Silicone rubber materials exhibit properties that make them ideal for application as housings in composite HV outdoor insulators. These include stability against UV and ozone; good dielectric properties unaffected by variations in temperature; non-toxic combustion products; excellent hydrophobicity recovery and transfer to pollution layer; high arc resistance according to IEC 61621 and high tracking resistance according to IEC 60587. HTV silicone rubbers are typically applied as housings on large composite hollow insulators manufactured using extrusion technology as well as on hollow and solid core insulators produced using injection moulding technology. LSR rubbers, by contrast, are generally applied as housings of large composite hollow insulators manufactured with injection moulding technology.
This edited past contribution to INMR by experts at Reinhausen Power Composites reviewed testing to assess long-term performance of special grades of silicone rubber adapted for HV outdoor applications. Performance of these HTV and LSR housed insulators was evaluated based on comparing long-term service experience in the field with results obtained from testing the materials in the laboratory.
Pollution Performance of Composite Hollow Core Insulators with HTV LSR Housings by Eric Moal
Test Program
The following design tests were performed on both HTV and LSR materials to assess performance under a range of service conditions:
• IEC 61621 – High arc resistance;
• IEC 60587 – High tracking resistance – Inclined plane test;
• Dynamic Drop Test (DDT);
• IEC 61462 (§7.3.2) / IEC 62217 (§9.3.2) – Accelerated weathering test;
• Artificial pollution test under AC and DC stress.
Designs were evaluated based on the 1000h salt fog test (IEC 62217) as well as both the 2000h (ENEL/Terna Cycle) and the 5000h (EDF Cycle) ageing tests applied to sample insulators. Testing included:
• IEC 62217 (2005-10) First edition – 5000-hour multiple stress test;
• IEC 61462 (§7.3.3) / IEC 62217 (§9.3.3) – Tracking and erosion test with different shed profiles and dimensions;
• Long-term outdoor test under AC stress.
Laboratory Tests of Materials Under AC & DC
1. IEC 61462 (§7.3.3) / IEC 62217 (§9.3.3) – Tracking and Erosion Test
Also known as the 1000-hour salt fog test, this test was passed and both LSR and HTV type insulators with different shed profiles and dimensions were tested successfully:
• No tracking occurred;
• Erosion depth (< 3 mm) did not reach the core;
• no shed, housing or interface was punctured.
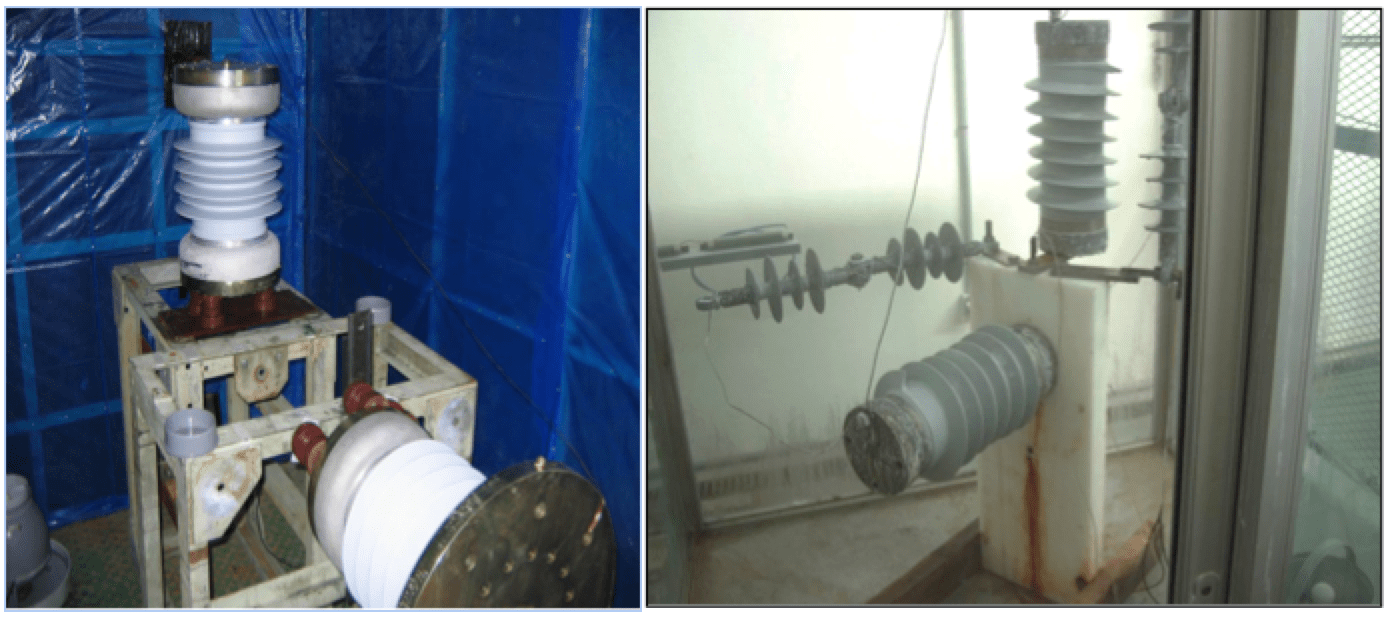
2. 2000 & 5000-Hour Multiple Stress Test
This test consists of accelerated ageing weather cycles that combine multiple stresses: humidification, heating to +50°C, rain, simulated radiation and salt fog, based on IEC 62217 Annex B (2005-10). Insulators were tested using the following cycle:
