilities which use them. They are the only ones to know how many such insulators have been installed and how many have failed. Understandably, insulator manufacturers are also interested to know these figures because they are clearly in a position to take the measures necessary to improve that rate.
Failure rate of a specific type of insulator can be used as a basis for assessing quality. In this case, all failures – mechanical and electrical – should be taken together. But from the utility point of view, it is also important to know failure rate evaluated in terms of its impact on reliability of the system where these insulators are installed. In this case, it makes more sense to determine failure rate of a particular insulator type based on number of failed insulators that actually resulted in an outage. When selection of a particular type of insulator is based mainly on failure rate, it is important to distinguish between these two different assessments of what really constitutes failure.
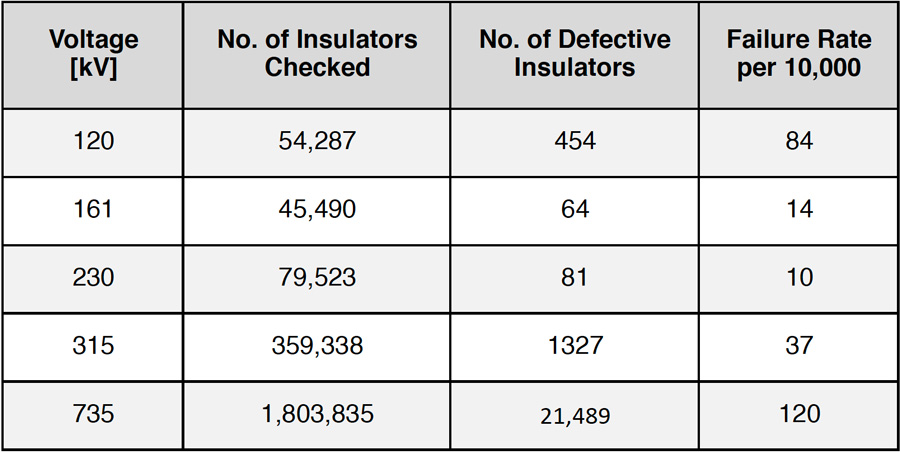
The failure rates presented in Table 1 are based on number of insulators found defective during line inspection and can be used to assess the quality of specific types of porcelain cap & pin insulators. Such high rates confirm that these insulators (which are no longer manufactured) were of questionable quality.

The failure rates of toughened glass insulators presented in Table 2 indicate that the quality of these insulators, already better than the porcelain insulators shown in Table 1, improved over the years. These rates were based on total numbers of insulators that failed, mechanically or electrically. Unfortunately, they do not give any information on the impact these failures may have had on reliability.
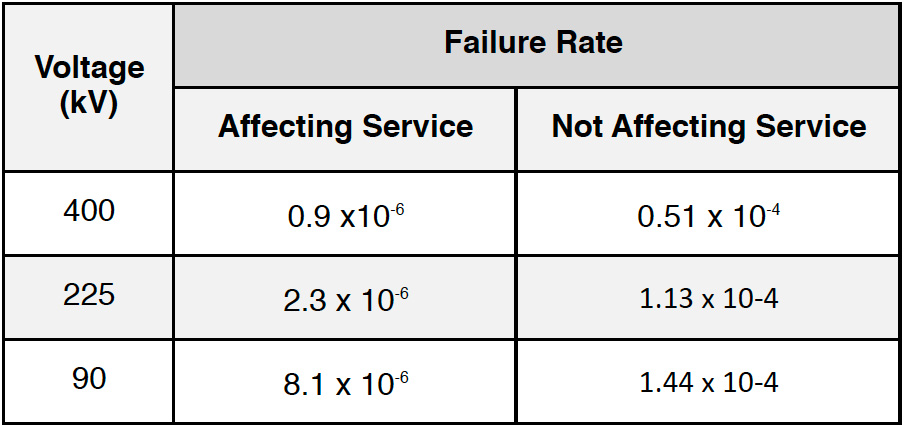
Table 3 illustrates the importance of distinguishing between mechanical failures that affect continuity of service and electrical failures which, in the case of cap & pin strings, usually do not. As can be seen, failure rates affecting service are about 50 times lower than failure rates not affecting service. The data in Table 3 applied to about 10 million cap & pin insulators of which 92% were toughened glass and 8% porcelain. The increase in failure rate as system voltage decreases may well be related to vandalism. It should be noted that failure rates of high quality porcelain cap & pin insulators are likely similar to those shown in Table 3.
The failure rate for composite insulators, quoted in a past CIGRE survey, was found to be on the order of 10-4 per year. This number corresponds to failures that affected service. However these numbers include failures of earlier designs of composite insulators and one can reasonably expect that the latest generations have a far lower failure rate.
Conclusions
Knowing the failure rate of a given type of insulator can be a useful tool on which to base expectations for its long-term performance. However, failure rate value by itself may not be sufficient to fully assess the impact such failures may have on performance of an electrical system. It is also important, especially for the utility, to know if the failure of a given insulator will cause a line drop and/or an interruption in service. In this respect, utility engineers should realize that line design is also an important consideration.