Application of composite insulators at substations has been steadily increasing due to reasons of improved safety as well as their excellent pollution performance, especially at installations with harsh environments. The main concern for these insulators, however, has related to possible premature ageing, potentially impacting long-term performance as well as service life. Over the past decades, many artificial and natural ageing tests and procedures have been developed to enhance knowledge and experience in this regard. In parallel, special artificial pollution laboratory tests have been designed to allow for the hydrophobic surface properties that are essential for good pollution performance.
This edited contribution to INMR by Dr. Jens Seifert of Reinhausen Power Composites reviews the historical development that influenced the standardization process within CIGRE and in IEC. Results with different test methods are also compared with test station experience
Background
Technical Brochure No. 142 was the first international document published regarding natural and artificial ageing and pollution testing of polymeric insulators. The challenges were summarized as: “Unfortunately, pollution tests of polymeric insulators in the laboratory present special problems. Such insulators, when new, are difficult to contaminate or wet and surface conditioning, by conventional techniques might not always produce realistic test results. Development of proper pollution test for polymeric insulators is a challenging technical problem. The major difficulty is method of contamination”. Since the hydrophobicity properties (i.e. loss, recovery and transfer) are dominating factors, adjusting to the relevant state can also be problematic.
Other challenges for ageing tests are: “It is necessary to understand the ageing mechanism of polymeric insulators…several types of accelerated ageing tests are currently in use. It must be noted that these test procedures are time consuming and sometimes not possible to perform on full-scale samples”. It is also questionable whether accelerated conditions under more severe test stress properly reflect real natural ageing conditions. Does some scale factor really exist between accelerated ageing tests and actual insulator service life?
Among the main ageing mechanisms for these insulators are:
1. ageing by water penetration (e.g. polarization of interfaces, hydrolysis);
2. ageing by UV radiation;
3. thermal ageing of the organic material (i.e. from elevated temperature);
4. impact of abrasion (e.g. from sandstorms, etc.);
5. corona effects (e.g. from high electrical field stresses);
6. effect of electrical discharges (e.g. partial surface discharges).
Most of these ageing mechanisms are reflected by the design tests in IEC 62217, such as the water diffusion test, the UV weathering test and the tracking and erosion test. Additional test developments also consider multiple and/or combined stresses (e.g. UV, thermal, electrical discharges) such as the 2000h and 5000h tests from FGH, ENEL, EDF and EPRI. The impact of high electrical field is presently under review in the revision of IEC 61109.
Table 1 summarizes development of testing from the 1970s to the 1990s, indicating test parameters as well as associated evaluation criteria. Some tests were intended to simulate special local climatic conditions or typical environmental situations that were considered as critical to ageing of polymeric materials. In particular, multiple-stress tests are highly complex and designed mainly to evaluate ageing of the housing.
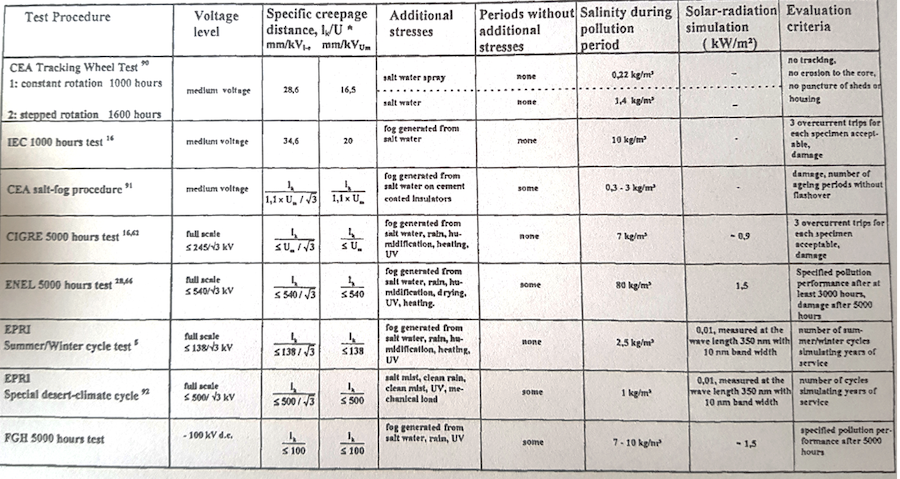
Unfortunately, few comparisons have been made between artificial (i.e. accelerated) laboratory test results and natural long-term ageing results, mostly at natural test stations. Yet such correlations and knowledge of the approximate acceleration factor are essential to assess whether an artificial ageing test is representative. Multiple-stress tests are also time consuming, costly and availability of laboratory facilities to perform them is limited. The 1000h salt fog tracking and erosion test was selected for the main body of IEC 61109:1992 while a modified 5000h test was defined in Annex C as “Ageing Test under Voltage Simulating Weather Conditions”. With establishment of IEC 62217 Ed. 1.0:2005, the 1000h test was defined in the main body while the wheel test and the 5000h multiple-stress test were defined in Annex A and B (both normative at the time).
