Failures of transmission line insulators due to natural pollution are often associated with changes in service environment or with incorrect parameters when specifying insulation during project design. Such outages normally occur when water on an insulator dissolves but in insufficient quantity to remove salt and other conductive contaminants that have accumulated on its surface. Leakage current flows over the wetted pollution forming high-resistance dry bands. While discharges across these dry bands usually self-extinguish, in exceptional cases they can develop into flashover.
A history of repeated outages affecting the 500 kV Xingó-Angelim II Line in northeastern Brazil a decade ago offers a good example of these types of issues. In this case, key factors such as changes in local precipitation patterns meant that insulators on this line had to endure longer periods with little to no natural washing. Indeed, in spite of studies on natural pollution in the areas through which the line runs, problems only intensified, in parallel with growth in the regional transmission grid.
This edited past contribution to INMR by engineers at Transmissora Aliança de Energia Elétrica S.A. (TAESA) reviewed experience with resolving flashover outages along this asset.
The 500 kV Xingó-Angelim II Line runs 193 km through northeastern Brazil, connecting the Xingó Hydroelectric Plant in Alagoas State to Angelim II Substation in Pernambuco. Since commissioning in 2004, the line has suffered a series of shutdown events concentrated mainly in the São Pedro Mountains in the highlands of Pernambuco. This is a region characterized by limited precipitation, typically only from April to August, as well as frequent fog and mist. About 57 km of the line, i.e. the section from Towers #284 to #397, passes through this area (Fig. 1).

