Overhead lines in contaminated areas must be designed with suitable insulation levels and leakage distance based on the characteristics of their environment. Polluted conditions can increase leakage current along insulator surfaces, leading to flashovers, line trips and possible outages.
There are different options to cope with polluted service conditions. One is increasing leakage distance and selecting the most suitable insulator profile. A second consists of application of silicone rubber insulators. These offer the benefit of a hydrophobic surface but must be properly specified and designed to avoid risk of permanent damage from sustained exposure to corona. A third alternative, seeing growing interest in recent years, is applying a silicone coating over glass or porcelain insulators.
Recently, there has also been research on application of naturally hydrophobic and even ‘super hydrophobic’ surface treatments in order to achieve the water repellency of silicone but without the silicone. This edited contribution to INMR by J.M. George, Scientific Director at Sediver, presents findings from recent investigations into the pollution performance of such treatments.
Almost all treatments available today are based on silanes or other organic chemistries revolving around the common goal of providing a hydrophobic surface. Sediver as well as other laboratories have been engaged in innovative research dealing with microscale, nanoscale or even hierarchical profiles. This field is complex and deals with the Wenzel to Cassie-Baxter transition (see Fig. 1), options of which are not yet deployed on an industrial scale but are still only at the basic research stage. Among the targets sought by most laboratories is super-hydrophobic status, i.e. a contact angle above 150°.
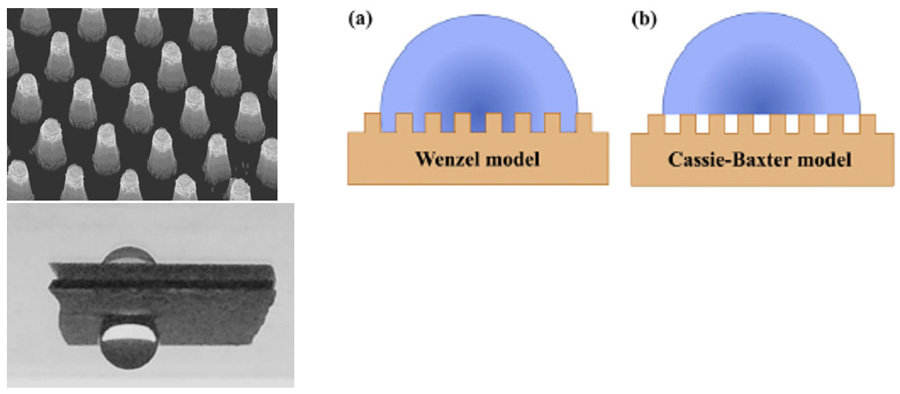
The example at the right in Fig. 1 shows a high contact angle but the water droplet sticks to the surface and never rolls off. This is a typical example of a Wenzel model but only partially addresses the overall goal, i.e. it is hydrophobic but not water repellant and therefore not ideal when dealing with insulators used in outdoor applications.
Evaluating Durability & Ageing of Potential Candidates
Sediver Research Center recently conducted intensive screening of existing options of surface treatments. The initial work consisted of checking the ability of candidate treatments to sustain electrical stresses, such as an energized insulator in a salt fog environment. The ‘survivors’ would then be tested under polluted environments, as described below.
Among the spectrum of different options to change the properties of a glass or porcelain surface, many fail by lack of adherence and either peel off or are easily scratched. Most important in the case of an outdoor insulator is ensuring electrical stability and functionality of the treated surface. Fig. 2 shows a glass insulator treated with silane-based chemistry during energized long-term exposure under salt fog. Even though the initial treatment showed good insulation properties, the surface degraded rapidly under the effects of minor dry band arcing around the insulator pin.
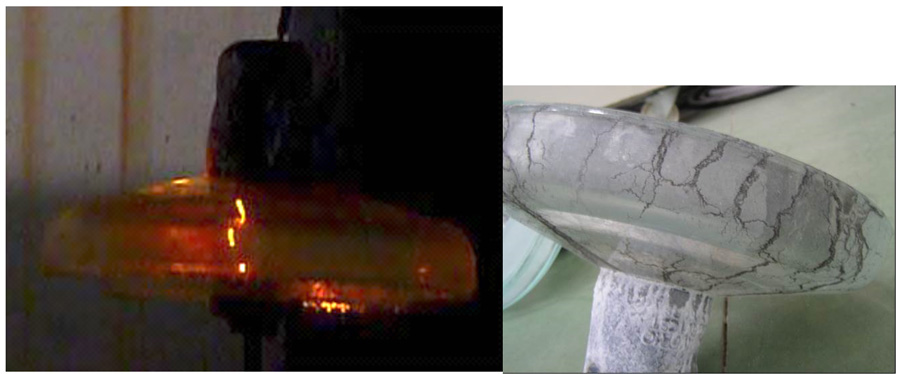
Five additional candidates were tested and benchmarked against a silicone-coated glass insulator used as reference. Fig. 3 shows the set up. Test duration was not initially considered and the idea was rather to monitor the behavior of samples over time.