As such, all three tests were normative and clear separation between ‘Tracking and Erosion’ and ‘Ageing Tests’ was not fully explained to users. During work on IEC 62217 Ed. 2.0:2012, a questionnaire was distributed asking for the preferred tracking and erosion test. The 1000h test was selected by National Committees and it was decided to conserve the wheel and the 5000h test in IEC TR 62730 as reference mostly for special customer requests and specifications. While the wheel test is considered as a ‘tracking and erosion test’, the 5000h test is better characterized as an ageing test. IEC TR 62730 is presently under revision to improve test repeatability by better definition of the spray method (i.e. indirect versus direct). Due to increasing demand from the marketplace, there will need to be consideration as to whether a multiple-stress test can be integrated into the standard as an ‘ageing test’ in addition to the 1000h tracking and erosion ‘design test’ and, if so, how.
Pollution tests for polymeric insulators are needed to establish pollution performance and therefore dimensioning. Among others, the following pollution tests have been studied and evaluated over the past 35 years:
• salt fog tests with defined salinity (in terms of kg/m³ salt fog density);
• clean fog tests with solid pollution layers (in terms of SDD in mg/cm² solid layer salinity);
• both above tests with artificially contaminated insulators;
• clean-fog test with naturally polluted insulators;
• rapid (solid layer) test;
• quick (clean fog) test;
• dust cycle method (DCM);
• dry salt layer method (DSL).
Up to now, relevant standards still do not exist but current work within CIGRE offers reason for optimism that such test standards will be established and representative as well as repeatable test procedures for insulators with hydrophobic surfaces/ hydrophobicity transfer mechanisms (HTM) will soon be defined. In 2021, a group of international experts collected experience across different countries and compiled a survey. Based on this consolidated knowledge, IEC TC36 decided at its Plenary Meeting in June 2021 to start a new project to develop a standard for artificial pollution testing with consideration given to the ‘HTM effect’. It is expected that this work will be completed within 36 to 48 months.
Examples of Ageing & Design Tests
IEC 62217 – 1000h
Also known as the 1000h salt fog test, this was developed as a design test and not an ageing test. However, research with different polymeric housing materials at the 20 kV Nordstrand Marine Test Station in Germany found that there was correlation between results of the 1000h test and long-term test station results in regard to tracking and erosion patterns. Today, this test is the standard IEC tracking and erosion design test, considered as representative, repeatable and cost efficient. Hydrophobicity is intentionally suppressed after about 100h and discharges are initiated to provoke tracking and erosion. Such an ageing profile is typical for marine applications with permanent salt fog (e.g. close to coastlines). This test was successfully passed, i.e.:
• no tracking occurred;
• erosion depth (< 3 mm) did not reach the core;
• no shed, housing or interface was
Different shed profiles and dimensions were tested successfully, with both LSR and HTV types of insulators.