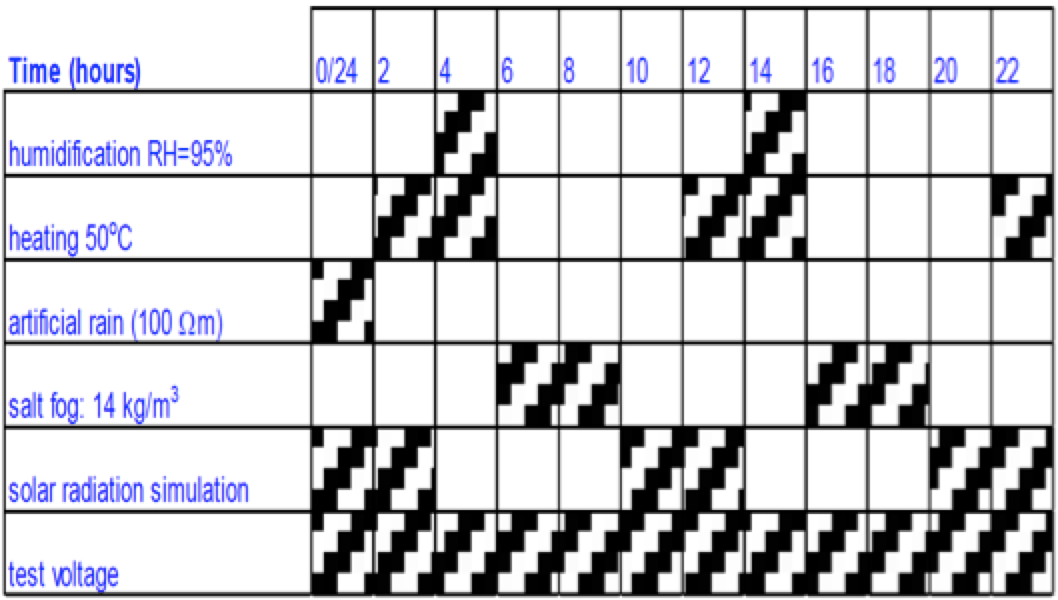
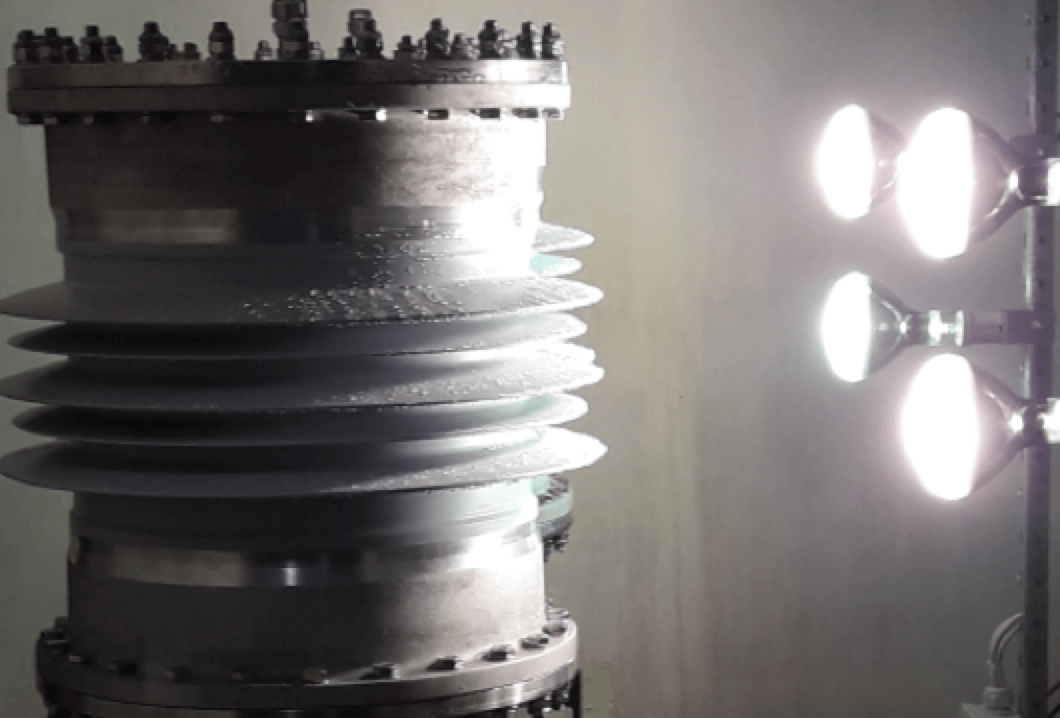
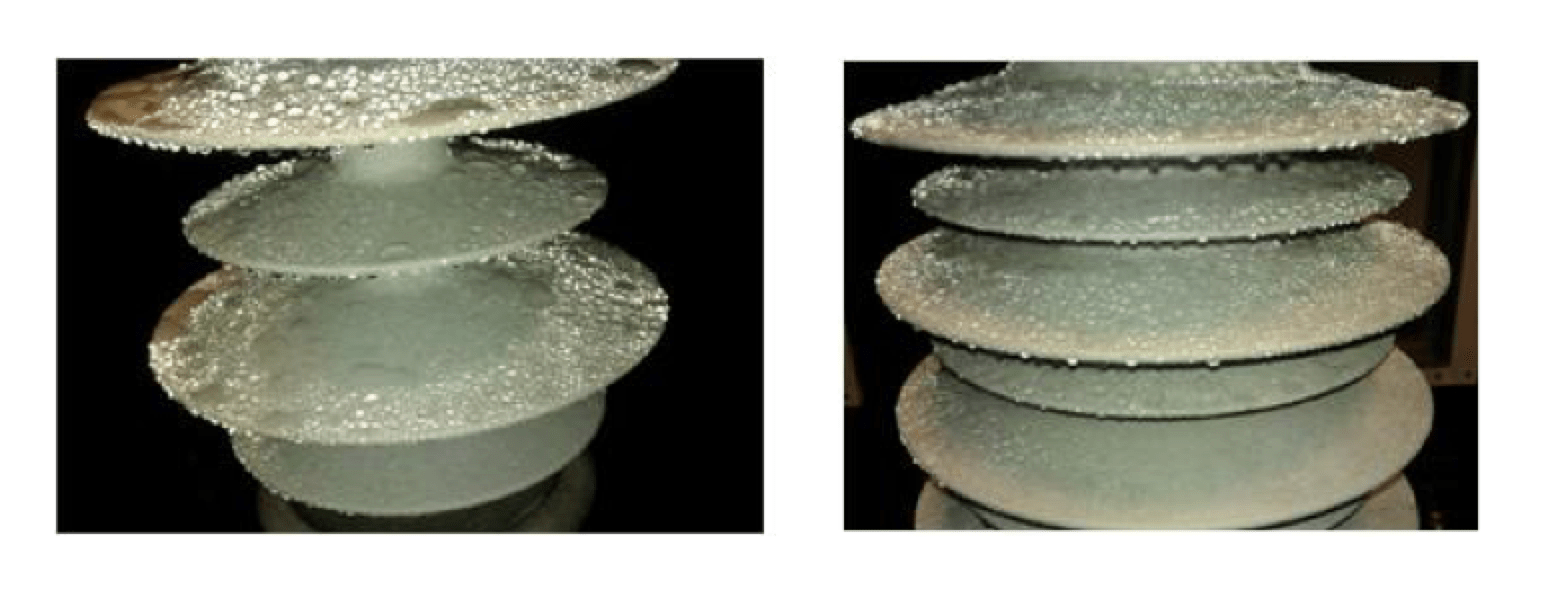
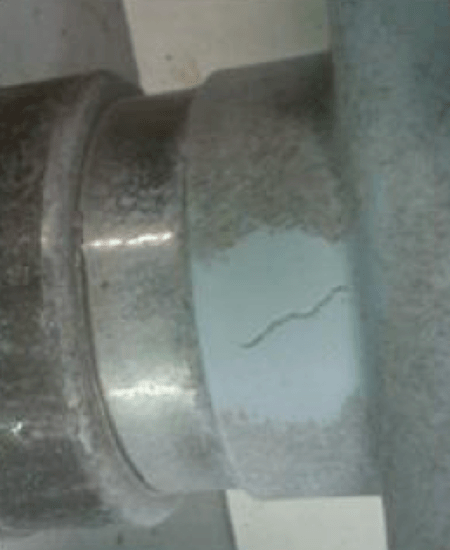
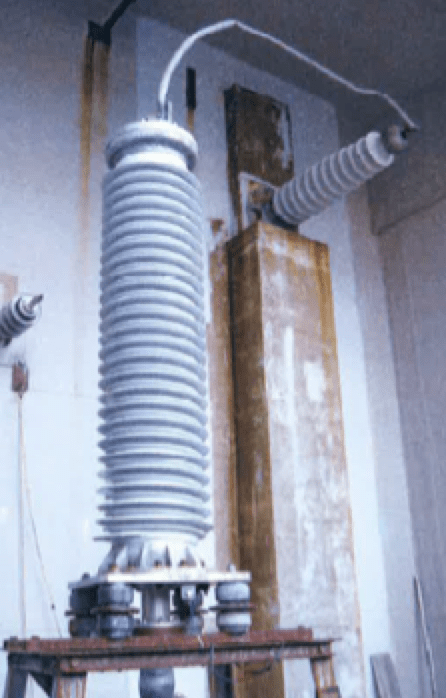
Solid and hollow core insulators were observed after the successfully passed 5000-hour ageing test with the following results for both LSR and HTV types:
• hydrophobicity tests (wettability class WC 2 to WC 4);
• slight erosion (1 mm depth < 3 mm max. criteria);
• no sheds punctured.
Satisfactory results were also observed after the 2000-hour multiple stress test according to the specification of Italian TSO, Terna, that saw LSR and HTV type 245 kV cable terminations tested in their actual service configuration.
Artificial Pollution Laboratory Test with DC
Artificial pollution tests were also performed on both LSR and HTV type composite hollow insulators based on IEC TS 61245 and using two different methods:
1. The solid layer method simulates the type A pollution associated with inland, desert or industrial areas, as defined in IEC 60815-1;
2. The salt fog method simulates type B pollution associated with coastal areas where salt water or conductive fog are deposited onto insulator surfaces.
These tests had satisfactory results and allowed the behaviour of different insulator designs and HTM housing materials to be verified under various levels and types of pollution. Results were analysed with consideration to the diameter correction proposed in IEC TS 60815-4.
Differentiating Short-Term Pollution Versus Long-Term Ageing Tests
Ageing Tests
The basic philosophy behind the 1000h, 2000h and 5000h tests is based on scaling to service and test station experience, e.g.
• Degree of tracking and erosion in the 1000-hour test is comparable to 10 to 15 years of marine environment, scaled to North Sea test stations (Brighton, U.K. & Nordstrand, Germany), as first introduced in the German VDE standard and later transferred into the first edition of IEC 61109;
• Degree of multiple stress of the 2000-hour test is comparable to more than 10 years of Mediterranean/Italian coastal conditions, as introduced into the ENEL/Terna specification;
• Degree of multiple stress of the 5000-hour test is comparable to more than 10 years of Mediterranean conditions at the Martigues Test Station, as introduced into the EDF specification. It also compares to Annex C of the first edition of IEC 61109, now under consideration as a suitable ageing test in the revised version of IEC 62217 (presently documented in IEC TR 62730).
The IEC needs to clarify whether a real multiple stress (ageing) test needs to be re-introduced in the future.
