Manufacturers of power distribution equipment are expected to provide products that last for decades, even under harsh service conditions. In the case of surge arresters, the housing protects the internal metal oxide varistor discs. Life expectancy of an arrester is therefore closely related to life of its polymer housing.
Compounding suitable polymeric materials for application on electrical equipment is complex and often clouded by the perception among users that the base polymer defines all the needed product characteristics. In reality, performance also depends greatly on what is compounded into the base polymer in terms of fillers and additives. Supplier experience also plays a role in ensuring a consistent and reliable polymeric material.
This edited contribution to INMR by Haley Engel of Hubbell Power Systems (HPS) in the United States reviews what is required to make a polymeric material suitable for application on critical equipment and components such as distribution arresters.
It is common belief that the single most important characteristic for insulating materials is hydrophobicity – the ability for water films to bead and break up potential leakage current paths. But the polymeric housing is also the primary defense system of an electrical component. That means other characteristics must also be taken into consideration to assure satisfactory long-term service performance:
• Resistance to tracking & erosion;
• Resistance to UV;
• High mechanical strength;
• Low moisture permeability;
• Short & long-term hydrophobicity.
Resistance to Tracking & Erosion
An important characteristic of any polymer compound is the ability to resist tracking and erosion, especially under contaminated conditions. With high contamination levels, sheds can begin to track and form an electrically conductive path along their surface. The presence of such new conductive paths defeats the purpose of the insulating material and can lead to a line-to-ground short. Moreover, high leakage currents combined with associated dry band arcing risks severely damaging the polymer surface in the form of erosion. Dry band arcing generates ozone, high temperatures and UV radiation exposure on the polymer surface. For example, the polymeric ESP™compound developed by HPS has been formulated not to track. Moreover, the EPDM base, when exposed to high temperatures, reverts to a gaseous state, leaving no conductive residue. This property prolongs service life, regardless of hydrophobicity level.
UV Resistance
Polymeric-housed devices such as arresters are exposed to UV in the form of sunlight and also from corona or dry band arcing. These can cause changes to the surface. In the case of ESP™ material, a light chalking develops during this process and protects the underlying substrate from UV damage.
High Mechanical Strength
Distribution components are often subject to high mechanical stress during handling and installation. It is therefore essential that the polymeric housing be robust enough to maintain mechanical integrity. Damage to housings in the case of surge arresters, for example, could lead to moisture ingress and ultimately electrical failure. Moreover, utilities worldwide also report instances of damage to polymeric insulation material from bird pecking. Experience at HPS confirms that EPDM-based materials are stronger mechanically and therefore more resistant to such damage.
Low Moisture Permeability
Low moisture permeability for an arrester housing is important given the frequent exposure to rain and humidity and the fact that moisture ingress is the most common cause of arrester failure. In the case of the ESP™ compound, special fillers have been incorporated to prevent build-up of moisture within the housing.
Short & Long Term Hydrophobicity
Hydrophobicity is the ability of a surface to bead water and reduce electrical activity. This property is especially valuable for polymers such as silicone rubber materials whose low surface tension helps withstand tracking and erosion. At the same time, field experience has shown that prolonged exposure to UV and contamination can degrade polymer surfaces, reducing the hydrophobic properties significantly or even completely. Such temporary loss in surface tension can render a polymeric material vulnerable to tracking during the period before hydrophobic properties recover. The ideal polymer housing would have either a permanently hydrophobic surface or a high level of resistance to leakage currents.
Components of a Reliable Polymeric Compound
Compounds suitable for electrical insulation usually consist of 10 or more ingredients that can be divided into three major categories: the base polymer; the fillers which make up nearly 50% of the compound; and active additives. Optimizing the formulation for an elastomer with these fillers and additives aims not only to achieve desired performance in the field but also to promote ease of manufacture.
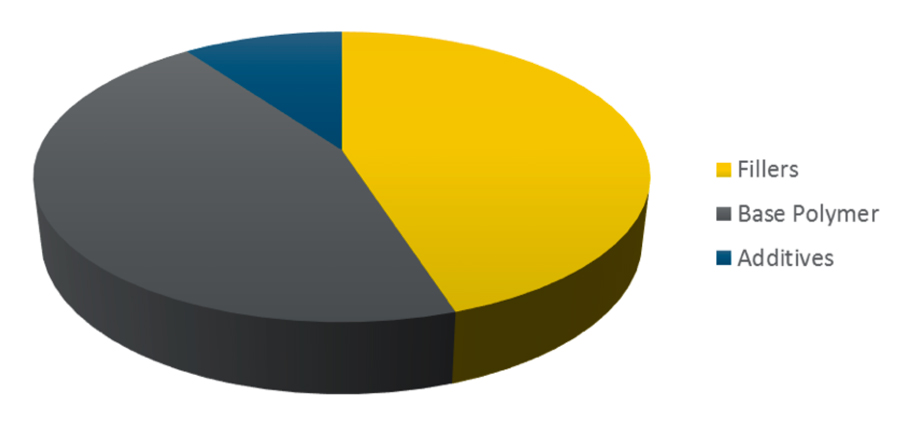
Base Polymer
The base polymer that makes up a compound is called an elastomer. The two referenced here, and the most widely recognized, are EPDM and silicone. But selection of base compound is only the first step in designing a reliable polymeric material for electrical applications. ESP™, for example, is an EPDM-based compound that has been formulated based on years of research starting during the transition in arrester housings from porcelain to polymer.