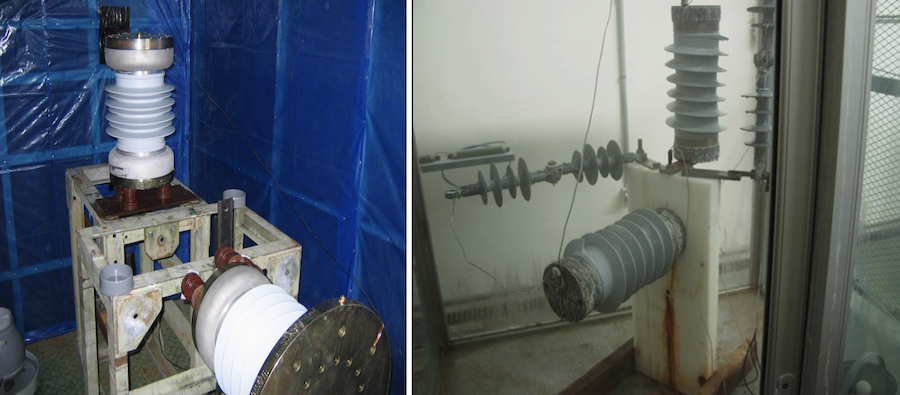
IEC TR 62730 – 5000h Test
This consists of accelerated weather ageing cycles, combining multiple stresses: humidification, heating to +50°C, rain, simulated radiation and salt fog (based on IEC 62217 Annex B 2005-10 with humidification, heating to +50°C, rain, simulated radiation and salt fog). The test was removed from IEC 62217 in its 2nd edition but conserved in IEC TR 62730 since it was no longer regarded as a design test but rather an ageing test. The test profile was developed to simulate conditions in Italy and France, i.e. with Mediterranean climates of high UV stress, elevated temperatures, natural pollution and vicinity to coastlines. Similar ageing patterns have been found at test stations located in these areas (e.g., Martigues). No scale factor has yet been