The first measure taken to resolve the problem was systematic live line washing of the line’s glass insulator strings. However, the cost of this maintenance operation soon proved untenable given the difficulty accessing towers and the short time required between successive washing cycles. In 2007, a decision was made to apply RTV silicone coatings onto the glass insulators. About 13,800 insulators were replaced with new ones of which more than 8,650 had been pre-coated.
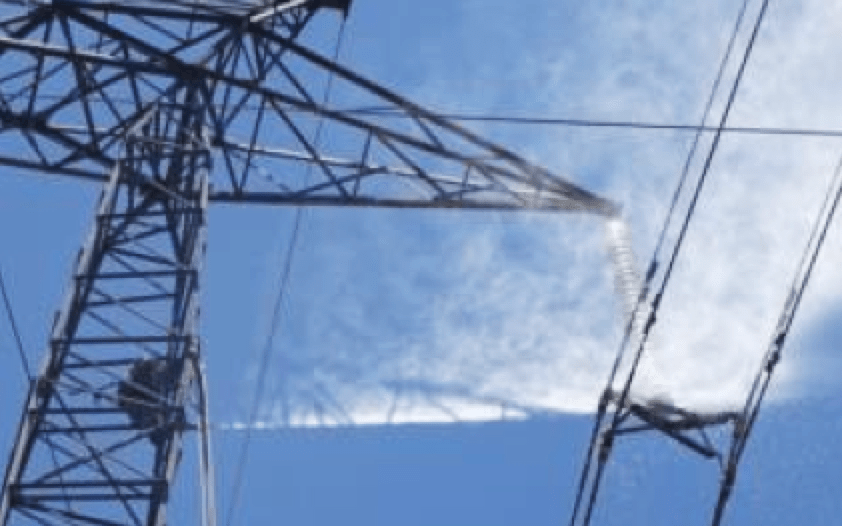
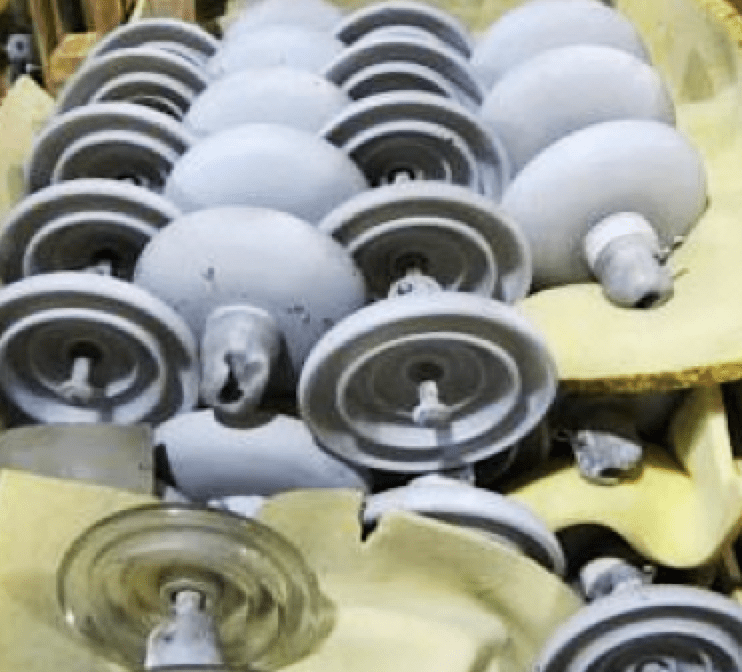
Nevertheless, only 3 years after application of the new silicone coated insulators, another pollution flashover outage occurred at Tower #284 – located near the start of the line section marked by hills. That incident gave the O&M Engineering Team the opportunity to remove and examine the condition of the coated insulators. After only a few years in service, there was already clear evidence of surface flaking and also loss of hydrophobicity, with consequent reduction in coating effectiveness. In 2015, following further outages, Tower #284 was affected yet again, indicating the need to consider alternative measures to mitigate the problem.
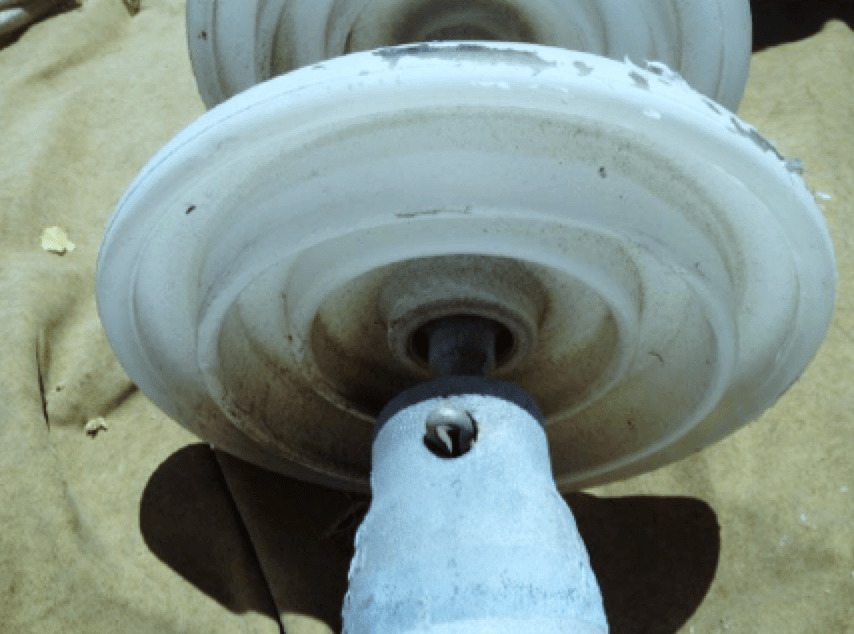
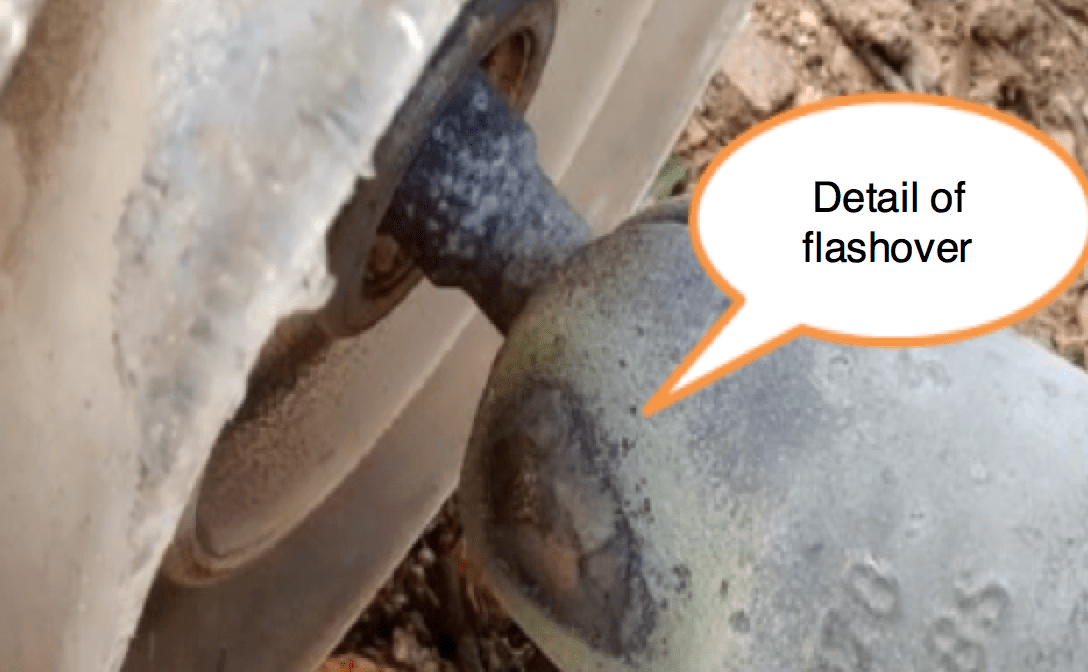
Review of Operating Data
The O&M Engineering Team conducted studies to evaluate possible solutions, taking account of all available data. First, cases of faults caused by pollution were analyzed to establish if these were still concentrated mainly in the São Pedro Mountains. This would confirm whether the primary problem was loss of coating effectiveness or if there was also growing pollution dispersion, i.e. other areas of the line were beginning to suffer from this problem as well.