AC/DC Artificial Pollution Tests for Conventional & Polymeric Insulators
Artificial pollution testing is well developed and accepted for porcelain and glass insulators in IEC 60507 for AC and IEC 61245 for DC (i.e. solid layer and salt fog methods). However, in the case of polymeric/composite insulators having hydrophobicity transfer mechanism (HTM) characteristics, no IEC test has yet been published. A number of ideas exist for AC and DC applications (e.g. CIGRE TB 691) whereby partial masking of hydrophobicity is simulated and hydrophobicity class (HC) is set at 3 to 4. This may be sufficient to most users but future plans for IEC standards in regard to HTM materials should nonetheless define clear test conditions to allow better reproducibility.
Some aspects of pollution tests for composite insulators are adequately covered by international standards but others require further research, i.e.:
• AC and DC pollution tests for hydrophilic surfaces are well established;
• AC and DC pollution tests for hydrophobic surfaces with HTM properties need further research;
• Ageing tests must be better defined in regard to wetting process (e.g. direct versus indirect spray method);
• Deposition of pollution and dust on polymeric materials is higher due to electrostatic characteristics but HTM materials more than compensate for this due to superior electrical performance.
Long-Term Outdoor Performance of HTV/LSR Hollow Core Insulators
French power utility, EDF, operates an outdoor test facility in Martigues. Located near the coast of southern France, this test station is subjected to severe pollution that ensures continuous leakage current, including:
• marine (salt fog);
• industrial (oil refineries and power plant).
Regular visual inspections performed each month include measurement of:
• pollution severity class;
• hydrophobicity class.
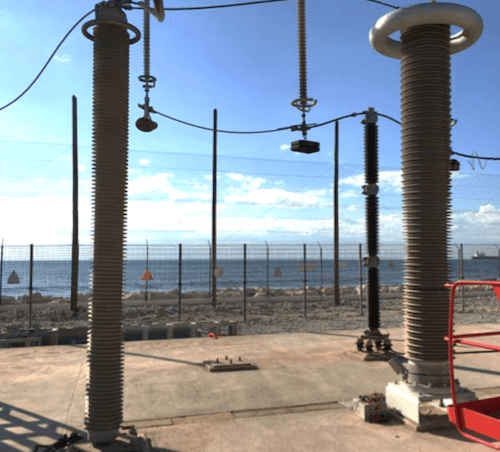
An LSR and an HTV hollow core insulator are now at this test station and have been energized there for more than 3 and 10 years respectively. According to IEC 60815-1:2008, Annex E, the SPS Class at the site is “d” (heavy) as confirmed by ESDD/NSDD measurements and the station is operated following recommendations from CIGRE TB 333. Test results to date are positive, i.e.:
• Hydrophobicity tests (wettability class WC 2 to WC 5);
• low leakage currents (the majority being <10 mA);
• no tracking.
Similar experience with HTV silicone insulators at other sites and across many equipment applications already covers more than 25 years.
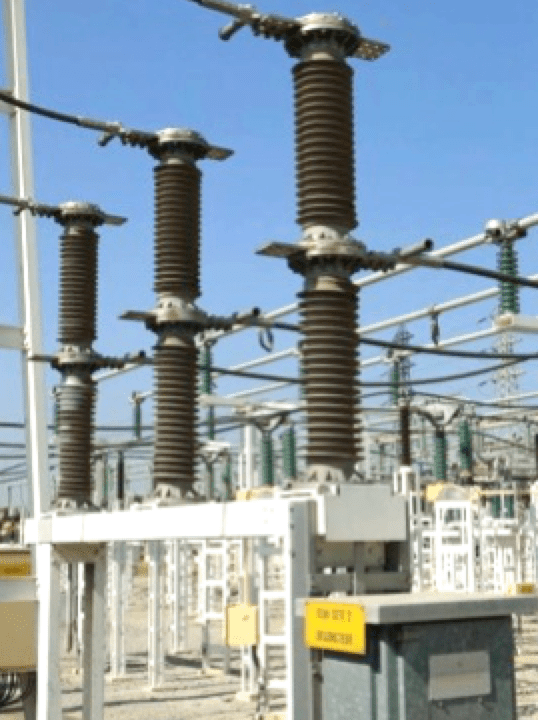
Conclusions
When properly designed from the perspective of shed profile and interfaces, LSR and HTV silicone material classes both successfully pass design tests according to IEC 61462 and IEC 62217. Laboratory material and insulator design tests are helpful tools during the material selection and qualification processes. But these should be supported by additional long-term installation at test stations located in severe environments. For example, insulators that passed the 5000h test have also shown excellent performance at the Martigues Test Station that simulates Mediterranean service conditions. Finally, feedback from this chain of testing is reinforced by over 25 years of positive service experience at Terna and EDF. As described above, a philosophy of proper testing ensures safe and reliable material selection and design practice for composite hollow core insulator applications in AC and DC using either LSR or HTV/HCR materials.