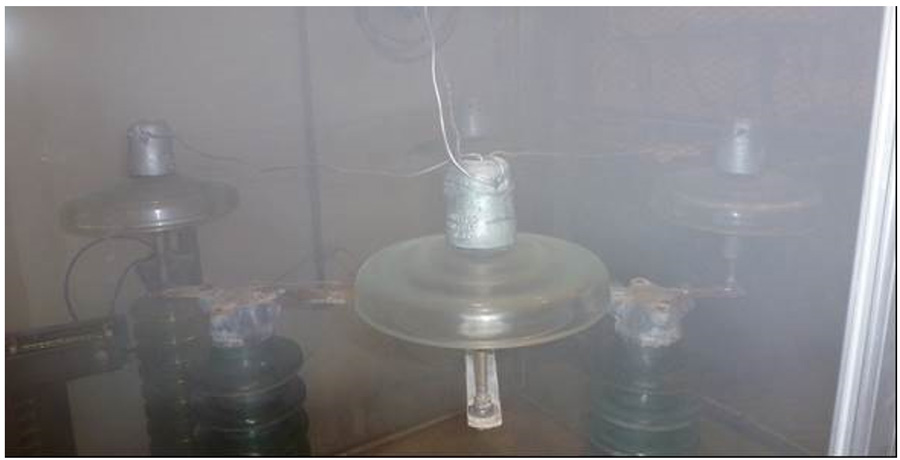
Fig. 4 depicts the main findings, where hydrophobicity is evaluated as a function of time. Two candidates seemed to maintain this property over at least 2000h, with results similar to a silicone-coated glass insulator. These candidates were kept for the next steps in the program.
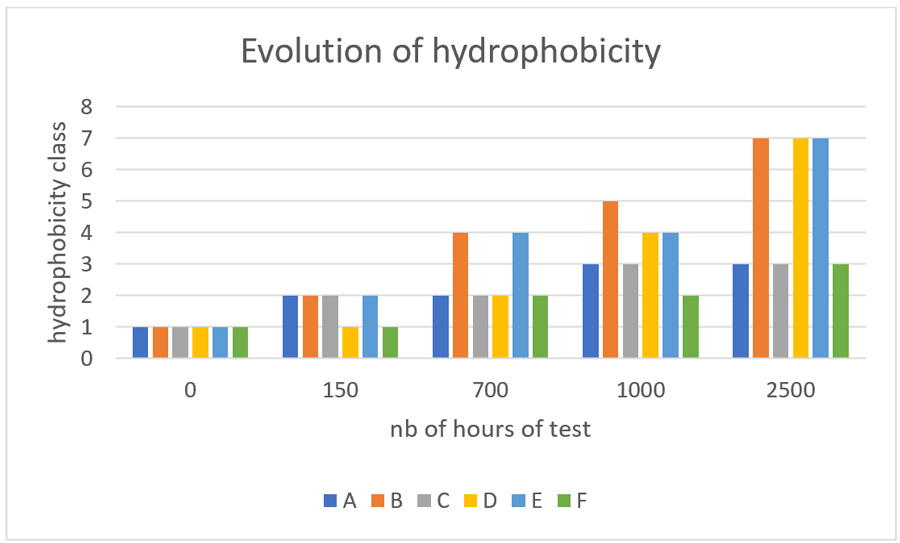
The results of this first phase showed two promising candidates. These were then tested for pollution performance under a 40g/l salt fog test as per IEC 60507 where they are compared to normal glass and to a silicone-coated glass insulator.