Table 1 lists failures since 2010, showing all towers affected as well as their type and the phases involved. One important clue coming from this data was that all flashover outages were occurring either at dawn or during the night. This reinforced the role played by humidity. Moreover, the fact that outages were often bi-phasic to ground suggested that both phases had similar characteristics. Finally, tower silhouettes were compared to confirm if faults were concentrated on the same type of insulator configuration (see Figs. 6 and 7).


Insulation on the Xingó-Angelim II Line was designed with 8320 mm creepage distance (i.e. 15.12 mm/kV) along the entire route – a value corresponding to light pollution according to IEC 60815. In order to confirm if problems were occurring only in hilly areas, a chart was plotted showing altitude of each tower in the line (see Fig. 80). Indeed, most towers affected were in the section passing the São Pedro Mountains and at much higher elevation than elsewhere on the line. This would make them more susceptible to conditions of fog and mist.

To better understand the role of natural cleaning, data was also collected on local rainfall patterns over recent years, using the town of Bom Conselho, located in the middle of the hilly area, as reference (Fig. 9).
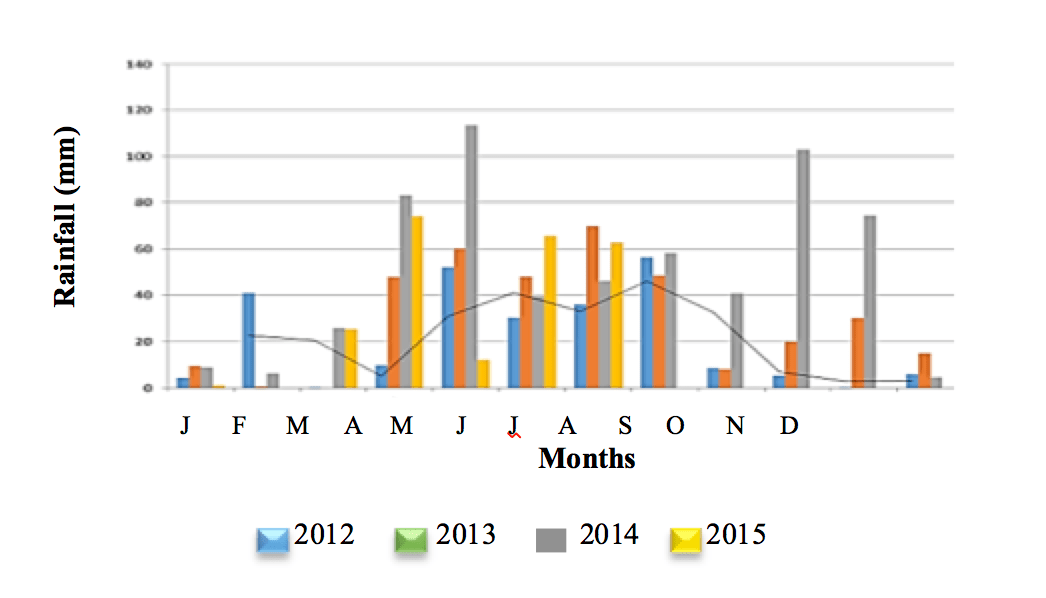
First Mitigation Program
Results of the study highlighted the need to concentrate mitigation efforts on towers near the São Pedro Mountains since this area was the focus of insulation failures due to natural pollution. Possible mitigation alternatives were compared in light of several factors:
• Numbers of strings involved;
• Cost of implementation;
• Experience at other utilities;
• Penalties applied by national regulatory authority;
• Safety of linemen and asset;
• Nature of solution.