>
References
[1] IEC 61621:1997
Dry, solid insulating materials – Resistance test to high-voltage, low-current arc discharges
[2] IEC 60587:2007
Electrical insulating materials used under severe ambient conditions – Test methods for evaluating resistance to tracking and erosion
[3] ISH 2019 – Comparison of Laboratory Test, Field Station and Service Performance of HTV and LSR Hollow Core Housings
By Moal, Eric (1); Seifert, Jens (2); Rädlinger, Konrad (2)
Organization(s): 1: Reinhausen France, France; 2: Reinhausen Power Composites, Germany
[4] CIGRE Technical Brochure No. 661, Feasibility Study for a DC Tracking and Erosion Test. WG D1.27, March 2015.
[5] CIGRE Technical Brochure No. 442; Evaluation of Hydrophobicity Properties of Polymeric Materials for Non-Ceramic Outdoor Insulation. Retention and Transfer of Hydrophobicity. WG D1.14, 2010.
[6] Electra Paper No. 272; Retention of Hydrophobicity under DC voltage stress – Evaluation with the dynamic drop test, Feb. 2014.
[7] IEC 61462:2007
Composite hollow insulators – Pressurized and unpressurized insulators for use in electrical equipment with rated voltage greater than 1 000 V – Definitions, test methods, acceptance criteria and design recommendations
[8] IEC 62217:2012
Polymeric HV insulators for indoor and outdoor use – General definitions, test methods and acceptance criteria
[9] ISO 4892-2:2013
Plastics – Methods of exposure to laboratory light sources – Part 2: Xenon-arc lamps
[10] E. Moal, V. Bergmann, C. Pons, A. Soergel, W. Manzke , Technical design requirements and test experiences on Composite Hollow Core Insulators regarding pollution performance under AC and DC stress – CIGRE Paris, 2018, reference A3-308.
[11] IEC 62217 (2005-10) First edition
Polymeric HV insulators for indoor and outdoor use – General definitions, test methods and acceptance criteria
Annex B- Test at multiple stresses
[12] IEC TS 61245:2015
Artificial pollution tests on high-voltage ceramic and glass insulators to be used on d.c. systems
[13] IEC 60815-1:2008
Selection and dimensioning of high-voltage insulators intended for use in polluted conditions – Part 1: Definitions, information and general principles
[14] IEC 60815-4:2016
Selection and dimensioning of high-voltage insulators intended for use in polluted conditions – Part 4: Insulators for d.c. systems
[15] IEC 61109:1992 – Composite insulators for a.c. overhead lines with a nominal voltage greater than 1000 V – Definitions, test methods and acceptance criteria
[16] ETG-Fachtagung “Grenzflächen an Isolierstoffen”, Bad Nauheim, 1999: ”Betrieberfahrungen und untersuchungen an kunstoffisolatoren in einer 20 kVLeitung auf der Insel Nordstrand” by Roland Bärsch, Hochschule Zittau – Martin Kuhl, CeramTec).
[17] CIGRE 15-07 / 1988: ”Results of accelerating ageing tests on components of electric system made with polymeric insulators” by G.P. Fini, G. Marrone, A. Porrino, ENEL Italy
[18] IEC TR 62730:2012 – HV polymeric insulators for indoor and outdoor use tracking and erosion testing by wheel test and 5 000h test
[19] CIGRE 33-304 / 1996: “Studies of long term performance of composite insulators and of the representativeness of ageing tests” by G. Riquel, EDF – D. De Decker, SEDIVER
[20] IEC 60507:2013 – Artificial pollution tests on high-voltage ceramic and glass insulators to be used on a.c. systems
[21] CIGRE TB 691 – Pollution test of naturally and artificially contaminated insulators
[22] CIGRE TB 333 – Guide for the establishment of naturally polluted insulator testing stations
[inline_ad_block]