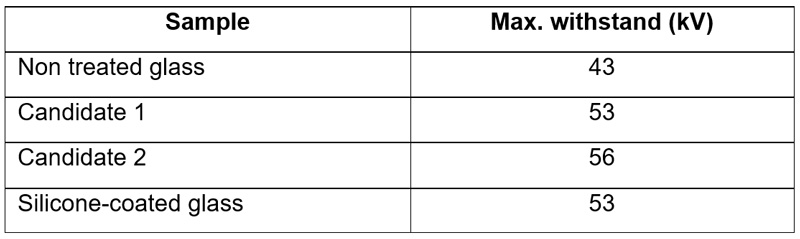
Results show that both candidates seem to have performance levels similar to a silicone coating. However, as shown in Fig. 6, hydrophobicity seems compromised by the end of the test. No recovery process was detected, unlike for a silicone coating that offers the benefit of a dynamic process. This raises another question related to test method – similar to what is done for silicone rubber or coatings. While a rapid flashover method could show better results, the fact that there is no recovery with these treatments should be considered sufficient threat that caution must be exercised when looking at laboratory test results.
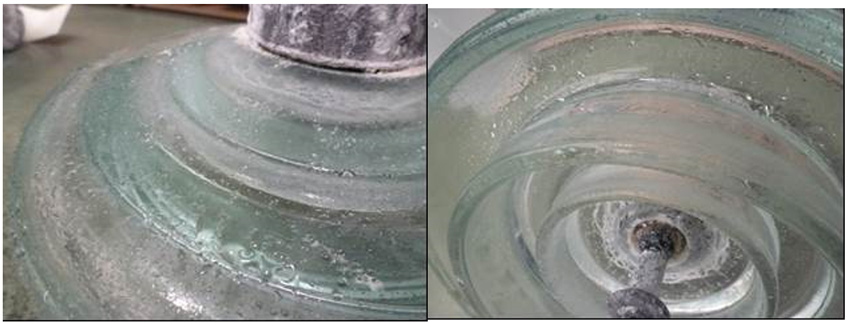
Field Dust Collection Observations
Salt fog test results, while achieving interesting values, raise a concern when comparing this technology with silicone surfaces, which offer dynamic properties such as recovery and transfer of hydrophobicity across a pollutant’s thickness. It appears obvious that the next step in the investigation requires verification that treatments display a self-cleaning property that is fundamental to prevent leakage currents in the pollutant.
To evaluate the effectiveness of potential candidates, treated insulator strings were installed near pollution sources such as a cement plant as well as a combined industrial and coastal environment. Periodically, a unit was removed to evaluate its condition as well as the volume of pollution deposited. ESDD and NSDD levels were then compared to a similar untreated unit installed in the same location (see Fig. 7).
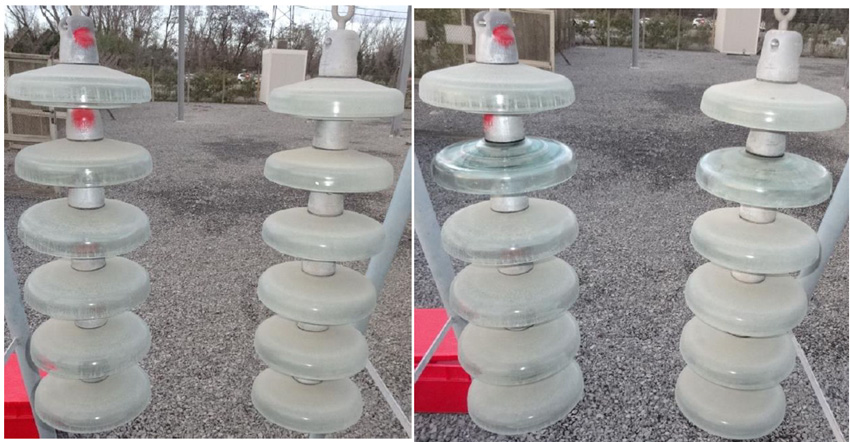
Evaluation of ESDD and NSDD was performed at various times over the year given that this area has a typical yearly pollution cycle. Results suggest that the treatment is not self-cleaning, with deposit levels that can generally be considered similar (see Fig. 8). At some point in the year, the treated string has a slightly lower NSDD but by the end of the year NSDD level is higher than for the untreated string. ESDD levels are similar.
Appearance of the insulators after washing is different as well. As evident from Fig. 9, the treated unit cleans better. This can be explained by the fact that the hydrophobic condition of the treatment modifies the morphology of deposits, making it easier to break them up during cleaning (see Fig. 10).