Considering the positive service experience with composite insulators applied on transmission lines in the same region as well as TAESA’s own experience with them, a recommendation was made to replace all 618 glass insulator strings between Towers #284 and #397 with an extra high pollution design of silicone insulator. This recommendation included towers with suspension as well as strain insulator assemblies. The composite insulators selected had almost 15,000 mm creepage distance, i.e. about 80% higher than the coated glass strings they would replace. They also offered superior hydrophobicity and other desired electrical properties (shown at Table 2). Application of these polymeric insulators increased specific creepage distance from 15.12 mm/kV to 27.3 mm/kV, enhancing line insulation to face pollution levels classified between heavy and very heavy. After their acquisition, an intense coordinated effort allowed replacement of all old strings in only three days of work with the line de-energized (Fig. 10).
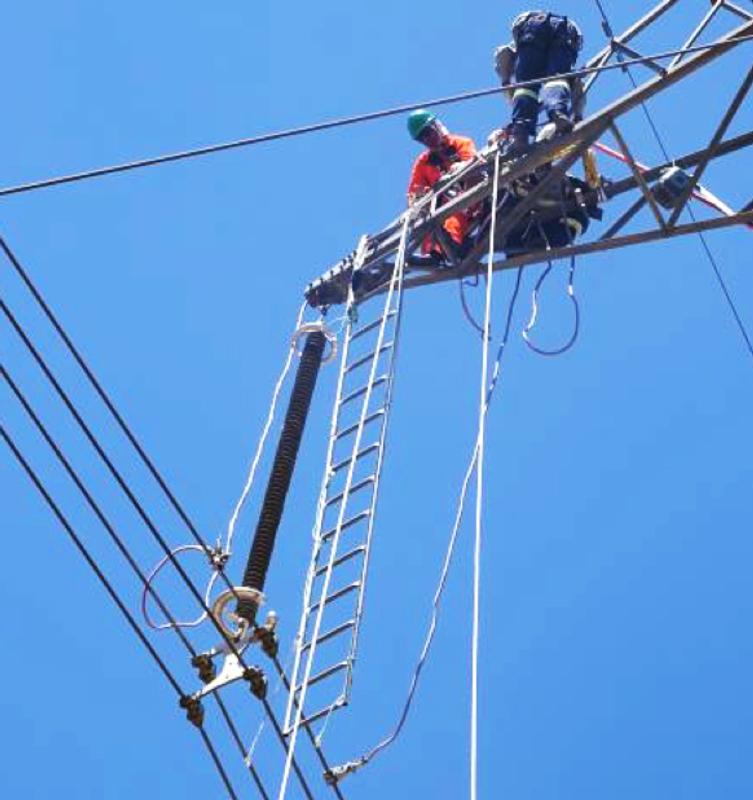
Recurrence of Outages
In 2016, after only about a year with the new polymeric strings, the line faced another increase in outage rate. While the outages had the same basic characteristics as past problems due to natural pollution, this time they were focused on towers located outside the São Pedro Mountains. Maintenance crews conducted corona camera inspections on some of these line sections to check what could be happening (see Figs. 11 and 12) and results showed that corona activity on glass insulator surfaces had increased dramatically. This confirmed suspicion of an unexpected high pollution phenomenon.