established between laboratory testing and natural test station experience. While this test is not mandatory for IEC qualification, it is nonetheless used in the specifications of different TSOs in the Middle East, North Africa and Southern Europe.
Insulators have been tested with the following ageing cycle:
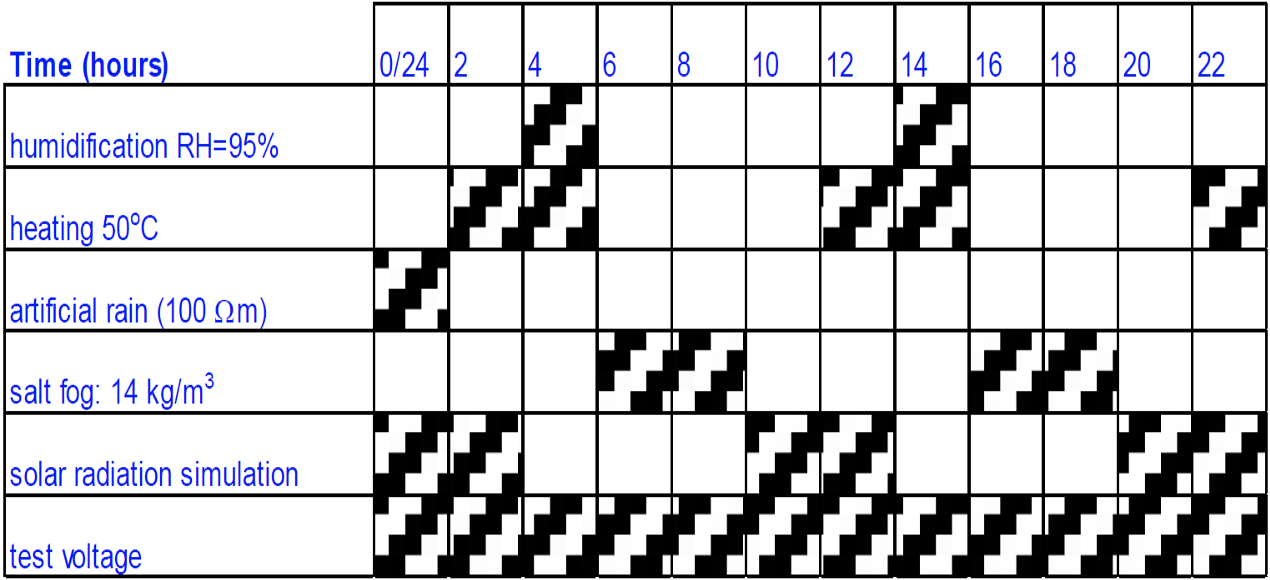
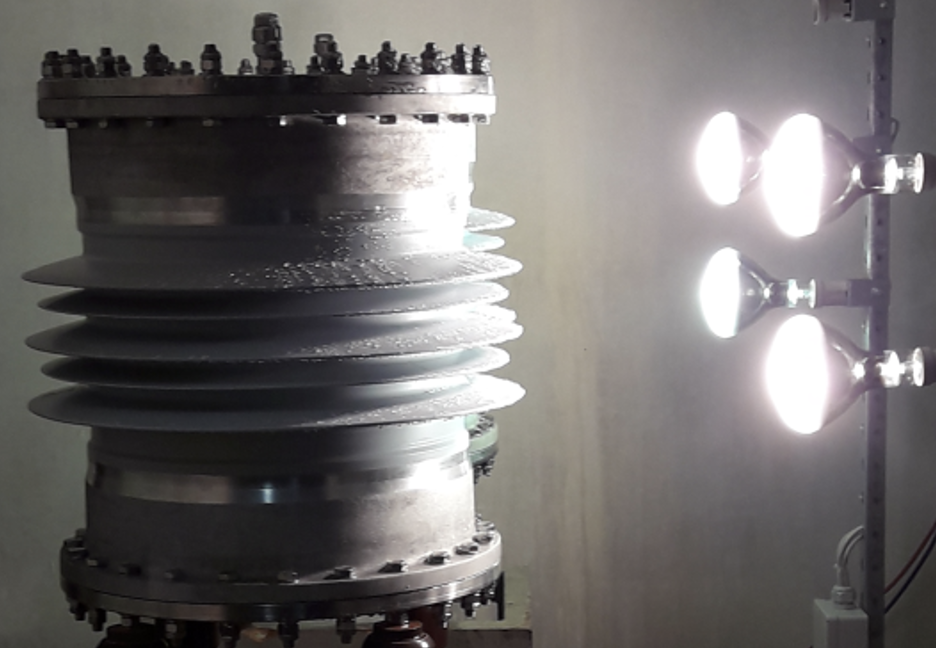
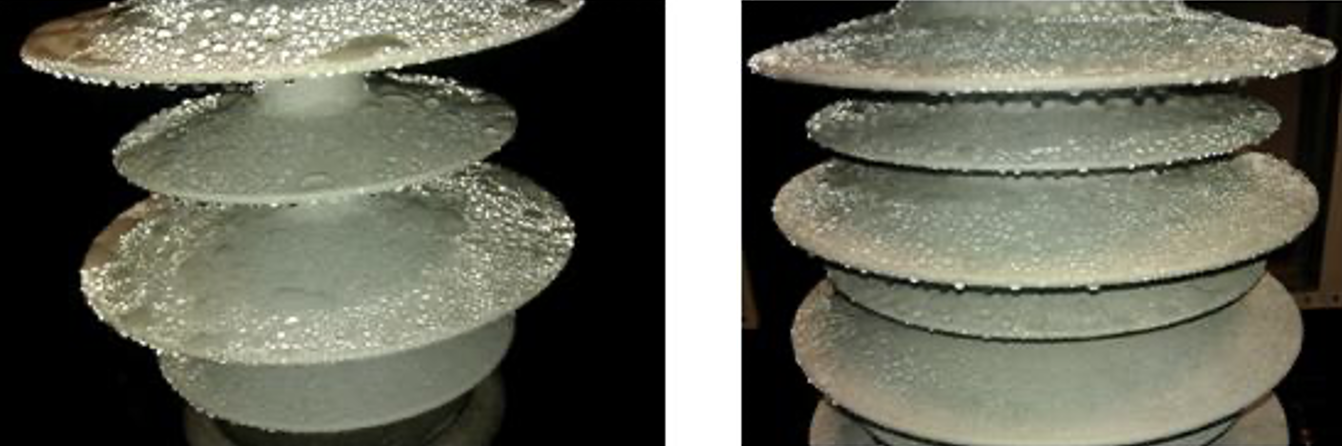
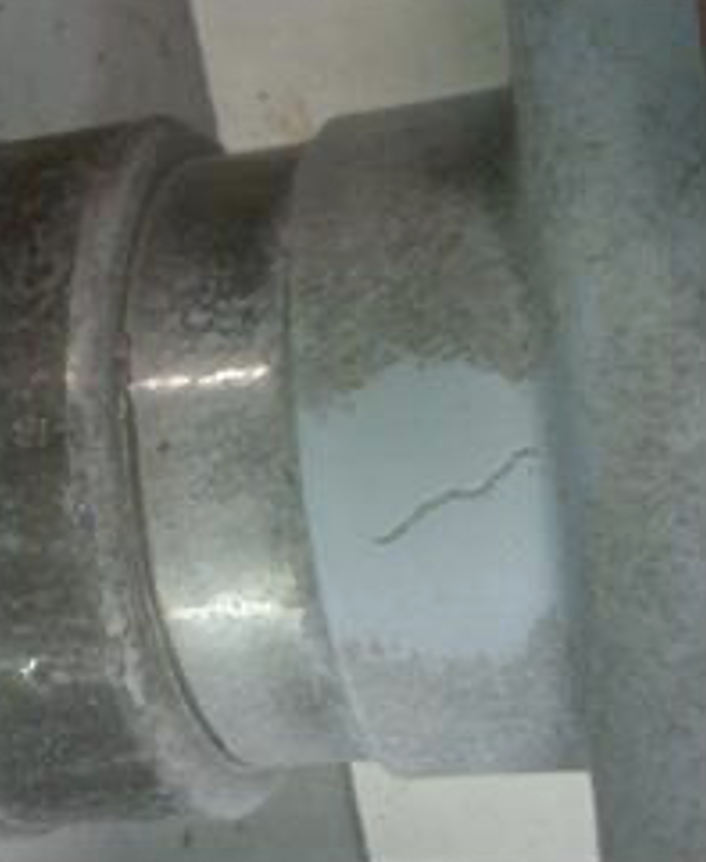
Test insulators (i.e. both solid rod and hollow core types) were visually examined after the 5000h ageing test. The test was successfully passed with the following results, applying to both LSR and HTV types:
• hydrophobicity tests (wettability class WC 2 to WC 4);
• slight erosion (1 mm depth < 3 mm max. criteria);
• No sheds were punctured.