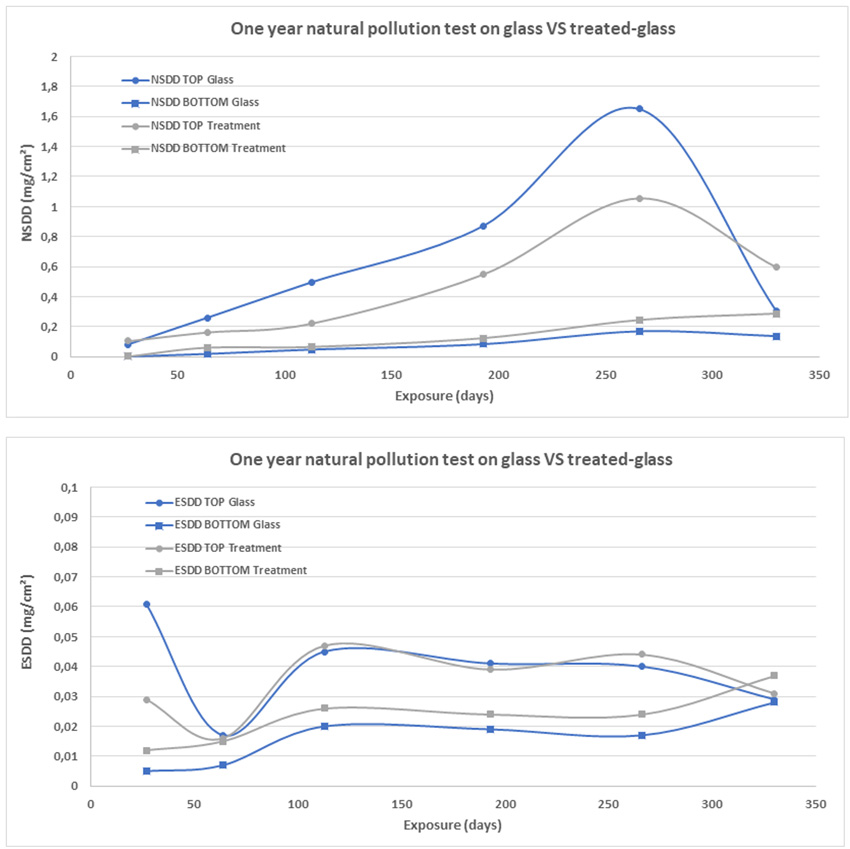

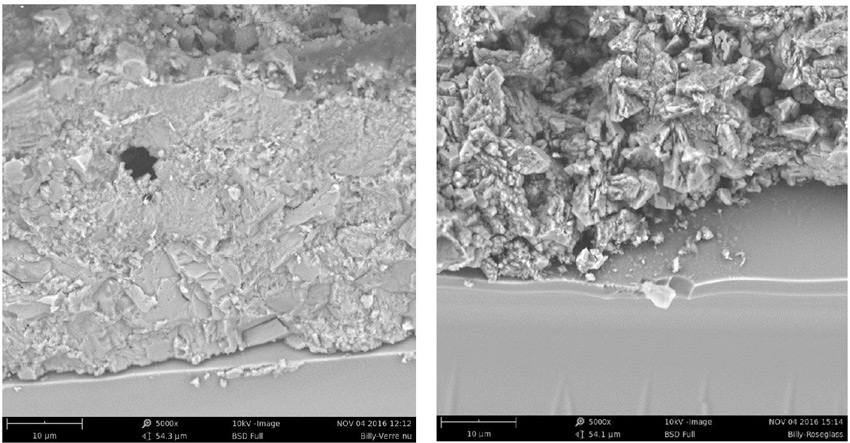
A similar study was performed in an environment that combined industrial and coastal conditions and results were consistent with previous observations (see Fig. 11). Pollutants accumulate in similar conditions between treated and untreated surfaces. This illustrates that being hydrophobic does not necessarily imply a self-cleaning property and therefore does not satisfy the need for mitigating pollution events on overhead lines. Transfer of hydrophobicity does not exist with these treatments. Fig. 12 summarizes clean fog pollution tests performed on these samples. There is no benefit of the treatment.