The main issue then became to understand why these problems had not occurred before since the basic geographic conditions had not changed. The only possible explanation behind the sudden spike in outages could be a change in local rainfall. O&M Engineers therefore analyzed precipitation patterns from 2015 and 2016, relying on data from Pernambuco since data from Sergipe and Alagoas States was not readily available. The assumption was that level of rain activity in all these regions behaved more or less the same, based on past experience.
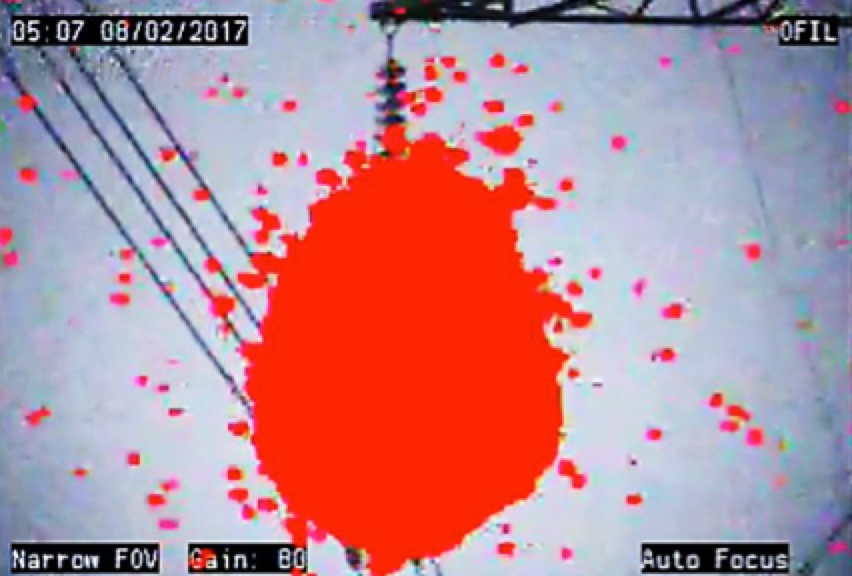
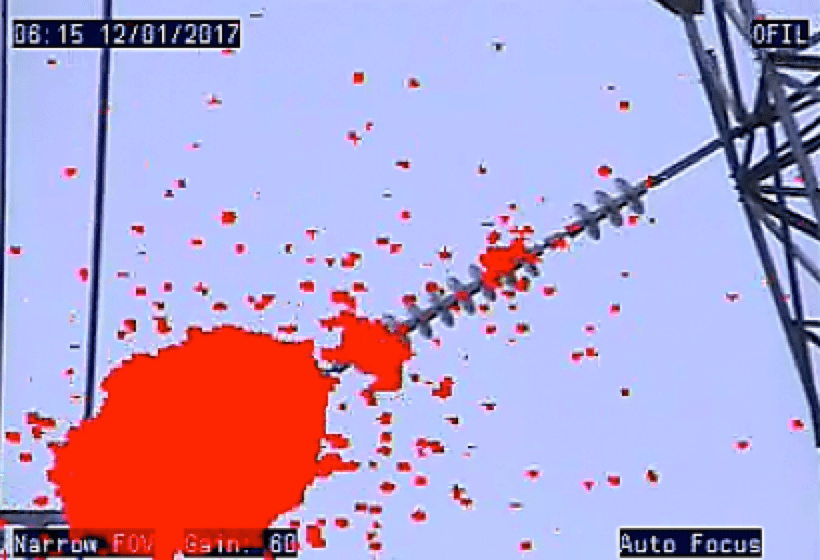
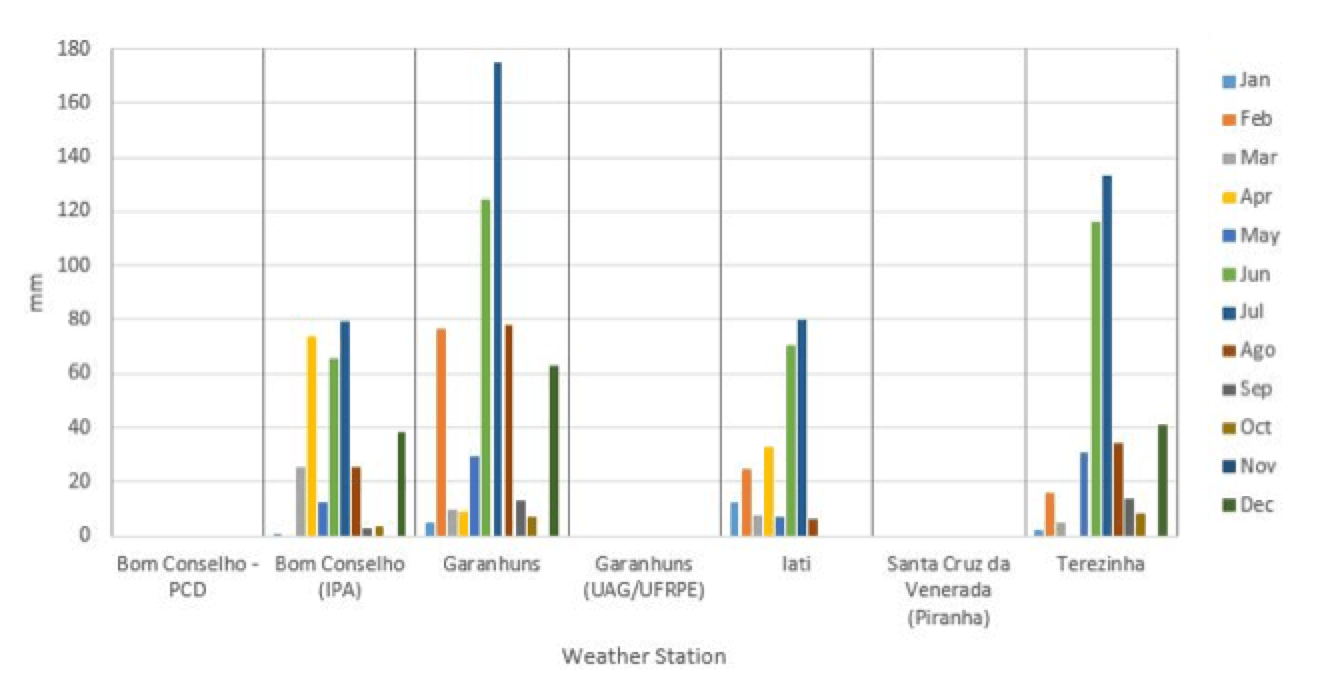
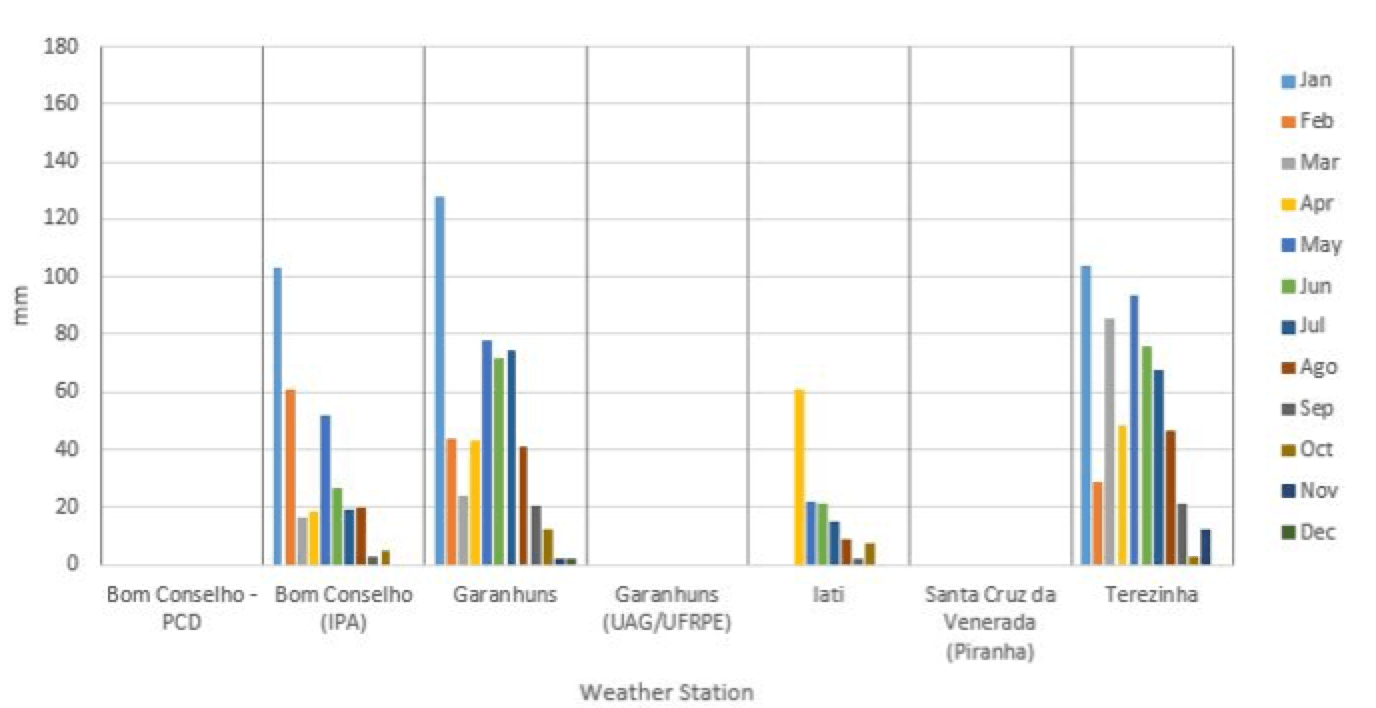
Looking at this data showed a notable decline in rainfall in 2016 compared with the previous year, except for Terezinha Station. There was also an extension of the dry season at most weather stations. This evidence could lead to future action to prevent new such outages by replacing the toughened glass insulators remaining in service on this line with the same high pollution polymeric type used near the São Pedro Mountains.
Monitoring Composite Insulators