Terna – 2000h Test
This is also considered a multiple-stress ageing test and is performed in accordance with Terna (Italian TSO) specifications. The test shall reflect the specific conditions in of Italy (e.g. severe salt fog pollution along coastlines) and has been performed on full size (1:1) samples. Recently, tests on short samples are also accepted.
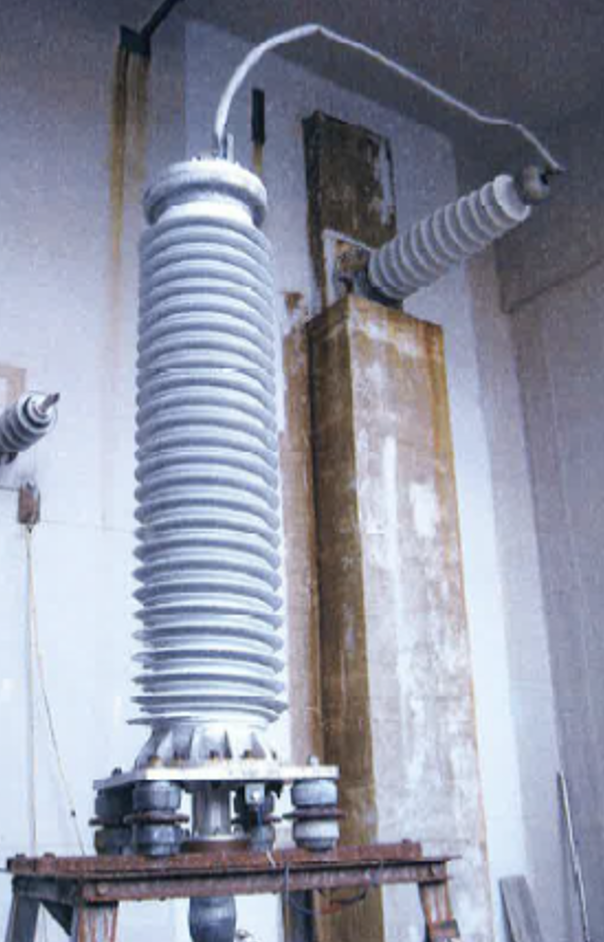
Satisfactory results have been observed after 2000h multiple stress testing according Terna specifications for 245 kV cable terminations of both LSR and HTV types, in actual configuration.
Pollution Tests: Examples with DC Stress
Solid Layer Method
The test object is coated with a uniform dry layer of some defined solid pollution and then energized and humidified. Pre-conditioning of insulators and test procedure were adjusted based on the test method of CIGRE TB 555. To allow pollution of the hydrophobic housing material, a thin layer of dry kaolin powder is applied on the insulator surface before application of the pollution layer. Contamination of the insulator surface is performed with DC voltage according to IEC TS 61245 by a mixture of kaolin, water and sodium chloride. Measurement of pollution is performed according to IEC TS 60815-1. After a defined drying period of 20 to 48h, the polluted test sample is placed in the test chamber and steam fog used for wetting the layer.