Fillers
Fillers are used to support the base elastomer and typically make up 40-60% of the compound. There are two types of fillers, classified as reinforcing and extending. Reinforcing fillers serve to improve tensile strength, modulus, tear strength and abrasion resistance of a compound. An extending filler is a loading or non-reinforcing material used to enhance desirable properties such as electrical characteristics and flammability resistance.
Alumina Trihydrate (ATH) acts as extending filler that further improves a compound’s electrical characteristics. An additional benefit is that, when overheated, ATH undergoes an endothermic reaction in which it rehydrates to release water. This leaves behind the inorganic component and in the process cools the surface making it more resistant to damage due to dry band arcing.
Additives
Additives support the manufacturing processes by protecting the chemical bond between fillers and elastomer during vulcanization. These materials make up a small percentage of the overall compound but help manufacturers achieve consistency in the final product.
The combination of the above three components aims to result in a versatile polymer that can stand up to environmental factors that might otherwise lead to deterioration and degradation.
Testing for Long-Term Reliability
Once the characteristics required of an ideal polymer housing material have been defined, the next step is to develop an appropriate test protocol. For example, Ohio Brass has developed a series of polymer test methods that aim to correlate laboratory performance with long-term reliability in the field.
Polymeric compounds for application in high voltage insulation should be tested for their ability to resist tracking, erosion, corona and UV radiation to ensure long-term reliability. Key test procedures have been defined to achieve the characteristics required for a suitable housing material. (Detailed information is found in Polymer Compounds used in High Voltage Insulators.) Table 1, for example, outlines a specific testing regime developed by HPS that allows different materials to be evaluated to assure optimum material selection for electrical insulation applications.

Resistance to Tracking & Erosion
The Hubbell tracking test was first developed to evaluate glaze compounds for porcelain and later used to evaluate tracking and erosion resistance of polymeric insulation materials as well as their ability to withstand surface electrical discharges. This test offers a screening method to ensure any polymeric material will perform as well as porcelain. Tracking evaluation is performed on a rectangular section of the molded material. Electrodes are clamped on opposing sides with a defined gap between them. The sample is then energized and repeatedly sprayed with a conducting solution. Surface currents between the electrodes heat and dry the sample until flow of current ceases. The sample is again sprayed with the conducting solution and these cycles continue until the material shows signs of carbonization or erosion on its surface. Such failure is usually the result of tracking and/or erosion and characterizes the polymer’s ability to withstand harsh service conditions.
Ultraviolet (QUV) & Corona Testing
Outdoor insulation is exposed to UV from sunlight as well as from corona and dry band arcing. UV testing aims to challenge a polymer’s ability to resist absorption of this radiation in combination with high humidity, which together can affect its dielectric and weathering properties. This characteristic is verified by two tests: QUV and corona cutting. QUV subjects a sample to cycles of high UV light, heat and humidity whereas the corona-cutting test subjects a mechanically stressed sample to concentrated corona from a ‘needle’ electrode. Presence of corona will age polymers by generating UV and ozone and passing this test demonstrates that proper chemical compounding has taken place during manufacture.
Additional Testing for Mechanical Strength & Moisture Permeability
To further qualify a polymer compound for electrical applications, abrasion and tear testing is done to ensure the material has high mechanical strength. In the case of distribution arresters, moisture permeability of the material must also be considered in conjunction with the end product’s sealing system. IEC 60099-4 and IEEE C62.11 surge arrester standards both provide guidelines for the extensive tests performed on the entire arrester design. These tests are then documented in the manufacturer’s type test reports to ensure that the product’s protective function remains consistent during service.
Conclusions
As a result of required performance criteria as well as test methods to verify these, two materials have emerged as the most suitable for application as distribution arrester housings – EPDM and silicone rubber based polymers. Hubbell standard tests, for example, have proven effective at determining material robustness and these same tests are still followed to qualify silicone and EPDM-based compounds. Hubbell has chosen a route of blending silicone with EPDM to formulate its material. This is an enhanced polymer utilizing a combination of EPDM and silicone with additives such as ATH to achieve a high level of resistance to tracking and erosion from corona and UV. This formulation also demonstrates high mechanical strength and resistance to moisture permeability.
Bibliography
[1] R.A. Bernstorf, Polymer Compounds used in High Voltage Insulators, Hubbell Power Systems, 2004
[2] Long Term Performance of Polymer Housed MO-Surge Arresters, CIGRE, 2004
[3] Dr. F. Schmuck, Dealing with Deterioration of Silicone Insulation in Critical Applications, http://www.inmr.com/dealing-deterioration-silicone-insulation-critical-applications-2/
[4] V. Sklenicka, K. Fiala and M. Bruckmet, Applying RTV Silicone Coatings to Restore Degraded Composite Housings, http://www.inmr.com/applying-rtv-silicone-coatings-restore-degraded-composite-housings/
[5] IEC 60099-4, Surge arresters – Part 4: Metal-oxide surge arresters without gaps for a.c. systems
[6] IEEE C62.11, IEEE Standard for Metal-Oxide Surge Arresters for AC Power Circuits (> 1 kV)