Application of this new insulator technology has brought with it the need for different inspection programs and techniques to prevent occasional failures and new outages. The corona camera already used is expected to help maintenance crews analyze evolution of pollution accumulation on polymeric surfaces over the years. However, to check for incipient problems leading to risk of brittle fracture, periodic close-up visual inspections will be required in combination with techniques such as E-field measurement and X-raying samples removed from the line. As of the end of 2017, the O&M Engineering Team had begun to establish a regular inspection plan for these insulators, using all these techniques, as well as revised inspection protocols to be undertaken by maintenance crews.
Conclusions
The 500 kV Xingó-Angelim II Line passes through an area of heavy natural pollution not sufficiently considered during project design. A combination of this and concentrated high humidity has resulted in this asset experiencing high outage levels over the years. The São Pedro Mountain Range was studied first since all outages were concentrated there. The solution first applied proved successful and the number of outages decreased, even before eventual replacement of toughened glass strings with a composite polymeric type. The subsequent spread of outages having the same characteristics as at other parts of the line suggested that the combination of humidity and pollution was again likely affecting insulators, but now at different locations. The logical conclusion was that these faults had not occurred before since the hills were the ‘weakest’ part of the line under humidity conditions. Once problems in this section had been resolved, other weaknesses began to show up.
The O&M Engineering Department was able to find support for this theory by analyzing data to confirm a decrease in precipitation during the rainy season in the year immediately after the first insulator replacement. This lack of rain brought with it increased pollution accumulation on glass insulator surfaces, which then triggered flashovers under conditions of high humidity. To resolve this, the same solution applied in the first case is considered, i.e. replacing existing glass insulator strings with polymeric types. Moreover, data from corona camera images has proven valuable in determining criticality of those strings needing to be replaced as soon as possible. Finally, different line inspection techniques will have to be implemented for the new polymeric insulators and TAESA is equipping and training its teams for this challenge.