During these tests, voltage is applied by the ‘Up & Down’ test method. Therefore, the test object is subjected to an initial voltage for 15 min and voltage is then raised in increments of 10% of test voltage every 1 min until flashover. After flashover, the voltage is re-applied and raised as quickly as possible to 90% of the previously obtained flashover voltage and subsequently increased in steps of 5% of the initial flashover voltage every 3 min until flashover. Voltage is then again raised rapidly to 90% of the most recently obtained flashover voltage, held for 3 min and then increased in steps of 5% every 3 min until flashover. This test is continued for a minimum duration of 100 min and a minimum of 10 flashovers. The key result of this test is the lowest flashover voltage occurring during the Up & Down test method.
Salt Fog Method
The test object is subjected to some defined ambient salinity. For salt fog tests, no additional preparation or pre-conditioning of the insulator surface is performed.
The test procedure has now been replaced by a modified ‘Up & Down’ method, as per the solid layer method. The test object is subjected to an initial voltage at the reference salinity for 20 min and voltage is then raised in steps of 10% of test voltage every 5 min until flashover. After flashover, voltage is re-applied and raised as quickly as possible to 90% of the previously obtained flashover voltage and thereafter increased in steps of 5% of initial flashover voltage every 5 min until flashover. Then, the voltage is again raised rapidly to 90% of the last obtained flashover voltage, held for 5 min and then increased in steps of 5% every 5 min until flashover. After a standard deviation of <5% of the last 5 flashovers is reached, the test is completed with the result being the mean value of the last 5 flashover voltages.