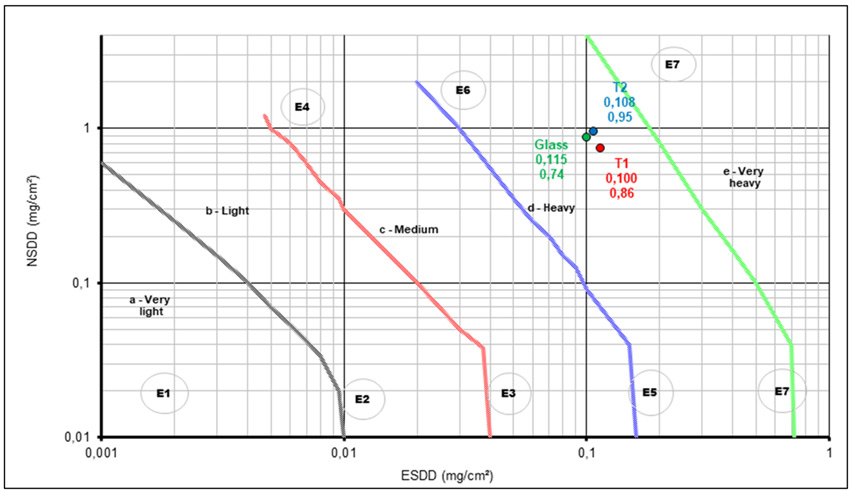
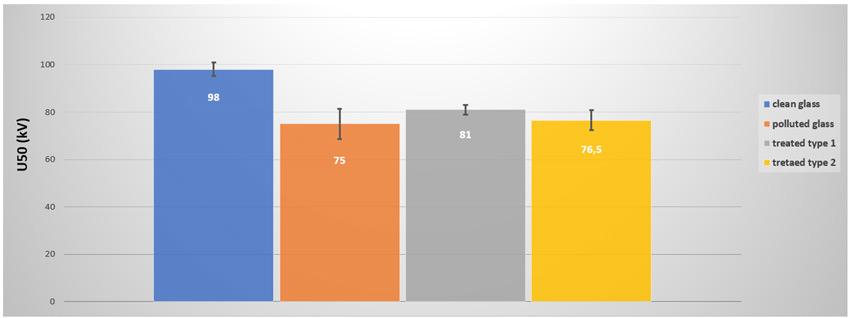
Energized Samples in Field Conditions
A third set of field results comes from the EDF test station in Martigues, located on the French Mediterranean coast in an industrial environment. Leakage currents were compared for untreated glass insulators, silicone-coated glass insulators and treated samples (using the best candidate from previous sequences). While not a heavy pollution site, Martigues is nonetheless interesting for the information that can be gathered in such an environment. Fig. 13 shows leakage currents measured over 3 years on each of the three strings energized at USCD = 46mm/kV. No flashover occurred during the test sequence, most likely because of the applied stress. Treated glass had a performance similar to the untreated insulator and lost hydrophobicity. The silicone-coated glass sample was still fully operational with low activity.
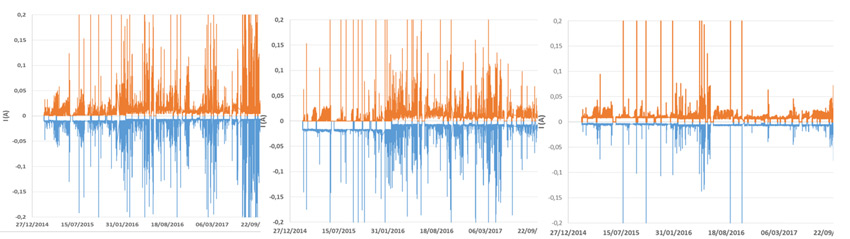
Conclusions
Application of hydrophobic treatments on ceramic insulators does not appear to show real benefit under polluted conditions, especially compared to silicone coatings. While the research here focused only on glass insulators, similar results could be expected from porcelain surfaces since glaze is a layer of glass.
The organic nature of the treatments considered in this study did not survive the environmental stress conditions and therefore they do not offer the benefits of hydrophobicity transfer and recovery, as do silicone coatings. Various tests performed showed that treatments lose their hydrophobicity rapidly once exposed to electrical activity at the surface. Another negative characteristic of treatments is absence of self-cleaning. To provide long-term benefit, these treatments should ideally prevent dust from accumulating on insulator surfaces. Rather, what has been observed under field conditions was dust deposits shielding the insulator surface and masking the hydrophobic nature of the treatment.
In addition, leakage currents were measured at an energized test station. Treated samples have values relatively close to an untreated unit, mostly because of progressive loss of hydrophobicity. By contrast, the silicone coating performed well. The only benefit of such treatments revealed during this research was their ability to promote easier washing since the deposit can be removed with less time and water pressure. This feature could nonetheless prove interesting for substations that are easier to reach and wash than long overhead lines.
The future for treatments aimed at reducing risk of pollution-related flashovers of overhead lines will require self-cleaning properties with chemistries that resist electrical activity. Organic materials do not seem such candidates and silicone-coated insulators remain superior for now mostly because of the ability of silicone to transfer hydrophobicity to the pollution layer.