Test Parameters
Different insulator designs are tested. All samples are designed with a length of 2 to 3 m and shed profiles are in line with IEC TS 60815-4, e.g. a creepage factor of 4. These can be assigned to three main groups: 1-x, 2-x and 3-x respectively. Within each group, housing material and basic design principles are the same. Tested housing materials are made using HTV silicone and LSR. The second number on the label of each test sample represents the respective sample within the group, the samples may have different diameters, shed overhang, and shed spacing. Figs. 7 and 8 show the pollution layers being tested with their respective ESDD (Equivalent Salt Deposit Density) and NSDD (Non-Soluble Deposit Density) values as well as tested salinity in correlation with the site pollution severity classes according to IEC 60815-1.
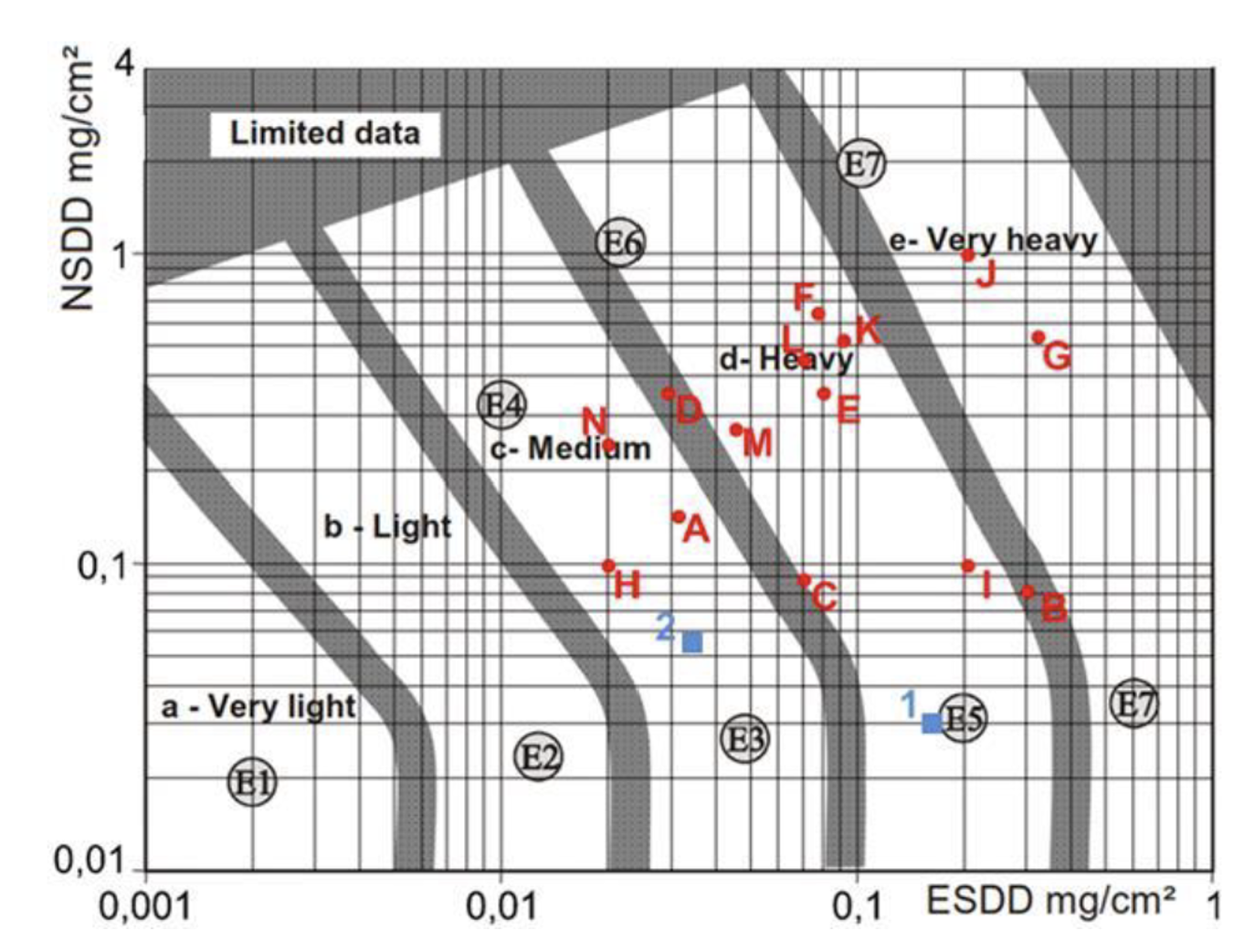
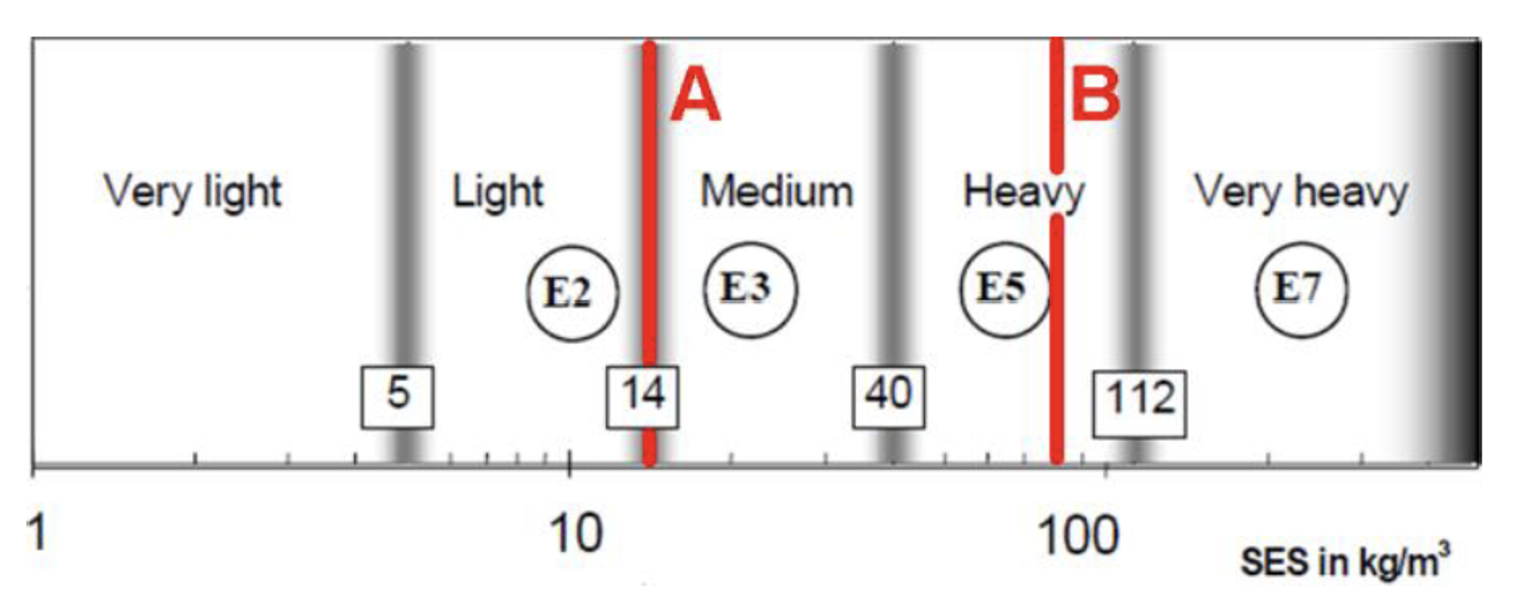
Normalizing Test Results
To compare test results obtained on insulators of different dimensions, minimum flashover voltages are converted into specific creepage distances (SCD), which are based on calculation rules of IEC TS 60815-4. This also allows for diameter correction for average diameters (Da) > 250 mm to standard diameter condition. Consequently, the index ‘0’ for applied diameter correction and index ‘FO’ for normalized flashover values are given (i.e. SCD0, FO) using the following equation:
Thus, decreasing flashover voltages result in increasing SCD0, FO values.
Up & Down Test Method Versus Withstand Test
More than 30 tests were performed on composite insulators that showed similar flashover behaviour during artificial pollution tests. Results of the Up & Down and the withstand test methods were close, as shown in Fig. 9. Minimum flashover voltages for the vertical test position were reached after 40 to 70 min, depending on fog distribution, and constant flashover voltage occurred for at least 30 min. This implies a long critical time range, which may be caused by a slow pollution wash-off process.
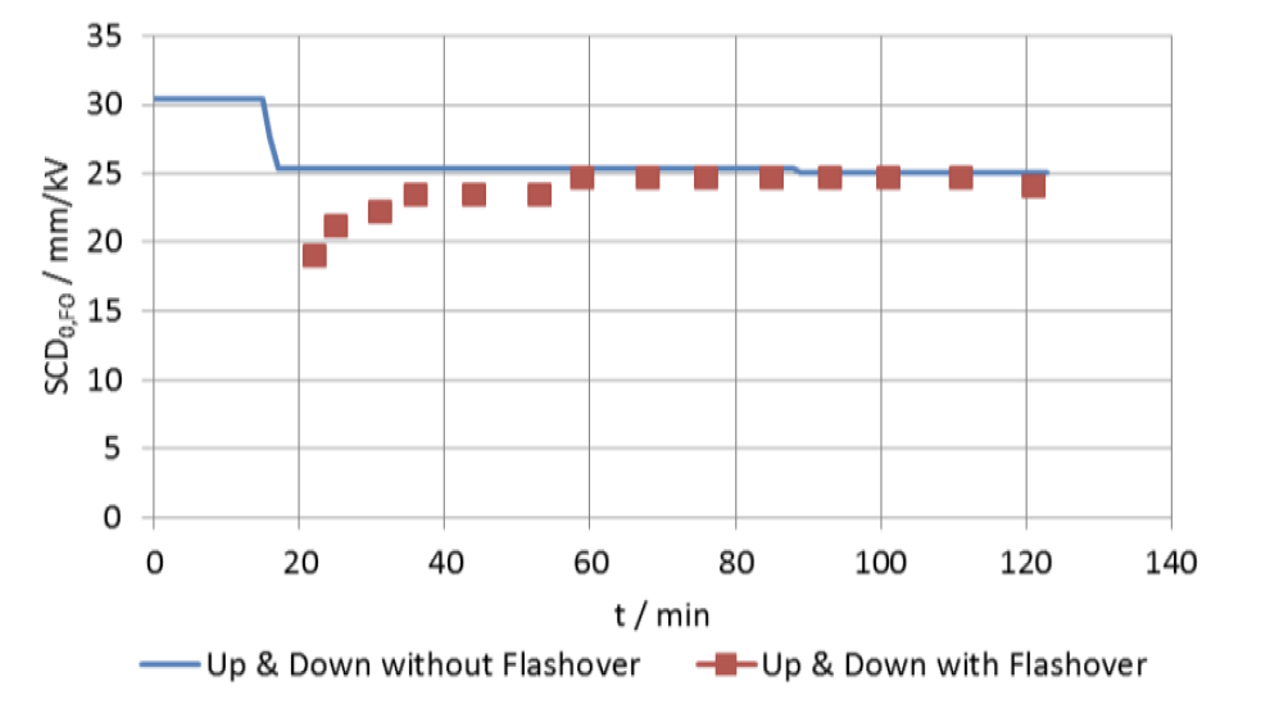
Thus, several flashovers can be obtained during the critical time range during artificial pollution tests on composite hollow core insulator samples. It must be noted that this is only valid for the vertical position. Horizontal insulators showed a faster wash-off process.